Cara Mengurangi Waktu Henti Mesin di Manufaktur
Pabrikan berada dalam kondisi peningkatan yang konstan, tetapi meningkatkan efisiensi dan mengurangi waktu tunggu telah membawa banyak perhatian pada jumlah waktu mesin tidak berproduksi. Perusahaan sering meremehkan biaya dan jumlah waktu henti yang mereka alami, meskipun faktanya hal itu sangat memengaruhi kapasitas seluruh toko. Berikut ini akan mengeksplorasi strategi dan solusi untuk melacak, mengkategorikan, mengekspos, dan pada akhirnya mengurangi waktu henti yang tidak direncanakan untuk memastikan produsen menghasilkan throughput sebanyak mungkin.
Berapa Downtime Costing Produsen?
Produsen sering kali mengetahui bahwa mereka memiliki masalah dan menyebutkan bahwa yang terbesar adalah waktu henti. Namun, itu mungkin sejauh mana produsen tahu tentang masalahnya. Laporan tahun 2017 berjudul "" menyatakan bahwa sebagian besar perusahaan secara signifikan meremehkan biaya downtime mereka yang sebenarnya. Selain itu, lebih dari 80% perusahaan tidak memiliki data atau kemampuan untuk secara akurat menghitung biaya waktu henti mereka. Dengan tren terkini dalam IIoT, konektivitas mesin, dan solusi pemantauan, produsen mulai mendapatkan jawaban atas pertanyaan yang bahkan tidak mereka ketahui seharusnya tanya.
Apa Penyebab Utama Henti?
Mengidentifikasi penyebab utama waktu henti adalah tempat yang baik untuk mulai mencari peningkatan. Penyebab downtime yang paling mengerikan sering mengungkapkan inefisiensi yang tampak jelas dan area untuk perbaikan. Di bawah ini adalah beberapa alasan paling umum untuk kegagalan mesin dan penyebab downtime di manufaktur.
Inefisiensi Proses
Setiap proses manufaktur memiliki periode waktu di mana peralatan tidak tersedia karena penyetelan, perubahan perkakas, perubahan material, perubahan suku cadang, perubahan program, atau perubahan lain apa pun pada produksi yang harus dilakukan saat peralatan dihentikan. Namun, banyak dari proses ini sangat tidak efisien karena kurangnya pengukuran, analisis, dan perbaikan. Meskipun sangat penting untuk melacak waktu ini, sebagian besar toko tidak dapat melakukannya, dan mereka yang melakukannya lebih sering daripada tidak mencoba melakukannya secara manual yang tidak efisien, tidak akurat, dan datanya seringkali sulit untuk dikompilasi, dianalisis, dan mendapatkan wawasan. dari.
Kesalahan Operator
Tidak ada orang yang sempurna. Manusia menjadi lelah, terluka, lupa, dll. Terkadang operator terlalu banyak bekerja atau merawat banyak mesin. Alasan-alasan ini dapat menyebabkan mesin mati untuk waktu yang signifikan sebelum diketahui. Kesenjangan keterampilan juga mengakibatkan sebagian besar tenaga kerja pensiun, membawa serta pengetahuan kesukuan yang mendalam yang mungkin tidak diteruskan ke karyawan baru.
Waktu Henti Material
Dengan biaya yang terkait dengan inventaris, banyak produsen ingin beroperasi se-ramping mungkin. Sayangnya, persediaan lean dapat meningkatkan kejadian waktu henti ketika ada gangguan dalam rantai pasokan. Memiliki wawasan tentang perkiraan permintaan dan pasokan bahan dapat membantu mengurangi masalah ini.
Inefisiensi Pemeliharaan
Terlalu sedikit atau terlalu banyak perawatan dapat menyebabkan kegagalan. Manfaat besar lainnya dari perangkat yang terhubung adalah mengurangi jumlah pemeliharaan preventif. Dengan data alat berat yang akurat, produsen dapat memprediksi dengan lebih baik kapan perawatan diperlukan. Dalam “ Peta Jalan menuju Otomatisasi Pemeliharaan Digital ," kami membahas bagaimana produsen dapat beralih ke strategi pemeliharaan yang lebih efektif dan hemat biaya untuk mengurangi biaya sekaligus meningkatkan waktu kerja peralatan.
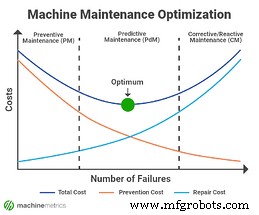
Namun, ini bukan tentang analisis prediktif . Dalam satu contoh, pabrikan mendokumentasikan lebih dari 14.000 jam untuk penyiapan mesin. Setelah mengadopsi MachineMetrics untuk secara otomatis melacak waktu penyiapan, perusahaan menemukan waktu yang sebenarnya untuk penyiapan alat berat mendekati 1.000 jam. Mampu mengurangi waktu henti yang direncanakan dapat membebaskan sumber daya dan mempermudah untuk mengetahui ukuran dan cakupan waktu henti yang tidak direncanakan. Itu bukan tentunya tentang waktu henti yang direncanakan versus tidak direncanakan, melainkan masalah terbesar yang memengaruhi produksi dan kapasitas.
Waktu Henti Budaya/Manajemen
Produsen berada di bawah tekanan. Membiarkan stres ini mencapai operator dapat membuat mereka merasa tidak punya waktu untuk bernapas, memperbaiki kesalahan, melakukan pembersihan rutin, atau perawatan. Budaya stres yang terus-menerus beroperasi pada kecepatan maksimum dapat menyebabkan peningkatan kesalahan operator dan perawatan alat berat. Inilah sebabnya ini penting untuk dimiliki data waktu siklus yang akurat untuk memastikan ekspektasi realistis.
Strategi yang Dapat Ditindaklanjuti untuk Mengurangi Waktu Henti Manufaktur
Ini penting untuk mengikuti perjalanan analitik menggunakan data sebagai landasan. Sebelum otomatisasi dapat diadopsi dan berhasil, data diperlukan untuk membawa visibilitas masalah dan mendorong pengambilan keputusan yang pada akhirnya dapat mengarah pada otomatisasi. Visibilitas ini akan menunjukkan di mana masalah itu ada, sejauh mana itu mempengaruhi produksi, dan bagaimana Anda dapat bekerja untuk menyelesaikannya. Tidak semuanya membutuhkan analisis prediktif.
Produsen mungkin membicarakan tentang fasilitas yang sepenuhnya otonom , tetapi Anda harus berjalan sebelum berlari. Menggunakan data sebagai dasar adalah langkah pertama untuk mempelajari apa yang paling memengaruhi produksi dan waktu tunggu. Sebuah solusi pelacakan waktu henti produksi menyediakan data mesin waktu nyata yang akurat dan memberi pekerja kemampuan untuk mencatat dan mengkategorikan penyebab waktu henti. Semua informasi secara otomatis dikumpulkan dan distandarisasi untuk ditampilkan dalam laporan dan dasbor real-time yang dibuat sebelumnya dan disesuaikan untuk memberikan visibilitas penting bagi para manajer. Wawasan ini mengidentifikasi kesenjangan dan peluang bagi para pemimpin manufaktur untuk mendorong peningkatan.
Berikut adalah beberapa strategi untuk membantu mengurangi tidak direncanakan waktu henti:
Melacak dan Mengkategorikan Waktu Henti Secara Akurat
Tanpa data waktu henti yang cukup akurat, ini sulit untuk memprioritaskan tindakan perbaikan. Beralih dari pelacakan mesin manual ke otomatis sangat penting untuk tidak hanya memahami jumlah total waktu henti yang dialami toko, tetapi juga ini juga berguna untuk melacak berbagai KPI, seperti pemanfaatan mesin dan OEE. Namun, operator masih penting untuk pengumpulan data downtime. Mereka dapat memberikan "mengapa" di balik waktu henti dengan mendokumentasikan alasan acara dengan cepat.

Dengan MachineMetrics, operator dapat dengan mudah mengkategorikan peristiwa waktu henti pada tablet yang ditempatkan di mesin. Semua data ini dikumpulkan dan disebarkan dalam laporan yang dibuat sebelumnya dan disesuaikan.
Untuk tampilan lantai toko yang lebih baik, MachineMetrics mengembangkan perangkat lunak dengan mempertimbangkan operator. Jika mesin mati atau mati lebih lama dari yang diharapkan, fitur muncul pada tablet yang ditempatkan di mesin yang memungkinkan operator mengkategorikan dan menambahkan alasan untuk waktu henti melalui tampilan Operator. Di antara pelacakan alat berat otomatis dan fitur yang memungkinkan operator mencatat alasan waktu henti langsung di tablet alat berat, MachineMetrics memberi operator dan manajer informasi yang mereka butuhkan untuk membuat keputusan operasional yang lebih baik dan bekerja untuk mengurangi waktu henti.
Mengekspos Waktu Henti secara Real-time
Menggunakan teknologi pelacakan otomatis memberikan visibilitas waktu nyata ke lantai toko, baik pemangku kepentingan berada di lantai toko atau di rumah. Peristiwa waktu henti langsung terlihat di dasbor. Dengan data waktu nyata dan perangkat lunak yang tepat, manajer dapat mengatasi waktu henti saat hal itu terjadi. Selain itu, pemberitahuan otomatis dapat dipicu berdasarkan peristiwa waktu henti. Misalnya, jika alarm pompa dipicu, MachineMetrics dapat mengirim pemberitahuan langsung ke bagian pemeliharaan untuk menyederhanakan respons waktu henti. Jika bahan hampir habis, kontrol inventaris dapat menerima pemberitahuan untuk mengisi ulang atau memesan lebih banyak persediaan untuk memastikan mesin tidak mati saat menunggu material.
Data waktu nyata juga menyederhanakan analisis dan laporan. Semakin cepat data mentah dikontekstualisasikan untuk dikonsumsi (dalam laporan dan dasbor), semakin cepat pembuat keputusan dapat menemukan dan menyerang penyebab downtime terbesar. MachineMetrics menggunakan teknologi terhubung dan komputasi awan canggih untuk memberikan laporan waktu henti cepat yang akurat dengan diagram batang Pareto interaktif yang menyoroti alasan utama waktu henti Anda.
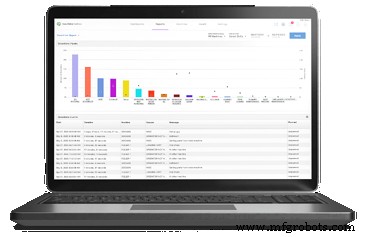
Diagram Pareto waktu henti dengan mudah mengidentifikasi alasan waktu henti yang paling umum dan mahal.
Tetapkan Sasaran Pabrik Manufaktur Tertentu
Tujuan memberikan arahan kepada staf dan organisasi. Dengan data yang akurat dan dasbor yang mudah diikuti, ini dapat melacak produksi antara shift, operator, dan alat berat untuk menetapkan garis dasar dan menetapkan tujuan. Manfaat lainnya termasuk kemampuan untuk:
- Mulai program akuntabilitas atau insentif
- Tambahkan nilai pada evaluasi staf
- Temukan kesenjangan pelatihan atau kebutuhan pelatihan ulang
Secara keseluruhan, sasaran dan data akurat bekerja sama untuk meningkatkan komunikasi secara keseluruhan. Karyawan yang memahami hubungan antara waktu henti dan sasaran, atau keuntungan, membantu memprioritaskan tanggung jawab dan dapat meningkatkan produktivitas mereka yang dapat mengurangi waktu henti.
Melakukan Pemeliharaan Peralatan Manufaktur Secara Reguler
Menemukan sweet spot untuk pemeliharaan dapat dilakukan dengan alat yang tepat. Melacak kinerja alat berat dapat membantu menyesuaikan jadwal perawatan atau bahkan memprediksi kapan pemeliharaan diperlukan . Dengan kemampuan untuk mengurangi atau menghilangkan waktu henti yang tidak direncanakan, pemeliharaan prediktif adalah pendorong lain dari teknologi terhubung. Manajer siapa dapat memprediksi kapan mesin perlu diservis dapat mempersiapkan dan merencanakan perawatan ke meminimalkan gangguan pada produksi dan jika bagian lain harus diservis selama waktu henti untuk menggabungkan dan mengurangi jumlah waktu henti secara keseluruhan. 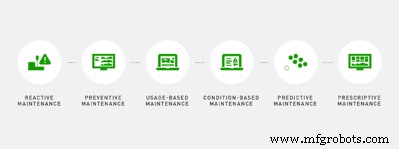
Tingkatkan Peralatan Manufaktur Anda
Meskipun solusi platform dapat mengurangi jumlah perangkat keras yang dibutuhkan, mesin lawas mungkin masih memerlukan cara untuk terhubung. Adaptor I/O sederhana atau pemantauan hidup/mati sudah cukup untuk mulai mengumpulkan data waktu henti. Sebagian besar peralatan modern akan memiliki sensor atau teknologi yang diperlukan tetapi mungkin memerlukan gerbang Industri untuk mengirim data ke platform. MachineMetric menawarkan perangkat keras dengan berbagai cara untuk terhubung untuk integrasi yang cepat dan mudah.
Melatih Karyawan Lini Produksi dengan Benar
Dengan adopsi teknologi baru, kesenjangan keterampilan, dan kesalahan operator menjadi penyebab umum waktu henti, pelatihan sangat penting. Pelatihan tidak bisa cukup menjadi serangkaian daftar periksa dan dokumen. Itu juga harus menyertakan pemahaman yang jelas tentang tujuan. Karyawan yang terlatih dengan baik akan mengurangi waktu henti dengan memahami tanggung jawab mereka dan bagaimana mereka memengaruhi tim, produksi, dan waktu henti. Ini penting untuk memungkinkan operator dengan visibilitas ke dalam produksi sehingga mereka dapat lebih memahami di mana mereka berdiri dalam hal tujuan produksi pada hari tertentu. Meskipun pelatihan terdengar cukup jelas, memiliki data kinerja dapat meningkatkan pelatihan dengan mengidentifikasi kesenjangan pengetahuan dan berfokus pada tantangan yang lebih mungkin dihadapi setiap karyawan.
Beralih dari Pola Pikir Reaktif ke Proaktif
B Berikut adalah beberapa jenis perawatan di bidang manufaktur. Pendekatan reaktif mengatakan, "mari kita perbaiki ketika rusak." Cara ini seringkali mengganggu, mahal, dan dapat mengakibatkan hilangnya produksi. Pendekatan proaktif mengatakan, "mari kita perbaiki sebelum rusak."
Pemeliharaan proaktif mempertimbangkan kondisi mesin dan pengamatan lingkungan yang dilakukan oleh staf untuk membantu mencegah masalah kecil menjadi masalah besar. Pola pikir proaktif dimulai dengan memantau seluruh proses dan menyatukan data untuk memahami apa yang terjadi di lantai produksi. Pendekatan proaktif adalah perubahan yang luas dan penting. Saat mesin dalam kondisi optimal, mesin berjalan lebih lancar dan dengan lebih sedikit kesalahan, yang berarti lebih sedikit waktu henti yang tidak direncanakan.
Identifikasi &Kurangi Pembunuh Produksi yang Jelas
Beberapa faktor dapat memengaruhi jumlah waktu henti yang dialami mesin. Beberapa penyebab paling umum adalah kesalahan operator, kegagalan peralatan, kekurangan material, dan masalah pemeliharaan tak terduga lainnya.
Untuk mengurangi waktu henti yang tidak direncanakan, Anda harus terlebih dahulu memahami berapa banyak waktu henti yang terjadi dan di mana itu terjadi. Jika Anda belum melakukannya, lacak waktu henti Anda sebagai persentase dari waktu produksi yang dijadwalkan. Catat setiap peristiwa waktu henti, termasuk berapa lama itu terjadi dan apa penyebabnya.
Setelah Anda memiliki data, saatnya untuk memprioritaskan. Berapa banyak waktu henti yang datang langsung dari masalah peralatan? Kekurangan bahan? Operator tidak mengikuti prosedur yang benar? Apa pun itu, Anda harus menyingkirkan "pembunuh" downtime untuk mengurangi persentase downtime Anda secara keseluruhan. Misalnya, jika masalah peralatan menyebabkan sebagian besar waktu henti Anda, Anda sebaiknya berfokus pada bagaimana alat berat itu bekerja dan apa yang dapat dilakukan agar kinerjanya sesuai dengan sasaran produksi.
Not all factors can be mitigated, but it's a good idea to mitigate as much as you can.
Implement a More Stringent Process Control Monitoring System
A process control monitoring system must be in place to reduce unplanned downtime. This type of system aims to detect and prevent process conditions that could lead to downtime.
A good process control monitoring system will have the ability to:
- Detect process variations
- Identify trends and patterns
- Make comparisons between actual performance and desired performance
- Predict problems before they happen
It's important to note that a process control monitoring system isn’t a one-time fix. It needs to be continually monitored and tweaked as the manufacturing process changes. Downtime will always occur, but having a stringent process control system in place can minimize the chances of unplanned downtime.
Have a Solid Plan for Unexpected Employee Absences
When employees are out sick or on vacation, there's a good chance that your production line will be affected. To maintain consistent output levels when staff members are away from work, it's important to have a solid plan to ensure you have enough coverage to keep up production. Low production levels can add up over time and significantly impact your overall bottom line.
Some things you can do to prepare for unexpected employee absences include:
- Identifying key employees
- Developing a strong bench of backup staff
- Ensuring there is good communication between departments
While these steps can't eliminate unexpected employee absences, they can help reduce the fallout and ensure production continues as seamlessly as possible.
Make a Detailed Inspection Checklist
A poorly maintained machine will lead to more frequent breakdowns and unplanned downtime. To reduce this risk, have a detailed inspection checklist in place. A thorough and well-organized inspection checklist will help to ensure that all necessary inspections are performed and potential problems are identified and addressed quickly.
Creating a detailed inspection checklist can be a daunting task. Here are some tips to get you started:
- Break down the checklist into categories
- Group related items together
- Identify specific areas to inspect
- Use pictures or diagrams to help illustrate the areas you’re inspecting
Specific examples of things you should include on your inspection checklist are:
- Electrical wiring and components
These are only a few basic starting points - your inspection checklist should be as detailed as possible to suit your specific production process.
Don't Forget to Make Backups
We all know that accidents can happen and machines can break down unexpectedly. To reduce the impact of such an event, it's important to have a backup of your data, programs, and machine configurations. A backup can help you get back up and running quickly in the event of a problem.
There are a number of ways to make backups. One common and reliable method is to make backups using cloud-based services that securely store your files online. MachineMetrics offers this service through a cloud-based manufacturing software that ensures data reliability through backup and recovery solutions, meaning your data will always be protected from data loss.
Taking Action with Your Data
Many manufacturers do not have accurate downtime data. They’re unsure of the exact reasons or how much downtime is costing the company. Many manufacturers are experiencing a skills gap and stressed resources. Adding manual data collection, analysis, and reporting only strains employees and resources further. This is why enabling a downtime tracking solution is so important.
With the high cost of production and lack of accurate data, managers can’t make effective decisions to reduce unplanned downtime. Manufacturers must hone processes, reduce waste, and maximize machine utilization. MachineMetrics makes this possible without increasing already strained employees and resources. Our production monitoring software can give you insight into your downtime issues to improve processes and reduce unplanned downtime.
Start Reducing Your Downtime Today
Pesan Demo