Waktu henti hampir nol:Ikhtisar dan tren
1. Ikhtisar Teknologi Pemeliharaan:
Banyak perusahaan manufaktur mendorong peralatan produksi mereka untuk setiap ons kapasitas sementara, pada saat yang sama, mencoba untuk memotong biaya overhead mereka. Ini telah memberikan penekanan kuat pada pentingnya layanan pemeliharaan berkualitas yang digunakan untuk merawat sistem mereka. Layanan dan pemeliharaan menjadi penting bagi perusahaan untuk mempertahankan produktivitas manufaktur dan kepuasan pelanggan pada tingkat setinggi mungkin. Dukungan aftermarket produk semakin menjadi faktor kunci dalam menentukan profitabilitas dan ketergantungan suatu perusahaan. Pentingnya fungsi pemeliharaan, dan oleh karena itu manajemen pemeliharaan telah berkembang pesat.
Teknologi pemeliharaan bertujuan untuk
- Tingkatkan keandalan perangkat dan kurangi waktu henti produksi
- Meningkatkan throughput
- Meningkatkan harapan hidup aset
- Tingkatkan kondisi keamanan dan kualitas
Melihat kembali sejarah pengembangan dan meramalkan kecenderungan perkembangan teknologi pemeliharaan, peta jalan menuju keunggulan dalam pemeliharaan dapat diilustrasikan seperti pada Gambar 1.
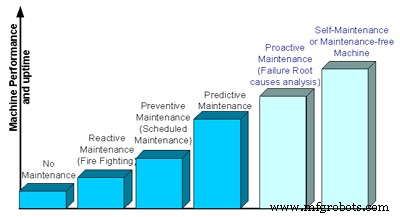
Gambar 1. Perkembangan teknologi pemeliharaan.
1.1 Tanpa Pemeliharaan
Ada dua jenis situasi di mana tidak ada pemeliharaan yang akan terjadi.
- Tidak ada cara untuk memperbaikinya:Teknik pemeliharaan tidak tersedia untuk beberapa aplikasi khusus, atau teknik pemeliharaan tidak dikembangkan dengan baik pada tahap awal.
- Tidak layak untuk memperbaikinya:Beberapa mesin dirancang untuk digunakan hanya sekali. Dibandingkan dengan biaya pemeliharaan, mungkin lebih hemat biaya jika membuangnya saja.
Tak satu pun dari skenario di atas berada dalam cakupan diskusi di sini.
1.2 Pemeliharaan Reaktif
Dalam bahasa Inggris yang sederhana, tujuan dari perawatan reaktif hanyalah untuk “memperbaikinya setelah rusak”, karena sebagian besar waktu mesin rusak tanpa peringatan dan sangat mendesak bagi kru perawatan untuk mengembalikannya bekerja. Ini juga disebut sebagai “pemadam kebakaran”.
Alasan terjadinya perawatan reaktif adalah karena beberapa operasi telah berkembang selama bertahun-tahun dengan sangat sedikit perhatian yang diberikan pada perawatan yang tepat dari mesin yang terlibat. Pada dasarnya, sedikit atau tidak ada perawatan yang dilakukan, dan mesin beroperasi sampai terjadi kegagalan. Pada saat ini, personel yang tepat dihubungi untuk menilai situasi dan melakukan perbaikan secepat mungkin. Oleh karena itu, Anda mendapatkan ungkapan "padam api" atau "pemadam kebakaran".
Dalam situasi di mana kerusakan peralatan bukan merupakan faktor kritis, karena banyak waktu henti tersedia, dan nilai aset tidak menjadi perhatian, mode pemadam kebakaran mungkin terbukti menjadi pilihan yang dapat diterima. Tentu saja, seseorang harus mempertimbangkan biaya tambahan untuk melakukan perbaikan secara darurat karena meminta tawaran untuk mendapatkan biaya yang wajar mungkin tidak berlaku dalam situasi ini. Karena persaingan pasar dan masalah lingkungan/keselamatan, trennya adalah penerapan program pemeliharaan yang terorganisir dan efisien dibandingkan dengan pemadaman kebakaran.
1.3 Pemeliharaan Pencegahan
Pemeliharaan preventif adalah strategi pemeliharaan peralatan berdasarkan penggantian, overhaul atau remanufaktur item pada interval tetap, terlepas dari kondisinya pada saat itu. Tugas Restorasi Terjadwal dan tugas Pembuangan Terjadwal keduanya merupakan contoh tugas pemeliharaan preventif.
Pemeliharaan preventif (PM) dapat dibagi menjadi dua kategori:
PM Kecil adalah perawatan dasar, yang merupakan tindakan melakukan servis peralatan yang paling mendasar (pelumasan, pembersihan, penyetelan rutin, dll.), yang penting untuk memastikan pengoperasian peralatan yang berkelanjutan. Kegiatan ini cukup sederhana hanya dengan beberapa mesin, downtime yang memadai dan dana yang cukup. Masalah mulai terjadi ketika ada banyak mesin dan tidak ada program yang terorganisir untuk menjadwalkan dan mengontrol tugas kerja. Solusinya adalah dengan menerapkan program pemeliharaan preventif kecil untuk memastikan bahwa kebutuhan dasar mesin ditangani secara tepat waktu dan efisien. Program tersebut memenuhi persyaratan minimum untuk melanjutkan operasi, tetapi tidak melakukan apa pun untuk mengantisipasi potensi kegagalan di masa mendatang.
PM Utama tidak hanya mencakup PM Kecil tetapi juga mulai menangani potensi kegagalan. Dengan opsi ini, mesin dijadwalkan tidak dapat digunakan sehingga tugas yang lebih terlibat dapat dilakukan. Berdasarkan jam kerja atau beberapa faktor waktu yang setara, komponen seperti bantalan, poros, sensor, roda gigi, perpipaan, dll., diganti untuk mengantisipasi potensi kegagalan dalam waktu dekat. Faktor waktu biasanya ditentukan melalui pengalaman dan bersifat statistik. Namun, dengan praktik ini, dimungkinkan untuk mengganti komponen yang masih dalam kondisi baik serta berisiko menimbulkan masalah melalui perawatan yang tidak tepat. Akibatnya, biaya terkadang dapat meningkat tanpa manfaat. Namun, PM Minor dan Mayor sangat penting untuk memastikan keandalan peralatan, sehingga kombinasi keduanya sering dilakukan.
1.4 Pemeliharaan Prediktif
Pemeliharaan prediktif (PdM) adalah strategi pemeliharaan tepat waktu. Pemeliharaan prediktif dapat digambarkan sebagai proses yang membutuhkan teknologi dan keterampilan orang, sambil menggabungkan dan menggunakan semua data diagnostik dan kinerja yang tersedia, riwayat pemeliharaan, catatan operator, dan data desain untuk membuat keputusan tepat waktu tentang persyaratan pemeliharaan peralatan utama/kritis. Integrasi berbagai data, informasi, dan proses inilah yang mengantarkan pada keberhasilan program PdM. Ini menganalisis tren parameter fisik yang diukur terhadap batas teknik yang diketahui untuk tujuan mendeteksi, menganalisis, dan memperbaiki masalah sebelum terjadi kegagalan. Rencana pemeliharaan dibuat berdasarkan hasil prediksi yang diperoleh dari pemantauan berbasis kondisi. Ini bisa lebih mahal di muka daripada PM karena perangkat keras pemantauan tambahan dan investasi perangkat lunak, awak, perkakas, dan pendidikan yang diperlukan untuk membuat program pemeliharaan prediktif. Namun, ia menawarkan peningkatan keandalan peralatan dan kemajuan informasi yang memadai untuk meningkatkan perencanaan, sehingga mengurangi waktu henti yang tidak terduga dan biaya pengoperasian.
Gambar 2 menunjukkan berbagai elemen program PdM yang terintegrasi untuk membantu dalam keputusan pemeliharaan.
*Sumber:Augustine DiGiovanni, Wakil Presiden Layanan CSI, Optimalisasi Pemeliharaan dengan Mengintegrasikan Teknologi dan Perubahan Proses
Gambar 2:Elemen program PdM.
Konsep utama PdM adalah:
- Gabungkan semua informasi
- Analisis informasi untuk degradasi peralatan
- Tentukan tindakan korektif
- Algoritme prediksi
- Tentukan kapan harus mengambil tindakan korektif
- Tindakan umpan balik yang diambil untuk riwayat pemeliharaan dan/atau analisis akar penyebab kegagalan
- Jadilah proaktif.
1.5 Pemeliharaan Proaktif
Pemeliharaan proaktif, secara umum, mencakup setiap tugas yang digunakan untuk memprediksi atau mencegah kegagalan peralatan. Untuk lebih spesifik, ada dua arah kerja.
- Ubah kegagalan reaktif menjadi kegagalan proaktif dengan menghindari kondisi dasar yang menyebabkan kesalahan dan degradasi mesin. Pemeliharaan proaktif berfokus pada analisis akar penyebab, dan bukan hanya gejalanya. Ini berusaha untuk mencegah atau memperbaiki kegagalan dari sumbernya setelah mengidentifikasi akar penyebabnya. Salah satu contoh paling populer dari perawatan proaktif menyangkut penyakit jantung dalam tubuh manusia. Untuk perawatan reaktif, respon hanya akan dilakukan setelah pasien dikirim ke ruang gawat darurat rumah sakit. Untuk pemeliharaan preventif, pasien mungkin menjalani operasi bypass atau transplantasi diikuti dengan pemeriksaan lanjutan. Untuk pemeliharaan prediktif, penyakit jantung dapat dideteksi menggunakan EKG atau teknologi ultrasonik dan mungkin pemasangan perangkat untuk pemantauan berkelanjutan. Untuk pemeliharaan proaktif, pengendalian penyakit akan melibatkan pemantauan kolesterol dan tekanan darah bersama dengan pengendalian diet.
- Umpankan informasi pemeliharaan kembali ke departemen desain dan operasi. Pencegahan kegagalan juga harus dilakukan di departemen desain dan operasi. Tugas kru pemeliharaan tidak hanya memperbaiki mesin atau mengganti suku cadang, tetapi mereka juga harus membantu dengan menyarankan cara meningkatkan desain dan pengoperasian mesin sehingga kegagalan dapat dicegah secara proaktif.
Masih ada beberapa perdebatan tentang efisiensi dan kecepatan respons kegagalan dari pemeliharaan proaktif, tetapi tidak diragukan lagi bahwa ada kekurangan komunikasi antara pemeliharaan dan desain
1.6 Perawatan diri
Self-maintenance adalah desain baru dan metodologi sistem. Mesin yang dapat merawat sendiri dapat memantau dan mendiagnosis dirinya sendiri, dan jika terjadi kegagalan atau degradasi apa pun, mesin tersebut masih dapat mempertahankan fungsinya untuk sementara waktu. Sebuah mesin pemeliharaan sendiri tidak termasuk dalam konsep pemeliharaan fisik konvensional, tetapi dalam konsep pemeliharaan fungsional. Pemeliharaan fungsional bertujuan untuk memulihkan fungsi yang diperlukan dari mesin yang rusak dengan menukar fungsi, sedangkan perbaikan tradisional (pemeliharaan fisik) bertujuan untuk memulihkan keadaan fisik awal dengan mengganti komponen yang rusak, pembersihan, dll. Cara untuk memenuhi fungsi pemeliharaan sendiri adalah dengan menambahkan kecerdasan ke mesin, membuatnya cukup pintar untuk pemeliharaan fungsional. Dengan kata lain, perawatan mandiri akan ditambahkan ke mesin yang ada sebagai sistem penalaran tambahan yang disematkan.
Pendekatan sistem lain untuk menciptakan kemampuan perawatan mandiri adalah dengan menambahkan fungsi pemicu layanan mandiri ke mesin. Mesin kemudian akan memantau sendiri, mendiagnosis sendiri, dan memicu sendiri permintaan servis dengan persyaratan perawatan yang terperinci dan jelas. Tugas pemeliharaan masih dilakukan oleh kru pemeliharaan, tetapi integrasi tanpa kesenjangan antara mesin, jadwal pemeliharaan, sistem pengiriman, dan sistem manajemen inventaris akan meminimalkan biaya pemeliharaan hingga batas maksimal dan meningkatkan kepuasan pelanggan ke tingkat tertinggi.
2. Dimana kita sekarang?
Sebagian besar industri manufaktur tradisional masih berjuang untuk mengurangi sifat pemadam kebakaran dari tugas pemeliharaan mereka. Salah satu produsen otomotif besar AS memiliki staf pemeliharaan antara 15.000 dan 18.000, di semua pabrik mereka digabungkan. Menurut mereka “85 persen sampai 90 persen [pekerjaan pemeliharaan mereka] adalah pekerjaan krisis” (breakdown). Beberapa perusahaan lain telah berhasil menerapkan program pemeliharaan preventif di pabrik mereka. Salah satu perusahaan pemasok suku cadang otomotif mengatakan bahwa hampir 80 persen tugas pemeliharaan mereka adalah pemeliharaan terjadwal dan hanya 20 persen yang merupakan pemadam kebakaran. Untuk sebagian besar industri manufaktur, rasio ideal pekerjaan terencana dan tidak terencana adalah 19:1, yang dianggap sebagai "kelas dunia" oleh banyak dari mereka. Jadi, jika sebuah perusahaan sudah mencapai tingkat 90 persen atau lebih tinggi untuk pemeliharaan terjadwal, dari sudut pandang penghematan biaya dan peningkatan produktivitas, apakah itu cukup baik? Sebenarnya, poin kunci di sini adalah apakah 90 persen dari pemeliharaan terjadwal diperlukan, yang mengarah ke topik diskusi utama kita:beralih dari pemeliharaan preventif ke pemeliharaan prediktif.
2.1 Pergeseran Dari Pemeliharaan Reaktif dan Pencegahan ke Pemeliharaan Prediktif
Pemeliharaan reaktif, dilakukan hanya ketika peralatan gagal, mengakibatkan biaya produksi yang tinggi dan waktu henti layanan yang signifikan yang disebabkan oleh kerusakan peralatan dan proses. Pemeliharaan preventif dimaksudkan untuk menghilangkan kerusakan mesin atau proses dan mengurangi waktu henti dengan menjadwalkan operasi pemeliharaan terlepas dari keadaan mesin atau proses yang sebenarnya. Interval perawatan preventif ditentukan menggunakan teori keandalan dan informasi tentang siklus hidup mesin atau proses.
Praktek ini sering mengakibatkan hilangnya produktivitas yang tidak perlu baik karena pemeliharaan dilakukan ketika proses atau mesin masih berfungsi pada tingkat yang dapat diterima, atau karena kerusakan yang tidak terduga terjadi sebelum operasi pemeliharaan terjadwal dilakukan. Menurut Majalah Forbes studi, satu dari setiap tiga dolar yang dihabiskan untuk pemeliharaan preventif terbuang sia-sia. Sebuah fasilitas perombakan besar-besaran melaporkan bahwa “60 persen pompa hidraulik yang dikirim untuk dibangun kembali tidak bermasalah dengan apa pun”. Inefisiensi tersebut merupakan akibat dari perawatan yang dilakukan sesuai dengan jadwal (fixed and guess work) yang bertentangan dengan kondisi dan kebutuhan mesin yang sebenarnya (fleksibel dan dinamis). Jadi, bahkan jika kita telah mencapai tingkat pemeliharaan preventif yang hampir sempurna, biayanya masih mewakili porsi yang cukup besar dari total biaya operasional, dan menyisakan banyak ruang untuk perbaikan dan penghematan biaya. Oleh karena itu, di pasar kontemporer, menjadi semakin penting untuk memprediksi dan mencegah kegagalan berdasarkan perilaku peralatan saat ini dan masa lalu, sehingga memastikan pemeliharaannya hanya saat dibutuhkan dan tepat saat dibutuhkan.
Perawatan preventif selalu dibandingkan dengan jadwal servis mobil. Jika Anda mengganti oli di mobil Anda setiap 3.000 mil apakah perlu atau tidak, Anda mengikuti kebijakan perawatan pencegahan. Perawatan prediktif adalah ketika Anda mengambil sampel oli dari waktu ke waktu dan memeriksa setiap perubahan karakteristiknya dan membuat prediksi kapan kendaraan Anda harus diservis. Anda mungkin mengetahui bahwa Anda perlu mengganti oli lebih sering, atau Anda dapat terus mengemudi sejauh ribuan mil tanpa menggantinya. Dengan menggunakan teknik perawatan yang lebih akurat ini, Anda tidak hanya akan merawat mobil dengan lebih baik, tetapi juga mengurangi biaya dengan menghindari servis yang tidak perlu.
Untuk alasan ini, kami mengusulkan perubahan paradigma dari pendekatan tradisional untuk mendeteksi dan mengukur kegagalan menuju pendekatan yang berpusat pada mendeteksi, mengukur dan memprediksi penurunan kinerja suatu proses, mesin, atau layanan. Penurunan kinerja adalah pertanda kegagalan sistem, sehingga dapat memprediksi kinerja sistem yang tidak dapat diterima (dalam suatu proses, mesin atau layanan) sebelum terjadi. Dengan demikian, praktik gagal-dan-perbaikan tradisional dapat digantikan oleh proses prediksi-dan-pencegahan yang baru.
2.2 Manfaat Pemeliharaan Prediktif
Manfaat pemeliharaan prediktif dapat dikategorikan sebagai berikut:
1. Tingkatkan produktivitas
- Meminimalkan atau menghilangkan waktu henti yang mahal dan meningkatkan waktu kerja yang menguntungkan.
- Mengurangi pemeliharaan tak terjadwal – perbaikan dapat dilakukan pada waktu yang paling tidak mempengaruhi produksi.
- Mengoptimalkan kinerja mesin – mesin selalu beroperasi sesuai spesifikasi.
- Mengurangi waktu yang diperlukan untuk melakukan perbaikan mesin – pemberitahuan sebelumnya tentang kondisi mesin memungkinkan pengaturan proses perbaikan yang lebih efisien.
- Mengurangi waktu lembur yang diperlukan untuk mengganti produksi yang hilang karena mesin yang rusak atau berkinerja buruk.
- Meningkatkan kecepatan agar mesin dapat dioperasikan, jika diinginkan.
- Meningkatkan kemudahan pengoperasian mesin.
2. Kurangi biaya keseluruhan
- Mengurangi perbaikan mesin yang tidak perlu – mesin diperbaiki hanya jika kinerjanya kurang optimal.
- Mengurangi persediaan suku cadang – banyak suku cadang dapat dibeli tepat pada waktunya untuk perbaikan yang akan dilakukan selama penghentian mesin yang dijadwalkan.
- Mengurangi depresiasi investasi modal yang disebabkan oleh perawatan mesin yang buruk – mesin yang dirawat dengan baik akan bertahan lebih lama dan berkinerja lebih baik.
- Mengurangi konsumsi daya listrik yang berlebihan yang disebabkan oleh kinerja mesin yang tidak efisien – menghemat uang untuk kebutuhan energi.
- Mengurangi kebutuhan akan peralatan siaga atau ruang lantai tambahan untuk menutupi waktu henti yang berlebihan – lebih sedikit investasi modal yang diperlukan untuk peralatan atau pabrik.
3. Hubungan pelanggan yang lebih baik dan tingkat kepuasan
- Mengurangi jumlah pelanggan yang tidak puas atau kehilangan pelanggan karena kualitas yang buruk – dengan kinerja alat berat yang kurang optimal, kualitas selalu menurun.
- Layanan tepat waktu mengurangi waktu tunggu dan waktu henti pelanggan.
- Kemungkinan mengidentifikasi permintaan layanan sebelum pelanggan mengetahui masalahnya.
- Mengurangi penalti akibat keterlambatan pengiriman yang disebabkan oleh mesin yang rusak atau berkinerja buruk.
- Mengurangi klaim garansi karena kualitas produk yang buruk yang disebabkan oleh kinerja mesin yang buruk.
4. Meningkatkan keamanan mesin
- Mengurangi cedera yang disebabkan oleh kinerja mesin yang buruk.
- Mengurangi hukuman keselamatan yang dikenakan terhadap perusahaan untuk mesin yang tidak aman.
- Mengurangi tarif asuransi karena mesin yang dirawat dengan baik meningkatkan keselamatan.
2.3 Persyaratan untuk Pemeliharaan Prediktif
Untuk menerapkan teknologi pemeliharaan prediktif, dua investasi harus dipertimbangkan oleh grup manajemen:
- Investasi dalam peralatan pemantauan dan diagnostik berbasis kondisi.
- Investasi dalam pelatihan staf
3. Metodologi Pemeliharaan Prediktif
3.1 Pemantauan dan Penilaian Kinerja Berbasis Kondisi
Dasar pemeliharaan prediktif adalah pemantauan berbasis kondisi. Tanpa terus-menerus memeriksa status pengoperasian alat berat dan melacak kecenderungannya untuk mengalami degradasi, tidak mungkin membuat rencana perawatan prediktif yang tepat.
Ada lusinan teknologi pemeliharaan prediktif yang dibangun berdasarkan pemantauan berbasis kondisi atau mekanisme pengujian konstan, dan beberapa telah menjadi standar di banyak industri. Teknologi standar dan banyak digunakan tersebut meliputi analisis getaran, analisis oli, analisis partikel aus, ultrasound, termografi, dan analisis emisi akustik. Tabel berikut menunjukkan cara profesional pemeliharaan secara tradisional menggunakan teknologi prediktif ini untuk aplikasi yang berbeda.
Metode Deteksi
Mode Kegagalan
Peralatan
Analisis Getaran
Tidak Saldo
Ketidaksejajaran
Cacat Bantalan
Gear Cacat
Turbulensi
Mesin Berputar
Analisis Oli dan Partikel Keausan
Kegagalan Pelumasan
Keausan Tidak Normal
Komponen Mekanik
Ultrasound
Kavitasi
Deteksi Kebocoran
Koneksi Lepas
Pelepasan Corona
Cacat Bantalan
Pompa Hidrolik
Sistem Udara/Uap/Vakum
Distribusi Daya
Saklar Listrik dan Transmisi Overhead
Bantalan
Termografi
Komponen Panas Tidak Normal
Komponen Listrik
Komponen Mekanik
Komponen Struktural
Emisi Akustik
Analisis
Retak Stres
Penahanan
dan Peralatan Transfer
Analisis getaran digunakan terutama dengan mesin yang berputar untuk menemukan masalah seperti cacat bantalan, kondisi tidak seimbang, dan ketidaksejajaran. Sebelum menggunakan analisis getaran, teknisi perawatan harus menunggu sampai bantalan gagal menyadari bahwa ada masalah. Namun, dengan menggunakan analisis getaran, pembacaan periodik dapat dilakukan dan direkam. Personel pemeliharaan kemudian dapat membandingkan pembacaan ini dengan pembacaan dasar. Ketika keausan mencapai tingkat tertentu, bantalan dijadwalkan untuk diganti sebelum rusak. Ini mengurangi jumlah perawatan reaktif dan memastikan penggantian terjadi dengan dampak minimal pada jadwal produksi atau fasilitas. Pada mesin berputar besar, sistem pemantauan kondisi online telah diadopsi secara luas. Informasi getaran dari setiap bagian bantalan dikumpulkan dan kinerja alat berat saat ini dievaluasi berdasarkan itu. Selanjutnya, pemeliharaan di masa mendatang dijadwalkan sesuai dengan evaluasi tersebut dan prediksi kinerja mesinnya. Dengan begitu, mesin hanya akan dibuka saat benar-benar diperlukan.
Analisis getaran juga digunakan untuk mendiagnosis beberapa masalah non-mekanis dalam sistem tenaga fluida dan gangguan lonjakan atau eksitasi fluida pada kompresor sentrifugal besar. Misalnya, pembatasan atau gangguan dalam sistem penanganan cairan menciptakan turbulensi dan getaran unik yang dapat membantu mengidentifikasi masalah.
Ultrasound digunakan terutama untuk deteksi kebocoran, terutama untuk kebocoran uap dan udara. Kebocoran ini bisa mahal, namun banyak perusahaan membiarkannya tidak diketahui.
Aplikasi umum untuk ultrasound termasuk deteksi kebocoran untuk pneumatik dan sistem gas lainnya, sistem vakum, gasket dan seal, dan steam trap. Ultrasound juga mendeteksi kebocoran katup dan juga merupakan cara paling umum untuk mendeteksi masalah kavitasi pada pompa hidraulik.
Ultrasound juga digunakan untuk pemeriksaan switchgear listrik dan saluran transmisi overhead, di mana pemeriksaan rutin memakan waktu dan berbahaya. Area ini dipantau untuk pelepasan korona, dan ketika instrumen "mendengar" pelepasan, teknisi dapat dengan cepat menemukan masalah dengan sedikit waktu yang terbuang. Dengan demikian, teknisi dapat menemukan masalah kecil sebelum menjadi kritis dan menyebabkan kegagalan peralatan.
Analisis Oli dan Partikel Aus adalah dua teknologi berbeda yang banyak digunakan untuk mendeteksi kesalahan terkait pelumasan. Analisis oli menentukan kondisi pelumas. Analisis partikel aus menentukan kondisi peralatan berdasarkan konsentrasi partikel aus dalam pelumas.
Misalnya, pertimbangkan kotak roda gigi yang menunjukkan tanda-tanda keausan yang tidak normal (mis., kebisingan atau panas berlebih). Sampel oli dapat diperiksa untuk partikel aus. Mempertimbangkan jenis dan kondisi partikel yang ditemukan, dimungkinkan untuk mengisolasi sejumlah kemungkinan masalah dan penyebabnya (misalnya, mengoperasikan peralatan di luar kecepatan desain atau kapasitas atau kegagalan filter). Setelah masalah diidentifikasi, tindakan pemeliharaan yang sesuai dapat dijadwalkan, sekali lagi dengan dampak minimal pada operasi atau fasilitas.
Beberapa aplikasi unik akan melibatkan analisis pelumas itu sendiri atau partikel keausan dalam pelumas. Misalnya, partikel keausan dapat terlihat saat pelumasan tidak mencukupi. "Pelumasan tidak mencukupi" tidak berarti tidak adanya pelumas dalam suatu sistem. Sistem pelumasan pada drive tertutup, misalnya, dapat memiliki nozzle semprotan yang tersumbat, mencegah pelumasan yang tepat mencapai area yang sulit diperiksa. Sementara bagian drive yang terlihat mungkin mendapatkan pelumasan yang tepat, area lain yang kurang pelumasan akan menghasilkan partikel keausan yang menunjukkan kondisi tersebut. Sampel juga dapat menunjukkan kondisi seperti kegagalan aditif, kontaminasi pelumas, atau pemuatan berlebihan yang melebihi nilai pelumas.
Termografi digunakan terutama untuk menemukan komponen listrik yang lebih panas dari biasanya. Kondisi seperti itu biasanya menunjukkan keausan atau kelonggaran. Dengan demikian, termografi memungkinkan teknisi untuk melakukan perawatan hanya pada komponen listrik yang memerlukan perhatian tanpa mengharuskan semua komponen mendapatkan tingkat perhatian yang sama.
Dalam utilitas, misalnya, torsi yang benar sangat penting pada komponen listrik untuk memastikan bahwa tidak ada panas yang dihasilkan dari sambungan yang longgar. Sebelum termografi, setiap sambungan di panel kontrol harus diperiksa secara manual untuk torsi yang benar. Dengan menggunakan termografi, hanya sambungan yang panas yang mendapat perhatian. Ini mengurangi staf yang diperlukan untuk melakukan pemeliharaan preventif pada koneksi.
Aplikasi lain termasuk pemantauan kabel luar ruangan, seperti saluran transmisi overhead, yang aus karena kondisi lingkungan. Termografi juga berfungsi untuk mengukur suhu transformator untuk menemukan masalah yang ditunjukkan ketika area tertentu lebih panas dari yang lain. Selain itu, mendukung pemeliharaan di industri yang memiliki proses suhu tinggi. Teknologi ini membantu menentukan area di mana bahan tahan api mengalami keausan dan memungkinkan perbaikan sebelum terjadi kegagalan besar.
Aplikasi termografi lain yang jarang digunakan adalah memeriksa keselarasan kopling tanpa mematikan peralatan secara besar-besaran. Saat kopling yang tidak sejajar berputar, itu menghasilkan panas. Semakin besar perbedaan suhu, semakin besar misalignment. Dengan menggunakan termografi, personel pemeliharaan dapat mengamati kenaikan suhu di seluruh kopling. Beberapa perusahaan telah menggunakan teknik ini cukup lama untuk mengembangkan profil kenaikan suhu untuk setiap jenis kopling. Dengan menggunakan profil ini, mereka dapat menentukan jumlah ketidaksejajaran (bukan pada bidang apa). Kemudian, teknisi dapat secara proaktif menjadwalkan kopling untuk penyelarasan kembali.
Emisi akustik (AE) analisis adalah kelas fenomena di mana gelombang elastis, dalam kisaran ultrasonik biasanya antara 20 kilohertz dan 1 megahertz, dihasilkan oleh pelepasan energi yang cepat dari sumber di dalam material. Gelombang elastis merambat melalui padatan ke permukaan, di mana ia dapat direkam oleh satu atau lebih sensor. Sensor adalah transduser yang mengubah gelombang mekanik menjadi sinyal listrik. Dengan cara ini, informasi tentang keberadaan dan lokasi kemungkinan sumber suara diperoleh. Dasar dari metode kuantitatif adalah teknik lokalisasi untuk mengekstrak koordinat sumber kejadian AE seakurat mungkin.
Analisis AE berbeda dari pengujian ultrasonik, yang secara aktif menyelidiki struktur. Analisis AE mendengarkan emisi dari cacat aktif dan sangat sensitif terhadap aktivitas cacat saat struktur dibebani melebihi beban layannya dalam uji bukti.
Analisis AE adalah metode yang berguna untuk investigasi kerusakan lokal pada material. Salah satu keunggulannya dibandingkan teknik NDE lainnya adalah potensinya untuk dapat mengamati proses yang rusak selama seluruh riwayat beban tanpa gangguan pada spesimen.
Analisis AE berhasil digunakan dalam berbagai aplikasi termasuk:mendeteksi dan menemukan kesalahan pada bejana tekan atau kebocoran pada tangki penyimpanan atau sistem pipa, memantau aplikasi pengelasan, proses korosi, pelepasan sebagian dari komponen yang mengalami tegangan tinggi dan pelepasan lapisan pelindung. Area di mana penelitian dan pengembangan aplikasi AE saat ini sedang dilakukan, antara lain, pemantauan proses dan pemantauan jangka panjang global atau lokal dari struktur teknik sipil (misalnya, jembatan, jaringan pipa, platform lepas pantai, dll.). Area lain di mana banyak aplikasi AE telah dipublikasikan adalah komposit matriks polimer yang diperkuat serat, khususnya bagian atau struktur yang diperkuat serat kaca (misalnya, bilah kipas). Sistem AE juga memiliki kemampuan mendeteksi sinyal akustik yang dihasilkan oleh kebocoran.
Kerugian dari analisis AE adalah bahwa sistem AE komersial hanya dapat memperkirakan secara kualitatif berapa banyak kerusakan yang terjadi pada material dan kira-kira berapa lama komponen akan bertahan. Oleh karena itu, masih diperlukan metode NDE lain untuk melakukan pemeriksaan yang lebih teliti dan memberikan hasil yang kuantitatif. Selain itu, lingkungan layanan umumnya sangat bising, dan sinyal AE biasanya sangat lemah. Dengan demikian, diskriminasi sinyal dan pengurangan noise sangat sulit, namun sangat penting untuk aplikasi AE yang sukses.
3.2 Agen Pengawas
Saat ini, pendekatan pemeliharaan berbasis kondisi (CBM) yang lazim melibatkan memperkirakan kondisi mesin saat ini berdasarkan pengenalan indikasi kegagalan. Baru-baru ini, beberapa teknik CBM prediktif dalam paradigma yang berpusat pada kegagalan ini telah diusulkan. Meskipun pendekatan ini, untuk menerapkan teknik CBM prediktif yang disebutkan di atas memerlukan keahlian dan pengetahuan sebelumnya tentang mesin atau proses yang dinilai karena mode kegagalan yang sesuai harus diketahui untuk menilai kinerja mesin atau proses saat ini. Karena alasan ini, metode CBM yang disebutkan di atas bersifat khusus untuk aplikasi dan tidak kuat.
Pusat Sistem Pemeliharaan Cerdas mengusulkan paradigma CBM baru untuk penilaian dan prediksi kinerja berdasarkan Agen Pengawas. Pendekatan baru ini didasarkan pada pemanfaatan informasi terkait kinerja yang diperoleh dari tanda tangan yang diekstraksi dari beberapa input sensor melalui pemrosesan sinyal generik, ekstraksi fitur, dan teknik fusi sensor. Penilaian kinerja dalam hal ini dibuat berdasarkan pencocokan tanda tangan yang mewakili kinerja terbaru dengan yang diamati selama perilaku sistem normal. Kecocokan yang erat antara tanda tangan ini akan menunjukkan kinerja yang baik, sementara perbedaan yang lebih besar di antara mereka akan menunjukkan penurunan kinerja dan kebutuhan akan pemeliharaan.
Karena tidak ada data kegagalan yang diperlukan agar teknik CBM ini dapat beroperasi, dan karena sifat metode yang digunakan adalah generik, kebutuhan akan pengetahuan ahli sangat berkurang. Namun, jika data kegagalan yang menjelaskan beberapa mode kegagalan tersedia, tanda tangan proses terbaru juga dapat dicocokkan dengan tanda tangan terkait kegagalan tersebut dengan hasil yang cocok dengan informasi diagnostik yang signifikan.
Figure 3 illustrates this CBM technique centered on describing and quantifying the process degradation instead of process failure. Finally, historical behavior of process signatures can be utilized to predict their behavior and thus forecast the process performance. Based on the forecasted performance, proactive maintenance is possible through the prediction of process degradation and prevention of potential failure before it occurs. Thus, the Watchdog Agent is enabled to yield the information about when unacceptable system performance will occur, why the performance degradation occurred and what component in the system needs to be maintained. This information will ultimately lead to optimal maintenance policies and actions that will proactively prevent downtime.
This entire infrastructure of multi-sensor performance assessment and prediction could be even further enhanced if Watchdog Agents mounted on identical products operating under similar conditions could exchange information and thus assist each other in building a world model. Furthermore, this communication can be used to benchmark the performance of “brother-products” and thus rapidly and efficiently identify underperforming units before they cause any serious damage and losses. This paradigm of communication and benchmarking between identical products operating in similar conditions is referred to as the “peer-to-peer” (P2P) paradigm. Figure 8 illustrates the aforementioned Watchdog Agent functionalities supported by the P2P communication and benchmarking paradigm.
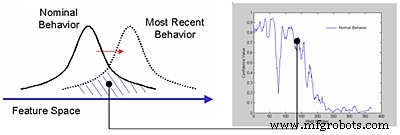
Figure 3:Performance assessment based on the overlap between signatures.
According to the standard for Open System Architecture for Condition-Based Maintenance (OSA-CBM), a typical CBM system consists of the following seven layers:
• Sensor module
• Signal processing
• Condition monitoring
• Health assessment
• Prognostics
• Decision-making support
• Presentation
The Watchdog functionality expands this standard topology to a multi-sensor level and realizes sensory processing, condition monitoring, health assessment and prognostics layers of the CBM scheme. The sensors and decision making layers within an Intelligent Maintenance System are realized outside the Watchdog Agent.
Conclusion
In today’s competitive market, production costs, lead time and optimal machine utilization are crucial issues for companies. Near-zero-downtime is the goal for a maintenance crew to maintain a company’s throughput and high productivity. Reactive maintenance, performed only when equipment fails, results in both high production costs and significant service downtime caused by equipment and process breakdowns. Preventive maintenance is intended to eliminate machine or process breakdowns and downtimes through maintenance operations scheduled regardless of the actual state of the machine or process. Therefore, in contemporary markets, it becomes increasingly important to predict and prevent failures based on the current and past behavior of the equipment, thus ensuring its maintenance only when needed and exactly when needed.
For these reasons, the shift from the traditional reactive maintenance and preventive maintenance to predictive maintenance should be the development direction of maintenance technology. Based on the condition-based monitoring technology, the traditional fail-and-fix practice can and eventually must be replaced by the new predict-and-prevent paradigm.
About the authors:
Hai Qiu and Jay Lee help direct the NSF Industry/University Cooperative Research Center on
Intelligent Maintenance Systems (IMS) at the University of Cincinnati. To learn more, visit www.imscenter.net.
References:
- Sandy Dunn, Condition monitoring in the 21 st century, http://www.plant-maintenance.com/articles/ConMon21stCentury.shtml
- Plant Maintenance Resource Center , 2002 Condition Monitoring Survey Results, http://www.plant-maintenance.com/articles/condition-monitoring-survey-02.shtml
- Robert J., Maintaining the bottom line, http://www.ecmweb.com/ar/electric_maintaining_bottom_line/
- J S Rao, Vibratory Condition Monitoring of Machines, CRC press 2000, ISBN 0849309379
- Bertele, Otto V. "Why Condition Monitor?" 3rd International Conference on Condition Monitoring. October 15-16, 1990.
- Bengtsson, M., 2002, Condition Based Maintenance on Rail Vehicles”, IDPMTR 02:06.
- Chris Davies, The use of Information Systems in Fault Diagnosis, http://www.bin95.com/download/Information_Systems_in_Fault_Diagnosis.pdf
- Don Fitchett, What is the True Downtime Cost (TDC)?, http://www.afestlouis.org/Download/True_Downtime_Cost.pdf
- L.Swanson, The impact of new production technologies on the maintenance function:an empirical study., International journal of production research, vol.37, No.4, pp849-869, 1999.
- Andy Foerster, A new age of remote monitoring and control, http://www.ecmweb.com/ar/electric_new_age_remote/
- Mark Lamendola, What’s new in remote predictive monitoring, http://www.ecmweb.com/ar/electric_whats_new_remote/
- SpectraQuest, Inc. http://www.spectraquest.com/
- Haynes, C J, Scheduling power plant maintenance using performance data, ASME paper 86-JPGC-PWR-63
- Ray Beebe, predictive maintenance by performance monitoring of plant, http://www.goldson.free-online.co.uk/techart/MFPT52.htm
- Michael V. Brown, Applying the predictive approach, http://www.newstandardinstitute.com
- William C. Worsham, Is preventive maintenance necessary?, http://www,reliability.com/articles/article37.htm
- Christer Idhammar, CMMS and preventive maintenance, http://www.idcon.com/articles/cmms.htm
- Susan Owen, Proactive power monitoring enhances preventive maintenance, http://www.ecmweb.com/ar/electric_proactive_power_monitoring/
- What is Proactive Maintenance, http://www.maintenanceresources.com/ReferenceLibrary/OilAnalysis/oa-what.htm
- James C. Fitch, P.E., Proactive Maintenance can Yield More than a 10-Fold Savings Over Conventional Predictive/Preventive Maintenance Programs, http://www.maintenanceresources.com/ReferenceLibrary/OilAnalysis/oa-pm.htm
- Daryl Mather, Fundamentals of Maintenance Planning:Planning and Scheduling, http://www.maintenanceworld.com/Articles/Mather/planning_scheduling.htm
- Dibyendu De, Productivity Improvement Through Operational Reliabilty and Knowledge Workers, http://www.maintenanceworld.com/Articles/Dibyendu/deb1.htm
- Plant Maintenance Resource Center , Maintenance Benchmarking Database:Overall Results, http://www.plant-maintenance.com
- Augustine DiGiovanni, Maintenance Optimization by Integrating Technologies and Process Change, http://www.compsys.com/enews/knewspro.nsf/v/ADIT-55JN86
- The Benefits of Predictive Maintenance:A-Z, http://www.maintenanceresources.com/ReferenceLibrary/PredictiveMaintenance/tbopm.htm
- Robert Edae, The importance of predictive maintenance, http://www.newsteel.com/features/NS9709f5.htm
- Lee, J. &Wang, Ben, (1999) Computer-aided Maintenance:methodologies and practices, Kluwer Academic Publishing.
- Lee, J. 1995. Machine performance monitoring and proactive maintenance in computer integrated manufacturing:Review and perspective. International Journal for Computer Integrated Manufacturing 8(5):370–380.
- NSF I/ UCRC Center for Intelligent Maintenance Systems, http://www.imscenter.net
- D. Djurdjanovic, J. Ni and J. Lee, “Time-Frequency Based Sensor Fusion in the Assessment and Monitoring of Machine Performance Degradation”, to appear in the Proc. of 2002 ASME Int. Mechanical Eng. Congress and Exposition, paper number IMECE2002-32032
- Thurston, M. and Lebold, M., 2001, “OpenStandards for Condition Based Maintenance and Prognostic Systems”, Pennsylvania State University, Applied Research Laboratory.