Reliability Centered Maintenance:5 Kunci Dasar RCM yang Efektif
Reliability Centered Maintenance (RCM) adalah pendekatan perawatan lanjutan yang digunakan untuk mencegah kegagalan besar pada peralatan yang banyak digunakan dan penting. Beberapa industri, seperti minyak dan gas, menggunakan prinsip-prinsip RCM untuk menjaga infrastruktur mereka yang luas tetap beroperasi dengan lancar. Mengelola keandalan peralatan fasilitas bukanlah konsep baru, tetapi ada beberapa alat modern yang tersedia untuk mendukung upaya ini.
Bagian dari pemeliharaan yang berpusat pada keandalan adalah manajemen berbasis kondisi (CBM), yang menggunakan kriteria operasi yang ditentukan untuk setiap alat sebagai tolok ukur kinerja. Dalam posting ini, kita akan mengeksplorasi lima dasar utama untuk menjalankan program RCM yang efektif. Rekomendasi ini dapat digunakan selama fase perencanaan, pelaksanaan, dan peningkatan untuk merampingkan pendekatan Anda terhadap manajemen pemeliharaan.
Apa itu Pemeliharaan Berpusat Keandalan?
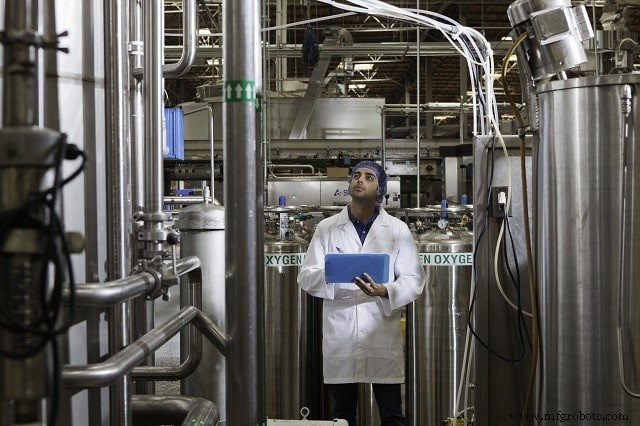
Pemeliharaan yang berpusat pada keandalan adalah praktik yang memprioritaskan pekerjaan berdasarkan kemungkinan kegagalan peralatan. Tujuan dari program RCM adalah untuk melindungi aset yang dapat menyebabkan gangguan parah jika terjadi kegagalan atau pemadaman. Pendekatan ini membantu manajemen memprioritaskan pekerjaan pemeliharaan yang sesuai dan memanfaatkan sumber daya secara efisien. Empat elemen kunci dari program RCM adalah:
- Mengidentifikasi titik kegagalan untuk setiap aset
- Berfokus pada pemeliharaan fungsi aset
- Memperingkat aset berdasarkan mode kegagalan
- Membuat strategi pemeliharaan untuk setiap aset individual
Program RCM adalah pendekatan yang sangat terfokus yang paling sering digunakan untuk aset bernilai tinggi dan penting. TI mungkin tidak berguna untuk subsistem dan aset dengan prioritas lebih rendah karena sifat analisis kegagalan dan tindak lanjut yang intensif. Pemeliharaan yang berpusat pada keandalan adalah pilihan yang bagus untuk digunakan dengan pendekatan lain, seperti pemeliharaan preventif dan pemeliharaan prediktif, sebagai bagian dari program pemeliharaan di seluruh perusahaan.
1. Tentukan Kondisi Batas untuk Sistem Terkait
Sepotong peralatan jarang ada dalam ruang hampa penuh. Saat meninjau sistem fasilitas Anda, selalu bermanfaat untuk mempertimbangkan fungsi peralatan dan input dan output yang terhubung. Ini mungkin termasuk jalur pasokan fasilitas untuk listrik, udara, air, atau bahan lainnya. Melakukan latihan ini akan membantu Anda memutuskan bagaimana menetapkan setiap bagian dari peralatan fasilitas ke sistem terkait. Setelah sistem didefinisikan, dimungkinkan untuk sepenuhnya menganalisis masing-masing sistem menggunakan prinsip RCM.
2. Jangan Terlalu Fokus pada Kegagalan Terkait Usia
Ini mungkin mengejutkan, tetapi penyebab kegagalan sistem peralatan adalah acak dalam banyak kasus dan tidak disebabkan oleh penurunan terkait usia. Misalnya, data dari industri penerbangan telah menunjukkan bahwa antara 70-90% mode kegagalan tidak berkaitan dengan usia. Hal ini penting ketika merencanakan kegiatan RCM karena alat ini dapat mengambil manfaat dari pemantauan berbasis kondisi. Pemantauan secara real-time akan segera menunjukkan titik kegagalan dan tidak membiaskan potensi kerusakan berdasarkan usia aset.
3. Identifikasi Potensi Kegagalan Fungsional
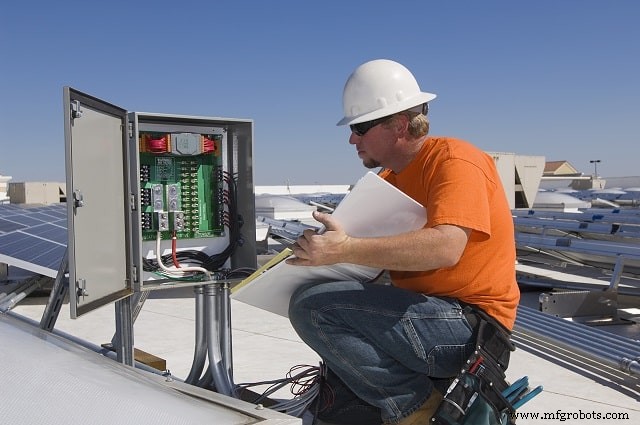
Salah satu cara terbaik untuk melindungi kinerja aset adalah dengan menentukan titik kegagalan yang potensial. Mode kegagalan dan analisis efek (FMEA) adalah salah satu contoh alat yang dapat digunakan untuk menentukan beberapa mode kegagalan yang kemudian dapat dikurangi. Saat meninjau titik kegagalan ini, akan sangat membantu untuk menentukan rentang operasi untuk parameter penting. Rentang operasi akan memberi Anda pengukuran nyata yang menentukan potensi kegagalan saat nilai bergerak di luar rentang tersebut.
4. Pilih Solusi Perawatan Berdasarkan Mode Kegagalan
Karena pendekatan RCM akan memprioritaskan mode kegagalan untuk setiap sistem peralatan, pendekatan ini juga dapat digunakan untuk memilih solusi perawatan yang sesuai. Dalam beberapa kasus, monitor in-line dapat digunakan sebagai solusi berbasis kondisi, atau jadwal pemeliharaan preventif dapat diikuti untuk mengganti bahan habis pakai umum dan mengikuti tugas pemeliharaan rutin untuk menjaga peralatan dalam kondisi kerja yang optimal. Sistem Manajemen Pemeliharaan Terkomputerisasi (CMMS) adalah sumber yang sangat baik untuk merencanakan dan mengatur pekerjaan ini. Digabungkan dengan tag aset manajemen fasilitas untuk menyederhanakan dokumentasi dan memantau penggunaan dan kondisi peralatan, alat ini mendukung program RCM yang efektif.
5. Mengadopsi Kerangka Proyek RCM yang Terbukti
Setiap program pemeliharaan akan mendapat manfaat dari organisasi yang lebih baik. Mengingat kompleksitas banyak sistem fasilitas, menggunakan CMMS yang dikombinasikan dengan kerangka kerja yang telah terbukti dapat membantu mengatasi beberapa masalah umum. Kerangka kerja proyek RMC dapat dijelaskan dalam 4 langkah umum.
- Pilih rencana berdasarkan hasil yang diinginkan
- Menganalisis data peralatan
- Terapkan peningkatan pemeliharaan
- Ukur manfaat yang sebenarnya dan buat perubahan yang diperlukan
Proses ini paling baik dipahami sebagai loop yang dapat diulang secara teratur untuk meningkatkan keputusan pemeliharaan berdasarkan data terbaru yang tersedia.
Pemeliharaan yang berpusat pada keandalan adalah pendekatan yang sangat baik untuk perusahaan yang mengelola aset penting dan bernilai tinggi dengan persyaratan kinerja yang menuntut. Saat mempelajari prinsip-prinsip RCM, ada baiknya berkonsultasi dengan beberapa sumber daya untuk membuat rencana komprehensif yang paling sesuai untuk organisasi, tim, dan peralatan Anda. Kami berharap dasar-dasar dalam postingan ini akan membantu Anda merampingkan praktik manajemen pemeliharaan.