Praktik Terbaik Operasi Gudang:55 Tip dan Taktik Luar Biasa untuk Meningkatkan Manajemen, Organisasi, dan Operasi Gudang
Manajer gudang tahu betul bahwa tugas mengelola operasi untuk fasilitas gudang jauh dari mudah. Manajer operasi gudang ditugaskan untuk memastikan aliran produk yang efisien masuk dan keluar dari fasilitas, mengoptimalkan tata letak bangunan, memastikan pesanan terpenuhi dan produk tersedia, tetapi tidak kelebihan stok. Tambahkan memastikan profitabilitas dan meminimalkan biaya overhead dan tenaga kerja ke dalam campuran, dan operator gudang memiliki pekerjaan yang tepat untuk mereka.
Dengan begitu banyak faktor yang harus diseimbangkan, pertimbangan untuk dipertimbangkan dalam setiap keputusan, dan tekanan dari pemangku kepentingan di semua sisi untuk menjadi lebih produktif, meminimalkan pengeluaran, dan menjaga kelancaran aliran rantai pasokan, tidak mengherankan jika ada banyak artikel dan sumber daya yang menguraikan praktik terbaik untuk operasi gudang.
Untuk menganalisis beragam informasi tentang praktik terbaik operasi gudang, kami telah mengumpulkan daftar praktik terbaik yang relatif ringkas dari berbagai sumber. Kami telah menjelajahi pelosok web untuk mengidentifikasi 51 praktik terbaik ini untuk operasi gudang guna menyediakan sumber daya yang berguna bagi manajer gudang yang ingin menjadi yang berkinerja terbaik di bidangnya dan menghasilkan hasil terbaik bagi perusahaan mereka. Meskipun dikategorikan berdasarkan topik, harap perhatikan bahwa praktik terbaik berikut tidak dinilai atau diberi peringkat dalam urutan kepentingan tertentu. Untuk melompat ke bagian tertentu, gunakan tautan dalam daftar isi di bawah ini.
55 Praktik Terbaik Operasi Gudang
Daftar Isi:
- Praktik Terbaik Pelacakan Aset untuk Operasi Gudang
- Praktik Terbaik Logistik Operasi Gudang
- Manajemen Keselamatan dan Risiko dalam Operasi Gudang
- Mengoptimalkan Alur Kerja Operasi Gudang
- Praktik Terbaik untuk Meningkatkan Manajemen Inventaris
Praktik Terbaik Pelacakan Aset untuk Operasi Gudang
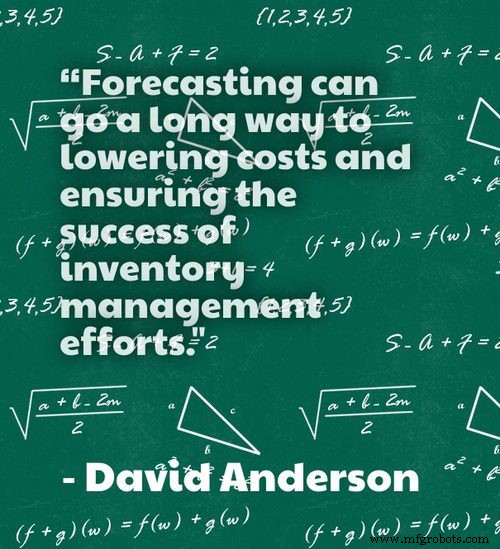
1. Gunakan pengumpulan data otomatis. “'Orang-orang yang menulis angka di atas kertas atau memasukkan string angka ke keyboard adalah pertanda buruk,' kata McKnight.
Manfaat pengumpulan data otomatis—melalui kode batang dan identifikasi frekuensi radio—sudah diketahui dengan baik, termasuk peningkatan produktivitas dan akurasi dan biaya tenaga kerja yang lebih rendah. Tetapi banyak perusahaan masih belum menerapkan pengumpulan data otomatis.
'Beberapa organisasi dengan 30.000 atau 40.000 nomor item dan banyak fasilitas masih yakin bahwa mereka lebih baik tanpa teknologi,' kata McKnight.” – Denny McKnight, mitra, Tompkins Associates Inc., perusahaan integrasi rantai pasokan yang berkantor pusat di Raleigh, N.C., dikutip oleh Leslie Hansen Harps dalam Praktik Terbaik di Pusat Distribusi Hari Ini , InboundLogistics.com
2. Jangan mengandalkan proses entri data manual. BUKAN:Gunakan komputer seluler dengan pemindai kode batang atau pembaca RFID di dok penerima untuk segera mengidentifikasi produk pada saat kedatangan. Ini membantu mengeluarkan produk dari dok dengan cepat dan menghilangkan hampir semua kesalahan yang terkait dengan penerimaan manual:termasuk kesalahan identifikasi, penghitungan, dan entri data. Dengan pemindaian dan teknologi RFID, Anda akan menghindari kesalahan yang merusak akurasi inventaris dan menghabiskan waktu serta sumber daya untuk memperbaikinya. Dan itu berarti staf gudang Anda dapat fokus untuk memproses pesanan pelanggan dengan lebih cepat.” – 10 Strategi Teratas Kehilangan Gudang dan Cara Menghindarinya , Solusi Motorola; Twitter:@MotoSolutions
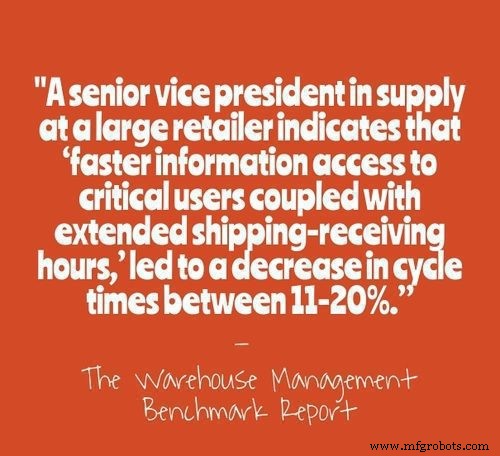
3. Promosikan visibilitas informasi di seluruh perusahaan. “Yang Terbaik di Kelasnya menunjukkan infrastruktur visibilitas gudang yang berkembang pesat yang memungkinkan mereka untuk berbagi informasi di seluruh operasi mereka dan di seluruh perusahaan. Responden lain menunjukkan visibilitas sebagai sarana untuk perbaikan. Seorang wakil presiden senior dalam pasokan di pengecer besar menunjukkan bahwa 'akses informasi yang lebih cepat ke pengguna penting ditambah dengan jam penerimaan pengiriman yang diperpanjang,' menyebabkan penurunan waktu siklus antara 11-20%.” – Laporan Tolok Ukur Manajemen Gudang , Grup Aberdeen; Twitter:@aberdeengroup
4. Pelacakan aset yang dipasangkan dengan sistem manajemen gudang (WMS) menyediakan otomatisasi yang diperlukan untuk memaksimalkan produktivitas gudang. “Bisnis pintar memahami bahwa mengendalikan inventaris, pemenuhan, dan biaya pengiriman sangat penting untuk kesuksesan. Perusahaan terus berupaya meningkatkan operasi gudang mereka dengan meningkatkan kelincahan, visibilitas, dan efisiensi tenaga kerja. Ini membutuhkan penggunaan praktik terbaik yang dikombinasikan dengan Sistem Manajemen Gudang (WMS) canggih yang secara optimal mengelola semua sumber daya dalam operasi distribusi sambil meminimalkan total biaya operasi atau kepemilikan (TCO).” – Gudang dan Pemenuhan:Sederhanakan Proses Pemenuhan Anda dan Buat Pelanggan Anda Puas , NetSuite; Twitter:@NetSuite
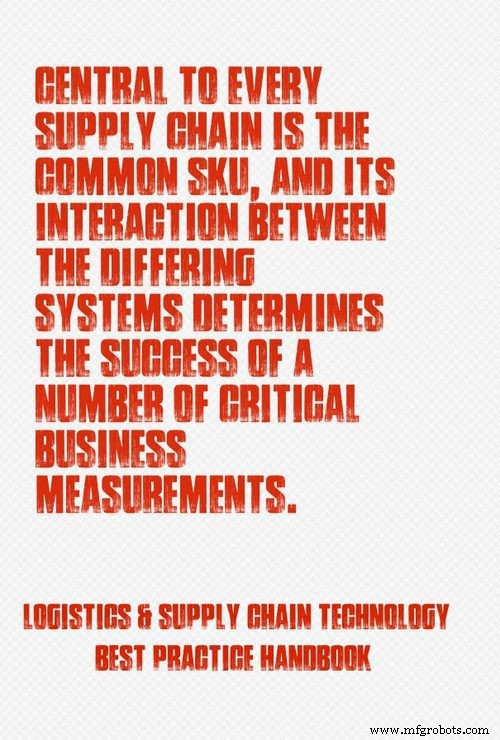
5. Sinkronisasi data meningkatkan visibilitas dan menyederhanakan tugas integrasi data yang biasanya padat karya. “Pusat dari setiap rantai pasokan adalah SKU umum, dan interaksinya antara sistem yang berbeda menentukan keberhasilan sejumlah pengukuran bisnis penting. Kunci untuk menyelaraskan aliran data di seluruh rangkaian aplikasi perangkat lunak yang kompleks dalam organisasi ukuran apa pun adalah menyinkronkan semua data yang terkait dengan SKU umum secara horizontal atau vertikal di dalam perusahaan. Pendekatan untuk menstandardisasi data produk umum di tingkat sistem dan tidak memiliki hambatan untuk transformasi data, dengan cepat menggantikan tugas integrasi data yang padat karya. Tahap evolusi berikutnya dalam perdagangan data antar organisasi adalah tempat penyimpanan data diperbarui dengan informasi SKU terbaru langsung dari pemasok. Transfer data yang dapat dioperasikan ini sekarang berada pada tingkat global dan hemat biaya, meningkatkan penyimpanan inventaris dengan mulus, meniadakan re-keying dan mengurangi ketidaksesuaian. Ini diatur untuk menjadi praktik terbaik di mana kesinambungan informasi SKU sangat penting untuk investasi WMS, BOS, dan POS. Salah satu sumber data masuk akal. Hasilnya – pengecer, pemasok, dan konsumen semuanya menjadi pemenang. Dengan sebagian besar perusahaan bertujuan untuk menghilangkan pengembalian dan pengiriman ulang; mengurangi denda rantai pasokan atau tolak bayar; memberikan pencocokan faktur dan penyimpanan stok yang lebih baik, suatu hari kita mungkin berbicara tentang karbon
sidik jari daripada jejak karbon.” – Buku Panduan Praktik Terbaik Teknologi Logistik &Rantai Pasokan , BASDA; Twitter:@BASDAUK
6. Gunakan lokasi tempat sampah untuk menemukan produk dengan cepat. “Apakah Anda menggunakan lokasi bin untuk menemukan produk Anda? Sebagian besar paket perangkat lunak distribusi yang tersedia saat ini menggunakan lokasi bin. Hal ini memungkinkan lokasi produk yang langsung dan akurat di dalam ruang pamer dan zona gudang Anda. Banyak distributor yang curiga untuk mengambil keuntungan dari alat ini karena kebutuhan yang dirasakan untuk menjaga lini vendor tetap bersama. Lokasi bin, pada kenyataannya, membebaskan Anda untuk menemukan produk berdasarkan volume penjualan, sehingga mengurangi jumlah langkah kaki yang diperlukan untuk memilih item utama yang cenderung muncul pada sebagian besar pesanan. Saya menyebutnya menemukan produk Anda berdasarkan peringkat kecepatan.
"Dapatkah Anda lulus 'Tes Suhu'? Apakah Anda dapat merekrut karyawan baru atau karyawan sementara dan yakin bahwa orang ini produktif dalam dua hingga tiga jam? Memanfaatkan lokasi bin menyediakan peta untuk diikuti oleh rekrutan baru. Hal ini memungkinkan Anda untuk mencari seseorang yang ahli di bidang penanganan material. Tanpa lokasi bin, Anda perlu mencari seseorang yang berpengalaman dalam lini produk yang Anda bawa untuk menemukan produk untuk memenuhi pesanan. Mereka akan membutuhkan lebih banyak pegangan tangan untuk mempelajari di mana lini produk yang berbeda itu disimpan di dalam empat dinding Anda. ” – Dan Belanger, Lakukan dan Larangan dalam Operasi Gudang yang Efisien (Dan Aman) , Asosiasi Distributor Gas dan Pengelasan (GAWDA); Twitter:@GasWeldEdge
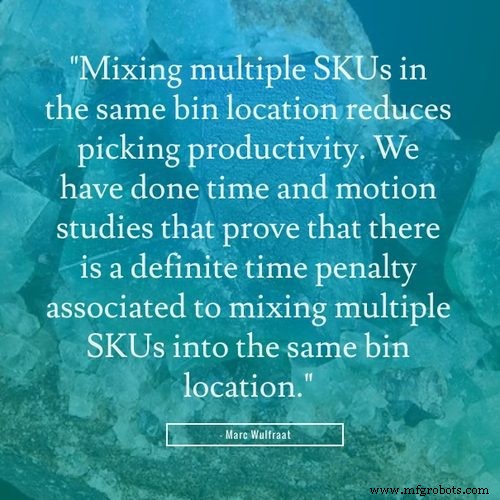
7. Jangan mencampur beberapa SKU dalam satu lokasi bin. “Mencampur beberapa SKU di lokasi bin yang sama mengurangi produktivitas pengambilan. Kami telah melakukan studi waktu dan gerak yang membuktikan bahwa ada penalti waktu yang pasti terkait dengan pencampuran beberapa SKU ke dalam lokasi bin yang sama.
“Kami melihat ini di banyak gudang di mana lokasi bin dapat mewakili tingkat rak yang berisi 5 – 10 permukaan pick SKU. Operator diarahkan ke tingkat rak dan kemudian perlu mencari melalui SKU yang berbeda untuk menemukan item yang akan diambil.
“Hal ini tidak hanya mengurangi akurasi, tetapi juga memperlambat operator sebanyak 15+ detik per transaksi pengambilan. Memiliki lokasi pengambilan terpisah untuk setiap SKU adalah aturan #1.” – Marc Wulfraat, Presiden, MWPVL, 5 Cara untuk Meningkatkan Produktivitas Pengambilan Pesanan , Rantai Pasokan247; Twitter:@SupplyChain247
8. Catat berapa kali inventaris diambil selama jangka waktu tertentu menggunakan sistem pelacakan aset. “Ada kalanya tidak masuk akal untuk menyimpan produk. Sebagai contoh, jika suatu barang diambil hanya lima kali dalam setahun, biaya penyimpanan dapat dihilangkan dengan pengiriman dropship dari produsen. Dengan mencatat berapa kali suatu produk diambil, Anda dapat menentukan nilai ruang tempat inventaris berada.” – Praktik Terbaik – Manajemen Inventaris , Pusat Pemenuhan Promosi; Twitter:@PFCFulfillment
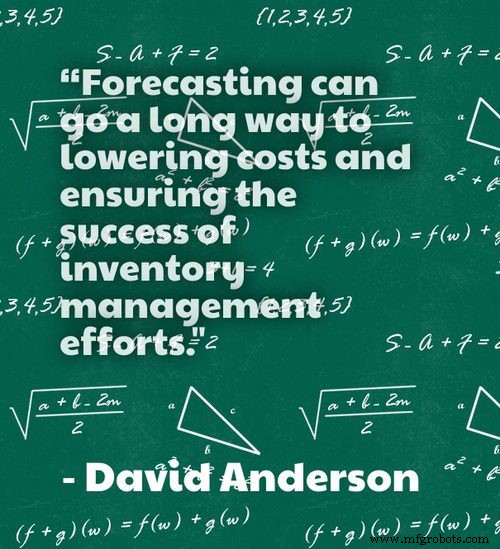
9. Pelacakan aset memungkinkan perkiraan yang lebih akurat, penting untuk menurunkan biaya dan meningkatkan manajemen inventaris. “Peramalan dapat membantu menurunkan biaya dan memastikan keberhasilan upaya manajemen inventaris. Ketika pengecer dapat secara akurat memprediksi item mana yang mereka butuhkan dan jumlah yang benar, mereka akan lebih cocok untuk memenuhi harapan pelanggan mereka tanpa memiliki kelebihan stok. Peramalan yang lebih baik membutuhkan pengamatan yang cermat dari riset pasar, model permintaan pasar, pola permintaan, tingkat stok minimum dan teknik historis dan dapat memainkan peran besar dalam manajemen inventaris yang sukses. – David Anderson, Tiga praktik terbaik manajemen inventaris , SalesWarp; Twitter:@SalesWarp
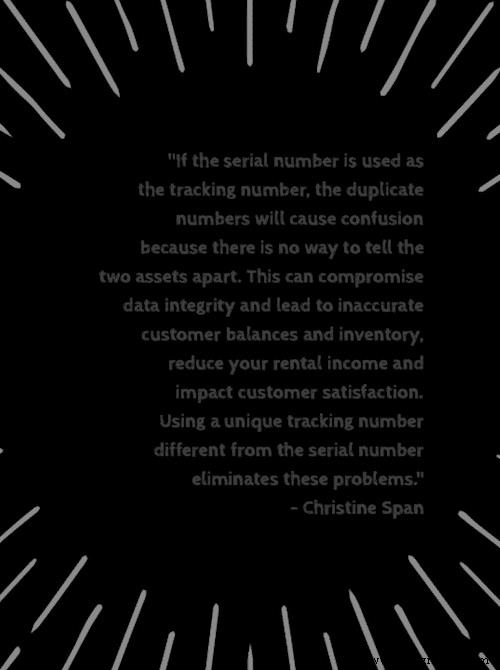
10. Gunakan nomor pelacakan unik, bukan nomor seri aset. “Ada kemungkinan bahwa nomor seri suatu aset akan identik dengan aset lain. Jika nomor seri digunakan sebagai nomor pelacakan, nomor duplikat akan menyebabkan kebingungan karena tidak ada cara untuk membedakan kedua aset. Ini dapat membahayakan integritas data dan menyebabkan saldo dan inventaris pelanggan yang tidak akurat, mengurangi pendapatan sewa Anda, dan memengaruhi kepuasan pelanggan. Menggunakan nomor pelacakan unik yang berbeda dari nomor seri menghilangkan masalah ini. Jika nomor pelacakan hilang, aset masih dapat dicari menggunakan nomor seri dan diberi label ulang dengan benar untuk mempertahankan riwayat aset. – Christine Span, Lima Praktik Terbaik Pelacakan Aset Terbaik , Lacak Tentang; Twitter:@trackabout
Praktik Terbaik Logistik Operasi Gudang
11. Buat pemberitahuan pengiriman lanjutan. “Ini mungkin tampak seperti tidak perlu dipikirkan lagi, tetapi banyak pusat distribusi masih belum menerapkan pemberitahuan pengiriman lanjutan (ASN) yang ditransmisikan secara elektronik. Mengandalkan jadwal pengiriman &penerimaan "biasa" dapat mengakibatkan inefisiensi di seluruh pusat distribusi. Penundaan terjadi, gangguan terjadi - dan itu menyebabkan penyimpangan dari jadwal "biasa". Masalah yang dihasilkan dimulai dengan staf yang tidak tepat di dok penerima dan riak melalui gudang. Namun, dengan memanfaatkan pemberitahuan pengiriman lanjutan elektronik dalam pesanan pembelian dan fungsi manajemen inventaris, tenaga kerja dapat direncanakan dengan lebih pasti. Pemenuhan pesanan dan aktivitas transportasi dapat disesuaikan untuk memastikan persyaratan waktu layanan yang tepat terpenuhi, dan moda transportasi dioptimalkan untuk menekan biaya.” – 11 Praktik Terbaik Gudang dan Pusat Distribusi untuk Rantai Pasokan Anda , Layanan Rantai Pasokan Lama
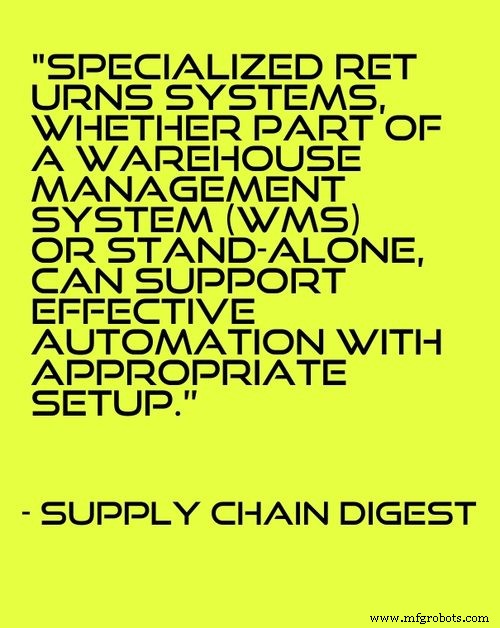
12. Terapkan proses pengembalian yang efisien. “Pengembalian pada dasarnya kompleks karena dampaknya terhadap inventaris fisik, inventaris elektronik, dan sistem akuntansi. Semua item harus diidentifikasi, ditugaskan ke pelanggan atau akun, diberi disposisi dan kemudian disortir secara fisik untuk diproses. Karena beberapa produk mungkin dibuang atau disimpan kembali untuk tolak bayar vendor, tidak semua barang dagangan masuk ke inventaris elektronik; beberapa barang dagangan harus dikemas ulang dan dipertanggungjawabkan secara manual versus elektronik. Akhirnya, kredit umumnya dikeluarkan di lain waktu dan seringkali hanya untuk sebagian dari pengembalian, termasuk barang yang dibuang atau tidak dapat dijual. Proses ini sulit untuk diotomatisasi dengan paket ERP generik dan sangat menantang dengan proses kertas sederhana. Sistem pengembalian khusus, baik bagian dari Sistem Manajemen Gudang (WMS) atau yang berdiri sendiri, dapat mendukung otomatisasi yang efektif dengan penyiapan yang tepat.” – Wawasan Pakar:Praktik Terbaik dalam Pengembalian Gudang , Intisari Rantai Suplai; Twitter:@scdigest
13. Tangani tugas secara efisien dan hindari penundaan. “Kadang-kadang ketika Anda menerima kiriman besar dari pemasok, mudah untuk memberinya ‘ol’, “Eh. Mari kita urus ini nanti. ” Akhiri penundaan dan luangkan waktu untuk memecahkan kotak, masukkan ke tempat sampah daur ulang, buka kemasan produk Anda dan simpan sesuai kebutuhan. Ini adalah kebiasaan yang harus Anda lakukan. Jika kiriman Anda datang pada waktu yang sama setiap hari/minggu, maka jadwalkan di kalender Anda. Menundanya hanya akan membuatnya menjadi binatang yang lebih besar, menunggu perhatian Anda.
“Jika Anda tidak punya waktu untuk menyimpannya di rak Anda, hal lain yang biasa saya lakukan ketika bekerja di ritel adalah saya akan mengambil semua kotak dan menyusunnya. Buka masing-masing dan lihat apa yang disertakan. Dari sana, buat tumpukan stoking mini di setiap kotak. Mengetahui di mana mereka pada akhirnya akan disimpan, kumpulkan barang-barang yang berdekatan, sehingga Anda dapat menariknya ke tempat yang benar di lantai gudang Anda dan menyimpannya dengan cepat. – Breena Fain, 6 Cara Mengoptimalkan Sistem Manajemen Gudang Anda , StitchLabs; Twitter:@StitchLabs
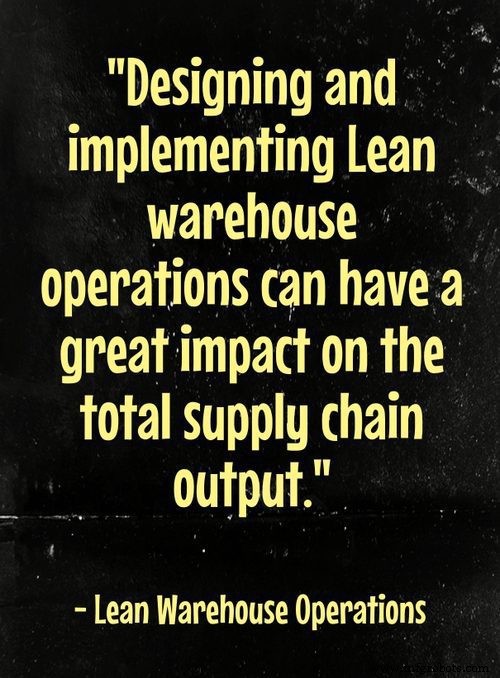
14. Terapkan praktik operasi gudang ramping. “Merancang dan mengimplementasikan operasi gudang Lean dapat berdampak besar pada total output rantai pasokan. Dengan mendekati area fokus limbah yang disebutkan di atas dengan solusi Lean, beberapa peluang yang muncul untuk mengurangi waktu tunggu di pergudangan meliputi:
- Pengurangan waktu penanganan material untuk pengambilan, penyimpanan, pembuatan palet, dan pengiriman pesanan.
- Keandalan informasi untuk mengoordinasikan sisa rantai pasokan.
- Pengurangan waktu bongkar muat truk dan kontainer.
- Pengurangan waktu yang dihabiskan untuk memeriksa dan mencari inventaris.
- Peningkatan fleksibilitas untuk beradaptasi dengan perubahan kondisi pasar dan spesifikasi pelanggan.” – Operasi Gudang Lean , Empat Prinsip
15. Kontrol pengiriman masuk dan keluar untuk mengurangi area biaya ini. “Perpustakaan virtual dipenuhi dengan artikel tentang cara mengurangi atau memperlambat area biaya ini. Ini harus menjadi fokus nomor satu Anda untuk mencegah erosi keuntungan. Gunakan konsultan untuk membantu Anda menawar secara kompetitif. Sementara perjanjian operator adalah hak milik, konsultan berpengalaman masih dapat membantu mengidentifikasi area untuk menegosiasikan pengurangan tanpa merusak tingkat layanan.” – Curt Barry, 10 Cara Meningkatkan Efisiensi Gudang dan Mengurangi Biaya , Pedagang Multi-Saluran; Twitter:@mcmerchant
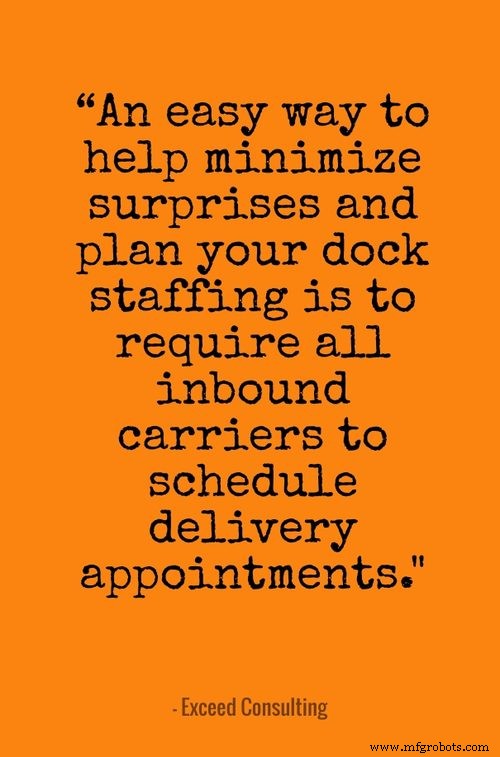
16. Mengharuskan vendor menerima janji temu. “Cara mudah untuk membantu meminimalkan kejutan dan merencanakan staf dok Anda adalah dengan meminta semua operator masuk untuk menjadwalkan janji pengiriman. Ada dua metode berbeda untuk menjadwalkan dan keduanya dapat digunakan secara bersamaan. Metode pertama adalah dengan hanya menetapkan setiap operator atau pengiriman waktu atau jendela waktu tertentu untuk pengiriman. Yang kedua adalah menetapkan jadwal harian, mingguan, atau bulanan tertentu atau berulang untuk tiba. Ini memungkinkan Anda untuk menjadwalkan staf yang sesuai dan memanfaatkan dok Anda sebaik mungkin. Vendor yang menerima janji temu sangat penting jika Anda berbagi dermaga atau mengirim baik inbound maupun outbound dari area yang sama. Dokumen atau data sebelumnya harus disediakan sebelum pengiriman dilakukan. Dengan meminta janji temu dan informasi tentang muatan yang masuk, kejutan diminimalkan.” – Kembali ke Dasar, Bagian 1:Menerima , Melebihi Konsultasi
17. Lakukan Analisis ABC, yang berguna untuk mengkategorikan inventaris Anda berdasarkan nilai. “ABC adalah hierarki barang Anda yang paling berharga hingga yang paling rendah (berdasarkan nilai dolar). Ini juga disebut sebagai Metode Kategorisasi Persediaan. Karena Anda mungkin tidak menghargai seluruh stok Anda secara setara, kontrol ini akan membuat Anda memfokuskan waktu dan sumber daya Anda pada item yang menghasilkan uang paling banyak.
“Item adalah tiket besar atau stok prioritas. Barang-barang ini memerlukan kontrol dan pemantauan yang lebih ketat karena merupakan kontributor pendapatan dan biaya terbesar Anda. Karena biayanya, kemungkinan besar Anda akan membawa volume yang lebih kecil. Karena barang-barang ini banyak dicari, mereka harus disimpan di bawah "gembok dan kunci". Selain keamanan, produk A-list akan membutuhkan frekuensi peninjauan stok dan pemesanan ulang yang lebih tinggi. Ini memastikan bahwa Anda memiliki persediaan yang memadai.
“Sebaliknya, item-C memiliki nilai yang lebih rendah tetapi Anda mungkin membawa barang-barang tersebut dalam jumlah besar. Misalnya, jika Anda memiliki toko perangkat keras, paku dalam jumlah besar dapat dianggap sebagai barang C. B-item duduk tepat di tengah untuk nilai, volume, frekuensi ulasan stok, dan pemesanan ulang. ” – Colleen Rodericks, Teknik pengelolaan inventaris dan praktik terbaik , arus masuk; Twitter:@inFlowInventory
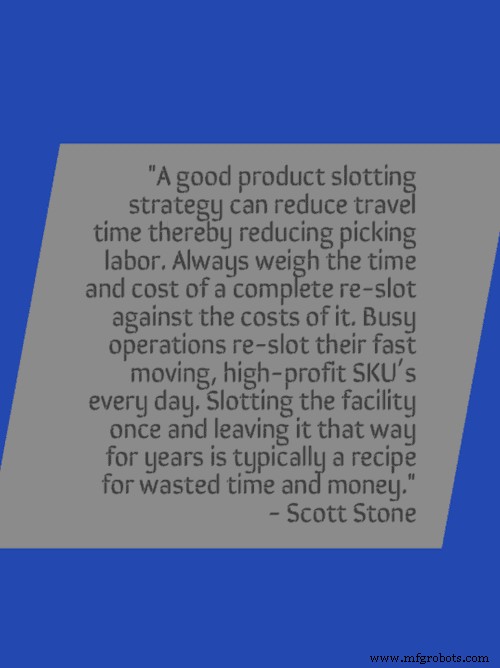
18. Re-slot posisi pick Anda sesering yang diperlukan. “Hingga 60% dari aktivitas harian pemetik dapat terlibat dalam waktu perjalanan (berjalan atau menggunakan forklift atau walkie), jadi mengurangi pengeluaran waktu itu adalah ide yang bagus. Strategi penempatan produk yang baik dapat mengurangi waktu tempuh sehingga mengurangi tenaga kerja pemetikan. Selalu pertimbangkan waktu dan biaya slot ulang lengkap dengan biayanya. Operasi yang sibuk mengatur ulang SKU mereka yang bergerak cepat dan menguntungkan setiap hari. Menempatkan fasilitas sekali dan membiarkannya seperti itu selama bertahun-tahun biasanya merupakan resep untuk membuang-buang waktu dan uang.” – Scott Stone, 13 Praktik Terbaik untuk Produktivitas Gudang, Cisco-Elang; Twitter:@CiscoEagle
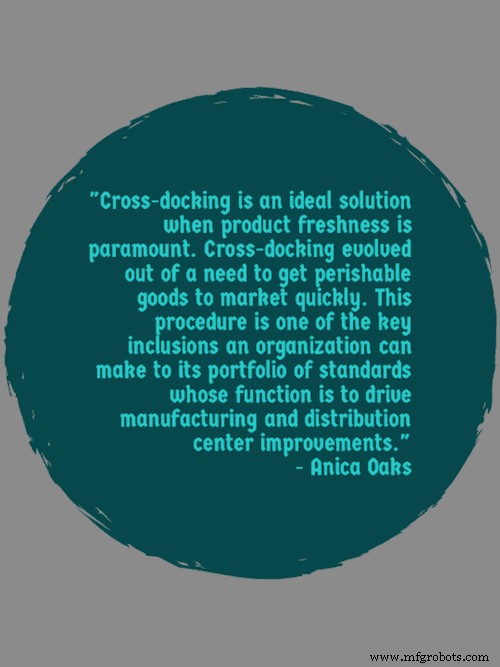
19. Manfaatkan cross-docking jika memungkinkan. “Perencanaan logistik yang unggul mencakup cross-docking jika memungkinkan. Cross-docking adalah praktik pembongkaran material dari kendaraan yang masuk dan segera memuat material yang sama ini langsung ke kendaraan keluar dengan interval pergudangan minimal atau nol di antaranya. Anggap ini sebagai pengiriman "Just-in-Time". Cross-docking adalah solusi ideal ketika kesegaran produk adalah yang terpenting. Cross-docking berevolusi dari kebutuhan untuk membawa barang yang mudah rusak ke pasar dengan cepat. Prosedur ini adalah salah satu penyertaan utama yang dapat dilakukan organisasi ke dalam portofolio standarnya yang berfungsi untuk mendorong peningkatan manufaktur dan pusat distribusi.” – Anica Oaks, 5 Lean Best Practices for the Warehouse, Blog Transformasi Manufaktur Apriso; Twitter:@Apriso
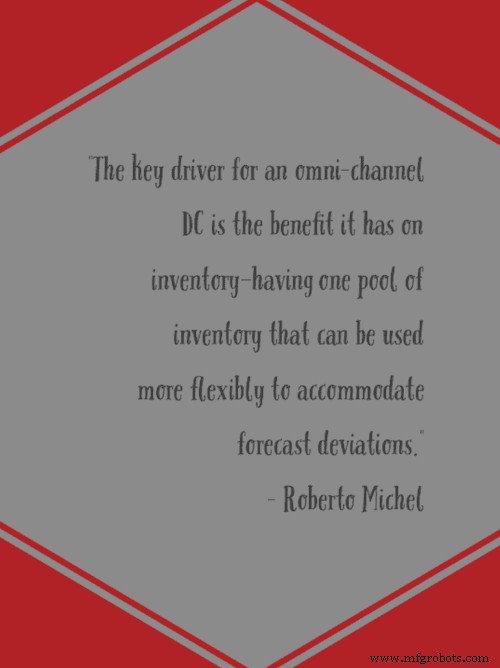
20. Buat DC yang memenuhi pesanan untuk beberapa saluran. “Untuk beberapa perusahaan yang mencari efisiensi pemenuhan saluran omni, trennya adalah beralih dari DC yang didedikasikan untuk satu saluran dan alih-alih memiliki DC yang memenuhi pesanan untuk beberapa saluran, kata Ian Hobkirk, pendiri dan direktur pelaksana Commonwealth Supply Chain Advisors. .
“'Sepuluh tahun yang lalu ketika e-commerce masih cukup baru, Anda memiliki banyak pemisahan saluran dalam cara perusahaan mendirikan dan menjalankan DC, dan pemenuhan e-commerce, dalam banyak kasus, dialihdayakan ke 3PL,' kata Hobkirk. 'Salah satu tren yang kita lihat sekarang di kalangan pengecer adalah memiliki pusat pemenuhan multi-saluran di mana inventaris dan pemenuhan untuk semua saluran berada di bawah atap yang sama.'
“Pendorong utama DC omni-channel adalah manfaat yang dimilikinya pada inventaris—memiliki satu kumpulan inventaris yang dapat digunakan secara lebih fleksibel untuk mengakomodasi penyimpangan prakiraan. 'Ada faktor lain yang mendorong pusat pemenuhan omni-channel, seperti biaya yang lebih rendah karena dapat menggunakan kumpulan tenaga kerja yang sama, tetapi faktor inventarislah yang benar-benar mendorong tren ini,' kata Hobkirk.
“Kenaikan pemenuhan omni-channel membuat manajemen inventaris lebih kompleks, yang meningkatkan kebutuhan akan sistem yang lebih baik untuk eksekusi, kolaborasi prakiraan, dan pelaporan manajemen, termasuk sistem manajemen gudang (WMS), perencanaan sumber daya perusahaan (ERP), serta manajemen permintaan dan lintas -kolaborasi disiplin, kata Don Derewecki, konsultan senior di firma penasihat rantai pasokan St. Onge Company.” – Roberto Michel, Manajemen Gudang/DC:Enam Praktik Terbaik untuk Manajemen Inventaris yang Lebih Baik , Manajemen Logistik; Twitter:@LogisticsMgmt
Manajemen Keselamatan dan Risiko dalam Operasi Gudang
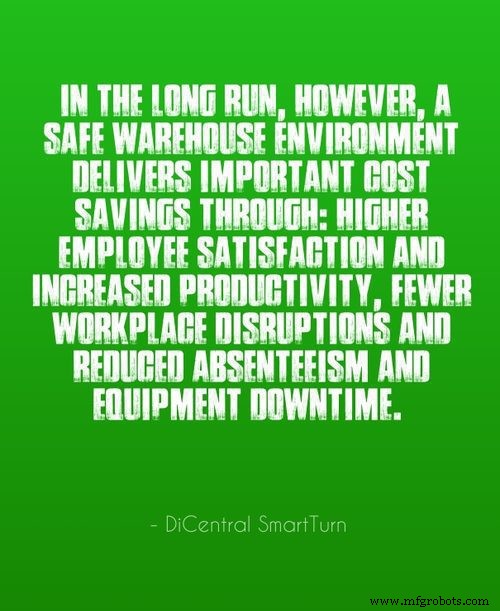
21. Jadikan keamanan gudang sebagai prioritas utama. “Ada lebih banyak keamanan gudang daripada kepatuhan terhadap kode kebakaran dan peraturan OSHA. Sayangnya, terlalu banyak gudang dan 3PL melihat keselamatan sebagai memenuhi minimum yang diamanatkan oleh hukum atau hati nurani mereka. Seringkali, keduanya tidak berjalan cukup jauh. Dalam bab ini, kita akan melihat Praktik Terbaik untuk Keselamatan Gudang, membahas manfaat dan risiko bagi karyawan, manajer, dan pemberi kerja dari keduanya menciptakan budaya keselamatan di gudang, dan gagal melakukannya. Bagi perusahaan yang gagal mempromosikan keselamatan, seringkali karena waktu yang tidak mencukupi, sumber daya yang tidak memadai, atau kesempatan untuk menghemat uang melalui pemotongan sudut. Namun, dalam jangka panjang, lingkungan gudang yang aman memberikan penghematan biaya yang penting melalui:kepuasan karyawan yang lebih tinggi dan produktivitas yang meningkat, gangguan di tempat kerja yang lebih sedikit, dan pengurangan ketidakhadiran serta waktu henti peralatan. Anda dapat memperpanjang umur infrastruktur gudang Anda seperti penyimpanan dan peralatan penanganan material, serta mengurangi kerusakan pada inventaris. Yang terpenting, jangan berasumsi bahwa tempat kerja yang aman memiliki harga yang sangat mahal.” – Praktik Terbaik Manajemen Inventaris dan Gudang , DiCentral SmartTurn; Twitter:@DiCentral_EDI
22. Bentuk komite keselamatan. “Meskipun tidak terlalu parah, kecelakaan gudang sangat banyak—industri pergudangan dan penyimpanan mengalami hampir 15.000 cedera dan penyakit setiap tahun, menurut Biro Statistik Tenaga Kerja AS.
“Untuk mencegah kecelakaan, operator gudang harus menekankan pelatihan pekerja dan menetapkan praktik keselamatan terbaik, kata Bob Shaunnessey, direktur eksekutif Dewan Pendidikan dan Penelitian Pergudangan (WERC), sebuah organisasi berbasis di Oak Brook, Illinois yang didedikasikan untuk manajemen gudang dan perannya dalam rantai pasokan.
“Untuk sebagian besar gudang, membentuk komite keselamatan adalah langkah pertama menuju penerapan prosedur keselamatan yang ditingkatkan.
“Anggota komite keselamatan biasanya dipilih dari kelompok organisasi tertentu—termasuk pekerja lantai gudang, pengawas shift, dan manajer departemen. Pendekatan ini memberi semua orang suara, tetapi menjaga ukuran komite menjadi jumlah peserta yang efektif.” – John Edwards, Keamanan Gudang:Bukan Kecelakaan , Logistik dalam negeri; Twitter:@ILMagazine
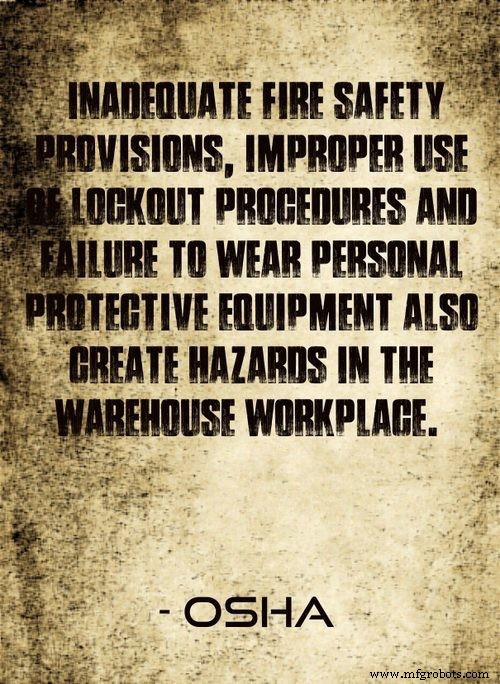
23. Siapkan rencana tanggap darurat. “Ketentuan keselamatan kebakaran yang tidak memadai, penggunaan prosedur penguncian yang tidak tepat dan kegagalan untuk memakai alat pelindung diri juga menciptakan bahaya di tempat kerja gudang. Pengusaha harus memiliki rencana darurat yang menjelaskan apa yang diharapkan dari karyawan jika terjadi keadaan darurat, termasuk:
• Ketentuan lokasi pintu keluar darurat dan
prosedur evakuasi;
• Prosedur akuntansi untuk semua karyawan
dan pengunjung;
• Lokasi dan penggunaan alat pemadam kebakaran dan
peralatan darurat lainnya.” – Panduan Saku OSHA, Seri Keselamatan Pekerja:Pergudangan , OSHA.gov; Twitter:@usdol
24. Hindari kecelakaan umum di dok pemuatan dan area pementasan. “Dok pemuatan atau area pementasan adalah area umum di gudang di mana cedera dan kerusakan produk terjadi. Bahaya umum meliputi:
• Produk jatuh ke kepala, kaki, lengan, dan kaki karyawan;
• Program pembersihan yang lemah yang mengakibatkan kemacetan;
• Karyawan melompat dari elevasi tinggi ke elevasi yang lebih rendah;
• Mengangkat pelat dok dan terus menyesuaikannya; dan
• Forklift atau jack palet meluncur dari dok.
“Kontrol meliputi:
• Mengamankan pelat dok agar tidak terguling;
• Melakukan pemeriksaan harian terhadap muatan dan pengaturan
penyimpanan sementara;
• Tidak pernah memungkinkan forklift atau dongkrak palet untuk mundur ke tepi
dok;
• Menegakkan aturan keselamatan tentang pergerakan karyawan dari ketinggian
dok yang lebih tinggi ke permukaan tanah yang lebih rendah; dan
• Memantau formulir inspeksi keselamatan yang ditugaskan West Bend; Twitter:@WBsilverlining
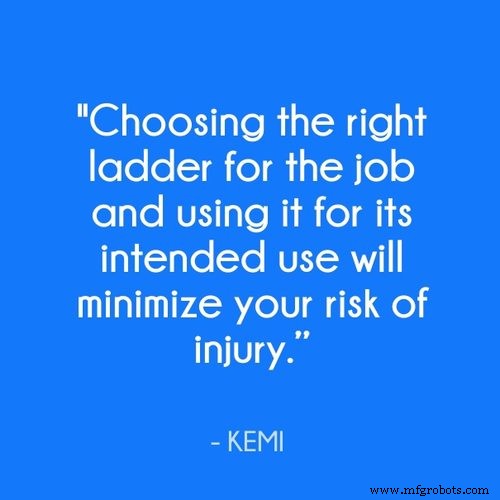
25. Sediakan tangga yang sesuai untuk berbagai pekerjaan di gudang Anda, dan berikan pelatihan sehingga pekerja dapat dengan mudah mengidentifikasi tangga yang paling tepat untuk tugas. “Penanganan material bukan satu-satunya sumber potensial cedera di dalam gudang. Item mungkin harus ditumpuk sehingga ruang digunakan lebih efektif. Tangga dapat digunakan untuk mencapai bagian atas rak atau rak. Memilih tangga yang tepat untuk pekerjaan itu dan menggunakannya untuk tujuan penggunaannya akan meminimalkan risiko cedera Anda.” – Keamanan Gudang , KEMI
26. Bersihkan tumpahan sesegera mungkin, dan singkirkan inventaris dan persediaan dari lorong ketika staf harus mengosongkan area untuk waktu yang singkat. “Gudang adalah tempat dengan banyak barang. Lorongnya yang sempit, tumpukan barang yang tinggi, dan pencahayaan yang buruk adalah bahan yang tepat yang dapat mengganggu jarak pandang. Tergelincir dan tersandung material atau tumpahan cairan adalah kecelakaan umum yang dapat dihindari jika gudang mempertahankan pencahayaan yang memadai dan melengkapi sudut gelap dengan lampu khusus yang dapat dengan mudah dinyalakan dan dimatikan. Singkirkan anak tangga atau punggungan yang tidak perlu dan dorong karyawan untuk tidak pernah meninggalkan kargo, kotak, dan barang apa pun tanpa pengawasan di lantai.
“Jika pekerja gudang perlu meninggalkan lantai untuk sementara, penting baginya untuk memindahkan material dari tengah lorong sambil tetap menyalakan lampu. Jika ada tumpahan, karyawan harus mengambil langkah yang tepat untuk menutup area dengan tanda-tanda yang terlihat dan membersihkan sesegera mungkin.” – Tom Reddon, 4 Cara Menghindari Insiden Gudang Paling Umum , Pengetahuan di Tempat Kerja
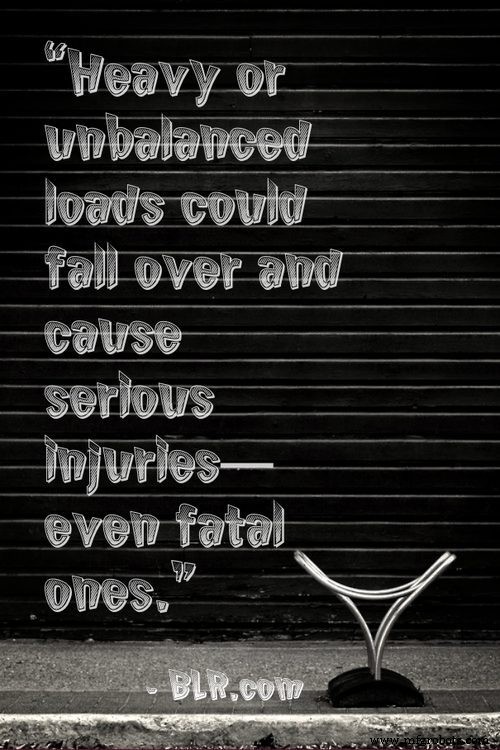
27. Hanya operator terlatih yang boleh menggunakan peralatan seperti forklift, derek, dan kerekan. “Forklift dan truk tangan bukan satu-satunya peralatan gudang yang terbukti berbahaya. Kontak dengan bagian konveyor yang bergerak dapat menyebabkan cedera serius. Itulah mengapa sangat penting untuk menjaga penjaga mereka di tempat. Derek, kerekan, dan derek hanya dapat dioperasikan oleh operator terlatih yang cukup tahu untuk menahan beban di atas orang atau untuk melepaskan tangan atau kaki mereka dari kontrol saat beban ditangguhkan. Selain itu, siapa pun yang bekerja di sekitar harus memperhatikan pergerakan crane; jika Anda bekerja atau berdiri di bawah derek, Anda sedang mencari masalah. Anda mungkin melihat bahaya dalam cara peralatan ini dimuat juga. Beban berat atau tidak seimbang dapat jatuh dan menyebabkan cedera serius—bahkan fatal.” BLR.com; Twitter:@BLR_INC
28. Gunakan praktik penyimpanan yang baik untuk meminimalkan risiko kebakaran. “Metode penyimpanan dapat mempengaruhi laju penyebaran api dan tingkat keparahannya untuk bahan yang sama. Misalnya, gulungan kertas yang disimpan secara vertikal dapat menimbulkan efek tumpukan. Untuk penyimpanan di dalam ruangan, tinggi maksimum tiang yang disarankan adalah 4,5m. Jarak bebas dari puncak tiang ke titik terendah anggota atap, perlengkapan listrik, atau detektor kebakaran harus minimal 1m. Pita warna harus dicat di dinding untuk menunjukkan ketinggian maksimum bahan yang dapat ditumpuk.” – N.V. Subba Rao dan K. Ramish Ramalingham, Manajemen Risiko di Gudang , Cholarisk.com
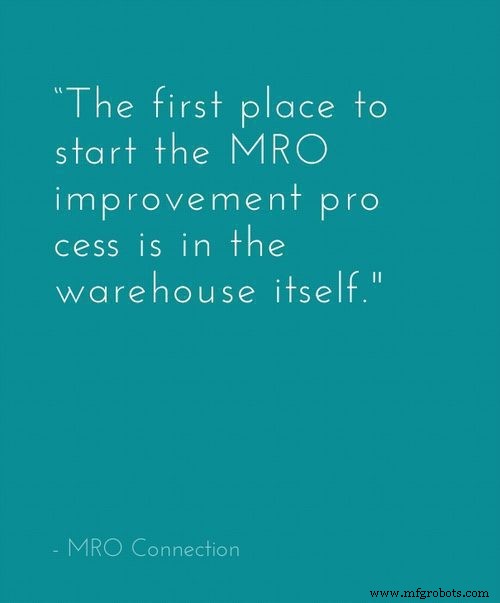
29. Peralatan keselamatan harus digunakan setiap saat. “Di gudang sangat penting bahwa forklift atau dolly hidrolik digunakan untuk mengangkat barang yang terlalu berat. Kacamata yang sesuai dan topi keras juga harus dipakai bila diperlukan. Karyawan harus mengetahui pintu keluar darurat dan alat penyiram yang dipasang di atap tidak boleh terhalang setiap saat. Safety equipment is implemented in order to minimize workplace injury, so although it may be time consuming to initiate its use, it does pay off in the long run.” – Warehouse Safety Principles:6 key guidelines to keep your workplace safe. , AdaptALift; Twitter:@aalhyster
30. Post safety expectations in highly visible locations and key areas. “Warehouse supervisors should ensure all safety expectations are posted clearly in close proximity to all equipment—forklifts, hydraulic dollies, hand jacks, etc. Doing so assures that employees have constant visual reminders of the inherent dangers of using such equipment, and the safety precautions they should take to avoid injury.” – Warehouse Safety Checklist:8 Things Every Manager Should Review , Legacy Supply Chain Services; Twitter:@legacyscs
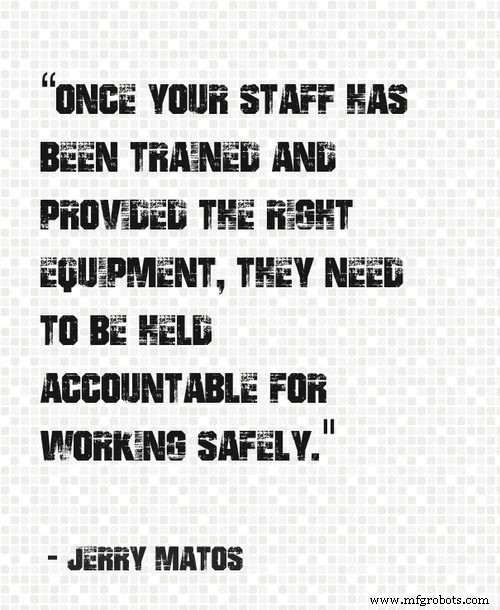
31. Establish accountability and give staff a sense of ownership over warehouse safety practices. “Once your staff has been trained and provided the right equipment, they need to be held accountable for working safely. This must apply to everyone in your warehouse. You cannot overlook bad habits of supervisors while reprimanding a dockworker. How you handle safety infractions is up to you, but your employees must own their actions. You will see better results if you offer suggestions for safer operation at the same time you express criticism.
“You do need to document lapses in safety. Without proper records, you may not have the backup you need to take action against an employee that continues to ignore your requirements. Documentation will also help protect you if an employee is injured performing an action after they have been instructed otherwise.” – Jerry Matos, Product Specialist, Cherry’s Industrial Equipment, 6 Ways To Encourage Warehouse Safety , Industrial Distribution; Twitter:@indistwebsite
32. Consider enlisting an outside expert to identify warehouse hazards. “To help improve the safety in the workplace, consider bringing in an outsider. The outsider does not necessarily need to be a consultant or OSHA representative, but may be a business associate, or peer. The point is to have a fresh pair of eyes evaluate the warehouse. Sometimes what is seen in plain sight every day may be an overlooked hazard.” – Best Practices for Warehouse Safety , Labor Law Center
Optimizing Warehouse Operations Workflows

33. Clear aisles make for an efficient flow of inventory. “The movement of inventory throughout the warehouse should be done by experienced materials handlers with certifications or licenses to operate forklifts and boom lifts. These materials handlers should be able to move from one section of the warehouse to another with ease due to aisles that are not full of unstored inventory. Inventory that has not been placed in its proper bin or warehouse location can cause problems with inventory systems, especially under a FIFO, or First In, First Out, inventory system. A FIFO system ensures that the inventory that was received yesterday is moved to the shipping dock before the inventory that was received today. This inventory system reduces the chance of obsolete inventory sitting in warehouse bins.” – Justin Johnson, Best Practices in Warehouse Operations , Chron.com
34. Store the most frequently picked items close to the shipping area. “When considering the level of effort involved in warehouse operations, the greatest expenditure of effort is in the picking process. To gain efficiencies in picking the labor time to pick orders needs to be reduced and this can achieved in a number of ways. Companies with the most efficient warehouses have the most frequently picked items closest to the shipping areas to minimize picking time. These companies achieve their competitive advantage by constantly reviewing their sales data to ensure that the items are stored close to the shipping area are still the most frequently picked.” – Martin Murray, Supply Chain/Logistics Expert, Warehouse Best Practices , About.com
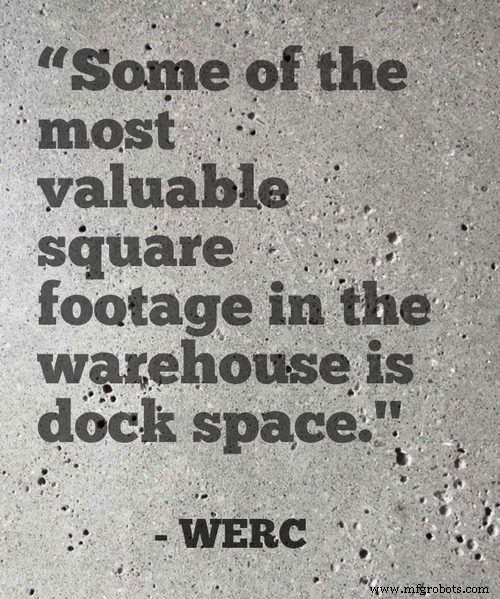
35. Implement efficient dock management practices. “Some of the most valuable square footage in the warehouse is dock space. All material must flow in and out of your docks, and these are limited in number (and not readily added to). Space on the inside and outside of the docks is some of the busiest in your warehouse. Dock best practice depends on the type of inbound you receive and for many companies balancing available dock doors, equipment, and labor is difficult, so the receiving dock becomes a choke point in the supply chain. Docks in today’s warehouses must be more flexible and must support a variety of receipts that are coming in at a faster rate and in greater frequency and with just in-time and VMI programs, smaller quantities and mixed pallets.” – Warehousing &Fulfillment Process Benchmark &Best Practice Guide , Warehouse Education and Research Council (WERC); Twitter:@WERC
36. Calculate resource and space requirements based on expected receipts and current backloads. “Put-away is the process of moving material from the dock and transporting it to a warehouse’s storage, replenishment, or pick area. Best-practice companies manage the put-away area by calculating resource and space requirements based on expected receipts and current backlogs. Best practice is to put away product the same day it’s received, because not doing so affects space, causes congestion, increases transaction errors, and makes product more susceptible to damage. In a busy warehouse, it is easy to let product put-away fall behind other tasks such as picking, replenishment, shipping, and loading. But pulling away resources from put-away tasks can affect fill rates by not having product in pick racks. This can bring about congestion in staging areas that overflow into aisles. Delaying put-away may also result in product damage as the merchandise is moved, again and again, to make way for higher priority receipts. Proper staffing of the put-away team will support down stream processes of picking and shipping, and in the long run lead to better customer order fill rates.” – Kate Vitasek, Best Practices in Material Handling and Put-away , Multi-Channel Merchant; Twitter:@mcmerchant
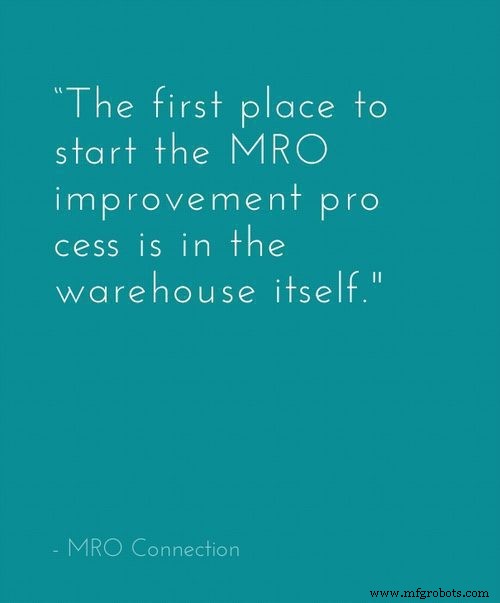
37. Establish stable warehouse operations within the warehouse first, then work to improve pre-planning efforts. “The first place to start the MRO improvement process is in the warehouse itself. Once stable warehouse operations have been established, maintenance and operations can work to improve their pre-planning efforts. At first glance, this appears to be a daunting task. Trying to organize, store, identify and properly manage thousands of disparate inventory items, with different and seemingly unpredictable demand patterns, creates an environment in which it is difficult to succeed. Creating an implementation strategy that is simple, straight forward and thorough, is critical to a successful MRO Warehouse Operation.” – Creating the “Perfect Warehouse,” MRO Connection
38. Maximize vertical space. “On the production floor, where space can be limited, it’s important to take advantage of every inch of available space (floor to ceiling). As noted in an Occupational Health &Safety article, solutions such as pallet racking can lead to safer working conditions as well as increased efficiency in the warehouse. Pallet racking, the most common way of storing pallet loads in the world, is an easy-to-use storage solution; it’s used in the vast majority of warehouses, manufacturing facilities, commercial warehouse operations, and even retail stores.” – Jennie Dannecker, 10 Ideas for More Efficient &Productive Warehouse Operations , Cerasis; Twitter:@Cerasis
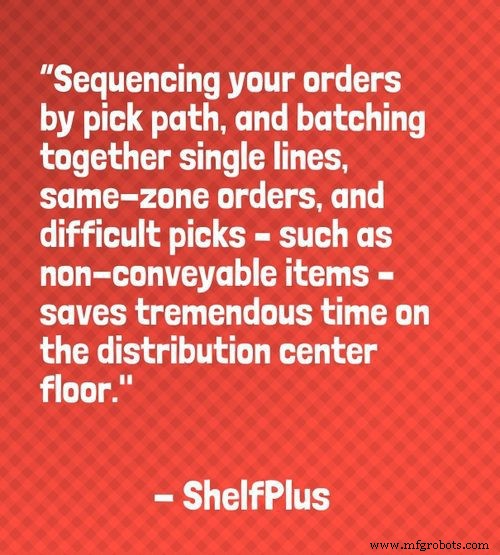
39. Use your WMS software to sequence orders and organize the workflow. “Sequencing your orders by pick path, and batching together single lines, same-zone orders, and difficult picks – such as non-conveyable items – saves tremendous time on the distribution center floor. Again, your WMS software should be able to organize the workflow and optimize sequence performance.” – 10 Ideas for a More Efficient Warehouse Operation , ShelfPlus
40. Communicate effectively — and often. “Clearly communicating to workers your organizational goals and the processes to achieve them is one key to effective warehousing operations. When managers fail to create an environment of open and clear communication, employee productivity suffers, resulting in high turnover and wasted resources.” – Increasing Warehouse Productivity , Inbound Logistics; Twitter:@ILmagazine
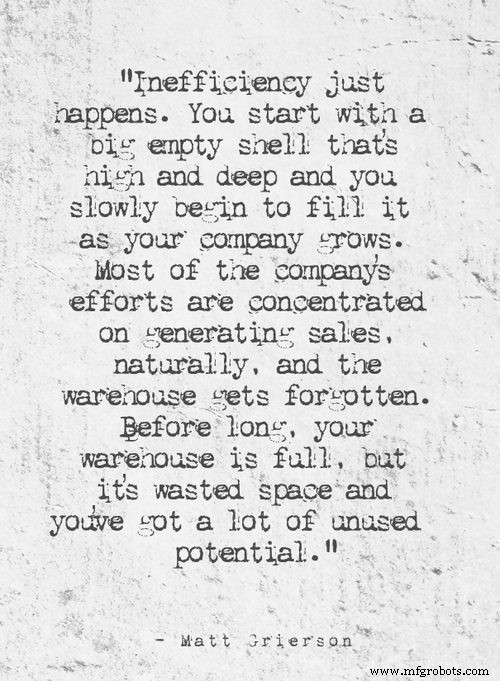
41. Make smart use of floor space. “Matt Grierson is managing director at Dexion, which provides industrial and commercial storage solutions across Europe. He says that only a small fraction of the companies that approach him believing they need to move into larger premises really do need to. The rest have enough space already, they’re just using it badly.
“Grierson says:‘Inefficiency just happens. You start with a big empty shell that’s high and deep and you slowly begin to fill it as your company grows. Most of the company’s efforts are concentrated on generating sales, naturally, and the warehouse gets forgotten. Before long, your warehouse is full, but it’s wasted space and you’ve got a lot of unused potential.’
“By using your space efficiently, your staff can get jobs done quicker and can complete more jobs in a day, you save on purchase or rent by not expanding unnecessarily, and you can go longer before the huge burden of relocating into bigger premises.
“Grierson adds:‘There are a lot of shelving options. Two-tier or mezzanine, fixed or mobile. If you can squeeze your rows of shelving together, and only open them up when access is required, you can save 50% of your floor space.'” – Tim Aldred, How to manage an effective warehouse , The Guardian; Twitter:@tim_aldred
42. Design storage systems to meet the needs of the current and planned mix of storage types. “The layout of a warehouse that supports an adjoining manufacturing facility will have different requirements than a facility supporting product distribution to stores or a facility that supports end-user fulfillment. Some operations place emphasis on replenishment of product to the point of use, others on product picking or order fulfillment.
“Regardless of the ultimate mission of the warehouse, best-practice companies have designed storage systems to meet the needs of the current and planned mix of storage types. They have optimized storage locations and layouts to fit product without the need to restack or repalletize it once received. The warehouse management system will track storage location profiles and properly assign product to the best storage location. As a result, best-practice companies have excellent cube-fill rates.
“In addition to optimizing the cubic fill of storage locations, best practice is to minimize travel time. If a product is in high demand it should be placed closer to its next point of use. In this case demand should be based on the number times the product is required, not on the number of units required. The difficulty of retrieval should also be considered in travel time. Higher-demand product should be placed on the most easily accessed storage space, typically floor level for racking and between waist and shoulder level in pick racks.” – Kate Vitasek, Storage and Inventory Control Best Practices , Multi-Channel Merchant; Twitter:@mcmerchant
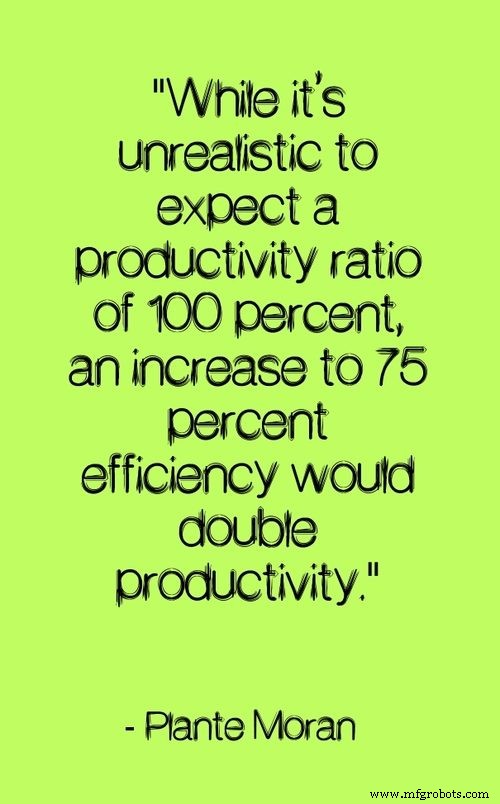
43. Reduce order processing cycle time. “In one analysis of a distribution operation, data revealed that the overall order processing cycle time was extremely inefficient. Of the total order cycle time, it was actually being worked on only 37.9 percent of the time. Six percent of the time was wasted while people dealt with problems such as waiting for lift equipment, computer issues, interruptions, and blocked aisles, and the remaining 56.1 percent of the time orders sat idle. This is a low productivity ratio by any standard. While it’s unrealistic to expect a productivity ratio of 100 percent, an increase to 75 percent efficiency would double productivity. How can this opportunity be captured? ” – Are Your Warehouse Operations Lean? , Plante Moran; Twitter:@PlanteMoran
44. Implement and maintain operational standards in all functional areas. “Maintain and use standards in all major functional areas. This will assist management in identifying systemic bottlenecks such as aisle congestion or other workflow problems.” – Warehouse Workflow Handbook , WERC; Twitter:@WERC
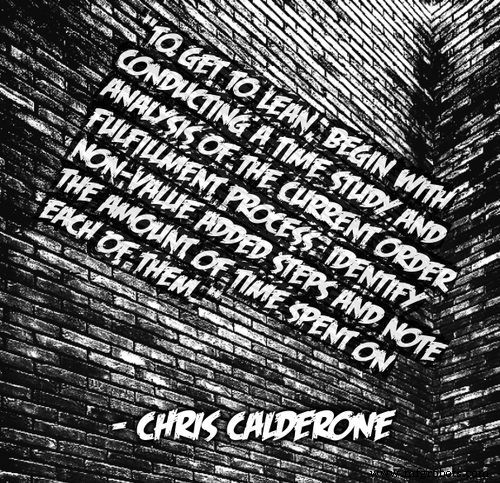
45. Improve cycle time utilization through lean applications. “Lean applications can help improve cycle time utilization, reduce costs, increase productivity, and increase customer satisfaction. To get to lean, begin with conducting a time study and analysis of the current order fulfillment process. Identify non-value added steps and note the amount of time spent on each of them. Then, assess overall workflow in an attempt to reveal inefficient product pick paths, wasted motion, excessive delays, excessive footsteps, aisle and work area congestion, and equipment availability.” – Chris Calderone, Creating a Lean HME Warehouse Operation , Lean Homecare; Twitter:@LeanHomecare
Best Practices for Improving Inventory Management
46. Reduce inventory inefficiencies. “Warehouse management systems are critical to tracking the various stages of the manufacturing process. From production to delivery, officials need to be able to monitor inventory as it makes its way through the supply chain. This is especially relevant during periods of growth, as a sudden influx of inventory may overwhelm employees on the floor, leading to costly errors. Without a robust inventory control system, managers may have difficulties locating materials or finished products, causing them to dedicate more manpower and resources to this process. Officials with Land Rover dealt with this issue on a regular basis, according to Zebra Technologies. When vehicles rolled off the assembly line, they were subject to a number of finalization processes, including testing, setting configurations and addressing any existing errors. Managers had a great deal of difficulty identifying where individual items were located along the supply chain, resulting in a high degree of uncertainty and risk.” – Nancy Master, Identifying Warehouse Management Best Practices , RFgen; Twitter:@RFgenSoftware
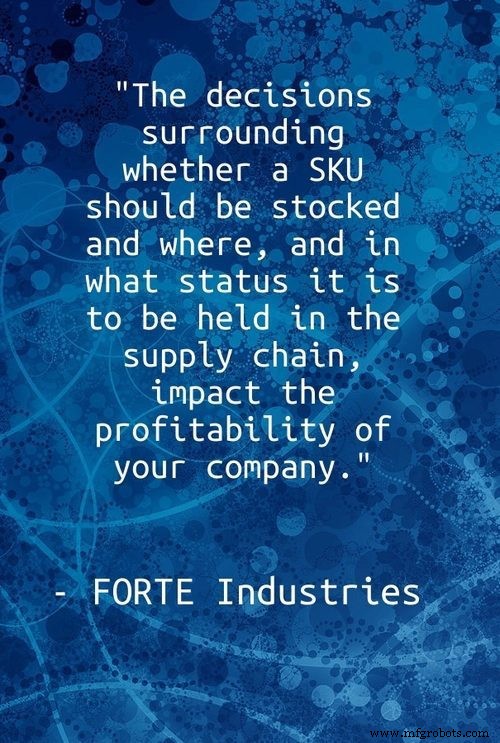
47. SKU profiling can facilitate profitability. “Understanding how every SKU carried in your distribution center (DC) can – and should – contribute to your company’s bottom line – is the best way to design and run DC operations. Here’s why:Each SKU has a potential cost impact that goes well beyond its actual purchase price. The decisions surrounding whether a SKU should be stocked and where, and in what status it is to be held in the supply chain, impact the profitability of your company. And from a selfish standpoint, these same decisions, made without sufficient evaluation, can rob your distribution center of capacity and efficiency.” FORTE Industries
48. Establish minimum holding stocks to cover lead times. “It has been established that the role of inventory management is to ensure that stock is available to meet the needs of the beneficiaries as and when required.
“Inventory represents a large cost to the humanitarian supply chain. This is made up of the cost of the inventory itself, plus the cost of transporting the goods, cost of managing the goods (labor, fumigation, repackaging, etc) and keeping the goods in warehouses. The inventory manager’s job is to make inventory available at the lowest possible cost.
“In order to achieve this, the inventory manager must ensure a balance between supply and demand by establishing minimum holding stocks to cover lead-times. To achieve this, the inventory manager must constantly liaise with the programs to keep abreast of changing needs and priorities. The warehouse must always have sufficient stocks to cover the lead-time for replacement stocks to avoid stock-outs.” – Warehousing and Inventory Management , Logistics Cluster; Twitter:@logcluster
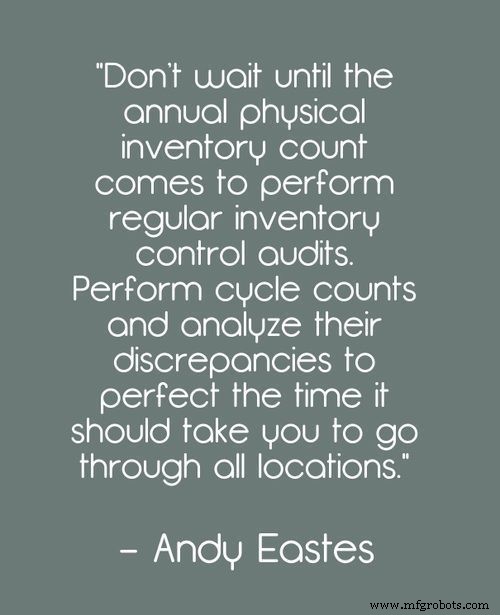
49. Perform cycle counts and analyze discrepancies. “Don’t wait until the annual physical inventory count comes to perform regular inventory control audits. Perform cycle counts and analyze their discrepancies to perfect the time it should take you to go through all locations. It’s good to have cycle counts go through all locations every quarter so that you have a more accurate back-office system.” – Andy Eastes, CEO of Agile Harbor, 10 Ways to improve warehouse efficiency and inventory management without software , SKUVault; Twitter:@skuvault
50. Develop an approved stock list for each location. “When you stock an item you are making a commitment—a commitment that the product will be available in reasonable quantities for immediate shipment or delivery to customers. Most distributors’ warehouses are filled with two things:‘stock’ and ‘stuff.’ Stock is the material you intend to be in the warehouse. That is, the items necessary to meet or exceed customers’ expectations of product availability. Stuff is everything else. You must separate the stock from the stuff in each of your warehouses. Our goal is to liquidate the stuff and arrange the stock items in such a way to minimize the cost of filling customer orders.” – John Schreibfeder, President of Effective Inventory Management, Inc., The First Step to Achieving Effective Inventory Control , via Lanham Associates; Twitter:@LanhamAssoc
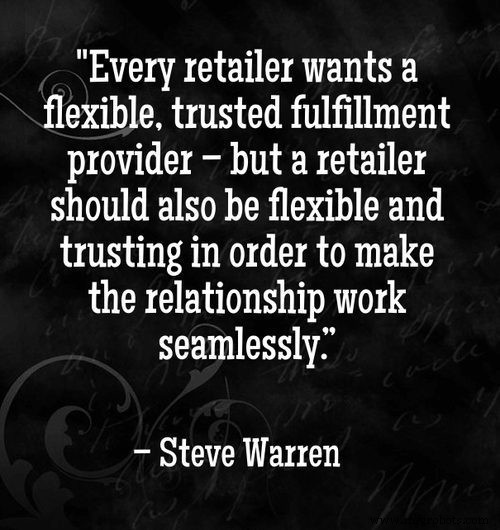
51. Maintain constant, consistent communication with vendors. “A good relationship with your vendors is crucial to your company’s success – especially if you outsource any part of your retail operations. Your fulfillment provider becomes your brand in the eyes of the customer, so it’s important that they understand your plans for your inventory as well as you do.
“This means constant communication of your promotional plans, product information, and upcoming releases. Every retailer wants a flexible, trusted fulfillment provider – but a retailer should also be flexible and trusting in order to make the relationship work seamlessly.” – Steve Warren, 4 Tips for Effective Inventory Management , Multi-Channel Merchant; Twitter:@mcmerchant
52. Achieve inventory analysis efficiency. “With solid inventory analysis, you can ensure that you are investing in the right amount of the right products to remain competitive. By developing and using a comprehensive set of tools to closely monitor the performance of your inventory, you can achieve more of your goals more efficiently.” – Bill Knapp, Socius, Beyond Software:6 Effective Inventory Management Practices , featured on the ERP Software Blog; Twitter:@erpsoftwareblog and @mssocius
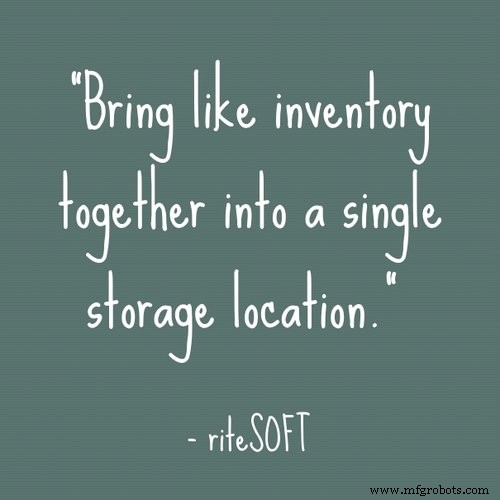
53. Understand the warning signals. “The easiest way to identify that you have too much—or the wrong inventory—is the amount of dust settled on the product in storage. If you see more than ½ inch of dust, then that’s likely a sign of obsolete inventory. However, there are other, more specific indicators that inventory management issues need to be addressed.
“If there are significant discrepancies between the book inventory and physical inventory, this is a direct indicator that there is a problem with inventory management. Another distinct indicator is when your warehouse staff is having trouble locating inventory on a timely basis—an issue that’s particularly critical when FIFO, batch/lot number or serial number controls are involved.
“The issue of locating specific inventory is typically tied to inventory discrepancies. And, of course, if you’ve seen a trend in the increased use of outside storage space, then this can indicate another ongoing inventory management issue.” – Norm Saenz and Don Derewecki of St. Onge, Inventory Management 101:Time to revisit the principles , Manajemen Logistik; Twitter:@LogisticsMgmt
54. Use both fixed and moveable tracking options. “When companies think of warehouse tracking, they think primarily of movable tracking options, tracking the units and pallets that actually get moved around the warehouse and sent up the supply chain. This is only one part of the warehouse management process – do not forget the benefits that come with used fixed trackers, too! By tracking fixed warehouse assets, you are able to assign and manage destinations much more easily, and arrange strategy protocols as needed without mass confusion. It is better to think of warehouse tracking in two different parts, one fixed and one movable.” – Justin Velthoen, 7 Tips for Warehouse Inventory Management , QStock Inventory; Twitter:@QStockInventory
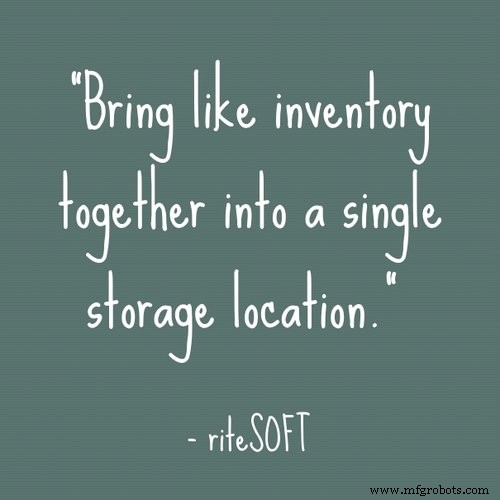
55. For physical count inventory, keep like inventory together in a single location. “Bawa inventaris seperti itu ke dalam satu lokasi penyimpanan. Bagian yang sama tidak boleh berada di beberapa area penyimpanan kecuali ukuran fisik menentukan batasan. In that case, keep available quantities to a minimum and move remainder to a location that isn’t part of the easily accessible storage (overstock location).” – Warehouse Management Tips for Physical Count Inventory , riteSOFT; Twitter:@ritesoft
Asset Tracking Solutions from Camcode:
- Kontrol Inventaris
- Inventory Management
- Custom Foil Labels
- Tanda Gudang
- Tanda Lorong
- Tag Baja Tahan Karat
- Label Lantai
- Label Keamanan
- Label Magnetik
- Tag Aset