Proses Menggambar Kawat dan Batang untuk Baja
Proses Menggambar Kawat dan Batang untuk Baja
Penarikan kawat dari batang baja adalah proses pengerjaan logam yang digunakan untuk mengecilkan penampang batang. Demikian pula batang diambil dari putaran baja dengan diameter lebih besar. Selama penarikan, volumenya tetap sama dan oleh karena itu ada pertambahan panjang dari kawat atau batang yang ditarik. Hal ini dilakukan dengan menarik kawat/batang melalui satu atau serangkaian dies gambar. Dalam hal seri cetakan gambar, cetakan gambar berikutnya harus memiliki diameter lubang yang lebih kecil dari cetakan gambar sebelumnya. Penggambaran biasanya dilakukan pada bagian bulat pada suhu kamar, sehingga diklasifikasikan sebagai proses pengerjaan dingin. Namun, ini dapat dilakukan pada suhu yang lebih tinggi untuk kabel besar guna mengurangi gaya.
Proses menggambar biasanya paling sering digunakan untuk menghasilkan penampang bulat, tetapi kotak dan bentuk lainnya juga dapat digambar. Gambar kawat/batang adalah proses industri yang penting, yang menyediakan produk komersial. Produk batang dan kawat mencakup berbagai aplikasi yang sangat luas yang mencakup poros untuk transmisi daya, mesin dan komponen struktural, blanko untuk baut dan paku keling, kabel listrik, kabel, stok kawat untuk pagar, stok batang untuk menghasilkan paku, sekrup, paku keling, pegas dan banyak lagi. Penarikan batang dari putaran baja digunakan untuk menghasilkan batang untuk pemesinan, penempaan, dan proses lainnya, dll.
Keuntungan menggambar dalam aplikasi di atas termasuk (i) kontrol dimensi yang dekat, (ii) permukaan akhir yang baik, (iii) peningkatan sifat mekanik seperti kekuatan dan kekerasan, dan (iv) kemampuan beradaptasi dengan produksi massal atau batch yang ekonomis.
Dalam proses menggambar, penampang batang atau kawat panjang dikurangi atau diubah dengan menarik (maka istilah menggambar) melalui die yang disebut draw die. Penarikan batang melalui die dilakukan dengan gaya tarik yang diterapkan pada sisi keluar die. Aliran plastik disebabkan oleh gaya kompresi, yang timbul dari reaksi logam dengan die.
Jadi, perbedaan antara menggambar dan ekstrusi adalah bahwa dalam ekstrusi material didorong melalui cetakan, sedangkan dalam menggambar ditarik melaluinya. Meskipun adanya tegangan tarik terlihat jelas dalam menggambar, kompresi juga memainkan peran penting karena bahan baja terjepit saat melewati bukaan cetakan. Untuk alasan ini, deformasi yang terjadi dalam menggambar kadang-kadang dinyatakan sebagai kompresi tidak langsung.
Variabel pemrosesan utama dalam menggambar adalah pengurangan luas penampang, sudut mati, gesekan sepanjang antarmuka benda kerja mati, dan kecepatan menggambar. Sudut cetakan mempengaruhi gaya menggambar dan kualitas produk yang ditarik.
Perbedaan mendasar antara menggambar batang dan menggambar kawat adalah ukuran bahan awal yang diproses. Gambar batang adalah istilah yang digunakan untuk menggambar batang dari putaran baja, sedangkan gambar kawat berlaku untuk menggambar kabel dari batang kawat baja. Ukuran kawat hingga 0,03 mm dimungkinkan dalam penarikan kawat.
Kecepatan penarikan untuk baja biasanya dapat mencapai 10 meter per detik untuk kawat yang sangat halus. Dalam menggambar, pengurangan luas penampang per lintasan berkisar hingga sekitar 45%. Biasanya, semakin kecil penampang awal, semakin kecil pengurangan per lintasan. Kabel halus biasanya ditarik pada pengurangan 15% hingga 25% per lintasan dan ukuran yang lebih besar pada 20% hingga 45% per lintasan. Pengurangan ringan (sizing pass) juga dapat diberikan pada rod untuk meningkatkan permukaan akhir dan akurasi dimensinya.
Penarikan batang dari putaran umumnya dilakukan sebagai operasi draft tunggal yang berarti bahwa putaran ditarik melalui satu lubang die. Karena putaran awal memiliki diameter yang besar, maka berbentuk potongan silinder lurus bukan melingkar. Ini membatasi panjang batang yang dapat ditarik. Sebaliknya, kawat ditarik dari batang kawat dalam gulungan yang terdiri dari beberapa ratus meter dan dilewatkan melalui serangkaian draw dies. Jumlah kematian biasanya bervariasi antara 4 dan 12.
Karakteristik proses penarikan kawat/batang terdiri dari (i) penarikan batang/batang kawat melalui die untuk memperkecil diameternya, (ii) penarikan menambah panjang kawat/batang saat diameternya mengecil, (iii) beberapa die digunakan secara berurutan (tandem) untuk kawat berdiameter kecil, (iv) sifat kawat/batang yang ditarik meningkat karena pengerjaan dingin, dan (v) temper kawat dapat dikontrol dengan perawatan swaging, drawing, dan annealing.
Karena proses menggambar terdiri dari menarik batang atau kawat melalui cetakan, itu menghasilkan peregangan atau pemanjangan material bersama dengan pengurangan luas penampang. Gaya tarik dibatasi oleh kekuatan material baja. Jika kawat/batang ditarik terlalu keras maka material akan putus. Gaya yang diperlukan untuk menarik kawat/batang melalui die ditentukan oleh besarnya pengurangan luas penampang. Semakin besar pengurangannya, semakin besar gaya yang dibutuhkan. Dengan demikian dapat dilihat bahwa pengurangan diameter maksimum yang dapat dicapai dibatasi oleh kekuatan luluh baja yang ditarik.
Kekuatan luluh tergantung pada komposisi baja dan biasanya pengurangan area melalui cetakan berada di wilayah 15% hingga 45%. Jika diperlukan pengurangan yang lebih besar maka ini dilakukan dengan menarik kawat melalui serangkaian dadu, masing-masing lebih kecil dari yang sebelumnya. Namun, deformasi plastis yang dialami oleh batang/kawat baja saat ditarik melalui die cenderung meningkatkan kekerasan dan mengurangi keuletan. Di sini keuletan mengacu pada kemudahan baja dapat dideformasi. Karena proses menggambar secara seri mempersulit pengurangan penampang, seringkali perlu dilakukan proses annealing antara penarikan yang berurutan untuk membantu proses deformasi baja. Di sisi lain, peningkatan kekuatan tarik yang dihasilkan dari penarikan sering dianggap sebagai sifat material yang sangat diinginkan.
Diameter yang sangat kecil dapat diperoleh dengan operasi penarikan berturut-turut melalui cetakan dengan diameter yang semakin kecil. Annealing sebelum setiap rangkaian reduksi memungkinkan persentase reduksi yang besar. Dalam proses menggambar baja proses anil juga disebut paten.
Penarikan kawat biasanya dilakukan dalam keadaan dingin, meskipun ada beberapa kasus di mana batang/kawat baja ditarik panas untuk meningkatkan keuletan. Pelumasan cetakan sangat penting dalam menggambar dingin untuk mencapai permukaan akhir yang baik serta untuk memaksimalkan masa pakai cetakan.
Penarikan kawat melibatkan peregangan logam ke bentuk yang diinginkan, dan karena itu dianggap sebagai deformasi daripada proses pelepasan. Sebuah keuntungan yang signifikan dari menggambar adalah bahwa ada sedikit limbah material. Namun, manfaat ini harus disesuaikan dengan tingginya biaya dies dan kemungkinan kebutuhan untuk melakukan anil untuk melawan pengerasan kerja.
Proses menggambar ditunjukkan pada Gambar 1. Pada gambar 'Do' adalah diameter awal batang dan 'Df' adalah diameter setelah menggambar. 'F' adalah gaya yang diterapkan. 'Alpha' adalah sudut mati dan 'Lc' adalah garis kontak.
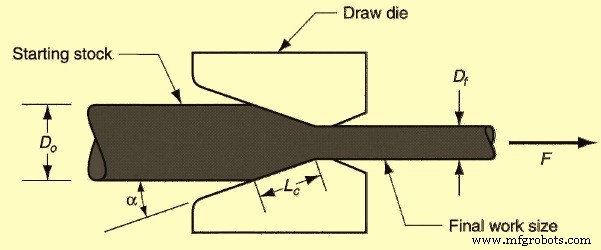
Gbr 1 Proses menggambar
Dengan menarik batang atau kawat melalui die, penampang berkurang. Persentase pengurangan luas (% r) diberikan oleh persamaan berikut “% r =100 x (Ao – Af)/Ao” Dimana 'Ao' adalah luas awal dan 'Af' adalah luas akhir kawat/batang setelah menggambar.
Proses menggambar
Sebelum menggambar yang sebenarnya, bahan yang akan digambar disiapkan dengan benar. Ini melibatkan tiga langkah yaitu (i) anil, (ii) pembersihan, dan (iii) penunjukan. Tujuan dari annealing adalah untuk meningkatkan daktilitas bahan awal untuk menerima deformasi selama menggambar. Annealing juga terkadang diperlukan di antara langkah-langkah dalam menggambar terus menerus. Pembersihan batang/putaran kawat diperlukan untuk mencegah kerusakan permukaan kerja dan draw die. Ini melibatkan penghapusan kontaminan permukaan (misalnya, kerak dan karat) dengan cara pengawetan kimia atau peledakan tembakan. Dalam beberapa kasus, pra-pelumasan permukaan kerja dilakukan setelah pembersihan. Penunjukan melibatkan pengurangan diameter ujung awal batang/putaran kawat sehingga dapat dimasukkan melalui cetakan undian untuk memulai proses. Ini biasanya dilakukan dengan swaging, rolling, atau turning. Ujung runcing dari batang/putaran kawat kemudian dicengkeram oleh carriage jaw atau perangkat lain untuk memulai proses menggambar.
Dalam hal penarikan kawat/batang baja tahan karat, permukaan batang/bulat kawat diperiksa terlebih dahulu. Hal ini dilakukan dengan pengujian tarik dan kekerasan, dan pengukuran diameter. Persiapan permukaan dilakukan dengan pengawetan dalam asam (baja feritik dan martensit) atau larutan basa (baja austenitik). Kulit yang telah disiapkan kemudian dilapisi dengan pelumas. Penarikan dingin dilakukan melalui cetakan berlian atau cetakan tungsten karbida sampai diameter yang diinginkan tercapai. Pembersihan minyak/pelumas kemudian dilakukan dan kawat dipanaskan (anil pada sekitar 1100 derajat C atau ditambah skin pass).
Peralatan menggambar
Penarikan rod dengan diameter lebih besar dilakukan pada draw bench yang terdiri dari entry table, die stand (yang berisi draw die), carriage, dan exit rack. Kereta digunakan untuk menarik stok melalui draw die. Ini didukung oleh silinder hidrolik atau rantai yang digerakkan motor. Dudukan cetakan sering kali dirancang untuk menampung lebih dari satu cetakan, sehingga beberapa batang dapat ditarik secara bersamaan melalui cetakannya masing-masing.
Wire drawing dilakukan pada mesin continuous drawing yang terdiri dari beberapa draw dies, dipisahkan dengan mengumpulkan drum di antara die. Setiap drum, yang disebut penggulung atau blok, digerakkan oleh motor untuk memberikan gaya tarik yang tepat untuk menarik stok kawat melalui die hulu. Ini juga mempertahankan ketegangan sederhana pada kawat saat melanjutkan ke undian berikutnya dalam seri. Setiap dadu memberikan sejumlah pengurangan tertentu pada kawat, sehingga pengurangan total yang diinginkan tercapai oleh seri. Tergantung pada baja yang akan diproses dan reduksi totalnya, anil kawat terkadang diperlukan di antara kelompok cetakan dalam rangkaian.
Draw bench untuk menggambar batang dan menggambar kawat kontinu ditunjukkan pada Gambar 2.
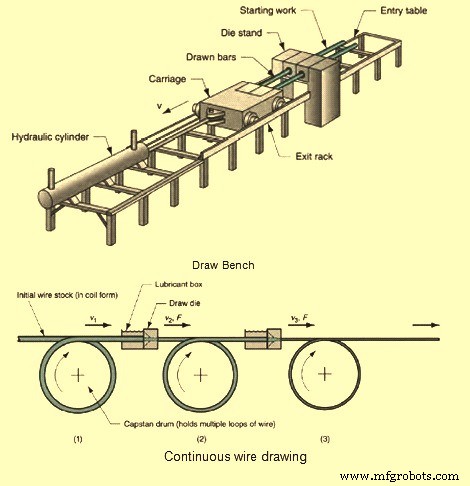
Gbr 2 Gambar bangku untuk menggambar batang dan menggambar kawat bersambung
Hasil undian
Terminologi die tipikal yang digunakan untuk menggambar batang/kawat ditunjukkan pada Gambar 3. Die draw tipikal memiliki empat daerah yang berbeda. Daerah-daerah tersebut adalah (i) masuk, (ii) sudut pendekatan, (iii) permukaan bantalan (daratan), dan (iv) relief belakang. Daerah entri biasanya berupa mulut berbentuk lonceng yang tidak bersentuhan dengan benda kerja. Bentuk bel menyebabkan tekanan hidrostatik meningkat dan mendorong aliran pelumas ke dalam cetakan dan mencegah goresan batang kawat/putaran ditarik dan permukaan cetakan. Pendekatan adalah tempat proses menggambar terjadi. Berbentuk kerucut dengan sudut (setengah sudut) biasanya berkisar antara 6 derajat sampai 20 derajat. Sudut yang tepat bervariasi sesuai dengan batang kawat/bahan bulat. Permukaan bantalan, atau tanah, menentukan ukuran kawat/batang yang ditarik akhir. Ini menghasilkan gaya hambat gesekan pada kawat/batang dan juga menghilangkan kerusakan permukaan akibat keausan die, tanpa mengubah dimensi. Terakhir, relief belakang adalah zona keluar. Ini dilengkapi dengan sudut relief belakang (setengah sudut) sekitar 30 derajat. Relief belakang memungkinkan material baja sedikit mengembang saat kawat meninggalkan cetakan dan juga meminimalkan abrasi jika gambar berhenti atau cetakan tidak sejajar.
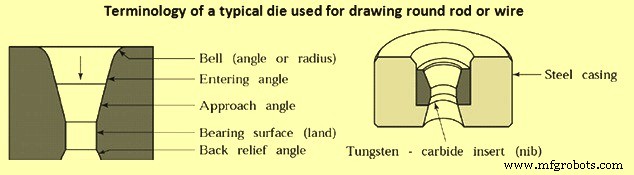
Gbr 3 Terminologi sebuah dadu biasa
Draw die terbuat dari baja perkakas atau karbida yang disemen. Untuk menggambar panas, cetakan baja tuang digunakan karena ketahanannya yang tinggi terhadap keausan pada suhu tinggi. Dies untuk operasi penarikan kawat berkecepatan tinggi sering menggunakan sisipan yang terbuat dari berlian (baik sintetis maupun alami) untuk permukaan aus. Semen karbida terdiri dari karbida titanium, tungsten, nikel, molibdenum, dan tantalum. Karbida yang disemen adalah yang paling banyak digunakan untuk menggambar dies karena kekuatan, ketangguhan, dan ketahanan ausnya yang unggul. Dies berlian digunakan untuk menggambar kawat halus dengan diameter mulai dari 2 mikrometer hingga 1,5 mm. Mereka terbuat dari berlian kristal tunggal atau dalam bentuk polikristalin dengan partikel berlian dalam matriks logam (kompak). Berlian polikristalin digunakan untuk menggambar kawat mati memiliki umur mati lebih lama, ketahanan yang tinggi terhadap aus, retak atau bantalan. Kedua karbida dan cetakan berlian biasanya digunakan sebagai sisipan atau ujung, yang disangga dalam selubung baja.
Mekanika menggambar kawat
Deformasi selama penarikan kawat/batang dipengaruhi oleh sejumlah faktor yang meliputi kimia baja, sudut pendekatan, pelumasan, kecepatan penarikan, dan reduksi sebagai yang paling signifikan.
Meskipun fakta bahwa volume tidak hilang selama deformasi sudah jelas, pada kenyataannya, ini adalah konsep yang sangat berguna yang membentuk dasar untuk menganalisis sejumlah masalah menggambar. Salah satu aplikasi yang paling umum melibatkan penentuan kecepatan kawat pada dudukan yang berbeda dan kecepatan penggulung yang diperlukan yang akan digunakan. Secara sederhana, keteguhan volume menyatakan bahwa laju volumetrik kawat yang masuk ke sebuah dadu harus sama dengan yang keluar. Karena luas penampang berkurang selama penarikan, kawat harus meningkatkan kecepatan untuk laju volumetrik material yang sama untuk masuk dan keluar dari cetakan. Laju volumetrik didefinisikan sebagai luas penampang kawat dikalikan dengan kecepatan kawat.
Dalam penarikan multi-pass, kecepatan kawat yang keluar dari setiap cetakan meningkat sehingga laju volumetrik aliran logam sama di semua cetakan. Oleh karena itu, penggulung, yang memiliki kecepatan sudut yang sama dengan kecepatan kawat keluar, digunakan untuk menarik kawat melalui cetakan setelah setiap reduksi. Jika hal ini tidak dilakukan, kawat putus karena tegangan kawat yang tidak seimbang antara cetakan.
Diameter kawat meningkat seiring dengan keausan cetakan gambar selama proses menggambar. Oleh karena itu, berdasarkan kekonstanan volume, kecepatan kawat berkurang seiring dengan bertambahnya ukuran dadu. Jika kecepatan linier dari penggulung penarik dicocokkan dengan ukuran kawat dari die baru, kecepatan penggulung menjadi lebih cepat dari kecepatan kawat saat diameter kawat meningkat. Kecepatan penggulung yang meningkat ini menerapkan tegangan tarik tinggi pada kawat, sering kali merusak kawat. Oleh karena itu, penggulung di unit gambar multi-lintasan dirancang sedemikian rupa sehingga kawat tergelincir pada penggulung saat die aus dan kecepatan kawat berkurang. Slip difasilitasi dengan membatasi jumlah lilitan di sekitar penggulung penarik dan membasahi permukaan kawat dan penggulung dengan pelumas penarik.
Meskipun tampaknya gaya dan daya dalam wiredrawing dapat dianalisis dengan menggunakan tegangan sederhana, kondisi deformasi pada kawat sebenarnya jauh lebih kompleks karena gaya tekan dan gaya drag yang dihasilkan oleh permukaan die. Gaya tarik mewakili gaya total yang diperlukan untuk diterapkan pada balok mati untuk mengatasi gesekan pada permukaan cetakan dan ketahanan material baja yang mengalami deformasi. Karena gaya tarik ditransmisikan oleh bahan yang tidak didukung, gaya tarik harus dibatasi untuk mencegah terjadinya deformasi plastis di luar cetakan. Jadi, tegangan luluh dari kawat yang ditarik merupakan batas atas dari tegangan tarik yang diijinkan. Praktik menggambar yang diterima biasanya membatasi tegangan tarik hingga 60% dari kekuatan luluh kawat yang ditarik. Tegangan tarik diperoleh dengan membagi gaya tarik dengan luas penampang kawat yang ditarik.
Meskipun secara umum tampak bahwa kerja atau energi yang dikonsumsi pada tempat penarikan ditentukan oleh bahan dan pengurangan yang diambil, jumlah aktual yang dibutuhkan jauh lebih tinggi dalam praktiknya. Ini disebabkan oleh inefisiensi yang ada selama deformasi, yang terutama diatur oleh sudut pendekatan. Inefisiensi tersebut tidak memberikan kontribusi yang berguna dalam mengurangi luas penampang dan umumnya hanya berfungsi untuk meningkatkan kebutuhan energi dan mempengaruhi kualitas kawat/batang. Kerja total yang digunakan pada draw stand dapat dipartisi menjadi tiga komponen yaitu (i) kerja homogen yang berguna yang diperlukan untuk mengurangi penampang, (ii) kerja yang diperlukan untuk mengatasi tahanan gesek, dan (iii) kerja redundan (tidak homogen) yang diperlukan untuk mengubah arah aliran.
Pekerjaan homogen ditentukan oleh penarikan (reduksi), dan pada dasarnya tidak tergantung pada sudut pendekatan. Gesekan dan kerja redundan, di sisi lain, digabungkan erat dengan geometri die dan memiliki efek yang berlawanan ketika sudut pendekatan diubah. Dalam kondisi penarikan normal, kerugian tipikal berada pada urutan 20% untuk pekerjaan gesekan dan sekitar 12% untuk pekerjaan yang berlebihan.
Kerja redundan dan kerja gesekan memiliki efek buruk pada sifat kawat selain meningkatkan energi yang dibutuhkan untuk menggambar. Salah satu konsekuensinya adalah bahwa sifat mekanik tidak homogen di seluruh penampang kawat. Karena deformasi redundan dan gesekan terkonsentrasi di dekat permukaan kawat, tingkat pengerasan regangan yang lebih tinggi menghasilkan lapisan permukaan dan dekat permukaan (analog dengan temper rolling) dan lebih besar daripada regangan yang dihasilkan dari pengurangan penampang. Juga, deformasi berlebihan memiliki efek buruk pada keuletan.
Daktilitas berbanding terbalik dengan regangan dan karenanya, deformasi berlebihan juga bertindak untuk membatasi jumlah lintasan dan pengurangan maksimum yang dapat diambil sebelum anil. Bahkan jika hal ini tidak menyebabkan masalah dalam menggambar, kerugian daktilitas yang dihasilkan dapat menyebabkan keretakan pada proses pembentukan berikutnya seperti pembengkokan dan pos dingin.
Lapisan pada permukaan kawat/batang biasanya tidak hanya mengalami perubahan penampang, tetapi juga mengalami deformasi akibat gaya geser karena gaya hambat yang diberikan oleh permukaan die. Bahkan untuk permukaan die yang sangat dipoles dan pelumasan hidrodinamik, sejumlah kerja gesekan selalu ada. Kerja friksi mendominasi pada sudut die rendah di mana gaya hambat permukaan meningkat sebagai akibat dari panjang kontak yang lebih tinggi di zona pendekatan untuk pengurangan tertentu. Pekerjaan gesekan dapat dikurangi dengan menggunakan sudut pendekatan yang lebih besar dan, pada tingkat yang lebih rendah, dengan meningkatkan pelumasan atau kondisi permukaan mati. Meskipun gaya gesekan juga berhubungan dengan beban mati, biasanya sedikit usaha yang dilakukan untuk mengendalikan gesekan dengan membatasi pengurangan karena ini memerlukan penyangga tambahan. Sebaliknya, praktik normal adalah mengoptimalkan sudut pendekatan dan efektivitas pelumasan.
Saat kawat memasuki zona pendekatan dari cetakan gambar, lapisan material di dekat permukaan mengalami deformasi karena pengurangan luas dan perubahan arah aliran, yaitu, lentur untuk menyesuaikan dengan perubahan arah dari zona pendekatan ke zona bantalan dari mati. Deformasi redundan, seperti deformasi gesekan, tidak terdistribusi secara merata di atas kawat dan biasanya maksimum pada permukaan dengan peningkatan kekerasan yang sesuai. Deformasi redundan didorong oleh sudut die yang lebih besar karena material yang lebih jauh dari garis tengah mengalami perubahan arah yang lebih tajam daripada material di dekat garis tengah dan karenanya mengalami tingkat distorsi yang lebih tinggi. Deformasi redundan mempengaruhi tingkat tegangan sisa pada kawat yang ditarik. Ketika sudut pendekatan meningkat, gradien deformasi antara permukaan dan garis tengah juga meningkat. Hal ini menyebabkan tegangan tarik yang semakin tinggi pada permukaan dan tegangan tekan pada inti. Efek sebaliknya terjadi selama penarikan, dan semburan tengah dapat terjadi karena tingginya tingkat tegangan tarik yang dihasilkan di inti kawat.
Pemilihan sudut die yang tepat sangat penting untuk keberhasilan setiap operasi wiredrawing. Berdasarkan fakta bahwa kerja gesek meningkat dengan menurunnya sudut die dan kerja redundan meningkat dengan meningkatnya sudut die, sudut pendekatan yang optimal harus ada. Sudut pendekatan yang optimal meminimalkan kerja gesekan dan redundan dan, sebagai akibatnya, gaya tarik. Selain meminimalkan kebutuhan gaya, sudut mati yang optimal juga memberikan peningkatan kualitas permukaan dan penyelesaian.
Geometri bagian kerja (zona pendekatan) dari die adalah faktor kunci dalam wiredrawing. Geometri ini dapat ditentukan oleh faktor delta, yang merupakan rasio busur lingkaran yang membentang di titik tengah permukaan cetakan dengan panjang kontak antara kawat/batang dan cetakan. Nilai delta yang rendah (semi-sudut kecil atau pengurangan luas yang lebih tinggi) menunjukkan efek gesekan yang lebih besar dan pemanasan permukaan karena kontak kawat/batang yang lebih lama di zona pendekatan. Nilai delta yang lebih tinggi (semi-angle besar atau pengurangan area yang lebih rendah) menunjukkan peningkatan tingkat deformasi redundan dan pengerasan permukaan karena perubahan arah yang berlebihan selama aliran melalui die. Delta besar sering menghasilkan kecenderungan yang lebih besar ke arah pembentukan rongga dan pusat ledakan. Nilai delta 1,50 berkinerja baik di banyak operasi penarikan komersial, sedangkan faktor delta lebih dari 3,0 harus dihindari secara umum.
Gambar dies hanya dapat mengekstrak panas dalam jumlah kecil, sehingga perhatian yang tepat harus diberikan pada pendinginan inter-pass, terutama pada tahap reduksi selanjutnya. Sementara sebagian panas dipindahkan ke cetakan, sebagian besar tetap di kawat dan upaya untuk menggunakan pendinginan mati untuk mengurangi suhu kawat terbukti sebagian besar tidak berhasil. Berbagai penelitian tentang keefektifan pendinginan die menemukan bahwa die biasanya menghilangkan kurang dari 5% hingga 20% dari panas yang dihasilkan dalam kawat. Hal ini disebabkan oleh fakta bahwa area tertentu dari kawat yang bersentuhan dengan permukaan cetakan hanya seperseribu detik. Meskipun cetakan diharapkan hanya menghilangkan sedikit panas dari kawat, suhu cetakan tidak dapat diabaikan, dan pendinginan kotak cetakan seringkali diperlukan. Ini terutama benar ketika sisipan karbida digunakan dalam selubung baja karena perbedaan besar dalam koefisien muai panas.
Aturan praktis yang baik untuk kenaikan suhu per lintasan dalam gambar kering (selain cetakan pertama) adalah 60 derajat C hingga 80 derajat C untuk baja ringan dan 100 derajat C hingga 160 derajat C untuk baja karbon tinggi. Nilai-nilai ini dibelah dua untuk menggambar basah. Tiga mode pendinginan kawat yang biasanya digunakan adalah (i) pendinginan langsung di mana air atau pendingin disemprotkan ke kawat yang keluar dari cetakan atau pada penggulung pengambil, (ii) pendinginan tidak langsung di mana air atau pendingin disemprotkan ke selubung cetakan atau disirkulasikan di bagian dalam pada selubung mati atau blok pengambil, dan (iii) ledakan udara di mana udara paksa mengenai kawat pada blok atau penggulung.
Pendinginan inter-pass sering kali menggunakan pendinginan air langsung pada kawat yang keluar dari cetakan gambar, dan menggunakan panas sisa dalam kawat untuk menghilangkan air terakhir dengan penguapan. Pendinginan langsung dikombinasikan dengan pendinginan blok internal dapat membawa suhu kawat di bawah 120 derajat C, yang merupakan suhu awal yang wajar untuk pengurangan berikutnya. Penting untuk mencegah oksidasi dan pengotoran permukaan internal blok untuk menjaga perpindahan panas yang baik antara kawat panas dan air pendingin. Cara efektif untuk mendinginkan kawat yang ditarik (i) memastikan bahwa kawat masuk ke die sedingin praktis, (ii) menghindari pengurangan berat, (iii) menggunakan pelumasan sebaik mungkin, (iv) mempertimbangkan untuk menggunakan tarikan balik, (v) menambah interval waktu antara pengurangan, (vi) menambah jumlah lilitan pada balok, dan (vii) menambah diameter balok.
Dua variabel utama yang mengontrol umur die adalah tekanan dan temperatur. Tekanan yang bekerja pada die dalam wiredrawing jauh lebih rendah daripada yang ditemukan dalam operasi pembentukan dingin lainnya. Oleh karena itu, suhu seringkali merupakan faktor yang jauh lebih penting dalam mengendalikan kehidupan die. Meskipun tampaknya logis bahwa keausan terjadi secara seragam di sepanjang zona pendekatan, hal ini tidak terjadi dalam praktiknya. Keausan maksimum (diukur dalam kehilangan volume) biasanya terjadi pada titik di mana kawat/batang awalnya bersentuhan dengan die. Di sana, kawah annular dalam terbentuk, yang biasanya dikenal sebagai 'cincin aus'. Dering terjadi karena bidang tumbukan kawat/batang pada die berosilasi pada posisi rata-rata karena ketidakteraturan ukuran dan getaran kawat. Akibatnya, zona sempit lubang mati mengalami beban siklik dengan kegagalan subkutan akhirnya karena kelelahan.
Setelah cincin keausan berkembang, deformasi dapat terjadi sebelum titik kontak pada cetakan gambar. Ini disebut 'bulging' dan dihasilkan dari pencadangan atau gangguan pada daerah dekat permukaan kabel saat kontak dilakukan di lokasi cincin aus di cetakan. Penggembungan yang terjadi pada titik kontak awal di tenggorokan mati membatasi masuknya pelumas ke cetakan dan mempercepat keausan cetakan. Jumlah keausan yang lebih sedikit terjadi di sepanjang panjang kontak zona pendekatan, meskipun di sini keausan juga tidak seragam dan sering kali menghasilkan permukaan keausan oval daripada lingkaran.
Kawat yang meluncur melawan area kerja dari cetakan gambar menyebabkan keausan cetakan sehingga keausan tergantung pada luas permukaan kawat, dan akibatnya panjang kawat yang melewati cetakan gambar. Seringkali, umur mati diukur dalam hal berat kawat yang ditarik atau waktu penarikan. Namun, ukuran tersebut harus diubah menjadi panjang kawat yang ditarik untuk mendapatkan indikasi mendasar dari keausan die. Oleh karena itu, ukuran praktis umur cetakan adalah panjang rata-rata kawat yang ditarik per satuan pertambahan diameter cetakan. Sebagai aturan umum, baja yang memiliki kekuatan luluh tinggi lebih tahan aus. Namun, penelitian terbaru menunjukkan bahwa kekerasan die tidak mengontrol keausan die, yaitu, peningkatan kekerasan material die tidak menyebabkan peningkatan substansial dalam masa pakai die.
Cacat gambar
Cacat pada kawat/batang yang ditarik dapat disebabkan oleh cacat pada bahan awal (jahitan, sliver dan pipa) atau dapat disebabkan oleh proses deformasi.
Cacat khas pada kawat/batang yang ditarik adalah retak tengah. Pusat cacat pecah atau retak (cupping) terjadi untuk sudut mati rendah pada reduksi rendah. Retak tengah dapat terjadi pada produk yang ditarik karena sudut cetakan yang lebih besar, reduksi per lintasan yang lebih rendah, dan gesekan, dll. Jenis cacat utama lainnya pada gambar adalah jahitan, yang merupakan goresan memanjang atau lipatan pada material. Jahitan dapat terbuka selama operasi pembentukan berikutnya (seperti mengganggu, menyundul, menggulung benang, atau menekuk batang atau kawat), dan dapat menyebabkan masalah kontrol kualitas yang serius. Berbagai cacat permukaan lainnya (seperti goresan dan bekas cetakan) juga dapat diakibatkan oleh pemilihan parameter proses yang tidak tepat, pelumasan yang buruk, atau kondisi cetakan yang buruk.
Karena bahan yang ditarik mengalami deformasi yang tidak seragam selama menggambar, produk yang ditarik dingin biasanya memiliki tegangan sisa. Untuk reduksi ringan, seperti hanya beberapa persen, tegangan sisa permukaan memanjang bersifat tekan (sementara sebagian besar dalam tegangan) dan umur kelelahan ditingkatkan. Sebaliknya, pengurangan yang lebih berat menginduksi tegangan permukaan tarik (sementara sebagian besar dalam kompresi). Tegangan sisa dapat menjadi signifikan dalam menyebabkan retakan korosi tegangan pada bagian dari waktu ke waktu. Selain itu, mereka menyebabkan komponen melengkung jika lapisan material kemudian dihilangkan seperti dengan menggorok, mengerjakan mesin, atau menggiling.
Batang yang tidak cukup lurus (atau disuplai sebagai kumparan) dapat diluruskan dengan melewatkannya melalui susunan gulungan yang ditempatkan pada sumbu yang berbeda.