Produksi Silico-Mangan dalam Tungku Busur Terendam
Produksi Siliko-Mangan dalam Tungku Busur Terendam
Silico-mangan (Si-Mn) adalah paduan yang digunakan untuk menambahkan silikon (Si) dan mangan (Mn) ke baja cair selama pembuatan baja dengan kandungan karbon rendah (C). Paduan Si-Mn standar mengandung 65% hingga 70% Mn, 15% hingga 20% Si dan 1,5% hingga 2% C. Nilai paduan Si-Mn adalah karbon sedang (MC) dan karbon rendah (LC). Industri pembuatan baja adalah satu-satunya konsumen paduan ini. Penggunaan Si-Mn selama pembuatan baja sebagai pengganti campuran paduan ferro-mangan (Fe-Mn) karbon tinggi dan paduan ferro-silikon (Fe-Si) didorong oleh pertimbangan ekonomi.
Baik Mn dan Si adalah konstituen penting dalam pembuatan baja. Mereka digunakan sebagai deoxidizers, desulphurizers dan elemen paduan. Si adalah deoxidizer utama. Mn adalah deoxidizer yang lebih ringan daripada Si tetapi meningkatkan efektivitas karena pembentukan silikat mangan dan aluminat yang stabil. Ini juga berfungsi sebagai desulfurizer. Mangan digunakan sebagai elemen paduan di hampir semua jenis baja. Yang menarik adalah efek modifikasinya pada sistem besi-karbon (Fe-C) dengan meningkatkan kemampuan mengeras baja.
Si-Mn diproduksi oleh reduksi karbo-termik bahan baku oksida dalam tiga fase, arus bolak-balik (AC), tungku busur terendam (SAF) yang juga digunakan untuk produksi Fe-Mn. Pengoperasian proses produksi Si-Mn seringkali lebih sulit daripada proses produksi Fe-Mn karena diperlukan suhu proses yang lebih tinggi. Ukuran umum SAF yang digunakan untuk produksi Si-Mn biasanya berkisar antara 9 MVA hingga 40 MVA yang menghasilkan 45 ton hingga 220 ton Si-Mn per hari.
Dalam reduksi karbo-termik bahan baku oksida, panas sama pentingnya untuk reduksi seperti C, karena reaksi reduksi endotermik dan kekurangan panas dapat menyebabkan tidak lengkap. Penetrasi elektroda yang baik sangat penting untuk memiliki panas yang cukup untuk mendorong reaksi hingga selesai.
Bahan baku yang digunakan dalam produksi Si-Mn terutama terdiri dari bijih Mn, terak Fe-Mn C tinggi, kuarsit, kokas dan batubara, serta fluks (dolomit atau kalsit). Sumber utama Mn dalam bahan baku produksi Si-Mn adalah bijih Mn dan terak yang kaya Mn dari produksi C Fe-Mn yang tinggi. Bahan muatan yang berbeda menunjukkan perilaku yang berbeda pada pemanasan dan reaksi dengan C, yang mempengaruhi konsumsi kokas dan energi listrik, jumlah terak dan komposisinya, dan produktivitas tungku.
Jumlah produksi terak per ton logam Si-Mn terutama ditentukan oleh rasio bijih/terak. Peningkatan porsi terak Fe-Mn dengan mengorbankan bijih Mn menyebabkan rasio terak/logam yang lebih besar dalam proses produksi Si-Mn. Volume terak yang tinggi menyebabkan peningkatan konsumsi energi dan mungkin kehilangan inklusi logam yang lebih tinggi dalam terak akhir.
Bijih Mn umumnya mengandung unsur-unsur yang tidak diinginkan yang tidak dapat dihilangkan selama tahap penambangan dan pemrosesan. Dalam hal ini kandungan P (fosfor) penting karena permintaan yang ketat dari elemen ini dalam paduan Si-Mn. Fe, P dan As (arsenik) lebih mudah direduksi daripada Mn dan karenanya mereka masuk lebih dulu ke dalam logam. Kandungan mereka dalam paduan akhir dengan demikian dikendalikan oleh pemilihan bijih. Terak Fe-Mn C tinggi adalah sumber Mn yang sangat murni karena pengotor yang mudah tereduksi dalam bijih telah diambil oleh logam Fe-Mn C tinggi selama produksinya. Kandungan pengotor, seperti P, dalam paduan Si-Mn dengan demikian dikendalikan, tidak hanya oleh pemilihan bijih Mn, tetapi juga oleh jumlah relatif bijih Mn dan terak C Fe-Mn yang tinggi dalam campuran bahan baku.
Suhu proses dalam kisaran 1600 derajat C hingga 1650 derajat C diperlukan untuk mendapatkan paduan Si-Mn dengan kandungan Si yang cukup tinggi dan untuk menghasilkan terak buangan dengan MnO rendah. Terak Fe-Mn memiliki suhu leleh yang relatif rendah (sekitar 1250 derajat C) dibandingkan dengan bijih Mn. Oleh karena itu, bagian terak Fe-Mn yang tinggi cenderung memberikan suhu proses yang lebih rendah. Ketika bijih Mn mulai meleleh pada sekitar 1350 derajat C, biasanya mengandung campuran fase padat dan cair, di mana fase padatnya adalah MnO. Pemanasan dan reduksi lebih lanjut hingga 1550 derajat C atau lebih diperlukan sebelum bijih yang meleleh bercampur dengan terak dan mengalir dengan bebas. Dengan bagian yang tinggi dari bijih Mn dalam campuran, suhu permukaan dan suhu proses di zona lapisan kokas biasanya lebih tinggi.
Untuk produksi Si-Mn di SAF, C (coke dan batubara) digunakan sebagai reduktor sementara panas disuplai oleh listrik. Arus listrik dikirim melalui muatan, dan panas dibuat sesuai dengan P =R*I2, di mana P adalah efeknya yaitu panas yang dihasilkan, R adalah hambatan muatan dan I adalah rapat arus.
Dalam SAF ujung elektroda terendam dalam campuran muatan berpori, dan energi listrik dibebaskan oleh busur mikro ke tempat tidur kokas kaya terak yang mengambang di atas bak paduan cair. Kebutuhan panas disuplai sebagai energi listrik dan kokas bertindak baik sebagai agen pereduksi dan elemen hambatan listrik. Tungku berbentuk lingkaran, dengan diameter luar 11,6 m dan tinggi 6,2 m menjadi ciri khas tungku 40 MVA. Reaksi yang terjadi selama produksi Si-Mn diberikan di bawah ini.
Reduksi Si dan Mn dalam produksi Si-Mn terjadi melalui serangkaian langkah reduksi yang berbeda berikut ini.
(SiO2) + 2C =Si + 2CO (g)
(SiO2) + 2SiC =3Si + 2CO (g)
(MnO) + C =Mn + CO (g)
(SiO2) + 2Mn =Si + 2(MnO)
(SiO2) + Si =2SiO (g)
Mn =Mn (g)
Reaksi kesetimbangan utama yang mengontrol distribusi Si dan Mn antara terak dan paduan Si-Mn adalah sebagai berikut.
(MnO) + C =Mn + CO (g)
(SiO2) + 2C =Si + 2CO (g)
Tanda kurung menunjukkan bahwa spesies ada dalam terak, sedangkan garis bawah menunjukkan spesies dalam paduan. C adalah sumber karbon, yang dapat dilarutkan dalam paduan atau padatan, yaitu kokas.
Kesetimbangan terak / paduan / gas yang lengkap membutuhkan pembentukan kesetimbangan yang simultan untuk kedua reaksi. Kedua reaksi tersebut sangat bergantung pada suhu dan tekanan CO dari sistem. Temperatur yang lebih tinggi memberikan keseimbangan kandungan Si dalam paduan Si-Mn yang lebih tinggi dan kandungan MnO yang lebih rendah pada terak yang dihasilkan. Tekanan gas CO yang rendah juga mendukung kandungan Si yang lebih tinggi dalam paduan Si-Mn dan lebih sedikit MnO dalam terak. Biasanya tekanan gas CO cukup dekat dengan 1 atmosfer di tungku busur terendam. Kombinasi dari dua reaksi di atas memberikan reaksi kesetimbangan terak / paduan parsial, yang dinyatakan dengan reaksi berikut.
2 (MnO) + Si =2Mn + (SiO2)
Reaksi ini sedikit bergantung pada suhu dan tidak bergantung pada tekanan dan komposisi fase gas.
Penggalian tungku Si-Mn 16 MW tiga fase memberikan informasi tentang distribusi fase di zona reaksi dalam tungku. Bagian dalam tungku biasanya dibagi menjadi dua area utama yaitu (i) zona pra-pemanasan dan pra-reduksi di mana komponen muatan masih padat, dan (ii) zona lapisan kokas di mana bijih, terak dan fluks cair. Dalam tungku ini, diamati bahwa oksida Mn direduksi hampir seluruhnya dari terak Fe-Mn dan bijih Mn di bagian atas unggun kokas. Hal ini ditunjukkan pada Gambar 1 yang didasarkan pada penggalian tungku 16 MW yang disebutkan di atas.
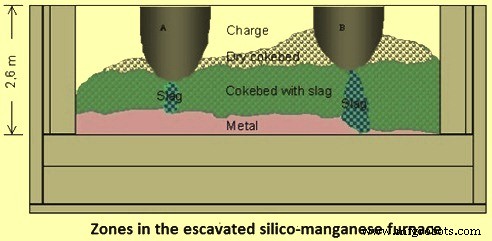
Gbr 1 Zona tungku silika-mangan
Penggalian tungku telah menunjukkan bahwa posisi ujung elektroda sekitar 600 mm di atas penangas logam telah sesuai untuk operasi yang baik. MnO2 dalam bijih didekomposisi lebih awal menjadi Mn2O3, tetapi reduksi lebih lanjut menjadi Mn3O4 oleh gas CO atau dekomposisi termal sederhana. Pra-reduksi ke MnO dengan signifikansi apa pun hanya diamati dalam denda muatan. Terak Fe-Mn yang kaya MnO direduksi hampir menjadi komposisi terak Si-Mn akhir sebelum pengurangan substansial dari pelelehan bijih Mn dimulai. Hampir semua reduksi MnO diselesaikan di bagian atas coke bed. Pembubaran dan reduksi kuarsa jelas terjadi di zona tempat tidur kokas setelah reduksi utama Mn oksida selesai. Mungkin 'pengambilan' Si dalam paduan cukup cepat dan terjadi saat logam Cair menetes ke bawah melalui tempat tidur kokas menuju wadah paduan cair.
Reduksi Mn oksida (MnO2) tertinggi terjadi dalam empat tahap. Tahap reduksi pertama dari MnO2 menjadi Mn2O3 dicapai pada suhu lebih besar dari 450 derajat C hingga 500 derajat C dan tahap kedua Mn2O3 menjadi Mn3O4 pada suhu lebih besar dari 900 derajat C hingga 950 derajat C dan keduanya dapat direalisasikan tanpa zat pereduksi dan hanya dengan dekomposisi termal. Kedua langkah dalam dekomposisi termal menunjukkan kisaran stabilitas Mn oksida. Reduksi Mn3O4 menjadi MnO hanya dimungkinkan oleh gas CO atau C padat. Pengurangan MnO oleh karbon pada tekanan atmosfer hanya dapat dilakukan pada suhu yang lebih besar dari 1410 derajat C. Untuk mencapai reduksi penuh, suhu perlu lebih tinggi lagi. Masalahnya di sini adalah tekanan uap Mn yang tinggi dan penguapan yang kuat. Dalam kasus proses produksi Mn dengan berbagai langkah reduksi, MnO pertama larut dalam fase terak dari mana Mn direduksi oleh C padat dan bergerak ke fase logam. Di sini solusi terak dan paduan yang tidak ideal sangat penting. Metode termodinamika terkini digunakan untuk menentukan fase dan neraca energi berdasarkan neraca massa.
Distribusi Si antara paduan Si-Mn dan terak multikomponen MnO-SiO2-CaO-Al2O3-MgO terutama ditentukan oleh suhu proses, kandungan SiO2 terak dan rasio R-nya yang didefinisikan sebagai (CaO + MgO) / Al2O3. Misalnya, kandungan kesetimbangan Si dalam paduan Si-Mn meningkat sekitar 6% jika rasio-R dikurangi dari 2 menjadi 1 asalkan suhu dan kandungan SiO2 konstan. Pengaruh suhu juga cukup besar. Kandungan kesetimbangan Si meningkat sekitar 6 % per 50 derajat C pada kisaran suhu 1550 derajat C hingga 1700 derajat C. Kandungan kesetimbangan MnO dalam terak Si-Mn tergantung pertama-tama pada suhu dan kedua pada kandungan SiO2 dari terak. Pada 1600 derajat C, kandungan kesetimbangan MnO menurun dari sekitar 9% pada saturasi SiO2 menjadi minimal sekitar 3% hingga 4% ketika kandungan SiO2 berkurang menjadi sekitar 40% hingga 45%.
Faktor-faktor yang mempengaruhi perolehan kembali Mn selain suhu adalah (i) kebasaan terak [(CaO + MgO) / SiO2], (ii) rasio CaO/MgO, dan (iii) kandungan Al2O3 terak. Peningkatan suhu mendukung reaksi reduksi endotermik baik secara termodinamika maupun kinetik. Pengaruh kimia terak pada reduksi Mn oksida lebih kompleks. Pemulihan Mn lebih tinggi untuk terak dasar, karena koefisien aktivitas MnO yang lebih tinggi dalam terak dasar. Penambahan kapur pada campuran bahan baku menurunkan konsentrasi kejenuhan MnO dan meningkatkan aktivitas MnO dalam terak untuk kandungan MnO yang sama. Hasilnya adalah penurunan keseimbangan konsentrasi MnO dalam terak dan peningkatan laju reduksi. Peningkatan kebasaan terak di atas 1,1 memiliki pengaruh yang kurang signifikan terhadap perolehan kembali Mn. Kandungan CaO dan MgO yang jauh lebih tinggi menghasilkan viskositas terak yang lebih tinggi yang melemahkan reduksi Mn. Al2O3 juga meningkatkan viskositas terak dan ini dapat memperlambat reaksi reduksi Mn. Agar terak dapat mengalir dengan baik, konsentrasi Al2O3 dalam terak tidak boleh melebihi 20%.
Selama peleburan Si-Mn, penambahan dolomit atau kalsit ke muatan meningkatkan kebasaan terak, yang meningkatkan fluiditas terak dan memfasilitasi pengurangan MnO dari terak. Kandungan SiO2 khas dalam terak Si-Mn berkisar antara 35% hingga 45%. Terak ini memiliki temperatur liquidus antara 1300 des C dan 1380 deg C, tergantung pada komposisi terak. Peningkatan suhu atau kandungan SiO2 dalam terak dan penurunan rasio (CaO + MgO) /Al2O3 semuanya meningkatkan koefisien partisi logam Si – terak.
Untuk meningkatkan fluiditas terak, kandungan MgO terak harus melebihi 7%. Pengurangan kandungan MnO yang signifikan dari terak dapat dicapai dengan meningkatkan proporsi MgO dalam terak. Hal ini pada gilirannya meningkatkan pemulihan Mn.
Produksi Si-Mn tergantung pada perilaku bijih Mn, terak Fe-Mn, kuarsa, dan fluks selama peleburan, reduksi, dan pembentukan terak. Proses ini dapat dibagi menjadi tiga tahap berikut.
- Pemanasan dan pra-reduksi dalam wujud padat – Pada tahap ini, yang terjadi pada suhu antara 1100 derajat C dan 1200 derajat C, oksida Mn direduksi menjadi MnO, dan oksida besi direduksi menjadi besi logam.
- Pembentukan terak cair dan reduksi Mn oksida – Tahap ini diselesaikan di bagian atas unggun kokas di mana suhunya tidak pasti dan dapat dinilai sebagai berikut. Kesetimbangan kandungan Mn oksida dalam terak pada 1500 derajat C dengan Fe-Mn (sebelum dimulainya reduksi SiO2) dalam kisaran 10% sampai 25% tergantung pada komposisi terak. Sampel terak yang diambil dari atas coke bed selama penggalian tungku mengandung sekitar 10% MnO. Kandungan MnO yang rendah seperti itu dalam terak diharapkan pada suhu yang lebih besar dari 1550 derajat C. Selanjutnya, terak cair diperlukan untuk memiliki viskositas rendah untuk meresap melalui unggun kokas. Oleh karena itu, suhu di bagian atas unggun kokas diperkirakan berkisar antara 1550 derajat C hingga 1600 derajat C.
- Reduksi SiO2 dari slag dan reduksi MnO lebih lanjut – Tahap ini terjadi pada kisaran suhu 1550 derajat C hingga 1650 derajat C. Kandungan SiO2 terak dalam coke bed diperkirakan berada di kisaran 40% sampai 45% yang sama dengan terak akhir. Hal ini menunjukkan bahwa laju pelarutan kuarsa ke dalam terak mendekati laju reduksi SiO2 dari terak dan mempertahankan konsentrasi SiO2 dalam terak relatif konstan. Kandungan MnO dalam terak semakin menurun menjadi sekitar 5% sampai 10%. Terak ini biasanya dibuang.
Komponen utama fase gas di interior tungku adalah CO. Silikon monoksida (SiO) dan uap Mn hanya ada dalam jumlah kecil. Pada suhu rendah di dekat bagian atas tungku, gas juga mengandung CO2 dan uap air.
Reaksi reduksi mengubah komposisi bijih, yang menyebabkan perubahan suhu leleh dan sifat lain dari bijih. Laju perubahan ini bergantung pada laju reduksi, yang dipengaruhi oleh beberapa parameter berbeda seperti suhu, komposisi dan morfologi bijih, sifat material karbon, dan lain-lain.
Jumlah terak per ton Si-Mn terutama ditentukan oleh rasio bijih/terak. Peningkatan porsi terak Fe-Mn dengan mengorbankan bijih Mn menyebabkan rasio terak/logam yang lebih besar dalam proses produksi Si-Mn. Volume terak yang tinggi menyebabkan peningkatan konsumsi energi dan mungkin kehilangan inklusi Mn yang lebih tinggi dalam terak akhir.
Keekonomisan peleburan Si-Mn ditingkatkan dengan meminimalkan hilangnya Mn sebagai inklusi logam, karena MnO terlarut dalam terak, dan dengan produksi paduan tinggi Si dan rendah C.
Si-Mn karbon rendah dengan sekitar 30% Si diproduksi dengan meningkatkan paduan standar dengan penambahan limbah Si dari industri paduan Fe-Si.
Konsumsi daya spesifik untuk produksi paduan Si-Mn standar dari campuran bijih Mn, terak C Fe-Mn C tinggi dan peleburan ulang logam kaya Si, biasanya dapat mencapai 3500 kWh hingga 4500 kWh per ton Si-Mn dan bergantung pada pertama-tama pada jumlah logam yang ditambahkan ke umpan. Konsumsi daya meningkat dengan kandungan Si dari Si-Mn yang dihasilkan, dan juga dengan jumlah terak per ton Si-Mn. Setiap tambahan 100 kg slag yang dihasilkan mengkonsumsi tambahan energi listrik sekitar 50 kWh. Sekitar 100 kWh per ton Si-Mn dan beberapa kokas disimpan jika fraksi bijih dalam muatan dikurangi menjadi MnO oleh gas CO yang naik dari zona reduksi peleburan.