Tinplate dan Proses Tinning
Tinplate dan Proses Tinning
Tinning atau tinplating adalah proses pelapisan lembaran tipis atau strip baja dengan timah (Sn), dan produk yang dihasilkan dikenal sebagai tinplate. Tinplate adalah pengukur cahaya, lembaran atau strip baja karbon rendah yang direduksi dingin, dilapisi pada kedua permukaannya dengan timah murni komersial. Ini menggabungkan kekuatan dan kemampuan bentuk baja dan ketahanan korosi, kemampuan solder dan penampilan timah yang baik. Dalam deskripsi yang luas ini, saat ini terdapat berbagai produk tinplate yang sangat luas, dibuat khusus untuk memenuhi persyaratan penggunaan akhir tertentu.
Pelat timah banyak digunakan untuk membuat berbagai jenis kaleng dengan cara menyolder atau mengelas. Mereka dicirikan oleh kilau logam yang menarik. Pelat timah dengan berbagai jenis kekasaran permukaan diproduksi dengan memilih permukaan akhir dari lembaran baja substrat. Mereka memiliki kemampuan melukis dan kemampuan cetak yang sangat baik. Pencetakan selesai dengan indah menggunakan berbagai pernis dan tinta. Sifat mampu bentuk yang tepat diperoleh untuk berbagai aplikasi serta kekuatan yang diperlukan setelah pembentukan dengan memilih tingkat temper yang tepat. Selain itu, ketahanan korosi yang sesuai diperoleh terhadap isi wadah dengan memilih berat lapisan yang tepat.
Tinplate digunakan untuk membuat semua jenis wadah seperti kaleng makanan, kaleng minuman, dan kaleng artistik. Aplikasinya tidak terbatas pada wadah. Tinplate juga telah digunakan untuk membuat suku cadang mesin listrik dan banyak produk lainnya.
Produksi dasar baja dan pelapisan selanjutnya dengan timah tidak tergantung satu sama lain, sehingga setiap rangkaian sifat dalam baja, secara teori dapat digabungkan dengan pelapis timah apa pun. Komposisi baja yang digunakan untuk pelat timah dikontrol dengan ketat dan sesuai dengan tingkat yang dipilih dan cara pemrosesannya, berbagai jenis dengan sifat mampu bentuk yang berbeda (juga dikenal sebagai temper) dapat diproduksi. Tinplate dijual dalam berbagai ketebalan baja, umumnya berkisar antara 0,15 mm hingga 0,6 mm.
Lembaran baja dapat dilapisi dengan berbagai ketebalan timah. Bahkan ketebalan yang berbeda pada dua permukaan (pelapis diferensial) juga dapat diproduksi untuk memenuhi berbagai kondisi pada permukaan internal dan eksternal wadah. Beberapa permukaan akhir juga diproduksi untuk beragam aplikasi. Tinplate memiliki perlakuan pasivasi khusus untuk menstabilkan permukaan dan meningkatkan daya rekat lak. Ini juga membawa lapisan minyak yang sangat tipis untuk meningkatkan sifat penanganan dan fabrikasinya. Minyak ini tentu saja cocok dengan produk makanan. Berbagai macam bahan yang dihasilkan memberi pengguna fleksibilitas yang besar dalam pilihan dan kemampuan untuk memilih bahan yang tepat secara tepat untuk penggunaan akhir tertentu.
Piring timah dan kemasan bahan makanan
Timah hadir dalam makanan hanya dalam jumlah kecil ion Sn (+2) yang terikat kompleks. Itu terjadi di sebagian besar bahan makanan. Kadar timah harus serendah mungkin karena kemungkinan iritasi lambung. Kadarnya biasanya kurang dari 1 mg/kg (miligram per kilogram) pada bahan makanan yang belum diproses. Konsentrasi yang lebih tinggi ditemukan dalam bahan makanan kaleng karena pelarutan pelat timah untuk membentuk senyawa atau kompleks timah anorganik. Umumnya batas maksimum 250 mg/kg untuk timah dalam makanan padat dalam kaleng dan batas maksimum 200 mg/kg untuk makanan cair dalam kaleng ditentukan. Stannous chloride diizinkan sebagai aditif makanan untuk produk makanan kaleng hingga 25 mg/kg (sebagai timah).
Sumber utama timah saat ini dalam makanan adalah bahan kontak makanan, terutama pelepasan dari kaleng ke bahan makanan asam. Kaleng timah sebenarnya adalah kaleng baja dengan lapisan tipis logam timah (tinplate). Seringkali ada lapisan berbasis resin internal pada pelat timah. Pelat timah terutama digunakan dalam kaleng, ujung kaleng, dan penutup terutama untuk botol kaca dan stoples. Namun, penggunaan kaleng semakin berkurang. Timah juga digunakan untuk melapisi peralatan dapur.
Timah bersifat amfoter, bereaksi dengan asam dan basa kuat, tetapi relatif tidak reaktif terhadap larutan yang hampir netral. Kehadiran oksigen sangat mempercepat reaksi dalam larutan. Pelat timah yang digunakan dalam wadah makanan hanya teroksidasi secara perlahan. Kandungan timah dalam bahan makanan tergantung pada (i) apakah kaleng tersebut dipernis, (ii) adanya zat pengoksidasi atau akselerator korosi, (iii) keasaman produk makanan dalam kaleng, (iv) berapa lama , dan pada suhu berapa kaleng disimpan sebelum dibuka, dan (v) lamanya produk disimpan di dalam kaleng setelah dibuka.
Oksidasi pelat timah diikuti oleh migrasi tak terhindarkan dari ion timah yang terbentuk ke dalam bahan makanan adalah mekanisme fisiokimia, yang dikenal sebagai efek anoda korban, yang melindungi baja di bawahnya agar tidak terkorosi oleh bahan makanan. Pembubaran kaleng melindungi kaleng dari kemungkinan perforasi, dan melindungi isinya dari degradasi (perubahan warna dan rasa) selama sterilisasi dan penyimpanan panas, yang biasanya memiliki umur simpan 2 tahun.
Konsentrasi timah dalam bahan makanan dalam kaleng yang tidak dipernis dapat melebihi 100 mg/kg sedangkan bahan makanan yang disimpan dalam kaleng yang dipernis memiliki kadar timah umumnya di bawah 25 mg/kg. Namun, menyimpan bahan makanan dalam kaleng terbuka tanpa pernis mengakibatkan peningkatan substansial dalam konsentrasi timah dalam bahan makanan. Sayuran kaleng dan buah-buahan dalam kaleng yang tidak dipernis hanya merupakan persentase kecil berat dari total asupan makanan, sementara mereka dapat berkontribusi 85 % dari total asupan timah. Ketebalan lapisan pernis sangat mempengaruhi kinerja kaleng makanan yang dipernis.
Tinplate-korosi dan kegunaannya
Untuk timah yang dicelup panas dan disepuh, lapisan oksida terbentuk pada timah di udara. Film ini cukup stabil dan memberikan penghalang untuk oksidasi lebih lanjut. Pada nilai pH antara 3 dan 10 dan tanpa adanya zat pengompleks, penghalang oksida melindungi logam dari makanan. Namun, di luar kisaran pH ini, korosi timah terjadi.
Beberapa korosi dapat diharapkan dari lapisan timah atau timah yang terpapar di luar ruangan. Dalam paparan dalam ruangan normal, timah bersifat protektif terhadap besi, baja, dan paduannya. Korosi dapat diperkirakan terjadi pada diskontinuitas lapisan (seperti pori-pori) karena pasangan galvanik yang terbentuk antara timah dan baja di bawahnya melalui diskontinuitas, terutama di atmosfer lembab.
Tinning adalah proses yang sangat hemat biaya, karena timah sudah tersedia dan harganya jauh lebih murah. Ini juga menawarkan kemampuan penyolderan yang sangat baik, serta perlindungan superior terhadap korosi.
Tinplating dapat menghasilkan warna abu-abu keputihan yang lebih disukai bila tampilan kusam atau matte diinginkan. Ini juga dapat menghasilkan tampilan metalik yang mengkilap ketika lebih disukai. Timah menawarkan tingkat konduktivitas yang layak, membuat tinning berguna dalam pembuatan berbagai komponen elektronik. Timah juga digunakan untuk kemasan makanan. Karena beberapa keunggulan, timah adalah logam pilihan untuk aplikasi pelapisan di berbagai industri seperti (i) dirgantara, (ii) pengemasan makanan, (iii) elektronik, (iv) telekomunikasi, dan (v) manufaktur perhiasan.
Pembentukan kumis timah dapat terjadi selama proses pengalengan dan dapat berdampak negatif pada hasil akhir. Timah memiliki kecenderungan kuat untuk membentuk kumis. Kumis timah adalah tonjolan kecil dan tajam yang dapat terbentuk di permukaan lembaran timah murni lama setelah proses pelapisan selesai. Kumis memiliki diameter 1 mm hingga 2 mm dan panjangnya bisa mencapai sekitar 3 mm. Kumis dapat menyebabkan kerusakan signifikan pada pelat timah yang sudah jadi. Karena kumis bersifat konduktif secara elektrik, mereka dapat menyebabkan korsleting pada komponen elektronik. Meskipun mekanisme yang tepat dari pertumbuhan kumis belum dipahami secara rinci, kumis timah hanya dapat terjadi pada pelapis timah murni yang dilapisi. Sebagai tindakan pencegahan, timah harus ditambahkan ke timah setidaknya 2%, atau pelapisan timah murni harus dipanaskan di atas suhu leleh timah.
Proses pengerasan
Tinplate pada dasarnya adalah produk baja, karena pada dasarnya adalah strip baja pengukur ringan yang dilapisi dengan timah di kedua permukaannya. Oleh karena itu, produksi pelat timah terbagi menjadi dua tahap utama yaitu (i) produksi strip atau lembaran baja karbon rendah tipis yang memiliki dimensi dan sifat mekanik yang diperlukan, dan (ii) proses pelapisan timah. Di sini hanya proses pelapisan timah yang dijelaskan. Strip atau lembaran baja karbon rendah tipis tempat pelapis timah diterapkan disebut 'pelat hitam'.
Sejumlah besar pelat timah yang relatif kuat sekarang diproduksi dengan teknik reduksi ganda. Pelat timah yang lebih tipis namun lebih kuat dapat diproduksi dengan metode reduksi ganda, yang memungkinkan penggunaan material yang lebih efisien dalam pembuatan kaleng. Setelah pengerolan dingin awal dan anil, alih-alih pengerolan temper, baja diberikan reduksi dingin kedua dengan pelumasan, sekitar 10% hingga 50%. Efek pengerasan kerja memberikan kekuatan tambahan pada baja, sementara strip mempertahankan keuletan yang cukup untuk dibentuk menjadi ujung dan badan kaleng. Ketebalan akhir bisa serendah 0,12 mm, kisaran tipikalnya adalah 0,14 mm hingga 0,24 mm. Rolling mill dua-berdiri atau tiga-berdiri dapat digunakan untuk reduksi ganda. Di beberapa pabrik, digunakan pabrik dengan tujuan ganda yang dapat menghasilkan material dengan reduksi ganda dan beroperasi sebagai pabrik temper (skin pass) konvensional. Baja reduksi ganda menunjukkan sifat arah yang sangat jelas dan arah butir selalu ditunjukkan dan diperhitungkan selama operasi pembentukan dengan pelat timah akhir.
Sebelum memasuki jalur tinning, strip biasanya dipangkas tepi dan diperiksa pada jalur persiapan koil. Pengukur ketebalan strip juga dapat dipasang sehingga pelat hitam off-gauge atau di bawah standar dapat dipotong. Gulungan dengan berat optimal dihasilkan dengan mengelas panjang strip bersama-sama.
Ada dua proses pengasaman pelat hitam yaitu (i) proses hot dip tinning dan (ii) proses electroplating.
Proses tinning hot dip
Proses hot dip tinning adalah proses merendam pelat hitam baja ke dalam bak timah cair murni pada suhu lebih besar dari 232 derajat C. Lapisan yang dihasilkan terdiri dari lapisan intermetalik yang sangat tipis yang pertama kali terbentuk pada antarmuka bahan dasar dan timah (misalnya saat mencelupkan pelat hitam, terbentuk paduan besi/timah) diikuti oleh lapisan timah murni.
Strip baja yang akan dilapisi timah pertama-tama dibuka gulungannya dan kemudian dibersihkan secara menyeluruh dan, opsional, siklus pengawetan. Setelah itu, seluruh permukaannya dibasahi dengan bahan fluks yang cocok untuk aplikasi, biasanya produk komersial standar. Fluks atau 'cairan solder' ini mengaktifkan permukaan strip dalam persiapan proses tinning. Mandi fluxing yang disebut diikuti oleh rendaman timah yang dipanaskan. Biasanya ini adalah panci berpemanas tahan, tetapi untuk keluaran tinggi, penggunaan panci berpemanas induksi juga dapat dipertimbangkan. Di sini timah cair ditahan pada suhu yang ditentukan, dan jumlah energi yang dihilangkan oleh strip yang dilapisi diganti. Sistem pemanas gas juga dapat digunakan tetapi cenderung tidak menguntungkan karena kerumitan pemasangannya.
Kecepatan strip mencapai hingga 200 meter per menit (m/menit). Pemandian timah memiliki suhu sekitar 250 derajat C hingga 290 derajat C (suhu leleh timah sekitar 230 derajat C). Mengingat konduktivitas panas timah yang relatif rendah, manajemen suhu rendaman perlu ditangani dengan hati-hati. Bagian hilir dari bak timah, yang berukuran cukup, inti dari sistem ini adalah desain dan integrasi proses dari unit penyeka dan pengembus karena menentukan ketebalan dan keseragaman lapisan atas lebar dan panjang strip. . Opsional, wiper udara dapat digabungkan dengan pengukur lapisan inline non-destruktif. Ini membentuk lingkaran kontrol tertutup yang memastikan kualitas produk yang seragam. Dari wiper udara, strip yang baru dilapisi memasuki zona pendinginan konveksi tinggi yang tidak bersentuhan dan kemudian melewati pengukur lapisan sebelum ditutup kembali pada recoiler. Rezim operasi khusus jalur tinning dalam mode stop-and-go memberikan pengurangan dramatis pada material penyortiran berlapis timah.
Keuntungan dari proses hot dip tinning adalah (i) tidak ada limbah dari proses produksi, (ii) tidak ada zat berbahaya (seperti cyanogen, timbal, dll) yang digunakan sama sekali dalam proses produksi, (iii) kecepatan pelapisan sangat tinggi ( beberapa kali lebih tinggi dari pelapisan elektrolitik, (iv) pelapisan tebal dan pelapis tipis dapat diproduksi pada kecepatan yang hampir sama, (v) ketebalan lapisan timah diatur oleh sistem pisau udara yang dikendalikan komputer, proses bebas kontak yang memastikan permukaan yang sangat tinggi kualitas, (vi) lapisan timah dan logam dasar terikat kuat karena lapisan antar logam terbentuk selama proses hot dip, (vii) risiko pertumbuhan whisker sangat kecil karena proses hot dip membuat struktur kristal timah menjadi seragam dan meminimalkan bagian dalamnya stres yang meminimalkan risiko pertumbuhan kumis.Keuntungan dari tinning hot dip jika dibandingkan dengan pelapisan timah elektroplating termasuk (i) kurang berpori daripada elektroplating, (ii) lebih ulet daripada elektroplating, (iii) hampir bebas stres, (iv) lebih ekonomis daripada ele ctroplating, dan (v) ketahanan korosi yang lebih baik daripada electroplating. Kelemahan dari hot dip tinning adalah bahwa ketebalan lapisan yang disediakan oleh hot dip tinning tidak terkontrol dengan baik jika dibandingkan dengan yang diberikan dengan metode elektroplating. Hot dip tinning tidak boleh digunakan bila diperlukan toleransi yang ketat.
Pengerasan dengan pelapisan listrik
Dalam elektroplating, item yang akan dilapisi ditempatkan ke dalam bejana yang berisi larutan satu atau lebih garam timah. Item terhubung ke sirkuit listrik, membentuk katoda (negatif) dari sirkuit sementara elektroda biasanya dari logam yang sama untuk disepuh membentuk anoda (positif). Saat arus listrik dilewati melalui sirkuit, ion logam dalam larutan akan tertarik ke benda tersebut. Untuk menghasilkan permukaan yang halus dan mengkilat, lembaran yang dilapisi kemudian dipanaskan sebentar di atas titik leleh timah.
Saat ini, tinplate hampir diproduksi hanya dengan pelapisan timah pada dasar baja dengan proses yang berkesinambungan (Gbr 1). Alasan utama untuk elektro-tinning strip baja menggantikan proses hot dip tinning karena memberikan tingkat kontrol ketebalan yang sangat tinggi, termasuk perbedaan ketebalan lapisan pada kedua sisi lembaran baja. Proses electro-tinning juga memberikan output tinplate yang lebih tinggi dengan kualitas yang unggul dan dengan biaya produksi yang lebih rendah. Selanjutnya, dengan peningkatan teknologi pelapisan dan kimia dasar baja, ketebalan dasar baja dan lapisan timah secara bertahap berkurang secara signifikan. Saat ini ketebalan lapisan tipikal berada dalam kisaran 0,1 hingga 1,5 mikron tergantung pada penggunaan akhir.
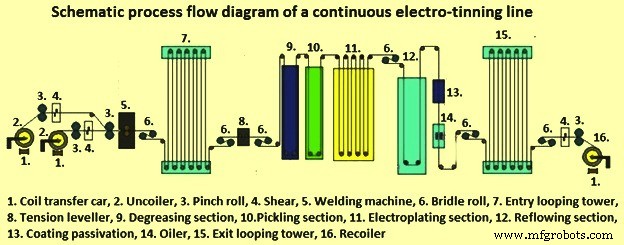
Gbr 1 Diagram alir proses skema dari garis elektro-tinning kontinu
Ada empat pilihan dasar proses electrolytic plating yang dapat digunakan untuk deposit timah. Ini adalah (i) alkali stannat, (ii) asam sulfat, (iii) asam fluoborat, dan (iv) asam sulfonat. Proses stannat didasarkan pada natrium atau kalium stanat. Untuk aplikasi pelapisan berkecepatan tinggi, potasium stannat digunakan karena memiliki kelarutan yang sangat tinggi dibandingkan dengan garam natrium. Untuk mencapai kepadatan arus hingga 1600 ampere per meter persegi (A/sqm), digunakan formulasi yang mengandung 210 gram per liter (g/L) kalium stannat dan 22 g/L kalium hidroksida. Konsentrasi kalium stannat dapat digandakan untuk mencapai kerapatan arus 4000 A/sqm. Efisiensi anoda dalam kisaran 75% hingga 95% dan efisiensi katoda dalam kisaran 80% hingga 90% adalah tipikal untuk proses alkali.
Dari semua proses pelapisan timah, proses alkali memiliki daya lempar yang unggul. Proses ini tidak memerlukan penggunaan bahan tambahan organik tetapi beroperasi pada suhu tinggi (70 derajat C hingga 90 derajat C). Aspek terpenting dari pelapisan timah alkali adalah kebutuhan kritis untuk kontrol anoda yang tepat. Jika anoda timah tidak dikontrol dengan baik selama proses pelapisan, hasil endapan berpori yang kasar. Film kuning-hijau harus ada di anoda selama operasi pelapisan untuk memastikan pelapisan yang sangat baik.
Solusi pelapisan berdasarkan sulfat stannous (7 g/L hingga 50 g/L) dan asam sulfat (50 g/L hingga 150 g/L) dapat menyimpan endapan dekoratif cerah atau lapisan matte tergantung pada jenis penghalus biji-bijian / sistem pencerah yang digunakan. Lapisan timah matte semi-terang dapat diperoleh dengan menggunakan gelatin dan senyawa organik, beta-naftol. Berbagai macam pencerah organik tersedia secara komersial untuk menghasilkan endapan perekat dekoratif yang cerah dari elektrolit sulfat stannous. Aditif ini umumnya didasarkan pada aldehida alifatik dan amina aromatik. Versi perbaikan di atas terdiri dari bahan pembasah seperti polietilena glikol yang larut dalam air dan turunan etilena yang larut dalam air sebagai bahan pencerah utama. Bright bath memiliki beberapa keunggulan dibandingkan proses matte yang meliputi peningkatan ketahanan korosi, pengurangan porositas, ketahanan terhadap sidik jari, peningkatan kemampuan solder serta penampilan kosmetiknya.
Proses asam sulfat beroperasi antara 20 derajat C sampai 30 derajat C pada dasarnya 100% efisiensi anoda dan katoda. Mandi asam tidak memerlukan pemantauan anoda yang hati-hati dari rendaman stannat alkali tetapi membutuhkan agen tambahan organik. Namun, daya lempar penangas asam biasanya lebih kecil jika dibandingkan dengan proses alkalin stannat.
Proses pelapisan asam lainnya berdasarkan timah fluoborat (75 g/L hingga 115 g/L) dan asam fluoborat (50 g/L hingga 150 g/L) dirancang untuk melapisi endapan timah matte murni. Keuntungan utama dari proses ini dibandingkan timah sulfat adalah dapat dioperasikan pada rapat arus katoda yang jauh lebih tinggi, hingga 10.000 A/sqm (dalam larutan pelapis yang diaduk). Gelatin dan beta-naftol biasanya digunakan sebagai penghalus biji-bijian dalam proses ini, yang dioperasikan pada kisaran suhu 20 derajat C hingga 30 derajat C. Efisiensi anoda dan katoda sekitar 100 %.
Baru-baru ini formulasi pelapisan timah berdasarkan asam metana-sulfonat (15% sampai 25% volume) mulai diterima karena larutan tersebut memerlukan pengolahan limbah yang sederhana, tidak mengandung fluorida atau boron, dan kurang korosif dibandingkan elektrolit berdasarkan asam fluoborat. Elektrolit metana-sulfonik, mirip dengan rendaman fluoborat, dapat menahan logam dalam konsentrasi tinggi dalam larutan (hingga 100 g/L timah) yang memungkinkan pelapisan pada kecepatan tinggi. Kelemahan utama dari proses asam metana-sulfonat adalah biaya pembuatan bahan kimianya yang tinggi.
Semua elektrolit pelapis timah asam yang disebutkan di atas menyimpan timah dari keadaan divalen (+2) dibandingkan dengan keadaan +4 untuk larutan alkali stannat. Proses asam dengan demikian menyimpan timah dua kali lebih cepat dari proses stannate dan beroperasi pada efisiensi katoda yang pada dasarnya 100%. Proses asam timah lebih mudah untuk mengontrol dan memelihara daripada larutan stannate. Mereka memiliki keuntungan tambahan untuk beroperasi pada suhu sekitar.
Sambil mempertimbangkan aliran proses di jalur pelapisan elektro kontinu (Gbr 1), kumparan pelat hitam diumpankan ke jalur pelapisan, dimuat ke uncoiler. Dua uncoiler diperlukan untuk operasi berkelanjutan. Ujung ekor kumparan yang sedang diproses dilas ke ujung kepala kumparan berikutnya yang akan diproses, yang mengharuskan kedua kumparan diam selama pengelasan. Untuk menghindari mati selama pengelasan, saluran dilengkapi dengan menara perulangan atau akumulator yang dapat menampung pelat hitam yang tidak digulung dalam jumlah yang bervariasi (seringkali hingga 600 meter). Garis elektro-tinning modern menggabungkan pemangkas samping setelah akumulator untuk memotong strip ke lebar yang benar. Selain itu, banyak garis sekarang menggabungkan perata tegangan atau regangan, yang menerapkan tegangan terkontrol di seluruh strip untuk menghilangkan distorsi.
Pada jalur electro-tinning kontinyu, waktu pembersihan sangat singkat (sekitar 1 detik hingga 2 detik). Oleh karena itu, diperlukan pembersihan yang efektif dari strip plat hitam. Kebutuhan ini dipenuhi dengan penggunaan elektrolisis untuk membantu pelarutan kimiawi dari residu minyak linting dan kontaminan organik lainnya. Arus besar yang dilewatkan selama elektrolisis menghasilkan gas pada permukaan strip. Hal ini menyebabkan pengangkatan kotoran dan residu dari strip. Bahan pembersih umumnya berupa larutan 1% sampai 5% dalam air dari campuran fosfat, bahan pembasah dan pengemulsi dalam basa natrium hidroksida / karbonat. Temperatur umumnya berkisar antara 80 derajat C sampai 90 derajat C dengan rapat arus 1000 A/sqm biasanya memadai.
Setelah dibersihkan, strip dicuci bersih, idealnya dalam air panas (70 derajat C) menggunakan semprotan bertekanan tinggi. Pengawetan menghilangkan lapisan oksida dan karat dan membuat permukaan tergores untuk pengendapan timah yang lebih baik. Selama proses strip biasanya dibuat anodik kemudian katodik dengan kerapatan arus berkisar antara 500 A/sqm dan 3000 A/sqm yang digunakan.
Berbagai jenis elektrolit dapat digunakan di bagian tinplating. Sel pelapis terdiri dari serangkaian tangki vertikal yang dilalui strip dengan cara serpentin. Jumlah plating tank yang digunakan, panjang anoda, dan lebar strip menentukan luas plating yang efektif. Ini, bersama dengan arus pelapisan yang tersedia, menentukan kecepatan saluran maksimum untuk berat lapisan tertentu. Garis tinning saat ini mencapai kecepatan 600 m/menit atau lebih dengan lebar strip tipikal antara 1000 mm dan 1250 mm. Strip baja dipandu melalui tangki dengan gulungan wastafel yang terletak di bagian bawah tangki dan rol konduktor dengan rol penahan tertutup karet di bagian atas. Ini mengumpulkan elektrolit dari strip dan mengembalikannya ke sel pelapis. Gulungan konduktor harus memiliki konduktivitas listrik yang baik dan resistansi kontak yang rendah antara gulungan dan strip basah. Gulungan ini umumnya terbuat dari baja yang dilapisi dengan tembaga dan kemudian kromium.
Setiap tangki plating memiliki empat bus bar anoda dan empat bank anoda, satu untuk setiap muka jalur bawah dan atas strip. Secara tradisional anoda terbuat dari timah murni 99,9% dan lebar 76 mm, tebal 50 mm dan panjang sekitar 1,8 m. Anoda dikonsumsi dalam proses dan diganti ketika ketebalannya berkurang sekitar 70%. Sebuah anoda aus dikeluarkan dari satu ujung bank dan yang baru dimasukkan di ujung lainnya, yang lain dipindahkan untuk memberi ruang. Dalam beberapa tahun terakhir, anoda inert yang terbuat dari titanium dilapisi dengan platinum atau oksida iridium telah menjadi lebih populer. Nippon Steel adalah yang pertama menggunakan anoda inert di jalur electro-tinning. Dalam hal ini ion stannous diproduksi secara off line di pembangkit listrik di mana oksigen bertekanan tinggi digelembungkan melalui larutan elektrolit yang mengandung manik-manik timah murni, melarutkan timah dan membuat elektrolit segar.
Anoda inert diposisikan sejajar dengan strip baja dalam posisi tetap. Tidak perlu sering memperbarui anoda ini. Ini menghasilkan variasi minimal dalam ketebalan lapisan timah di sepanjang lebar strip. Masker tepi yang dapat disesuaikan memastikan lebar anoda yang benar untuk menghindari penumpukan timah di tepi strip. Karena tidak perlu membuang dan mengganti anoda timah, penggunaan anoda inert juga mengurangi kebutuhan tenaga kerja.
Sistem alternatif anoda timah paralel juga telah digunakan. Dalam sistem ini jembatan anoda disejajarkan sejajar dengan strip dan diisi dengan anoda timah konvensional. Bank anoda ditempatkan dekat dengan strip mengurangi tegangan awal yang diperlukan. Saat anoda perlahan larut, tegangan dinaikkan untuk mempertahankan arus yang diberikan. Ketika anoda telah dikurangi dengan ketebalan tertentu seluruh bank diganti. Sistem ini diklaim memberikan kontrol yang sama atas ketebalan timah seperti pada anoda inert.
Pada akhir bagian pelapisan terdapat bagian kontrol tarik-keluar yang pada dasarnya menghilangkan sisa elektrolit dari strip untuk pemulihan selanjutnya. Timah diendapkan sebagai lapisan keputihan yang memiliki sedikit kilau logam. Jika diperlukan, ini adalah aliran yang dilebur dengan pemanasan induksi atau resistansi (atau kombinasi) untuk menghasilkan hasil akhir seperti cermin yang cerah. Dalam pemanasan resistansi, arus bolak-balik yang tinggi dilewatkan melalui strip melalui gulungan konduktor. Dengan pemanasan induksi, strip melewati serangkaian kumparan tembaga yang didinginkan secara internal di mana arus frekuensi tinggi dilewatkan. Arus eddy yang diinduksi dan kerugian histeresis memanaskan strip dan melelehkan lapisan timah. Proses peleburan aliran ini meningkatkan ketahanan korosi produk dengan pembentukan lapisan paduan timah-besi yang inert.
Sebelum aliran peleburan, pelat difluks dengan memperlakukan dengan elektrolit encer atau bahan kimia berpemilik untuk mencegah cacat permukaan yang muncul di pelat. Pelat timah yang meleleh memiliki lapisan tipis oksida timah di permukaannya, yang jika tidak dirawat dapat tumbuh selama penyimpanan. Untuk meningkatkan ketahanan noda dan kemampuan lakrut, pasivasi kimia atau elektrokimia diterapkan pada strip. Bentuk pasivasi yang paling umum melibatkan perlakuan katodik pada suhu antara 50 derajat C dan 85 derajat C dalam larutan dikromat atau asam kromat yang mengandung 20 g/L dikromat (perlakuan lain yang sekarang jarang digunakan adalah penggunaan fosfat atau karbonat). Perawatan ini menyimpan lapisan kompleks kromium dan oksida terhidrasinya, yang menghambat pertumbuhan oksida timah, mencegah penguningan, meningkatkan daya rekat cat dan meminimalkan pewarnaan oleh senyawa belerang. Sebelum meminyaki tinplate harus benar-benar kering. Meminyaki dengan dioktil sebacat atau asetil tributil sitrat dilakukan dalam proses penyemprotan elektrostatik.
Inspeksi kualitas dilakukan dengan inspeksi in-line sebelum recoiling dan meliputi pemeriksaan ketebalan strip, deteksi lubang kecil, dan ketebalan timah.
Ada proses elektro-tinning lain yang memiliki tangki pelapisan horizontal daripada vertikal. Konfigurasi ini bersama dengan kerapatan arus tinggi yang digunakan (6500 A/sqm), memungkinkan saluran berjalan cepat, dengan kecepatan di atas 600 m/mnt menjadi umum. Tangki pelapisan berada di dua dek dengan masing-masing tingkat berisi hingga 18 tangki pelapis (panjang 1,8 m dengan kedalaman 300 mm) dengan tepi anoda kecil yang didukung pada sandaran karbon konduktor, yang dilewati strip. Anoda memanjang sekitar 130 mm di luar tepi strip dan penyangga dimiringkan pada sudut melintasi lebar tangki yang memastikan jarak konstan antara strip dan permukaan anoda untuk anoda dengan ketebalan yang semakin berkurang. Pada pintu masuk dan keluar dari setiap tingkat pelapisan dan di antara sel-sel pelapis individu yang berdekatan, strip melewati antara sepasang gulungan, gulungan konduktor atas disebut gulungan katoda. Timah dilapisi di bagian bawah di dek pertama. Baja kemudian diputar 180 derajat dan memasuki dek kedua di mana sisi lainnya dilapisi.
PH sistem ini (sekitar 3) tinggi untuk sistem asam, tetapi tidak ada asam bebas yang ditambahkan ke bak mandi. Bak tersebut mengandung timah klorida (sekitar 35 g/L sebagai Sn 2+), natrium dan kalium fluorida, natrium klorida dan kalium hidrogen fluorida bersama dengan aditif organik seperti poli-alkilena oksida atau asam naftalena sulfonat. Elektrolit terus bersirkulasi dalam sistem, meluap ke ujung tangki dan disirkulasikan kembali. Di dek bawah, elektrolit disemprotkan ke bagian atas strip untuk membasahinya. Setelah pelapisan strip melewati tangki pembilasan, pemeras gulungan dan pengering udara panas semua terletak di dek ketiga atas. Dalam proses ini, pencairan aliran biasanya dengan pemanasan induksi. Elektrolitnya mengandung timah fluoro-borat (30 g/L sebagai Sn 2+), asam fluoro-borat dan asam borat untuk mencegah hidrolisis ion fluoro-borat. Juga, aditif berpemilik digunakan. Diklaim bahwa jalur ini dapat beroperasi pada rentang kerapatan arus yang lebih luas yang memungkinkan fleksibilitas jalur yang lebih besar. Meskipun jalur pertama yang dibangun adalah horizontal, jalur selanjutnya adalah vertikal, berisi hingga 16 tangki pelapis dan berjalan pada kecepatan jalur 640 m/menit atau lebih tinggi.
Dalam produksi pelat timah, pembuatan dasar baja dan penerapan pelapis timah tidak tergantung satu sama lain sehingga secara teoritis setiap pelapis timah, atau kombinasi pelapis, dapat diterapkan pada dasar baja apa pun. Dengan demikian kisaran bahan yang diklasifikasikan sebagai pelat timah dapat mencapai ribuan, pelat timah memang tersedia dalam kualitas yang lebih banyak daripada hampir semua produk lembaran logam pengukur cahaya lainnya. Dalam prakteknya kisaran ketebalan dasar baja adalah dari 0,13 mm sampai 0,60 mm dan lapisan timah dari 0,5 g/m2 sampai 15,2 g/m2 timah per permukaan. Ada standar internasional dan nasional yang menentukan rentang dan toleransi untuk berbagai karakteristik, dan metode untuk memverifikasinya.