Produksi Pelat Timah dan Baja Bebas Timah
Produksi Pelat Timah dan Baja Bebas Timah
Pelapisan timah adalah proses pelapisan tipis lembaran baja dengan timah (Sn), dan produk yang dihasilkan dikenal sebagai pelat timah. Paling sering digunakan untuk mencegah karat. Lembaran baja di mana lapisan timah dilakukan dikenal sebagai pelat hitam. Ketika kromium (Cr) dan kromium oksida digunakan untuk pelapis sebagai pengganti timah, maka lembaran yang dilapisi dikenal sebagai baja bebas timah.
Baja bebas timah diproduksi dengan menerapkan perlakuan asam kromat elektrolitik di atas lembaran baja. Pada baja bebas timah terkadang film polietilen tereftalat (PET) atau polipropilen dilaminasi untuk menghilangkan proses pengecatan dan pembersihan saat menggunakan baja bebas timah.
Sejarah
Industri tinplate didirikan atas penemuan proses pengawetan makanan yang disterilkan untuk jangka waktu yang lama oleh Nicolas Appert pada tahun 1810. Proses Appert diadaptasi untuk pengawetan makanan dalam wadah tinplate oleh John Hall pada tahun 1812 di London. Pada tahun 1820-an, makanan kaleng dijual secara luas di Inggris dan Prancis, dan pada tahun 1839, makanan kalengan dijual di AS.
Mulai tahun 1880-an, serangkaian inovasi teknis yang terjadi telah mengubah industri tinplate. Ini termasuk penggantian besi tempa dengan pelat baja hitam pada sekitar tahun 1880, pengembangan reduksi dingin berkelanjutan pada tahun 1927 yang menghilangkan pengerolan paket panas, pengenalan pelapisan elektro kontinu dalam skala kecil di Jerman pada tahun 1934 dan pada skala komersial di Jerman. Amerika Serikat pada tahun 1937 yang menggantikan proses hot dip, penemuan reduksi dingin ganda pada tahun 1960, dan penemuan baja bebas timah pada awal tahun 1960-an di Jepang dan Amerika Serikat.
Saat ini ada dua proses pengasaman pelat hitam yaitu (i) proses hot dipping dan (ii) proses elektroplating.
Proses tinning hot dip
Proses pencelupan panas adalah teknik modern pertama dalam pembuatan pelat timah. Ini terdiri dari pencelupan panas lembaran baja tunggal dalam bak timah cair. Proses ini sekarang telah dihentikan di banyak negara dan hanya menyumbang persentase yang sangat kecil dari produksi tinplate dunia.
Pabrik strip panas tidak menghasilkan strip baja yang cocok untuk tinning. Oleh karena itu ukuran strip canai panas dikurangi di pabrik pengerolan dingin sehingga pelat hitam yang cocok untuk pengalengan diproduksi.
Pelat timah yang dibuat dengan proses pelapisan timah celup panas terdiri dari penggulungan pelat hitam dingin, pengawetan asam untuk menghilangkan kerak apa pun, anil untuk menghilangkan pengerasan regangan, dan kemudian melapisinya dengan lapisan tipis timah. Awalnya ini dilakukan dengan memproduksi paket piring individu atau kecil, yang kemudian dikenal sebagai proses pack mill. Pada akhir 1920-an strip mill mulai menggantikan pack mill, karena mereka dapat memproduksi pelat hitam dalam jumlah yang lebih besar dan lebih ekonomis.
Perangkat tinning terdiri dari setidaknya satu panci timah cair, dengan fluks seng klorida (ZnCl2) di atasnya, dan panci gemuk. Fluks mengeringkan pelat dan menyiapkannya agar timah menempel. Jika panci timah kedua digunakan, yang disebut panci pencuci, panci itu berisi timah pada suhu yang lebih rendah. Ini diikuti oleh panci minyak, yang berisi minyak dan mesin tinning. Mesin tinning memiliki dua rol kecil yang dimuat bersama pegas sehingga ketika pelat kaleng dimasukkan, gulungan memeras sisa timah. Pegas pada mesin tinning dapat diatur ke gaya yang berbeda untuk memberikan ketebalan timah yang berbeda. Terakhir, minyak dibersihkan dengan dedak halus dan ditaburi dengan debu.
Proses produksi pelat timah celup panas di atas digunakan selama abad ke-20. Prosesnya semakin rumit seiring berjalannya waktu, karena secara bertahap ditemukan bahwa penyertaan prosedur tambahan diperlukan untuk meningkatkan kualitas.
Proses pelapisan elektrolit
Pelat timah sekarang sebagian besar diproduksi oleh pelapisan timah di atas dasar baja dalam proses yang berkelanjutan.
- Penyalaan elektrolitik terus menerus dikembangkan pada tahun 1930-an dan 1940-an dalam upaya untuk mengurangi jumlah timah yang dibutuhkan per satuan luas, serta untuk memanfaatkan panjang strip (kumparan) yang digulung di pabrik strip panas dan pabrik penggilingan dingin.
- Jalur timah elektrolitik pertama mulai beroperasi di Jerman pada tahun 1934 dan pada skala komersial di Amerika Serikat pada tahun 1937. Kekurangan timah selama Perang Dunia Kedua mendorong peningkatan skala besar pelapisan elektro, yang segera menjadi teknik manufaktur dominan pelat timah .
Beberapa faktor yang memberikan keunggulan proses elektrolisis tinning dibandingkan proses hot dip tinning tercantum di bawah ini.
- Proses kontinu kecepatan tinggi sebagai lawan dari proses lembaran demi lembaran kecepatan rendah dari tinning celup panas.
- Kontrol ketebalan lapisan yang sederhana dan akurat pada rentang yang luas dibandingkan dengan ketebalan lapisan minimum yang relatif tinggi yang dapat diperoleh melalui proses tinning celup panas, yang tidak diperlukan untuk sebagian besar penggunaan akhir.
- Kemungkinan untuk memproduksi pelat timah dengan massa pelapis yang berbeda di setiap sisinya untuk memenuhi kondisi korosi yang berbeda yang ada di dalam dan di luar kaleng pelat timah atau wadah pelat timah.
- Konsistensi fungsional dan visual dari produk yang diperoleh.
Urutan operasi yang terjadi pada jalur pelapisan timah elektrolitik, dengan kecepatan hingga 10 meter per detik adalah sebagai berikut.
- Pengisian koil– Kumparan pelat hitam ditempatkan pada mandrel uncoiling dan dimasukkan ke dalam bagian masuk dari garis tinplating. Ujung kepala kumparan baru kemudian dilas ke ujung ekor kumparan sebelumnya untuk menjalankan fasilitas terus menerus. Looping tower mengakumulasi panjang material yang bervariasi untuk memungkinkan pengelasan dua kumparan tanpa menghentikan operasi di bagian pemrosesan.
- Pemangkasan samping– Strip pelat hitam dipangkas ke samping hingga lebar akhir. Memo secara otomatis dikumpulkan, dilepas, dan didaur ulang di toko peleburan baja.
- Pembersihan dan pengawetan – Strip selanjutnya dibersihkan secara elektrolisis, diasamkan, dan dibilas dengan mengalir melalui serangkaian tangki untuk memastikan bahwa permukaan strip pelat hitam bersih dan sesuai untuk menerima pengendapan elektro timah.
- Elektroplating- Strip melewati tangki yang berisi anoda timah di kedua sisi strip dan dalam elektrolit. Timah larut dari anoda dan diangkut melalui elektrolit untuk disimpan di strip. Jumlah timah yang mengendap pada strip ditentukan oleh jumlah arus listrik yang mengalir antara anoda dan strip. Untuk menghasilkan lapisan diferensial, pengaturan arus yang berbeda digunakan untuk masing-masing bank anoda. Pelat timah yang kusam seperti berlapis terkadang disebut dengan hasil akhir matte.
- Menara peleburan – Di menara peleburan ini proses reflow timah terjadi saat pelat timah berlapis elektrolit melewati menara. Di bagian menara peleburan, suhu strip dinaikkan dengan resistensi atau pemanasan induksi tepat di atas titik leleh timah (231,9 derajat C) dan kemudian strip segera dipadamkan dengan air dingin. Kaleng mulai meleleh dan mengalir kembali secara merata di sepanjang strip. Produk sekarang memiliki tampilan permukaan cerah atau mengkilap yang lebih khas. Jika lapisan timah matte (belum dicairkan) diperlukan, maka menara peleburan dimatikan. Ketika pelat timah berlapis berbeda sedang diproduksi, maka tanda pengenal biasanya ditempatkan di kedua sisi strip sesaat sebelum peleburan.
- Perlakuan kimia – Larutan natrium dikromat selanjutnya diterapkan pada pelat timah berlapis elektrolit untuk membuat film kromium oksida pelindung ringan. Proses pasivasi ini melindungi permukaan pelat timah dari pembentukan oksida timah, yang menurunkan kemampuan lacquerabilitasnya. Dua perlakuan kimia yang umum digunakan untuk pelat timah elektrolitik adalah larutan natrium dikromat (SDCD) dan natrium dikromat katodik (CDC). Dalam kasus SDCD ada resistensi moderat terhadap pembentukan oksida timah dengan stabilitas penyimpanan terbatas dan digunakan di mana permukaan timah yang sangat pasif tidak diperlukan atau merugikan penggunaan akhir. Saus natrium dikromat bertujuan untuk tidak melebihi 1,6 miligram kromium/sq. meter permukaan. Dalam kasus CDC, dengan penambahan arus listrik katodik, permukaan yang sangat pasif terhadap pembentukan oksida timah disediakan. Perlakuan katodik natrium dikromat biasanya memiliki tujuan 5,4 miligram kromium/sq. meter permukaan.
- Meminyaki – Lapisan oli yang sangat tipis kemudian diterapkan secara elektrostatis ke pelat timah yang sudah jadi. Minyak diterapkan untuk meminimalkan goresan permukaan timah dalam perjalanan dan penanganan. Fungsi utama meminyaki tidak mencegah pembentukan karat seperti pada produk yang tidak dilapisi. Minyak yang digunakan pada pelat timah berlapis elektrolit biasanya adalah asetil tributil sitrat (ATBC). Minyak dioleskan secara merata ke kedua sisi.
- Recoiling – Strip pelat timah berlapis elektrolit yang telah selesai akhirnya digulung kembali di ujung keluar jalur pelapisan timah elektrolitik pada mandrel pengambil yang memiliki diameter dalam standar.
- Pemeriksaan kualitas – Seluruh proses dipantau secara otomatis dan manual untuk memastikan pelat timah berlapis sesuai dengan spesifikasi dan memenuhi harapan pelanggan.
Dalam hal baja bebas timah, pelapis kromium dan kromium oksida menawarkan daya rekat pernis yang unggul dan sifat penyimpanan yang baik. Pelapis ini adalah campuran logam kromium dan kromium oksida. Tidak seperti pelat timah dengan banyaknya bobot pelapis, hanya satu produk berlapis krom standar yang biasanya diproduksi. Produksi baja bebas timah mengikuti urutan pemrosesan yang sama seperti selama produksi pelat timah elektrolitik. Garis pelapis secara mekanis serupa. Selama proses pengendapan elektrolitik, kromium dan kromium oksida diendapkan. Lapisan logam kromium pada setiap permukaan yang diaplikasikan adalah sekitar 55,0 miligram/sq. meter luas. Film oksida berkisar antara 7 hingga 22,0 miligram/sq. meter, tetapi umumnya berada di sisi bawah kisaran ini.
Tidak seperti timah, lapisan krom tidak dapat dialiri ulang. Oleh karena itu, jalur pelapis khusus untuk pelapis baja bebas timah tidak memiliki menara leleh seperti yang digunakan pada jalur pelapis timah elektrolitik untuk mengalirkan kembali timah ke keadaan cerah.
Produk juga diminyaki secara elektrostatis sebelum keluar dari jalur pelapisan. Secara historis, minyak butil stearat (BSO) digunakan untuk tujuan ini. Minyak ini telah dikembangkan untuk pelumasannya untuk mencegah goresan. Dalam beberapa kasus, telah diketahui bahwa minyak asetil tributil sitrat (ATBC) seperti yang digunakan pada pelat timah elektrolitik lebih kompatibel dengan beberapa sistem pernis dan cat tertentu. ATBC lebih disukai dalam kasus ini dengan mengorbankan pelumasan BSO yang lebih besar.
Garis pelapisan pelat timah elektrolitik khas ditunjukkan pada Gambar. 1.
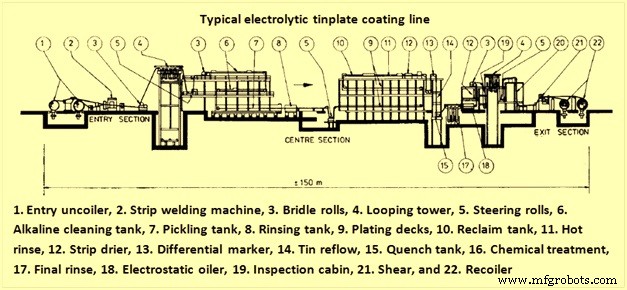
Gbr 1 Garis pelapis pelat timah elektrolitik umum
Pelat timah dan produk baja bebas timah
Pelat timah dan produk baja bebas timah diproduksi dengan karakteristik produk standar tertentu, termasuk terminologi, komposisi, sifat mekanik, permukaan akhir, dan berat pelapis, dll. Pelat timah dan produk bebas timah dijelaskan dalam artikel yang tautannya
http://www.ispatguru.com/tinplate/, dan http://www.ispatguru.com/tin-free-steel/.