Membuat Rencana Pemeliharaan yang Efektif
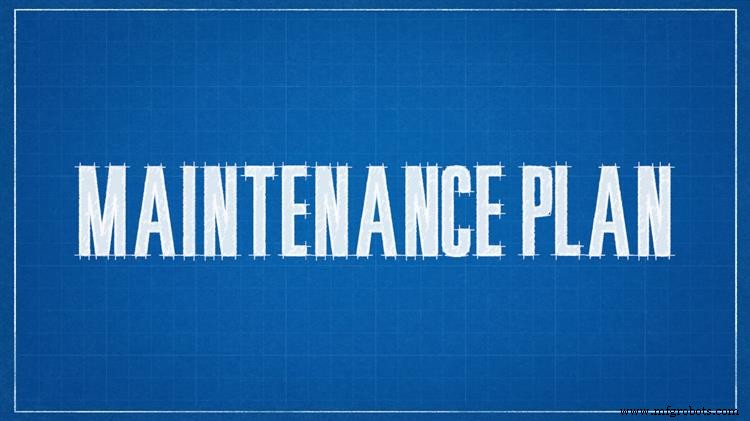
Membuat rencana pemeliharaan umumnya tidak sulit dilakukan. Tetapi membuat program pemeliharaan komprehensif yang efektif menghadirkan beberapa tantangan yang menarik. Akan sulit untuk memahami seluk-beluk apa yang membuat rencana pemeliharaan efektif tanpa memahami bagaimana rencana tersebut merupakan bagian dari lingkungan pemeliharaan total.
Artikel ini menjelaskan perbedaan antara rencana perawatan biasa dan program perawatan yang baik dan efektif.
Mendefinisikan Persyaratan
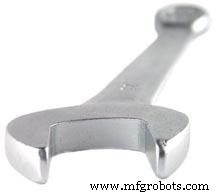
Praktisi pemeliharaan di seluruh industri menggunakan banyak istilah pemeliharaan untuk mengartikan hal yang berbeda. Jadi untuk menyamakan kedudukan, perlu dijelaskan cara penggunaan beberapa istilah ini di seluruh dokumen ini untuk memastikan pemahaman yang sama oleh semua yang membacanya. Harus ditekankan, bagaimanapun, bahwa ini adalah interpretasi pilihan penulis dari istilah-istilah ini, dan tidak harus dianggap sebagai kebenaran Injil.
Dalam bahasa olahraga, kebijakan pemeliharaan mendefinisikan “aturan permainan”, sedangkan strategi pemeliharaan mendefinisikan “rencana permainan” untuk permainan atau musim tersebut.
-
Kebijakan pemeliharaan – Dokumen tingkat tertinggi, biasanya berlaku untuk seluruh situs.
-
Strategi pemeliharaan – Turunkan level berikutnya, biasanya ditinjau dan diperbarui setiap 1 hingga 2 tahun.
-
Program pemeliharaan – Berlaku untuk sistem peralatan atau pusat kerja, menjelaskan paket total semua persyaratan pemeliharaan untuk merawat sistem tersebut.
-
Daftar periksa pemeliharaan – Daftar tugas pemeliharaan (preventif atau prediktif) yang biasanya diturunkan melalui beberapa bentuk analisis, yang dihasilkan secara otomatis sebagai perintah kerja pada frekuensi yang telah ditentukan.
-
Rencana pemeliharaan jangka pendek (terkadang disebut “jadwal kerja”) – Pemilihan daftar periksa dan perintah kerja ad-hoc lainnya yang dikelompokkan bersama untuk diberikan kepada tim bengkel untuk diselesaikan selama periode pemeliharaan yang ditentukan, biasanya mencakup satu minggu atau satu shift.
Loop Informasi Pemeliharaan
Gambar 1 di bawah ini menjelaskan aliran informasi pemeliharaan dan bagaimana berbagai aspek cocok bersama.
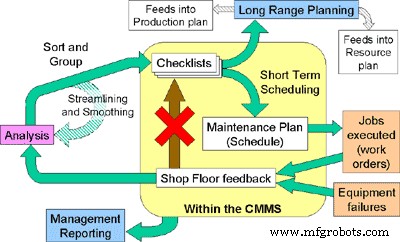
Gambar 1 – Lingkaran Informasi Pemeliharaan
Blok persegi besar menunjukkan langkah-langkah yang terjadi dalam sistem manajemen pemeliharaan terkomputerisasi, atau CMMS.
Ini adalah praktik yang baik untuk melakukan beberapa bentuk analisis untuk mengidentifikasi tugas pemeliharaan yang tepat untuk merawat peralatan Anda. RCM2 mungkin adalah metodologi yang paling terkenal, tetapi ada banyak variasi.
Analisis akan menghasilkan daftar tugas yang perlu disortir dan dikelompokkan ke dalam potongan yang masuk akal, yang masing-masing membentuk isi daftar periksa. Kadang-kadang mungkin perlu untuk melakukan pemulusan dan perampingan kelompok tugas ini secara berulang.
Langkah selanjutnya yang paling jelas adalah menjadwalkan perintah kerja yang dihasilkan oleh sistem ke dalam rencana kerja untuk tim bengkel.
Namun, yang kurang umum adalah menggunakan data daftar periksa ini untuk membuat rencana jangka panjang pekerjaan pemeliharaan yang diperkirakan. Rencana pemeliharaan ini memiliki dua tujuan:
Hasilnya dapat digunakan untuk menentukan kebutuhan tenaga kerja di masa mendatang, dan
Mereka dimasukkan ke dalam rencana produksi.
Jadwal pekerjaan yang direncanakan dikeluarkan ke bengkel dan pekerjaan selesai. Umpan balik dari perintah kerja ini, bersama dengan detail kegagalan peralatan, disimpan dalam CMMS untuk tujuan pelaporan historis.
Tanggapan logis untuk umpan balik lantai toko ini adalah bahwa isi daftar periksa harus disempurnakan untuk meningkatkan kualitas pemeliharaan preventif, terutama untuk mencegah terulangnya kegagalan.
Namun, kesalahan umum adalah melompat langsung dari umpan balik perintah kerja dan segera mengubah kata-kata di daftar periksa. Ketika ini terjadi, integritas program pemeliharaan preventif segera dikompromikan karena kata-kata yang direvisi pada daftar periksa tidak memiliki dasar ilmiah yang dapat dipertahankan. Ini harus dihindari sedapat mungkin.
Pendekatan yang jauh lebih baik untuk menghindari permainan tebak-tebakan ini adalah dengan mengarahkan semua perubahan daftar periksa melalui analisis yang sama seperti yang digunakan pada awalnya untuk membuat daftar periksa awal. Ini berarti bahwa integritas program pemeliharaan dipertahankan dalam jangka panjang. Tersirat dalam pendekatan ini, bagaimanapun, adalah kebutuhan untuk memiliki sistem yang kuat di mana isi analisis dapat ditangkap dan diperbarui dengan mudah.
Akhirnya, semua informasi yang ditangkap ke dalam CMMS harus dimanfaatkan dengan baik jika tidak maka akan membuang-buang waktu. Ini adalah nilai laporan manajemen yang dapat dibuat dari informasi pemeliharaan.
Dalam Analisis RCM
Tanpa menjelaskan proses analisis RCM yang lengkap, pada tahap ini penting untuk menunjukkan beberapa detail yang penting untuk isi analisis semacam itu karena pengaruhnya terhadap rencana pemeliharaan secara keseluruhan.
Tabel 1 – Informasi yang ditangkap dalam analisis gaya RCM
RCM
Tambahan
Identifikasi:
Fungsi
Kegagalan fungsional
Mode kegagalan
Efek kegagalan
Hirarki peralatan hingga ke tingkat komponen
Akar penyebab kegagalan
Alat analisis untuk memilih:
Kategori efek kegagalan
Tugas pemeliharaan preventif/ korektif (sebagaimana sesuai)
Frekuensi tugas
Kerajinan
Durasi tugas
Penanda berjalan/berhenti
Kolom tengah adalah apa yang akan ditemukan dalam analisis gaya RCM pada umumnya.
Selain itu, ada nilai dalam membangun hierarki sistem peralatan yang menunjukkan rakitan, subrakitan, dan komponen individual. Ini membantu untuk melacak bagian mana dari sistem yang sedang dipertimbangkan setiap saat, dan daftar komponen juga membantu mengidentifikasi persyaratan suku cadang untuk sistem.
Yang sangat penting adalah identifikasi yang jelas dari akar penyebab setiap kegagalan, karena ini akan mempengaruhi pemilihan tugas pemeliharaan yang sesuai. Untuk mengilustrasikan hal ini, pertimbangkan misalnya, gearbox yang disita. "Direbut" adalah efeknya. Mungkin ada beberapa akar penyebab mode kegagalan ini yang dapat diatasi dengan cara yang berbeda melalui rencana pemeliharaan. Biasanya tidak ada gunanya mengarahkan pemeliharaan pada efek kegagalan.
Juga penting dari perspektif perencanaan adalah untuk mengidentifikasi waktu yang diperlukan untuk melaksanakan setiap tugas secara mandiri. Jumlah total waktu tugas ini memberikan indikasi yang baik tentang berapa lama total perintah kerja yang dibutuhkan.
Semua hal di atas bergantung pada proses produksi dan konteks operasi situs, jadi komentar ini harus dianggap sebagai pedoman.
Berikut ini adalah beberapa hal yang perlu dipertimbangkan saat membuat program pemeliharaan preventif:
Tugas pemeliharaan preventif harus:
- bertujuan pada proses kegagalan
- spesifik
- sertakan spesifikasi atau toleransi
Jika memungkinkan, lakukan tugas prediktif, bukan preventif
- mengukur atau memeriksa kondisi terhadap standar
- laporkan hasilnya
- buat tugas lanjutan untuk diperbaiki atau diganti di kesempatan berikutnya
“Periksa dan ganti, jika perlu” tugas menghancurkan waktu yang direncanakan
Frekuensi dan perkiraan waktu untuk setiap tugas harus akurat dan bermakna
Cobalah sedapat mungkin untuk hanya merencanakan waktu shutdown untuk tugas-tugas "tidak berjalan". Tetap "berjalan" tugas yang harus dilakukan selama periode produksi normal. Susun program pemeliharaan untuk memungkinkan hal ini.
Penyortiran dan Pengelompokan Daftar Periksa Rencana Pemeliharaan
Setelah menganalisis semua persyaratan pemeliharaan untuk sistem peralatan, tugas individu ini akan dikelompokkan bersama untuk membuat daftar periksa, berdasarkan kriteria umum untuk:
- Kerajinan
- Frekuensi
- Tugas keselamatan / non-keselamatan
- Pemeriksaan berjalan / tidak berjalan dan masuk akal
- Pengaturan waktu, dll. …
Menghaluskan Beban Kerja PM
Untuk memperlancar beban kerja PM, pendekatan yang kuat adalah dengan mendasarkan penyebaran aktivitas PM pada daftar periksa yang muncul dari analisis gaya RCM. Ini mengasumsikan bahwa analisis telah dilakukan secara menyeluruh dan dalam format yang dapat diubah dengan mudah.
Grafik pada Gambar 2 di bawah ini mengilustrasikan bagaimana mungkin untuk mengatur terjadinya perintah kerja PM sedemikian rupa untuk menciptakan aliran pekerjaan pemeliharaan preventif reguler yang semulus mungkin, sambil tetap menyisakan cukup waktu untuk melakukan "tindak lanjut" tersebut. tugas pemeliharaan korektif yang diidentifikasi dari melakukan pemeriksaan preventif/prediktif selama penghentian pemeliharaan terakhir.
Penting untuk diperhatikan bahwa hanya karena dua daftar periksa mungkin memiliki frekuensi yang sama, tidak perlu menjadwalkannya untuk dilakukan pada waktu yang sama. Terkadang, tentu saja, masuk akal untuk menjadwalkan PM pada hari yang sama, tetapi jangan berasumsi bahwa ini selalu benar. Sebagai aturan umum, dalam lingkungan produksi proses otomatis atau berkelanjutan, jumlah total pekerjaan pada satu daftar periksa atau pekerjaan yang direncanakan untuk satu periode pemeliharaan tidak boleh melebihi 80 persen dari total waktu yang tersedia.
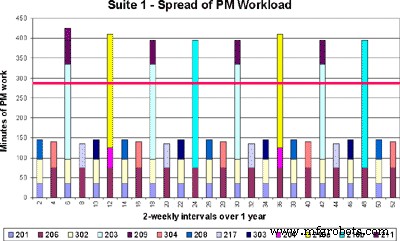
Gambar 2 – Menghaluskan beban kerja PM
Untuk mencapai pola beban kerja yang dihaluskan ini, mungkin perlu untuk kembali ke pengaturan waktu, frekuensi, pengelompokan, tanggal mulai, dll., yang ditentukan dalam analisis asli dan pengerjaan ulang beberapa data. Ini adalah pendekatan berulang yang disebutkan sebelumnya dalam deskripsi Gambar 1.
Penjadwalan Jangka Pendek Pekerjaan Pemeliharaan yang Direncanakan
Diakui dengan baik di kalangan pemeliharaan modern bahwa ada nilai besar dalam merencanakan beban kerja pemeliharaan pada tingkat makro dalam jangka panjang serta pada tingkat terperinci dalam jangka pendek. Kedua aktivitas ini memiliki tujuan yang sangat berbeda.
Perintah kerja reguler dibuat secara otomatis di Maximo setiap malam dari templat perintah kerja di tabel PM Master. Perintah kerja baru ini biasanya dibuat 30 hari sebelum tanggal Mulai Target yang ditentukan pada PM. Perintah kerja lainnya juga dibuat secara manual oleh pengguna sistem, seperti pengrajin dan insinyur.
Semua perintah kerja ini perlu diprioritaskan sesuai dengan kepentingan dan urgensi tugas, dan mereka perlu direncanakan ke dalam beban kerja mingguan kru pemeliharaan untuk memastikan bahwa pemilihan pekerjaan yang seimbang ditugaskan ke setiap kru tanpa mereka menjadi kelebihan beban.
Contoh layout jadwal kerja pemeliharaan mingguan ditunjukkan pada Gambar 3 di bawah ini.
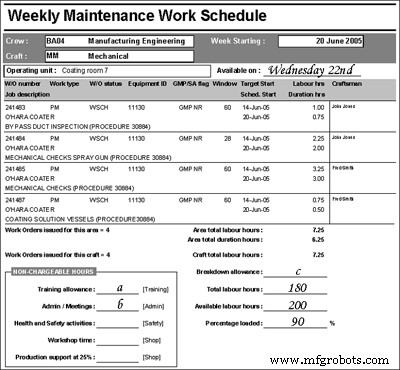
Gambar 3 – Contoh jadwal kerja pemeliharaan mingguan
Paling sering, CMMS hanya akan menghasilkan data laporan dalam format teks atau numerik. Karena insinyur suka melihat sesuatu dalam representasi grafis atau gambar, bagaimanapun, mungkin perlu untuk menggabungkan penggunaan CMMS dengan paket lain yang memiliki kemampuan grafis, seperti spreadsheet. Deskripsi berikut bergantung pada kemampuan CMMS untuk menghasilkan “flat file” dari laporan, yang kemudian dapat diimpor ke dalam spreadsheet dan dimanipulasi lebih lanjut.
Jika memungkinkan, akan lebih baik untuk menyimpan semua data mentah dalam CMMS dan hanya menghasilkan semua grafik dan laporan dari lingkungan itu. Namun, ada dua kendala dalam pendekatan ini:
Sangat sedikit paket CMMS yang memiliki kemampuan grafis;
Sangat sedikit paket CMMS yang akan menangkap atau menyediakan spektrum penuh data yang mungkin diperlukan untuk menyusun pilihan grafik yang diinginkan.
Oleh karena itu, solusi alternatifnya adalah menyalin pilihan data yang diperlukan dari CMMS ke lingkungan spreadsheet yang dapat dimanipulasi lebih lanjut.
Perencanaan Pemeliharaan Jangka Panjang
Beberapa situs menikmati kemewahan memiliki jendela pemeliharaan tetap dan teratur yang dibangun ke dalam rencana produksi. Misalnya, dapat disepakati bahwa setiap Selasa pagi Unit Produksi 1 akan menghentikan produksi dan peralatan akan tersedia untuk kru pemeliharaan selama enam jam. Selama periode enam jam ini, kru pemeliharaan memiliki kesempatan untuk menugaskan sebanyak mungkin orang yang diperlukan untuk menyelesaikan semua kegiatan pemeliharaan yang direncanakan di pusat kerja tersebut. Setelah itu, sistem diserahkan kembali ke tim produksi hingga minggu depan.
Namun dalam banyak kasus, tidak ada rutinitas rutin seperti itu. Peluang bagi tim pemeliharaan untuk melakukan pemeliharaan terencana perlu dinegosiasikan dan disepakati dengan tim produksi atas dasar “sesuai kebutuhan”. Sayangnya, ini sangat sering direduksi menjadi departemen pemeliharaan yang meminta akses ke peralatan. Lebih jauh lagi, permohonan ini sering ditanggapi dengan tanggapan yang tidak simpatik dari tim produksi bahwa mereka harus menjalankan peralatan untuk memenuhi target mereka dan oleh karena itu mereka tidak mampu melepaskannya untuk pemeliharaan. Ini adalah pandangan yang sangat picik menurut saya.
Pembuatan rencana pemeliharaan jangka panjang yang menunjukkan jumlah jam pekerjaan pemeliharaan preventif yang harus dilakukan di setiap pusat kerja selama rentang waktu 18 hingga 24 bulan adalah alat yang berharga. Ini memberi penjadwal produksi visibilitas jumlah waktu yang diperlukan untuk pemeliharaan preventif ini sehingga mereka dapat secara proaktif merencanakan untuk melepaskan peralatan untuk periode tersebut. Hal ini membuat pekerjaan perencanaan kegiatan pemeliharaan menjadi lebih sederhana.
Sifat lingkungan produksi di lokasi penulis membuat sulit untuk menerapkan pola jendela pemeliharaan yang teratur dan tetap seperti yang dijelaskan di atas. Untuk alasan ini, rencana pemeliharaan jangka panjang dibuat untuk memberi tim produksi peringatan awal sebanyak mungkin tentang persyaratan pemeliharaan yang diantisipasi. Rencana ini menunjukkan perkiraan jam pemeliharaan untuk setiap unit operasi, menurut jenis kapal, dalam potongan mingguan selama rentang waktu 24 bulan.
Tabel 2 di bawah ini mengilustrasikan seperti apa struktur rencana pemeliharaan jangka panjang. File datar dibuat dari tabel data master di Maximo yang berisi rincian semua tugas pemeliharaan dan daftar periksa dengan detail peralatan yang sesuai, durasi, frekuensi, kerajinan, tanggal jatuh tempo berikutnya, dll. Informasi ini diimpor ke dalam spreadsheet, yang menggunakan serangkaian filter dan formula untuk menghasilkan rencana jangka panjang.
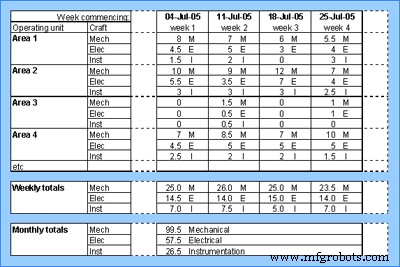
Tabel 2 – Contoh tata letak rencana pemeliharaan jangka panjang
Berdasarkan laporan ini, perencana produksi membuat tunjangan yang diperlukan dalam kalender produksi sehingga peralatan akan tersedia untuk pemeliharaan. Tunjangan ini awalnya dibuat di tingkat makro. Tanggal dan waktu yang tepat untuk pemeliharaan akan disepakati dalam satu atau dua minggu sebelum jatuh tempo.
Susunan angka ini juga dapat digunakan untuk membantu kelancaran beban kerja selama berminggu-minggu dengan menyesuaikan tanggal jatuh tempo tugas pemeliharaan di CMMS seperti yang dijelaskan sebelumnya.
Rencana Tenaga Kerja Jangka Panjang
Penjelasan di atas menjelaskan bagaimana mengidentifikasi perkiraan jumlah jam pemeliharaan di area produksi. Bagian berikut ini mencakup pendekatan untuk memverifikasi bahwa ada cukup tenaga kerja yang tersedia untuk melaksanakan semua pekerjaan.
Untuk memastikan bahwa setiap tim di lokasi memiliki sumber daya pengrajin yang memadai yang tersedia untuk mencakup semua pekerjaan yang akan muncul di area mereka, perkiraan beban kerja vs. tenaga kerja jangka panjang dapat dibuat. Ini sama dengan grafik yang membandingkan jam kerja yang harus dilakukan setiap bulan dengan jam kerja yang tersedia. Grafik dibuat untuk setiap kelompok kerajinan dalam setiap tim lokakarya, yang mencakup cakrawala 18 hingga 24 bulan ke depan.
Jika prediksi jangka panjang menunjukkan bahwa tingkat aktivitas pemeliharaan akan meningkat melampaui tingkat yang dapat dicapai dengan sumber daya yang ada, peringatan dini ini akan memastikan bahwa akan ada cukup waktu untuk merekrut dan melatih sumber daya tambahan sebelum situasinya hilang. lepas kendali. Demikian pula, penurunan tingkat aktivitas pemeliharaan yang diprediksi akan memberikan visibilitas awal yang memadai tentang peluang untuk menugaskan kembali sumber daya pengrajin ke tim atau aktivitas lain. Pendekatan proaktif ini akan meningkatkan pemanfaatan tenaga kerja dan mengurangi kepanikan.
Di bawah ini adalah beberapa kategori data yang digunakan untuk membuat grafik:
Beban kerja (yaitu segala sesuatu yang akan menyita waktu pengrajin)
- jam pemeliharaan preventif dari CMMS
- tunjangan perincian
- pekerjaan korektif / tindak lanjut / tugas berbasis hasil
- pekerjaan proyek (jam ad-hoc untuk setiap aktivitas proyek yang akan datang secara mandiri)
- tunjangan rapat/pelatihan, dll.
Tenaga Kerja (yaitu tersedia jam kerja bersih)
- jam kerja kotor yang tersedia di kru
- tunjangan cuti dan sakit
- tunjangan tambahan untuk lembur
Jumlah jam beban kerja untuk setiap bulan menarik garis beban kerja. Jumlah jam tenaga kerja menarik garis kapasitas tenaga kerja. Jika beban kerja melebihi kapasitas tenaga kerja, beban harus dihaluskan, atau sumber daya tambahan mungkin diperlukan.
Jam pemeliharaan preventif dari CMMS diperoleh dari total dari rencana pemeliharaan jangka panjang yang dijelaskan pada bagian sebelumnya. Tunjangan untuk kerusakan, pekerjaan korektif, dll., dihitung sebagai rata-rata 12 bulan bergulir dari data aktual yang ditunjukkan dari CMMS. Data untuk tunjangan lainnya dapat bersumber dari tempat lain jika tidak tercantum dalam CMMS.
Tenaga kerja pada dasarnya adalah jumlah jam kerja efektif yang tersedia untuk setiap kapal di kru.
Beberapa contoh grafik ditunjukkan pada Gambar 4 di bawah ini.
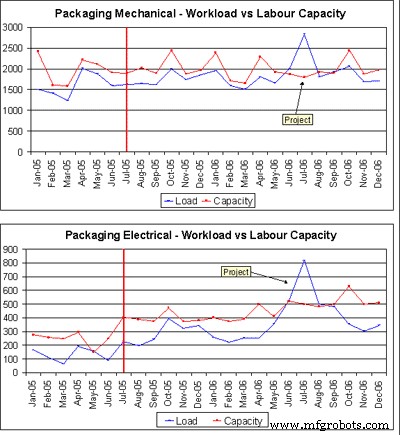
Gambar 4 – Contoh grafik beban kerja vs. kapasitas tenaga kerja
Di mana tenaga kerja melebihi beban kerja, semuanya terkendali. Jika beban kerja melebihi tenaga kerja, beberapa kegiatan yang tidak penting pada saat itu perlu dikurangi, atau meningkatkan ketersediaan orang.
Masukan dan Pelaporan
Umpan balik informasi kembali dari lantai toko, baik melalui tanggapan perintah kerja yang direncanakan, atau dari kegagalan peralatan akan ditangkap di CMMS. Informasi ini dapat diringkas pada laporan seperti yang ditunjukkan pada Gambar 5 di bawah ini. Penerima utama dari laporan ini adalah teknisi keandalan yang menjaga setiap sistem peralatan.
Idealnya, insinyur harus melihat setiap perintah kerja yang diajukan di wilayahnya, tetapi ini tidak selalu layak, jadi laporan ringkasan seperti ini berguna. Insinyur keandalan kemudian harus memutuskan tindakan yang tepat dalam menanggapi setiap kegagalan atau pengamatan.
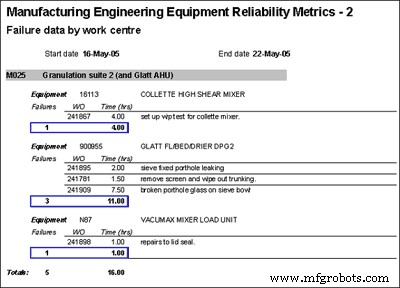
Gambar 5 – Contoh laporan kegagalan mingguan
Algoritme yang ditunjukkan pada Gambar 6 di bawah ini menjelaskan proses pemikiran yang harus dipikirkan oleh para profesional keandalan setiap kali mereka meninjau perintah kerja yang gagal seperti yang ditunjukkan pada ringkasan laporan pada Gambar 5 di atas.
Namun harus diingat bahwa setiap kali opsi “Amende Checklists” dipilih, amandemen ini harus diarahkan melalui analisis RCM asli untuk memastikan integritas program pemeliharaan tidak dilanggar. Mengubah daftar periksa tanpa menjalankan metode dan struktur analisis asli adalah suatu kesalahan. Terlepas dari pendekatan yang telah digunakan untuk merekam analisis asli, dalam jangka panjang perlu memaksa para insinyur keandalan untuk mengarahkan setiap amandemen melalui analisis dan mencatat hasilnya untuk referensi di masa mendatang.
Jika spreadsheet telah diidentifikasi sebagai opsi yang paling tepat, maka spreadsheet harus disusun dengan cara yang kuat dan ramah pengguna. Jika kikuk untuk memperbarui, itu akan rusak, dan integritas program hilang. Sistem database adalah pilihan yang jauh lebih baik untuk tujuan ini, jika tersedia yang cocok.
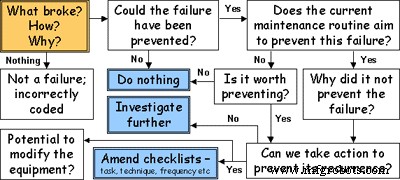
Gambar 6 – Algoritma “Apa yang rusak”
Hasil
Tujuan dari tindakan pemeliharaan harus untuk memantau kesehatan organisasi pemeliharaan. Di mana semuanya terkendali, metrik akan mencerminkan keberhasilan yang telah dicapai. Sebaliknya, mereka juga harus digunakan untuk menyoroti area masalah dan ketidakberesan untuk mendorong perilaku yang diinginkan atau area untuk perbaikan.
Grafik pada Gambar 7 di bawah ini mengilustrasikan beberapa manfaat yang telah direalisasikan di situs penulis sebagai hasil dari memiliki organisasi pemeliharaan yang berfungsi dengan baik. Grafik ini hanya merupakan bagian dari metrik pelaporan reguler yang digunakan untuk mengelola aktivitas pemeliharaan.
Grafik pertama menunjukkan kesesuaian dengan jadwal pemeliharaan mingguan yang direncanakan. Target ditetapkan pada 95 persen dan secara konsisten melebihi semua tim teknik.
Grafik 2 dan 3 menunjukkan bagaimana jumlah kegagalan telah menurun dari bulan ke bulan di satu pusat kerja tertentu selama 12 bulan terakhir, dan dengan demikian, waktu rata-rata antara kegagalan telah meningkat selama periode yang sama.
2 grafik terakhir menunjukkan ketersediaan alat berat di dua pusat kerja utama tempat analisis ulang penuh atas semua persyaratan perawatan baru-baru ini dilakukan menggunakan pendekatan RCM2 yang disesuaikan. Jelas untuk melihat bagaimana, dalam kedua kasus, ketersediaan peralatan jauh di luar kendali dan sejak aktivitas peningkatan dimulai, ketersediaan stabil dan sekarang masih melacak secara konsisten di atas 90 persen. Ini adalah hasil dari beberapa hal:pertama adalah meningkatkan kualitas rutinitas pemeliharaan preventif, dan yang lainnya adalah perencanaan pemeliharaan yang baik
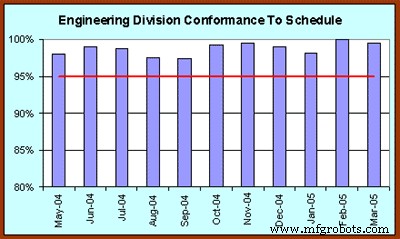
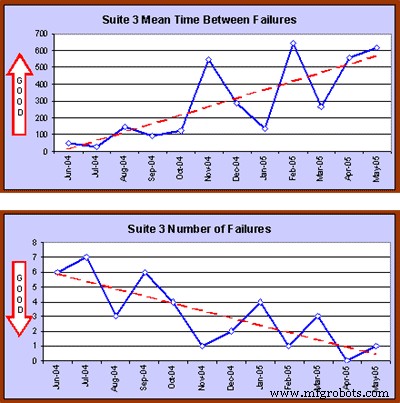
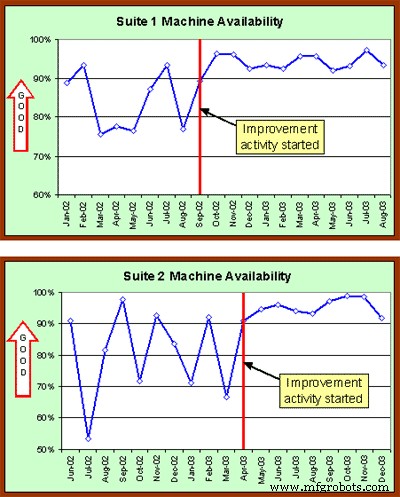
Gambar 7 – Contoh grafik yang menunjukkan manfaat program pemeliharaan yang efektif