Pelajaran utama untuk manajemen senior
Apa tantangan terbesar Anda terkait dengan perawatan berbasis kondisi? Itulah pertanyaan sederhana yang kami ajukan di Allied Reliability kepada ribuan profesional perawatan dan keandalan. Tanggapan No. 1 yang kami terima adalah ini:meyakinkan manajemen senior mengapa pemeliharaan berbasis kondisi itu penting.
Seperti yang baru-baru ini dijelaskan oleh salah satu manajer pemeliharaan:"Kami memiliki program pemantauan kondisi yang sangat kuat di sini selama sekitar 15 tahun. Kami sangat berhasil mencegah kerugian produksi dengan menemukan dan menyelesaikan masalah peralatan sebelum peralatan gagal. Sayangnya, perusahaan telah melalui serangkaian perubahan manajemen dan reorganisasi menjadi 'lebih kompetitif.' Manajer baru belum memahami pentingnya fungsi 'baru' yang mereka peroleh, sehingga upaya pemantauan kondisi sekarang agak sulit. Kebanyakan manajer bertanya-tanya mengapa mereka harus melakukan semua itu karena peralatan tampaknya berfungsi baik-baik saja. Mereka bertanya, 'mengapa kita mendedikasikan sumber daya untuk ini?'"
Apakah ini pola pikir manajemen Anda? Jika demikian halnya, maka 7 Agustus 2006 harus menjadi peringatan bagi mereka. Saat itulah raksasa minyak BP mengakui bahwa lubang kecil seperempat inci adalah bagian dari masalah korosi luas yang mempengaruhi 16 mil dari pipa 22 mil dari Prudhoe Bay di Alaska. Akibatnya, BP terpaksa menutup produksi hingga 400.000 barel per hari dari ladang minyak terbesar di Amerika Serikat itu.
Dengan biaya penutupan dan perbaikan yang mencapai ratusan juta dolar, dampak keuangannya sangat mengejutkan. Namun pertempuran BP dengan korosi di Alaska adalah cerminan dari masalah yang jauh lebih besar yang mengganggu banyak pabrik:Aset yang menua dan pemeliharaan yang buruk selama bertahun-tahun sekarang memakan korban finansial mereka.
Berikut ini adalah dua pelajaran utama yang harus dipelajari oleh setiap manajer senior dari insiden BP.
WAKTU ADALAH UANG
Terlepas dari apa yang mungkin Anda dengar, proses perawatan dasar sangat sederhana:
Sekarang, rahasia sebenarnya untuk perawatan yang efektif adalah langkah pertama - deteksi. Mengapa? Itu karena ada korelasi langsung antara waktu deteksi dan biaya perawatan. Sederhananya, semakin dini Anda dapat mendeteksi masalah, semakin cepat, murah, dan mudah untuk melakukan perbaikan. Sebuah grafik di halaman berikutnya menggambarkan hal itu.
Anda telah melihat kerusakan di BP. Biaya perbaikan darurat bisa sangat besar. Ada perbedaan besar antara pemeliharaan darurat dan pemeliharaan proaktif terencana.
Pelajaran No. 1: Dalam pemeliharaan, waktu adalah uang. Deteksi terlambat berarti koreksi yang mahal.
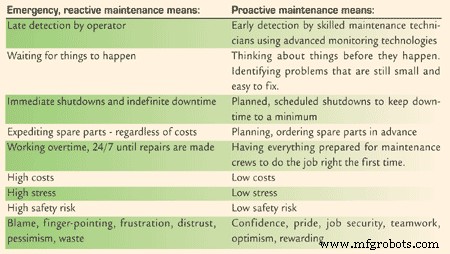
KEBENARAN TENTANG KERUSAKAN
Lubang seperempat inci di pipa BP tidak terjadi begitu saja dalam semalam. Seperti kebanyakan kegagalan, itu berkembang selama beberapa minggu, bulan atau tahun.
Faktanya adalah, masalah peralatan dimulai dari yang kecil dan semakin memburuk seiring waktu, memberikan sinyal peringatan di sepanjang jalan. Sinyal ini bisa berupa sedikit perubahan dalam dimensi fisik - seperti ketebalan pipa di BP. Atau, itu bisa berupa perubahan kecil pada suhu, getaran, atau suara.
Tidak semua perubahan tersebut dapat dideteksi oleh indera manusia. Tapi, mereka dapat diambil dengan peralatan khusus yang dirancang untuk tujuan itu. Itulah bidang pemantauan kondisi dan pemeliharaan prediktif. Dengan teknologi canggih seperti analisis getaran, termografi inframerah, dan ultrasound, teknisi terlatih dapat secara rutin memantau peralatan dan mendeteksi sinyal peringatan dini ini.
Perbedaan antara waktu spesialis pemeliharaan prediktif mendeteksi masalah dan saat operator mengetahuinya sangat besar. Ingat, waktu deteksi sama dengan uang. . . uang besar.
Kenyataannya adalah, sebagian besar pabrikan tidak melakukan perawatan yang cukup prediktif dan berbasis kondisi. Meskipun pemeliharaan prediktif telah ada selama lebih dari 40 tahun, itu masih baru bagi beberapa organisasi. Itu mengarah pada deteksi terlambat, pemeliharaan reaktif, dan semua biaya menyakitkan yang menyertai hasil tersebut.
Pelajaran No. 2: Pemantauan kondisi dan pemeliharaan prediktif harus menjadi bagian utama dari strategi keandalan Anda dan menyumbang setidaknya 50 persen dari pekerjaan pemeliharaan Anda.
(Klik Gambar untuk Memperbesar)
Grafik 1. Pemeliharaan prediktif menemukan masalah lebih awal, membantu Anda menghindari kerusakan.
John Schultz adalah Profesional Pemeliharaan dan Keandalan Bersertifikat melalui Society for Maintenance &Reliability Professionals dan merupakan mitra dengan Allied Reliability. Sebagai perusahaan konsultan, teknik, dan layanan terbesar yang berfokus pada pemeliharaan prediktif dan preventif, Allied melayani lebih dari 200 pabrik dan fasilitas. Untuk wawasan John lebih lanjut, berlangganan kursus elektronik gratis baru "Cara Menghindari Tujuh Kesalahan Terbesar dalam Pemeliharaan Prediktif" di www.alliedreliability.com. Anda juga dapat menghubungi 812-841-9252 atau mengirim email ke [email protected]