Tungku Busur Terendam
Tungku Busur Terendam
industri pemanfaatan energi listrik dimulai dengan pengembangan mesin dinamo oleh Werner von Siemens. Tungku busur listrik telah digunakan selama bertahun-tahun baik untuk peleburan besi tua (tungku busur terbuka) dan untuk proses reduksi (tungku busur terendam). Dalam kasus tungku busur terendam (SAF), bijih dan zat pereduksi diumpankan ke tungku terus menerus dari atas sehingga elektroda terkubur dalam campuran dan busur terendam. Tungku ini dinamai tungku busur terendam karena busurnya terendam. Susunan fisik yang paling umum terdiri dari mandi melingkar dengan tiga elektroda vertikal diatur dalam segitiga. Enam tungku elektroda dengan bak melingkar atau persegi panjang juga digunakan tetapi lebih jarang digunakan.
Tungku busur terendam telah menemukan aplikasinya di lebih dari 20 area industri utama yang berbeda seperti paduan ferro, industri kimia, timah, seng, tembaga, tahan api, titanium oksida, daur ulang, fosfor, dll. Diagram skema khas dari tungku busur terendam untuk ferro produksi krom bersama dengan keseimbangan material diberikan di Gbr.1
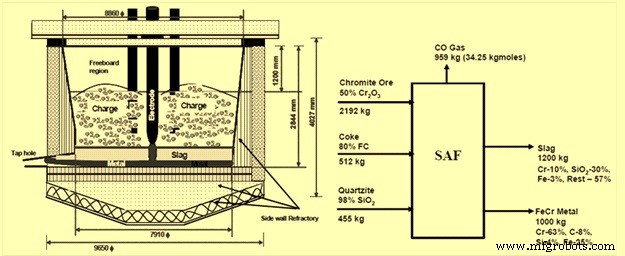
Gbr 1 Diagram skematik tipikal dari tungku busur terendam untuk produksi ferro chrome bersama dengan keseimbangan material.
Sejarah
Meningkatnya permintaan paduan besi dan agen deoksidasi dalam pembuatan baja pada awal abad kedua puluh menyebabkan pengembangan tungku busur terendam pertama. Pembangunan SAF pertama dimulai pada tahun 1905. Unit 1,5 MVA ini dipasang di Horst Ruhr, Essen, Jerman untuk produksi kalsium karbida. Itu berhasil ditugaskan pada tahun 1906 dan didasarkan pada teknologi DC (arus searah).
Sejak itu sejumlah besar SAF (baik dengan tungku berbasis DC dan AC) telah ditugaskan dengan beragam aplikasi. Saat ini, sebagian besar tungku busur terendam didasarkan pada konsep berbasis AC (arus bolak-balik).
Prinsip dan karakteristik SAF
Prinsip SAF konvensional adalah pemanasan hambatan listrik. Energi listrik diubah menjadi energi panas dan reduksi dengan menggunakan hambatan (R) dari beban atau terak cair, kadang-kadang, diperkuat oleh hambatan listrik busur antara terak dan elektroda. Energi ditransmisikan ke tungku perapian oleh elektroda karbon. Kekuatan tungku adalah produk dari resistansi perapian dan kuadrat arus elektroda. Oleh karena itu, peningkatan arus elektroda yang terbatas dapat mengakibatkan peningkatan beban yang relatif besar.
Karakteristik proses di SAF adalah elektroda menembus bahan mentah ke bawah di perapian di atas kolam logam. Biasanya terak menembus ke dalam tempat tidur kokas ini, tetapi tidak sejauh bersentuhan dengan ujung elektroda. Panas listrik untuk peleburan dikembangkan di sekitar ujung elektroda di mana sebagian besar penurunan tegangan terkonsentrasi. Tempat tidur kokas yang dipanaskan memiliki konduktivitas listrik dan termal yang sangat tinggi dibandingkan dengan muatan dingin. Akibatnya hanya sebagian kecil dari arus yang keluar dari sisi elektroda. Tempat tidur kokas juga melakukan panas ke zona peleburan jauh dari elektroda. Gas reaksi dari zona peleburan, terutama gas CO (karbon mono oksida), mengalir ke atas melalui bahan mentah yang turun, sebagian memanaskannya terlebih dahulu, menghasilkan panas sensibel, dan sebagian lagi menyebabkan reduksi keadaan padat dari oksida besi yang lebih tinggi.
Namun, ketebalan zona di mana bahan dipanaskan hingga suhu reaksi sangat kecil sehingga gas tidak memiliki waktu retensi yang cukup untuk menghasilkan reduksi yang ekstensif. 10% hingga 20% pra-pengurangan normal dalam operasi pengisian daya dingin.
Persamaan dasar untuk masukan daya ke tungku diberikan oleh persamaan P =3E Cos ?I =3RI², di mana P adalah daya, E tegangan muka antara transformator dan perapian tungku, I adalah arus elektroda dan R perapian ohmik perlawanan. Adapun faktor daya persamaannya adalah PF =Cos ? – V [R/(R²+X²)], di mana R dan X berturut-turut adalah hambatan ohmik dan reaktansi sistem. Reaktansi tungku X terutama ditentukan oleh dimensi tungku dan pengaturan listrik dan mendekati konstan selama kondisi operasi umum yang sama dipertahankan. Tanpa mempertimbangkan faktor daya pada jaringan listrik, hambatan ohmik di perapian dan arus listrik yang diizinkan di elektroda adalah parameter yang menentukan beban dalam tungku.
Namun, efek faktor daya yang rendah dapat dengan mudah dikompensasikan dengan pemasangan bank kapasitor untuk memperbaiki faktor daya pada jaringan.
Ada cara yang berbeda untuk mengatur resistensi ohmik dengan pemilihan bahan baku dan terutama granulometri dan kualitas bahan karbon. Namun, ada beberapa faktor utama berikut yang memerlukan pertimbangan khusus.
- Kecenderungan untuk menumpuk coke bed yang besar biasanya memberikan penurunan resistensi ohmik.
- Bahan konduktif dalam muatan cenderung memberikan aliran arus dari sisi elektroda yang lagi-lagi menghasilkan resistansi yang berkurang.
- Peningkatan suhu pada sisi elektroda meningkatkan kemungkinan aliran arus dari sisi dan dengan demikian menurunkan hambatan total.
Pengalaman SAF konvensional adalah ekonominya bergantung pada ketersediaan tenaga listrik yang murah. Lebih lanjut persyaratan jenis zat pereduksi tertentu untuk mengontrol resistivitas listrik dalam tungku adalah penting. Waktu retensi yang rendah di tungku dibandingkan dengan tungku sembur memberikan kesempatan untuk menurunkan pengurangan keadaan padat dan pemanfaatan gas di dalam tungku. Oleh karena itu, gas lepas mewakili sebagian besar masukan panas dalam proses dan pemanfaatan gas yang berarti merupakan faktor utama dalam penghematan proses.
Kualitas bahan baku memiliki dampak terbesar pada proses. Di satu sisi mempengaruhi komposisi terak dan di sisi lain pola peleburan di dalam tungku (berdasarkan sifat fisik dan jumlah input energi).
Sifat fisik menentukan apakah smelter dapat berjalan dalam (i) mode resistansi konvensional menggunakan resistansi listrik terak, atau (ii) mode busur terlindung menggunakan resistansi listrik terak dan busur atau menggunakan resistansi listrik dari feed mix.
Fitur SAF
SAF tipikal dengan operasi terak terdiri dari cangkang tungku berbentuk lingkaran atau persegi panjang dengan lubang keran terpisah untuk terak dan logam. Untuk beberapa proses, terak dan logam disadap melalui satu lubang keran dan dipisahkan ke hilir melalui pengecoran kaskade atau skimmer. Cangkang tungku dilapisi tahan api dan – jika pendinginan cangkang tambahan diperlukan oleh proses tersebut – air didinginkan oleh sistem pendingin dinding samping khusus. Bagian bawah cangkang biasanya didinginkan dengan ventilasi udara paksa. Elektroda dikonsumsi oleh tungku mandi. Elektroda yang memanggang sendiri dengan selubung atau elektroda yang sudah dipanggang secara berkala diperpanjang dengan potongan baru. Elektroda secara semi otomatis dimasukkan ke dalam bak dengan tungku pada beban listrik penuh dan tanpa gangguan operasi tungku.
Rakitan kolom elektroda berisi semua fasilitas untuk menahan, menyelipkan, dan mengatur penetrasi ke dalam bak. Semua operasi elektroda dilakukan secara hidrolik.
Tenaga listrik biasanya disuplai dari transformator tungku melalui saluran arus tinggi, tabung bus fleksibel berpendingin air di elektroda dan klem kontak ke elektroda. Jika proses menghasilkan off gas yang mengandung sejumlah CO, tungku biasanya dirancang sebagai jenis tungku tertutup dan off gas dikumpulkan dan digunakan untuk aplikasi lebih lanjut seperti pembangkit listrik, pemanasan, pemompaan, pembangkit uap, dll.
Fitur normal utama tungku berbasis AC adalah sebagai berikut.
- Kolom elektroda perawatan rendah untuk berbagai jenis elektroda
- Perangkat penahan dan selip elektroda yang dirancang kuat dan aman dari kegagalan
- Desain tungku yang kuat tidak memungkinkan penonjolan/gerakan
- Sistem pengisian elektroda berongga
- Desain atap berpendingin air kedap gas menghasilkan gas kaya CO berkualitas tinggi
- Penerapan sistem pemulihan energi dimungkinkan
Tungku DC konvensional
Tungku DC umumnya tipe melingkar dan energi listrik diubah menjadi panas terutama oleh busur, yang didirikan antara ujung elektroda dan mandi terak. Elektroda atas dihubungkan sebagai katoda dan sistem bawah konduktif dihubungkan sebagai anoda. Tungku tipikal dengan operasi rendaman terak terbuka biasanya terdiri dari 1 hingga 3 lubang keran terak dan 1 hingga 2 lubang keran logam pada ketinggian yang lebih rendah. Tungku memerlukan pengaturan pendinginan lanjutan di area atap dan dinding samping karena fakta bahwa suhu terak cair bersentuhan langsung dengan bahan tahan api dan karena panas radiasi busur. Konsep refraktori biasanya dirancang dengan hati-hati untuk mengadopsi kondisi agresif ini. Elektroda dikonsumsi oleh proses tungku. Elektroda prebaked secara berkala diperpanjang dengan potongan baru. Konsep konvensional menerapkan lengan elektroda untuk mengatur elektroda. Fungsi mekanis dan prinsip transfer daya listrik mirip dengan kolom elektroda berbasis AC konvensional.
Juga tungku DC dapat dirancang sebagai jenis tungku tertutup dan CO dapat dikumpulkan. Konsumsi energi dapat dioptimalkan karena kombinasi regulator gerakan elektroda dengan pengontrol pengapian thyristor dan kecepatan elektroda yang tinggi. Sistem kolom elektroda DC biasanya memungkinkan tergelincir dan terjepit di bawah daya penuh (menyediakan waktu penyalaan daya yang maksimal). Perangkat bagian tengah yang dapat diganti dengan cepat sangat penting untuk waktu pengoperasian yang maksimal. Dalam tungku DC biasanya pengaturan makan cerdas diperlukan untuk memaksimalkan throughput dan umur refraktori. Fitur lain dari tungku DC adalah sebagai berikut.
- Desain cangkang yang kuat
- Sistem pengisian elektroda berongga
- Desain sistem pendingin atap dan dinding samping untuk mendukung perlindungan yang memadai pada tingkat konsumsi energi sedang
Tungku DC biasanya beroperasi dengan busur terbuka, yang melebur material dalam waktu yang sangat singkat. Bahan dapat diisi melalui sistem elektroda berongga langsung ke busur. Biasanya busur menari di ujung elektroda. Oleh karena itu, juga praktis untuk mengisi bahan secara langsung di sekitar ujung elektroda. Di beberapa tungku dimungkinkan untuk menumpuk lapisan pelindung dinding samping dengan bahan yang diisi. Sebagian besar proses, di mana terak terlalu panas tidak memungkinkan perlindungan dinding samping semacam ini. Secara umum dapat dinyatakan bahwa konsumsi energi keseluruhan tungku DC lebih tinggi dibandingkan dengan tungku AC karena hal-hal berikut.
- Ada beban panas radiasi yang lebih tinggi di freeboard tungku
- Ada persyaratan pendinginan tungku tambahan karena suhu proses yang lebih tinggi
- Ada asap logam tingkat tinggi yang menghabiskan energi tambahan
Manfaat tungku DC adalah penggunaan langsung bahan halus yang menghilangkan kebutuhan investasi dalam proses aglomerasi intensif yang dibutuhkan di bagian hulu tungku. Selain itu, tingkat harga bahan halus yang lebih rendah membantu mengurangi biaya pengoperasian secara keseluruhan.
Penerapan SAF
Area aplikasi SAF meliputi produksi ferro chrome, ferro nickel, ferro mangan, silico mangan, ferro niobium, Ilemenite (TiO2 slag) serta potensi daur ulang limbah.
Awalnya, paduan ferro secara eksklusif diproduksi di tanur sembur khusus yang menghasilkan besi kasar yang terdiri dari silikon, kromium, dan mangan isi kecil hingga sedang. Jenis peleburan dan kesetimbangan metalurgi menentukan kandungan karbon dari paduan ini. Tungku busur terendam adalah unit yang jauh lebih berkualitas untuk menghasilkan paduan besi berkaitan dengan kontrol suhu dan penyesuaian potensi reduksi yang berbeda. Seiring waktu, industri paduan ferro independen didirikan yang memenuhi permintaan industri baja yang terus meningkat saat ini. Mayoritas paduan besi diproduksi oleh peleburan pirometalurgi yang berlangsung di tungku busur terendam. Daya saing yang kuat dari tungku busur terendam di sektor ini terutama dicapai dengan pemasangan unit peleburan daya tinggi yang canggih.
Saat ini lebih dari 99% paduan besi dan produksi TiO2 dilakukan di tungku busur terendam AC. Tidak ada aplikasi dalam pirometalurgi untuk tungku DC yang tidak dapat dilakukan di tungku AC.
Pengembangan sistem elektroda besar, teknologi transformator canggih, dan prinsip konstruksi tungku baru telah memungkinkan desain SAF persegi panjang berkapasitas besar dengan dimensi panjang hingga 36 m dan lebar 17 meter. Dari sudut pandang teknologi, unit yang lebih besar pun dimungkinkan, tetapi kelayakan ekonomisnya harus diperiksa dengan cermat.
Saat ini SAF tungku persegi panjang 120 MVA berkapasitas tinggi dengan thyristor plus sistem pendingin tembaga dan tungku DC 70 MW untuk ferro chrome telah dipasang.
Perkembangan baru diakui untuk proses yang menerapkan operasi penangas terak yang meningkat dalam konstruksi unit yang sangat efisien dengan kepadatan daya tinggi. Kepadatan daya yang lebih tinggi di tungku menyebabkan fluks panas yang lebih tinggi melalui dinding samping yang memerlukan penerapan konsep pendinginan baru.
Sistem kontrol juga mengalami evolusi yang signifikan selama dekade terakhir seperti yang ditunjukkan di bawah ini.
- 1906 – Dikontrol secara manual
- 1955 – Pengontrol berkas listrik seimbang
- 1960 – Pengontrol kumparan bergerak
- 1965 – Pengontrol transduktor
- 1975 – Pengontrol transistor
- 1985 – Pengontrol H&B
- 1995 – Pengontrol perangkat lunak
Sejak akhir 1950-an, semua SAF dilengkapi dengan pengontrol elektroda. Tungku busur terendam canggih saat ini menggunakan pengontrol perangkat lunak. Aplikasi DC untuk teknologi tungku busur terendam menunjukkan peningkatan pangsa di seluruh dunia di area khusus terutama di beberapa paduan besi, pembersihan terak, dan unit produksi TiO2. Namun demikian, sebagian besar tungku busur terendam dan akan tetap berbasis teknologi AC.