Tungku Induksi dan Aspek Operasional Penting
Tungku Induksi dan Aspek Operasional Penting
Pengembangan tungku induksi untuk pembuatan baja telah menjadi keuntungan bagi produsen baja kecil. Tungku ini mudah dipasang, dioperasikan, dan dirawat. Tungku ini lebih kecil dalam ukuran panas dengan investasi biaya rendah dan disukai oleh pabrik baja berkapasitas lebih rendah. Dalam tungku ini, baja diproduksi dengan melelehkan bahan muatan menggunakan panas yang dihasilkan oleh medan elektromagnetik.
Tungku induksi pada dasarnya terdiri dari wadah, kumparan induktor, dan cangkang, sistem pendingin dan mekanisme miring. Wadah dibentuk dari bahan tahan api, yang dilapisi dengan kumparan tungku. Wadah ini menampung bahan muatan dan kemudian meleleh. Pilihan bahan refraktori tergantung pada jenis muatan dan pada dasarnya terdiri dari refraktori asam, basa atau netral.
Kumparan induktor adalah kumparan tembaga berbentuk tabung dengan jumlah lilitan tertentu. Arus bolak-balik (AC) melewatinya dan fluks magnet dihasilkan di dalam konduktor. Fluks magnet yang dihasilkan menginduksi arus eddy yang memungkinkan pemanasan dan selanjutnya proses peleburan di dalam wadah.
Shell adalah bagian terluar dari tungku. Ini menampung wadah dan kumparan induktor, dan memiliki kapasitas termal yang lebih tinggi. Ini terbuat dari paralelepiped persegi panjang dengan pelat baja karbon rendah dan disambungkan di sudut-sudutnya oleh pembawa tepi dari potongan sudut dan strip logam non-magnetik.
Sistem pendingin biasanya melalui sistem aliran satu arah dengan kumparan tembaga berbentuk tabung yang terhubung ke sumber air melalui selang karet fleksibel. Proses pendinginan penting karena rangkaian tungku tampak resistif, dan daya sebenarnya tidak hanya dikonsumsi dalam bahan yang diisi tetapi juga dalam resistansi koil. Kehilangan kumparan ini serta hilangnya panas yang dilakukan dari muatan melalui wadah tahan api membutuhkan kumparan untuk didinginkan dengan air sebagai media pendingin untuk mencegah kenaikan suhu yang tidak semestinya dari kumparan tembaga.
Bahan baku dan sumber energi
Scrap peleburan baja, besi reduksi langsung dan besi kasar/besi cor adalah bahan baku input untuk tungku induksi. Rasio barang-barang ini dan teknologi peleburan bahan masukan ini bervariasi sesuai dengan ketersediaan bahan baku dan lokasi pabrik. Bahan baku yang dipilih lebih lanjut diperlukan untuk produksi baja kualitas tertentu. Untuk operasi peleburan yang lebih baik dan efisien dalam tungku induksi, pengisian bahan baku harus memenuhi kriteria berikut.
- Harus sepadat mungkin. Pemadatan skrap penting untuk memastikan pemanasan yang seragam dan cepat serta untuk menghemat energi.
- Harus bersih. Karat, minyak, minyak, dan pasir, dll. sebaiknya nol.
- Harus bersih secara metalurgi, yaitu bebas dari gumpalan terak, oksida, dll., terutama untuk besi, tengkorak, dan paduan besi tereduksi langsung.
- Tidak ada atau kurang ujung runcing yang tajam, terutama dalam kasus skrap yang berat dan besar.
- Ini harus dipisahkan dari bahan berbahaya seperti bahan peledak, wadah tertutup, zat menguapkan, dan tersedia dalam ukuran yang dapat dikenakan biaya di lantai toko.
Listrik adalah satu-satunya sumber energi untuk peleburan baja di tungku induksi. Tungku induksi dijalankan dengan daya maksimum sejak awal. Ada beberapa kesalahpahaman tentang menjalankan tungku pada keran rendah pada awalnya dan kemudian secara bertahap meningkat ke keran yang lebih tinggi. Masukan daya maksimum meningkatkan laju peleburan dan karenanya mengurangi waktu siklus panas. Faktor daya dipertahankan mendekati satu.
Penurunan tegangan dari sumber juga harus dipantau untuk efisiensi energi yang lebih baik. Tingkat konsumsi daya lebih lanjut tergantung pada ukuran tungku dan diturunkan karena kapasitas tungku meningkat kira-kira hingga 15 hingga 17 ton dan setelah itu tingkat konsumsi tetap hampir konstan di sekitar 600 kWh/ton.
Aspek penting dari operasi
Saat baja cair dieksitasi oleh arus yang berlawanan dengan arus yang mengalir dalam kumparan induksi, baja cair diaduk untuk menaikkan permukaannya di tengah. Permukaan baja cair naik lebih tinggi karena frekuensi menjadi lebih rendah, yaitu agitasi baja cair terjadi lebih kuat di tungku frekuensi rendah daripada di tungku frekuensi tinggi. Efek agitasi ini memungkinkan untuk memastikan suhu yang seragam dari baja cair dan kualitasnya yang seragam serta untuk mempromosikan jebakan bahan yang diisi dan fusi zat pengatur komposisi kimia, khususnya penambahan karbon. Di sisi lain, agitasi yang berlebihan dapat menyebabkan masalah seperti keausan oksidatif pada baja cair dan peleburan dari refraktori atau bahaya percikan baja cair.
Setelah pencairan selesai, terak dihilangkan. Terak yang dihasilkan selama peleburan cenderung menempel pada dinding tungku. Ini mengurangi volume tungku sehingga mengurangi keluaran logam per panas. Superheating logam dilakukan pada suhu yang lebih tinggi dan ditahan selama beberapa menit. Ini menghambat terak untuk mengendap pada lapisan tungku menjaga tungku tetap bersih dengan volume penuh.
Komposisi terak bervariasi tergantung pada proses spesifik yang digunakan dan jenis baja yang diproduksi. Komposisi terak tungku dan sendok seringkali sangat kompleks. Terak yang terbentuk merupakan hasil reaksi kompleks antara silika, oksida besi dari skrap baja, oksidasi lain dari produk peleburan, dan reaksi dengan lapisan tahan api. Terak terdiri dari fase cair kompleks oksida besi, mangan, magnesium dan silikon, silikat dan sulfida ditambah sejumlah senyawa lain, yang mungkin termasuk alumina, kalsium oksida dan sulfida, oksida tanah jarang dan sulfida, dll.
Saat memproduksi baja, kimia produk akhir dikendalikan. Analisis kimia dari semua bahan masukan dilakukan untuk mendapatkan keputusan tentang campuran muatan. Setelah menyelesaikan 50% pengisian bahan masukan, sampel mandi dianalisis untuk komposisi kimianya. Berdasarkan analisis kimia sampel rendaman pada tahap ini, perhitungan dibuat untuk penambahan logam lebih lanjut. Jika sampel rendaman pada tahap ini menunjukkan persentase karbon, belerang dan fosfor yang tinggi, maka kandungan besi tereduksi langsung dari muatan meningkat. Sampel mandi akhir diambil ketika 80% peleburan selesai. Berdasarkan analisis sampel ini, penyesuaian lain dibuat dalam muatan. Kandungan karbon yang lebih rendah dalam sampel dikoreksi dengan meningkatkan jumlah pig iron/cast iron dalam muatan. Silikon dan mangan dalam logam dioksidasi oleh oksida besi dari besi tereduksi langsung. Sulfur juga diencerkan dengan besi tereduksi langsung. Karena penggunaan besi reduksi langsung, elemen jejak dalam baja yang dibuat di tungku induksi tetap terkendali.
Baja cair adalah output yang diinginkan dari tungku induksi. Jumlahnya tergantung pada kapasitas tungku, dan kualitasnya tergantung pada bahan baku dan komposisi baja. Temperatur sadapan tergantung pada jenis baja dan panas super yang dibutuhkan dalam baja cair untuk penggunaan akhirnya. Penyadapan baja pada suhu tinggi meningkatkan erosi tahan api dan konsumsi daya.
Pemanasan super yang tidak perlu dari baja cair ke suhu tinggi menghabiskan energi secara signifikan. Meminimalkan panas berlebih dari bak cair akan menghemat energi. Tergantung pada spesifikasi baja dan kehilangan suhu selama transfer baja cair ke mesin pengecoran kontinyu, suhu superheat harus diputuskan. Dalam setiap panas, suhu mandi baja cair harus diukur dan dipantau untuk mendapatkan penghematan energi yang optimal. Sistem kontrol daya yang tepat dengan penyesuaian potensiometer perlu disediakan untuk meminimalkan kehilangan energi akibat panas berlebih.
Memiringkan tungku untuk efek penuangan lelehan merupakan kegiatan operasional terakhir sebelum pengecoran. Tungku biasanya dimiringkan untuk mencapai sudut 90 derajat atau lebih besar untuk penuangan baja cair secara lengkap.
Aspek lain dari pembuatan baja tungku induksi
Bergantung pada kerapatan daya yang dipasang dan praktik peleburan, efisiensi termal tungku induksi dapat melebihi 80%, tetapi biasanya berkisar antara 60% hingga 78%.
Tungku induksi biasanya tetap terbuka selama seluruh proses peleburan di mana para pekerja melakukan skimming terak dan pemantauan kualitas rendaman cair. Namun, ini menyebabkan kehilangan panas yang signifikan dan karenanya penutup atau penutup khusus perlu dipasang untuk mengurangi kehilangan panas. Secara khusus, mengurangi waktu tutupnya tetap terbuka saat meleleh, dapat menghasilkan penghematan energi yang besar.
Kebutuhan energi teoritis untuk melebur besi hanya 340 kWh per ton sedangkan daya aktual yang dibutuhkan sekitar 600 kWh. Perbedaan ini disebabkan oleh dua faktor yaitu (i) yang melekat pada prinsip peleburan dalam tungku induksi yang meliputi inefisiensi dalam rugi-rugi bus bar listrik, rugi-rugi arus eddy, rugi-rugi refraktori, rugi-rugi air pendingin, dll., dan (ii) kerugian operasional yang sebagian besar disebabkan oleh penyimpanan baja cair yang tidak perlu dan berlebihan dalam tungku induksi.
Peralatan tungku induksi harus ditempatkan dengan jarak minimum antara setiap peralatan untuk mengurangi kerugian kabel. Untuk sangat mengurangi rugi-rugi perkabelan, penting untuk memperpendek jarak antara badan tungku dan kapasitor peningkat faktor daya karena arus yang sangat besar mengalir di antara keduanya.
Efisiensi tungku induksi dinyatakan sebagai total, dikurangi kerugian perpindahan listrik dan panas. Diagram keseimbangan panas tipikal tungku induksi tipe wadah wadah frekuensi tinggi dan menengah ditunjukkan pada Gambar. 1. Rugi-rugi listrik terdiri dari transformator, konverter frekuensi, kondensor, pengkabelan, kabel, koil, dll. Rugi-rugi pada kumparan merupakan faktor penting, di mana tungku kapasitas tergantung. Kehilangan panas dalam tungku induksi terdiri dari kehilangan konduksi panas yang keluar dari dinding tungku ke sisi koil, kehilangan radiasi panas yang dilepaskan dari permukaan lelehan, kehilangan penyerapan di ring hood, kehilangan leleh terak, dll. Kumparan tungku didinginkan dengan air yang juga menghasilkan dalam kehilangan panas. Efisiensi panas tungku frekuensi tinggi dan menengah (60 % – 78%) sedikit lebih besar dari tungku frekuensi rendah (58 % – 71%).
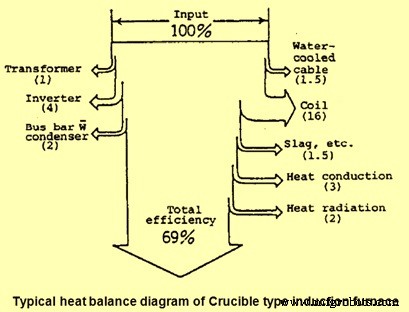
Gbr 1 Diagram keseimbangan panas tipikal tungku induksi wadah
Salah satu masalah yang paling kritis dengan proses pembuatan baja tungku induksi adalah keterbatasan untuk memperbaiki baja untuk mengurangi kandungan fosfor di bawah batas yang diinginkan. Fosfor yang lebih tinggi dan pengambilan nitrogen selama peleburan induksi membuat produk akhir menjadi keras dan rapuh dan tidak dapat digunakan untuk banyak aplikasi penting. Selain itu, kualitas besi spons yang sebagian besar bersumber dari unit produksi berbasis batubara juga memiliki kualitas yang kurang baik, terutama dari segi metalisasi dan kandungan fosfor. Karena kelemahan ini, penggunaan DRI yang lebih tinggi dalam tungku induksi menghasilkan hasil yang rendah dan konsumsi energi/daya yang lebih tinggi serta fosfor yang lebih tinggi dalam baja.
Emisi lingkungan
Karena tidak ada batu bara atau bahan bakar yang dibakar dalam tungku induksi dan tidak ada prosedur pemurnian yang dilakukan, emisi hanya bergantung pada kebersihan dan komposisi bahan yang diisi. Dua kategori utama emisi dapat dibedakan. Kategori pertama dan utama berkaitan dengan kebersihan muatan, mis. karat, kotoran, pasir pengecoran, cat, minyak, logam yang digalvanis atau disolder, yang kesemuanya merupakan unsur yang menimbulkan emisi debu dan asap (organik atau logam). Kategori kedua berkaitan dengan reaksi kimia pada suhu tinggi, (misalnya sambil menahan atau menyesuaikan komposisi logam), yang dapat menimbulkan asap metalurgi karena oksidasi.
Selain itu, lapisan tahan api (asam-SiO2, netral-Al2O3, atau basa-MgO) dapat menambahkan sejumlah kecil partikel debu ke emisi. Sulit untuk mendapatkan data emisi rata-rata karena kebersihan muatan, yang merupakan kontributor dominan terhadap emisi, sangat bervariasi dari unit ke unit.
Tingkat emisi dari tungku induksi tergantung pada bahan muatan yang sekali lagi tergantung pada produk yang dibuat dari tungku itu. Jika produk yang dibuat adalah pengecoran dengan kualitas yang baik maka emisinya berkisar antara 1 sd 2 kg/ton metal charge tetapi jika ingot/billet yang mana maka tingkat emisi orde 10 sampai 20 kg/ton metal charge adalah normal. . Tingkat emisi tertinggi terjadi selama pengisian dan pada awal siklus peleburan. Ukuran partikel berkisar dari 1 – 100 mikro meter, dengan lebih dari 50% lebih kecil dari 10 -20 mikro meter. Mengisi sisa minyak atau bor dalam tungku dingin menyebabkan adanya uap organik dalam gas buang.
Sejumlah besar asap dan gas panas dilepaskan dari bejana tungku terbuka selama operasi tungku induksi dan menyebar ke seluruh lantai pabrik, mempengaruhi kesehatan pekerja.
Mengenai potensi polusi tungku induksi, dapat diamati bahwa volume, kuantitas dan emisi berbahaya dari kontaminan padat dan gas cukup rendah dibandingkan dengan tungku busur listrik. Peralatannya tidak perlu rumit seperti tungku busur listrik sehingga dapat menghemat biaya untuk unit tungku induksi skala kecil. Pada saat yang sama, polutan yang dikeluarkan harus sesuai dengan peraturan.
Langkah-langkah yang terlibat untuk pengendalian polusi termasuk menangkap asap dengan mekanisme tudung hisap yang dirancang dengan baik. Kap harus menarik seluruh gas buang yang harus dibersihkan oleh pemisah siklon. Pembersihan lebih lanjut dari partikulat yang lebih halus dilakukan baik melalui bag filter atau scrubber basah, dan kemudian mengeluarkan gas bersih untuk masuk ke atmosfer. Mekanisme suction hood dapat berupa tipe side, swivel atau canopy hood. Langkah terakhir adalah pembuangan bahan padat yang tersisa sebagai lumpur atau debu.
Konsentrasi partikulat dalam emisi dari tungku induksi untuk produksi baja cair tidak boleh melebihi 100 mg/cum, dinyatakan pada kondisi referensi 0 derajat C, 101,325 kPa dan kondisi kering tanpa koreksi kandungan oksigen, dan dikompensasikan untuk efek apa pun pengenceran udara ke konsentrasi.
Tungku pengaman dan tungku induksi
Bekerja dengan logam cair selalu menjadi pekerjaan yang berbahaya. Tungku induksi efisiensi tinggi saat ini telah meningkatkan kondisi kerja dengan membuat toko lelehan menjadi lebih sejuk, bersih, dan umumnya tempat kerja yang tidak terlalu berbahaya karena kebisingan panas dan asap yang terkait dengan tungku pembakaran tidak ada. Namun tungku ini tidak menghilangkan bahaya yang melekat dalam bekerja di dekat logam cair.
Alasan sebagian besar kecelakaan di bengkel peleburan dengan tungku induksi adalah (i) masuknya logam basah atau lembap ke dalam leburan, menyebabkan ledakan air/logam, (ii) kurangnya keterampilan operator selama pengambilan suhu, pengambilan sampel, atau penambahan besi. paduan, menyebabkan percikan logam, (iii) menjatuhkan potongan besar bahan muatan ke dalam bak cair, menyebabkan percikan logam, (iv) perhatian yang tidak tepat pada pengisian menyebabkan tindakan menjembatani, (v) kegagalan untuk berdiri di belakang garis pengaman, menyebabkan situasi terperangkap , (vi) bersentuhan dengan konduktor listrik, mengesampingkan sakelar interlock pengaman atau bersentuhan dengan kapasitor yang tidak terisi penuh, menyebabkan sengatan listrik atau sengatan listrik, dan (vii) kurangnya pelatihan operator yang tepat.