Teknologi PERED untuk Produksi Besi Pengurangan Langsung
Teknologi PERED untuk Produksi Besi Pengurangan Langsung
Teknologi PERED juga dikenal sebagai teknologi 'Pengurangan Persia'. Ini adalah teknologi reduksi langsung yang ditemukan dan dipatenkan oleh 'Mines and Metals Engineering GmbH' pada tahun 2007. Proses reduksi langsung PERED mengubah oksida besi, dalam bentuk pelet atau bijih lump, menjadi produk yang sangat tereduksi yang cocok untuk pembuatan baja. Pengurangan oksida besi terjadi tanpa peleburannya dengan bantuan reduksi gas dalam keadaan padat dalam tungku poros vertikal. Teknologi ini meningkatkan proses reduksi langsung untuk produksi besi tereduksi langsung (DRI).
Prosesnya adalah proses reduksi langsung berbasis gas yang telah dikembangkan oleh tim spesialis yang berpengalaman di berbagai bidang proses reduksi langsung untuk memastikan bahwa semua aliran proses yang berbeda diperhatikan dalam proses utama untuk mendapatkan hasil yang optimal dan efisien. . Gas yang paling populer digunakan untuk reduksi adalah gas alam yang direformasi meskipun gas lain seperti gas Corex dan gas oven kokas dll juga dapat digunakan. Teknologi PERED menurunkan biaya modal, konsumsi air, biaya pemeliharaan, dan konsumsi energi.
Dalam PERED, proses reduksi berlangsung pada suhu yang lebih rendah karena metode pendinginan yang lebih baik dan pengurangan emisi gas polutan. Dengan panas yang lebih sedikit, gas pereduksi yang lebih homogen, umpan pelet yang lebih terkontrol, dan penggunaan kompresor sentrifugal, PERED membutuhkan lebih sedikit air, listrik, dan gas untuk beroperasi, di samping pengeluaran operasional dan pemeliharaan yang lebih sedikit.
Keluaran dari pabrik reduksi langsung PERED dapat berupa (i) besi reduksi langsung dingin (CDRI), besi briket panas (HBI), kombinasi CDRI/HBI, HBI/besi reduksi langsung panas (HDRI), dan CDRI/ HDR.
Teknologi PERED adalah teknologi hemat energi yang ditingkatkan dan karenanya menghemat energi dan sumber daya. Itu membuat penggunaan energi dan bahan baku secara optimal yang menghasilkan pengurangan biaya produksi dengan keuntungan tambahan menjadi lebih ramah lingkungan dibandingkan dengan proses reduksi langsung berbasis gas lainnya. Teknologi ini juga memberikan peningkatan fleksibilitas selama pengoperasian. Ini telah dibuat untuk memiliki fleksibilitas dalam penggunaan berbagai bahan baku (seperti bijih dengan belerang tinggi) dan sumber energi. Proses tersebut dapat menggunakan hingga 50% bijih besi dalam bentuk lump. Proses ini bekerja pada tekanan yang terbukti lebih tinggi. Gas proses kering yang digunakan dalam proses menghasilkan aliran gas yang lebih tinggi dengan sistem yang sama, yang pada gilirannya meningkatkan produksi atau untuk produksi yang sama mengurangi konsumsi daya.
Pabrik reduksi langsung pertama berdasarkan teknologi PERED dengan kapasitas desain 0,8 juta ton per tahun (Mtpa) dimulai pada Juni 2017 di kota Shadegan, provinsi Khouzestan, Iran. Pabrik DRI dimulai tanpa masalah. Produk dari tanaman ini memiliki metalisasi lebih dari 93%, dan kandungan karbon lebih dari 1,5%. Kapasitas pabrik 75 ton per jam (tph) dicapai pada hari pertama seiring dengan angka konsumsi yang baik untuk utilitas. Kapasitas pabrik yang dirancang juga tercapai dalam waktu singkat. Pabrik PERED DRI kedua dengan kapasitas 0,8 Mtpa ditugaskan selama Oktober 2017 di Kompleks Baja Mianeh di provinsi Azarbaijan Timur di Iran (Gbr 1). Dua pabrik PERED lagi masing-masing 0,8 Mtpa dan satu pabrik 0,3 Mtpa sedang dibangun. Pabrik 0,3 Mtpa di PR China didasarkan pada gas oven kokas.
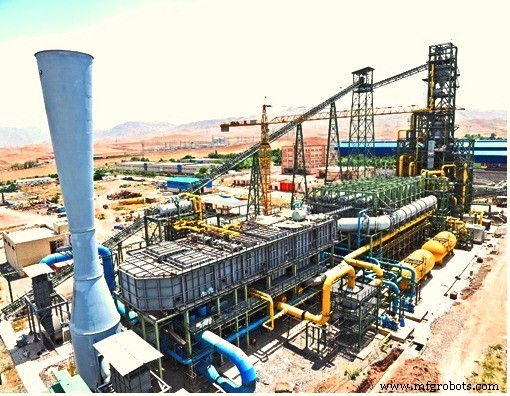
Gbr 1 Pabrik PERED DRI di Kompleks Baja Mianeh di provinsi Azarbaijan Timur, Iran
Proses PERED terdiri dari beberapa perbaikan atas teknologi reduksi langsung berbasis gas yang ada. Fitur yang paling penting dari proses pengurangan PERED diberikan di bawah ini.
- Proses PERED adalah proses berkelanjutan yang memanfaatkan aliran gas pereduksi yang tidak terputus untuk menghilangkan oksigen (O2) dari bahan umpan oksida besi dan juga untuk karburasi DRI produk.
- Konsumsi bahan bakar diminimalkan dengan mendaur ulang gas teratas dari tungku poros vertikal kembali ke proses.
- Sistem reformasi gas dirancang khusus untuk penggunaan karbon dioksida (CO2) yang dihasilkan selama reduksi oksida besi di tungku poros vertikal. Sistem ini dirancang untuk konversi katalitik gas alam tanpa pembentukan jelaga. Ini menghilangkan kebutuhan sumber eksternal O2 untuk oksidasi parsial metana (CH4).
- Proses ini dirancang untuk mencapai pemulihan panas maksimum dengan memanaskan udara utama, gas alam, dan gas umpan.
Dalam proses PERED, inovasi dan review peralatan utama dimulai langsung dari tungku poros vertikal. Tungku poros unik dari jenisnya dan dirancang untuk meningkatkan pola aliran padat dan gas sehingga dapat meningkatkan reaksi yang terjadi di dalam tungku. Ini menghasilkan volume zona reduksi yang lebih tinggi sehingga menghasilkan tingkat produksi yang lebih tinggi. Tungku memiliki injeksi gas pereduksi ganda yang meningkatkan distribusi gas di dalam tungku. Pengumpanan dan distribusi beban bijih di dalam tungku ditingkatkan untuk pencapaian hasil yang lebih baik. Distribusi beban bijih di dalam tungku ditingkatkan karena pengenalan pipa umpan yang baru ditemukan.
Ada beberapa fitur khusus di dalam tungku poros. Di zona atas yang juga merupakan zona reduksi, fitur khusus meliputi (i) pengumpanan dan distribusi oksida oleh pipa umpan khusus, (ii) optimalisasi rasio tinggi terhadap diameter untuk meningkatkan pemanfaatan tungku, dan (iii) optimalisasi reaksi reduksi; Fe (oksida)+CO=Fe (logam)+CO2 dan Fe (oksida)+H2=Fe (logam)+H2O
Reaksi reduksi dapat dioptimalkan di zona reduksi tungku karena (i) tidak ada peralatan di zona reduksi tungku, (ii) ada pengurangan pembentukan butiran halus karena peningkatan distribusi material di dalam tungku karena pipa umpan khusus , (iii) optimalisasi volume reduksi efektif di dalam tungku, (iv) desain zona reduksi untuk menghilangkan kemungkinan pencemaran akibat kebocoran gas, dan (v) desain tungku khusus untuk mengurangi biaya modal dan perawatan. Karakteristik desain khusus dari zona reduksi tungku mencakup (i) desain pelepasan gas atas ganda dari ujung piringan atas, (ii) profil suhu beban yang ditingkatkan untuk memastikan kualitas produk yang seragam, (iii) pengurangan sisa besi butiran/pelet bijih untuk meningkatkan umur refraktori di saluran gas atas, (iv) optimalisasi ukuran tungku untuk mendapatkan volume zona reduksi yang diperlukan, dan (v) suhu off gas yang lebih rendah karena peningkatan efisiensi sehingga memiliki beban yang lebih rendah pada scrubber. Karakteristik desain zona reduksi juga menyediakan (i) injeksi gas pereduksi ganda, (ii) desain port bustle persegi panjang untuk injeksi gas yang lebih baik dan perawatan yang lebih baik, (iii) konstruksi refraktori tirus untuk menangani pembengkakan DRI, (iv) fleksibilitas untuk memiliki suhu dan komposisi gas yang berbeda karena injeksi oksigen, (v) peningkatan pemanfaatan gas yang sibuk, (vi) peningkatan distribusi gas di dalam tungku, (vii) suhu unggun yang seragam di seluruh tungku, (vii) penghapusan kemungkinan pengelompokan di dalam tungku, (vii) fleksibilitas untuk menggunakan gumpalan bijih besi, dan (viii) peningkatan produktivitas dan kualitas produk.
Ada juga reformasi insitu gas yang terjadi di dalam tungku poros vertikal. Gas panas mengandung persentase tertentu dari CH4, CO2 dan H2O. Gas ini ketika bersentuhan dengan besi metalik (besi metalik bertindak sebagai katalis), menghasilkan gas pereduksi tambahan di dalam tungku poros. Reaksi reformasi insitu adalah seperti yang diberikan di bawah ini.
CH4+H2O=CO+3H2 dH>0
CH4+CO2=2CO+2H2 dH>0
Di satu sisi, reaksi reformasi in-situ endotermik membutuhkan suhu gas yang lebih tinggi, sementara di sisi lain, degradasi pelet/benjolan bijih besi, pembentukan butiran halus, dan pengelompokan terjadi ketika suhu tinggi. Desain tungku poros PERED memiliki port hiruk pikuk ganda untuk mengoptimalkan jumlah CH4 dalam gas hiruk pikuk yang dibutuhkan untuk mengontrol suhu unggun.
Fitur khusus dari gas reformer yang digunakan dalam proses PERED adalah sebagai berikut.
- Gas alam dipanaskan terlebih dahulu dalam penukar pemulihan gas buang reformer
- Sistem pemulihan mendapatkan panas dari gas tumpukan reformer
- Reformer adalah reformer multi-ruang dengan tabung katalis. Ini menggunakan tabung reformer berdiameter 250 mm dan dirancang untuk memiliki kebutuhan ruang yang lebih sedikit
- Katalis 'Performex' telah dikembangkan khusus untuk proses
Zona pendinginan tungku poros vertikal memiliki pengumpan beban berputar 360 derajat. Desain feeder yang canggih memberikan kinerja zona pendinginan yang lebih baik dan seragam. Beban diumpankan di zona pendinginan dengan empat poros berputar yang dikontrol secara independen. Karena ini adalah zona dingin, tidak ada jaket air. Jika ada cluster yang terbentuk maka cluster yang sama copot dengan rotasi terbalik dan kontrol kecepatan. Gas pendingin ke zona pendingin disuntikkan dari header luar dan gas pendingin panas dikumpulkan secara seragam dengan lepas landas berbentuk. Juga, tidak ada kemungkinan kegagalan di header karena tidak ada refraktori di header. Selanjutnya sistem pendingin dirancang untuk menghilangkan partikel dalam scrubber. Gas dikompresi dan diumpankan ke zona outlet produk bawah tungku vertikal.
Spesifikasi khas dari pembangkit PERED 0,8 Mtpa bersama dengan angka konsumsi diberikan di Tab 1
Tab 1 Spesifikasi umum untuk pabrik PERED |
No.Sl. | Subjek | Satuan | Nilai |
1 | Kapasitas | Mtpa | 0,8 |
2 | Ukuran pelet oksida | mm | 5-35 |
3 | Diameter tungku vertikal | m | 5,5 Kira-kira |
4 | Total tinggi | m | 52 Kira-kira |
5 | Tingkat produksi per jam | t/j | 105 |
6 | Jam operasional pabrik per tahun | Jam | 8,000 |
7 | Suhu operasi tungku vertikal | Deg C | 850 |
8 | Tekanan operasi atas normal untuk tungku | kg/cm persegi g | 0,6 |
9 | Tekanan operasi bawah normal untuk tungku | kg/cm persegi g | 2,1 maks. |
10 | Persyaratan untuk pengurangan gas | N cum/jam | 170.000 |
11 | Pengurangan gas per ton produk | N cum | 1600 |
12 | Kepadatan DRI | t/cum | 1.7 |
13 | Kepadatan oksida besi | t/cum | 2.3 |
Fitur yang berguna dari proses pengurangan PERED
Berikut ini adalah fitur berguna dari pabrik reduksi langsung PERED.
- Proses terbukti dengan keberhasilan pengoperasian pabrik komersial
- Biaya modal spesifik pabrik yang rendah
- Konsumsi energi spesifik yang rendah menghasilkan biaya energi yang lebih rendah
- Biaya operasi pabrik rendah
- Konsumsi air spesifik rendah
- Pencemaran lingkungan tingkat rendah
- Tersedia beberapa pilihan produk yang meliputi CDRI, HDRI dan HBI
- Prosesnya fleksibel sehubungan dengan penggunaan oksida besi. Dapat menggunakan hingga 50% bongkahan bijih besi
- Ada fleksibilitas dalam proses penggunaan bijih belerang tinggi
- Ketersediaan desain tersedia untuk pembangkit dengan kapasitas lebih dari 1 Mtpa