Alcoa Mengejar Keunggulan Keandalan
Jika Anda tidak tahan dengan panasnya cuaca, sebaiknya Anda tidak mencari pekerjaan di fasilitas Logam Utama Alcoa di Indiana selatan.
Potline bernapas api dan cawan lebur berisi logam cair dapat mendorong suhu sekitar lantai produksi mendekati tiga digit. Panas tampak terpancar dari mesin. Keringat bercucuran di pipi dan punggung pekerja. Istirahat yang sering untuk air dan Gatorade adalah suatu keharusan.
Ini adalah lingkungan yang menuntut secara fisik, tetapi panas nyata yang dirujuk dalam paragraf pertama lebih terkait dengan posisi pabrik khusus ini di industri peleburan aluminium. Situs ini, bagian dari Operasi Warrick besar-besaran Alcoa, dibangun pada akhir 1950-an dan mulai memproduksi aluminium mentah untuk industri lembaran kaleng pada awal 1960-an.
Ini adalah pabrik tua di industri yang peka terhadap usia dan teknologi. Ada 33 pabrik peleburan Amerika yang beroperasi pada 1980. Saat ini, ada 13. Hanya 6 persen dari kapasitas aluminium dunia yang akan diproduksi tahun ini di pabrik peleburan yang berusia lebih dari 50 tahun. Jam terus berdetak.
Untuk status ini, tambahkan itu:
-
25 persen tenaga kerja pabrik saat ini memenuhi syarat untuk pensiun melalui usia atau masa kerja;
-
upah yang dibayarkan oleh pabrik termasuk yang tertinggi di industri; dan,
-
beberapa tahun yang lalu, biaya perawatan peleburan ini per metrik ton aluminium yang diproduksi adalah yang tertinggi kedua dalam sistem Alcoa global.
Bisakah kamu merasakan panasnya? Setiap karyawan di pabrik ini melakukannya. Namun alih-alih menunggu kematian yang tampaknya sudah dekat, personel pemeliharaan dan operasi telah melangkah maju dan mengambil tindakan.
“Kita harus melakukannya jika ingin mempertahankan standar hidup ini dan menjaga agar pabrik ini tetap hidup,” kata manajer Sistem Bisnis Alcoa, Mark Keneipp. “Ini adalah kenyataan baru. Anda hanya perlu menghadapinya.”
Dimulai dengan melihat ke cermin.
“Tantangan kami adalah untuk menjadi kompetitif dalam biaya meskipun usia kami sudah tua,” kata Keneipp. “Kami tidak lagi berada di depan kurva usia. Kita harus memiliki cakrawala 15 hingga 20 tahun untuk menarik modal di dalam Alcoa. Jika 25 sampai 30 tahun, itu akan bagus. Untuk itu, kami harus terus membuktikan diri sebagai pabrik yang ramping, hemat biaya, stabil, dan efisien.”
Ini bukan lingkungan untuk yang lemah. Tetapi melalui kerja keras dan ketekunan, ada banyak imbalan.
Lorong-lorong yang panjang, sempit dan suhu yang tinggi merupakan karakteristik dari area potline di pabrik Alcoa Primary Metals. Potline situs menghasilkan 265.000 metrik ton aluminium setiap tahun. Batas Waktu Panggilan
Upaya untuk mempertahankan kehadiran Alcoa Primary Metals di komunitas manufaktur Indiana selatan dimulai di tingkat perusahaan.
Pada tahun 1997, CEO Alcoa Alain Belda mulai membawa prinsip Toyota Production System (TPS) ke 250 lokasi global perusahaannya.
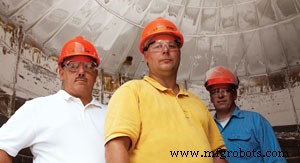
Manajer produksi pabrik aluminium Rodney Cunningham (kiri), koordinator proses Larry York dan senior staf insinyur proses Brian Audie berdiri di dalam tangki alumina yang kosong di halaman Operasi Warrick Alcoa. Situs tersebut secara tradisional menggunakan empat tangki seperti bejana penampung untuk alumina, bahan utama dalam proses peleburan aluminium. Inisiatif lean manufacturing dan pemikiran kritis membuat pabrik berhemat menjadi dua tangki, menghemat banyak uang perusahaan.
TPS adalah filosofi lean manufacturing yang dibangun di atas produksi “tepat waktu”, eliminasi pemborosan, dan pemecahan masalah yang cepat. Namun, pabrik peleburan Indiana membuat penemuan penting saat menerapkan sistem tersebut.
“TPS, flow, dan lean tidak akan berfungsi jika Anda memiliki peralatan yang tidak stabil dan tidak dapat diprediksi,” kata Keneipp.
Pemeliharaan pabrik dan keandalan mesin yang efisien, efisien, dan hemat biaya harus diutamakan.
Untuk mengilustrasikan maksudnya, Keneipp menawarkan diagram yang disebut "gunung es pemeliharaan." Di atas air adalah biaya pemeliharaan langsung terkait dengan bahan, tenaga kerja, lembur, layanan kontrak, dan overhead dan manfaat. Di bawah permukaan mengintai biaya tidak langsung yang terkait dengan waktu henti, penyiapan dan startup, jadwal yang terlewat, inventaris berlebih, manajemen krisis, pembelian darurat, dan efek riak keseluruhan pada produksi.
“Komponen tidak langsung disandera oleh peralatan dan proses pabrik yang tidak stabil,” katanya.
Semua limbah ini merusak sistem dan meningkatkan biaya operasi dan pemeliharaan.
Mekanik umum Dick Day telah memimpin organisasi, standarisasi, dan inisiatif penghematan biaya di boks alat terpusat pabrik .
Pada tahun 2002, pabrik peleburan ini memiliki total biaya perawatan lebih dari $35 juta. Rasionya yang “sangat tinggi” lebih dari $137 dalam biaya perawatan untuk setiap metrik ton aluminium yang diproduksi (lihat “Fakta-faktanya” untuk tonase tahunan) menempatkannya di urutan kedua hingga terakhir di antara pabrik peleburan Alcoa di seluruh dunia. Rata-rata global pada tahun 2002 adalah $90 per metrik ton.
Pabrik Alcoa ini dan para pemimpinnya memiliki dua pilihan.
“Manajer pabrik, Royce Haws, mengatakan kami akan mengurangi biaya kami. Itu bukan pilihan untuk tetap di tempat kami berada. Itu akan terjadi,” kata Keneipp. “Kita bisa melakukannya dengan cara yang cerdas atau dengan cara yang picik. Ketika Anda menjadi rabun jauh, itu adalah hari-hari yang menakutkan. Sulit untuk menarik modal ke pabrik untuk mengejar hal-hal yang perlu dilakukan ketika Anda hanya menunda perawatan. Tidak ada yang merasa baik tentang pendekatan itu. Itulah motivasi bagi orang-orang untuk mencari sesuatu yang lebih baik.”
Sherman Clark mengulurkan tangan saat derek di atas memindahkan bagian atas wadah ke tempatnya. Menangkap Ombak
Jika Anda belum menebaknya sekarang, pabrik Alcoa memilih pendekatan cerdas untuk menurunkan biaya perawatan. Pemimpin pemeliharaan bekerja sama dengan konsultan dari Life Cycle Engineering (LCE) dan Ron Moore Group pada awal 2003 untuk menciptakan pendekatan yang disebut Reliability Excellence Process, yang diterapkan dalam tiga "gelombang". Proses ini didasarkan pada keyakinan bahwa kemitraan yang diformalkan dan didefinisikan dengan baik sangat penting antara pemeliharaan dan operasi. Dalam kemitraan ini, operasi memiliki peralatan dan memiliki kepentingan utama dalam keandalan. Pemeliharaan adalah mitra setara yang berdedikasi untuk menyediakan metode, keterampilan, keahlian, dan dukungan yang tepat waktu dan efektif.
“Itu perubahan besar,” kata pengawas teknik keandalan Joseph Motz. “Dulu lingkungan silo dengan banyak penunjuk jari.”
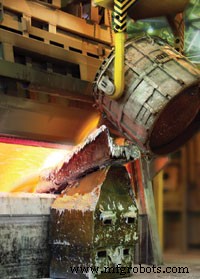
Logam cair dituangkan dari wadah
di Departemen Ingot tanaman Alcoa.
Beberapa contoh:
Seorang operator melihat potensi masalah. Tidak ada perbaikan yang dijadwalkan atau dibuat. Mesin rusak. Siapa yang harus disalahkan?
Atau, pemeliharaan muncul untuk pekerjaan pemeliharaan preventif dua jam. Saat berada di mesin, ia menemukan masalah tambahan dan menyelesaikan pekerjaan PM delapan jam kemudian, sehingga memengaruhi output. Siapa yang harus disalahkan?
Jawaban dalam kasus ini adalah pemeliharaan dan operasi.
“Kami harus menyadari bahwa kami semua berada di tim yang sama,” kata Motz. “Kami semua di sini untuk membuat aluminium. Jika kita pergi ke arah yang berbeda dan tidak bekerja sama, prosesnya tidak akan berhasil.”
Gelombang 1 dalam pendekatan tiga gelombang dimulai pada Juni 2003.
“Gelombang 1 adalah Ron Moore,” kata Keneipp. “Kami membawanya untuk berbicara dengan para pemimpin pabrik utama. Dia menantang paradigma kuno. 'Anda perlu mengambil lebih banyak filosofi pemilik aset.' 'Anda membuang-buang uang.' Dia mengguncang segalanya dan membuka mata.”
Gelombang 2 tiba pada bulan Agustus dengan penilaian Reliability Excellence penuh oleh LCE. Selama periode dua minggu, perusahaan melakukan wawancara panjang dengan 90 karyawan operasi dan pemeliharaan (per jam dan gaji), serta pengontrol pabrik.
Informasi tersebut menyebabkan:
-
analisis keuangan yang merinci perkiraan nilai dalam menutup kesenjangan menuju keunggulan dalam keandalan dibandingkan dengan biaya implementasi (disajikan sebagai perhitungan laba atas investasi);
- rencana induk awal yang menguraikan proses dan metodologi yang diperlukan untuk menutup kesenjangan.
“Kami ingin melihat kondisi kami saat ini dan mengidentifikasi kondisi target,” kata Keneipp. “Kesenjangan antara keduanya adalah rasa sakit atau keuntungan Anda. Apakah sepadan dengan upaya untuk menjembatani kesenjangan? Kami harus membuktikan nilai itu kepada manajemen senior. Kami harus membuktikan ada manfaat dalam memasukkan uang ke pabrik lama.
“Menghadapi semua fakta, adalah bijaksana untuk mendapatkan persetujuan uang sesegera mungkin untuk melanjutkan.”
Gelombang 3 dimulai pada bulan September. Pemimpin operasi dan pemeliharaan:
-
mengimplementasikan rencana induk
-
mendidik semua karyawan tentang peran dan tanggung jawab baru mereka terkait dengan peningkatan keandalan peralatan
-
mengadakan lokakarya tentang teknik peningkatan keandalan yang tepat
-
menetapkan proses yang ditetapkan dan ukuran kemajuan yang efektif
“Ini tidak mudah. Tidak satu pun dari barang-barang ini, ”kata manajer produksi potroom Rodney Cunningham. “Tetapi jika Anda memiliki komitmen manajemen dan kemitraan antara pemeliharaan dan operasi, peluang keberhasilan Anda meningkat. Tanpa hal-hal itu, Anda tidak akan berhasil.”
Meningkatkan Standar
Menetapkan definisi di berbagai bidang telah membantu memicu perbaikan. Fokus utama adalah untuk mendefinisikan "apa yang mungkin?" dan “apa itu kemajuan?”
Sebuah jawaban datang dengan menerima efektivitas peralatan keseluruhan (OEE) sebagai metrik kunci di seluruh pabrik. OEE melacak sumber kerugian pengoperasian, termasuk ketersediaan, kinerja, dan kualitas peralatan, dan dinyatakan sebagai persentase kinerja optimal.
“Ini pada dasarnya ditentukan oleh beberapa kinerja terbaik di masa lalu,” manajer produksi elektroda Tom Svoboda. “Anda melihat itu terjadi. Itu bukan fiktif atau hipotetis. Apakah peralatan berjalan luar biasa bulan itu atau Anda benar-benar di atas proses, itu terjadi. Pertanyaannya adalah, jika Anda melakukannya selama satu periode waktu itu, mengapa Anda tidak dapat melakukannya sepanjang waktu?”
Menggunakan analogi olahraga untuk mengilustrasikan pentingnya 100 persen OEE, jika seorang pelompat tinggi biasanya melompat 6 kaki 6 inci tetapi menetapkan yang terbaik dari 7 kaki, apa yang secara khusus menyebabkan kinerja puncak 100 persen ini. Apakah dia berlatih secara berbeda? Apakah dia mengubah pola makannya sebelum bertemu? Apakah dia memakai sepatu yang berbeda? Dia benar-benar menaikkan standar. Apa yang dapat dipelajari dan apa yang dapat dilakukan untuk mencapai tanda tersebut berulang kali?
Pemeliharaan dan operasi bekerja sama untuk menentukan kinerja puncak untuk fungsi pabrik (misalnya, perakitan anoda), proses (pembongkaran bijih), hasil (memo) dan peralatan individu (tungku cincin). Dalam mengumpulkan informasi ini, ditentukan bahwa penghematan biaya tahunan sebesar $8,3 juta dimungkinkan sebagai hasil dari pencapaian tujuan OEE.
Dengan informasi latar belakang, status saat ini ditentukan dan kondisi target ditetapkan. Aktivitas – proyek kerja yang menggunakan alat lean manufacturing seperti kaizen dan Continuous Improvement – berlangsung. Kemajuan diukur dan dianalisis. Dan, manfaat nyata dihitung.
Pada tahun 2004, peningkatan sebesar $2,4 juta dikaitkan dengan perolehan OEE.
Melihat lebih dalam dan mengambil tindakan juga menyebabkan penurunan biaya perawatan di pabrik peleburan. Pada tahun pertama setelah memulai inisiatif keandalan, pengeluaran turun $1,9 juta, dari angka awal $32 juta menjadi $30,1 juta. Pada tahun 2004, angka itu turun lagi $700.000. Rasio biaya pemeliharaan per metrik ton yang diproduksi juga turun menjadi $109 pada tahun 2004.
Rencana 'Direncanakan'
Upaya besar juga dilakukan untuk mendefinisikan elemen pemeliharaan dengan lebih baik. Secara khusus, dalam sistem keandalan yang dipimpin operator ini, “bagaimana pekerjaan dapat direncanakan?” dan “bagaimana cara menyelesaikan pekerjaan?”
“Melihat ke belakang, kami membodohi diri sendiri dengan berpikir bahwa kami sehat,” kata manajer pemeliharaan Danny Reyes. “Banyak metrik lama kami tidak dapat dihubungi. Kami pikir 'persen pekerjaan yang direncanakan dan dijadwalkan' kami mencapai 85 persen dan 'persen penyelesaian PM' kami mencapai 90 persen.”
LCE memberi tahu pabrik bahwa itu menggunakan definisi yang salah.
“‘Persen pekerjaan yang direncanakan dan dijadwalkan’ sebenarnya hanya ‘persen yang dijadwalkan.’ Perencanaan sangat terbatas,” kata Reyes. “Itu sesuai jadwal. Mungkin 10 persen dari pekerjaan itu direncanakan.”
Rasio 35 banding 1 antara personel pengrajin (140) dengan perencana (empat) adalah inti masalahnya.
“Itu tidak bekerja dengan baik,” kata perencana pemeliharaan Larry McCubbins. “Waktunya sangat sedikit untuk merencanakan. Anda menjadi penjadwal, dan bukan penjadwal yang sangat baik.”
Lingkungan reaktif tumbuh subur dalam pengaturan ini. “Kami melakukan ‘pendekatan pemeliharaan rumah,'” kata Keneipp. “Begitulah cara Anda dan saya menangani proyek pada Sabtu pagi. Ini benar-benar tidak terencana dan tidak efisien.”
Pabrik tersebut telah menambahkan tiga perencana dengan total tujuh, memberikan rasio yang lebih mudah dikelola yaitu 20 banding 1.
“Itu memungkinkan orang-orang ini untuk mengatur, mengatur pekerjaan, merencanakannya, menjadwalkannya dengan pusat produksi, memastikan semua suku cadang ada di sana, memastikan peralatan mati dan waktu dialokasikan,” kata pengawas pemeliharaan peleburan Scott Deon.
Kunci lain untuk perencanaan yang lebih baik:
-
Sebuah dokumen formal sekarang menguraikan komponen pekerjaan yang direncanakan (lihat sidebar di halaman 14). “Empat perencana malang yang kami coba lakukan semuanya tidak melakukan hal yang sama,” kata Deon. “Format baru ini sekarang menstandarisasi cara melakukan pekerjaan.”
-
Area formal dan aman sekarang digunakan oleh para perencana untuk perlengkapan pekerjaan. Di masa lalu, suku cadang dan bahan yang dibutuhkan dikirim sedikit demi sedikit ke lokasi kerja. Tumpukan mungkin duduk selama berminggu-minggu sampai semua barang tiba. Selama waktu tunggu, tidak jarang suku cadang atau alat dipindahkan, hilang atau digunakan untuk pekerjaan lain.
“Sesuai dengan perencanaan pekerjaan, ia memesan semua bahan dan mengirimkannya ke sini. ,” kata McCubbins. “Ketika semuanya untuk pekerjaan itu ada di sini, kami mengumpulkannya di satu atau dua palet. Kerajinan kemudian datang dan membawanya ke lokasi kerja dan melakukan pekerjaan itu.”
-
Komunikasi yang efektif.
“Dulu saya pikir saya tahu apa yang diinginkan orang. Proses ini mengajari saya bahwa saya tidak melakukannya, ”kata McCubbins. “Saya tidak tahu apa yang mereka inginkan dan apa yang tepat untuk mereka. Di masa lalu, saya merencanakan pekerjaan dan tidak mengajukan pertanyaan.”
Menambahkan Deon:“Dengan tanggung jawab bersama dengan produksi, kami sekarang tahu pekerjaan mana yang lebih dulu. Orang yang memiliki peralatan harus tahu apa yang paling penting. Sebelumnya, saya tidak berpikir kami menebak. Tapi apakah kita sudah 100 persen? Mungkin tidak.”
-
Rapat mingguan yang terfokus dan efektif.
“Pemilik aset memimpin rapat dan perencana/penjadwal pemeliharaan area adalah fasilitator,” kata Keneipp. “Jika ini adalah rapat perencanaan, kami mendiskusikan bagaimana kami akan melakukan ini. Jika ini adalah rapat yang menjadwalkan, kami menetapkan jadwalnya.”
Juga terkait dengan bagaimana pekerjaan diselesaikan, pabrik mengambil langkah-langkah untuk mendokumentasikan riwayat peralatan dan menstandarisasi instruksi tugas pemeliharaan.
“Pada hari-hari awal, Anda bisa mendapatkan catatan, tetapi kemudian dokumentasi berhenti,” kata insinyur listrik stasiun penyearah Dan Decastra. “Jadi, kami membuat lokasi di server dan mulai mendokumentasikan. Untuk stasiun ini, kami membuat daftar 'anak nakal'. Kami memilih masalah besar dan mulai dari sana. Sekarang, Anda dapat kembali ke tahun 2001 dan melihat riwayat sakelar udara, kontak, transformator, dan selip.”
Menambahkan insinyur keandalan Jonathan Fulton:“Mungkin sepertiga dari tenaga kerja pemeliharaan kami dapat pensiun besok jika mereka mau. Itu adalah potensi tanggung jawab yang sangat besar bagi kami. Dan, sulit untuk mendapatkan perajin yang berkualitas dari luar. Untuk mengatasi hal ini, kami melakukan standarisasi proses kerja dan mengembangkan riwayat peralatan. Dengan melakukan ini, kita bisa mempercepat orang dengan keahlian teknis.”
Catatan Tempat Tidur
Contoh perbaikan terakhir adalah bagaimana pabrik mendefinisikan dengan lebih baik siapa yang membeli produk perawatan dan bagaimana uang dihabiskan untuk alat dan bahan jenis habis pakai.
Di masa lalu, berbagai macam personel pemeliharaan di pabrik peleburan membeli perkakas tangan, perkakas listrik, produk keselamatan, pembersih, produk penanganan material, dan ratusan barang kebutuhan lainnya. Produk yang dibeli disimpan di tempat penyimpanan alat yang terdesentralisasi di sekitar fasilitas dan di sejumlah tempat penyimpanan tidak resmi (loker, peti, dan lubang lemari).
“Karena pabrik terus berkembang, area ditambahkan. Mereka memiliki kelompok kecil dan seseorang melakukan pemesanan dan mereka mengumpulkan persediaan mereka di sana-sini, ”kata mekanik umum Dick Day. “Kami menghabiskan banyak uang untuk mencoba memberi makan boks satelit ini. Mereka tidak dikelola. Orang-orang membeli barang, tetapi sebenarnya tidak dapat diakses.”
Jika seorang mekanik membutuhkan alat tertentu, dia akan mencarinya. Itu ada di suatu tempat. Jika dia tidak dapat menemukannya, dia akan memesannya. Alat yang dibeli itu mungkin hilang sebelum sampai padanya. Hal ini menyebabkan pemborosan dan pemborosan.
Untuk mengatasi hal ini, boks terpusat dibangun dan semua boks satelit dan item lubang kubus dibawa ke area yang aman dan terjaga keamanannya ini.
Masuklah yang tidak berharga.
“Kami menyadari bahwa kami memiliki banyak barang usang – sesuatu untuk peralatan yang mungkin telah kami keluarkan 10 tahun lalu,” kata Keneipp.
Dan, datanglah yang berharga.
“Sungguh menakjubkan semua yang keluar dari kayu. Seseorang membawa lemari dengan lebih dari $ 38.000 pompa dan dongkrak di dalamnya, ”kata Day, yang menjadi petugas utama boks pusat. “Kami mulai menggunakan apa yang kami miliki. Untuk beberapa bahan, kami tidak perlu memesan apa pun selama setahun.”
Hari ini, Day bertanggung jawab untuk membeli produk yang berhubungan dengan perawatan ini. Dia menerima pembelian, menyimpan barang dan membagikannya sesuai kebutuhan.
“Kami tahu apa yang kami miliki dan di mana lokasinya,” katanya.
Day juga telah menciptakan sistem minimum/maksimum untuk berbagai produk dan memulai upaya standarisasi merek perkakas listrik dan perlengkapan las.
“Dengan alat-alat listrik, kami telah menstandarisasi sebagian besar pada DeWalt, dan kami semakin mendalami alat nirkabel mereka,” katanya. “Untuk perlengkapan las, kami telah menstandarisasi senjata wire feed kami dan suku cadang pengganti untuk senjata tersebut.”
Dia mengerjakan pekerjaan rumahnya dan menemukan cara inovatif untuk memangkas biaya.
Beberapa contohnya adalah:
Sarung Tangan :“Kami biasa membeli merek sarung tangan yang memiliki sedikit tab di atasnya seharga $12 sepasang. Itulah yang semua orang 'harus miliki,'” katanya. “Anda bisa membeli sarung tangan yang sama dengan sedikit karet di dalamnya seharga $2,67 per pasang. Orang-orang menyukainya.”
Minyak hidrolik :“Kami membelinya per galon dengan harga $8 per pop. Membelinya dalam jumlah besar, sekarang kami menghemat $3 per galon. Saya menuangkan minyak ke dalam kendi yang dapat digunakan kembali seharga 57 sen per buah.”
Selang asetilen :“Kami dulu membelinya dalam bentuk spool. Sekarang, kami membelinya dengan gulungan 500 kaki dan memotong apa yang dibutuhkan orang tersebut. Kami menghemat 25 persen.”
Day mengatakan itu semua masuk akal.
“Saya melihatnya sebagai uang saya,” katanya. “Jika ini adalah bisnis saya, beginilah cara saya menjalankannya.”
Membuat Mereka Berkeringat
Melalui kerja keras, kemitraan, kepemilikan, dan pemikiran inovatif, pabrik peleburan Alcoa ini menjadi lebih stabil, ramping, dapat diprediksi, andal, dan hemat biaya.
Manfaat biaya OEE adalah $4,4 juta per tahun untuk tahun 2005 hingga saat ini dibandingkan dengan angka dasar tahun 2003.
Biaya pemeliharaan tahun 2005 mencapai $27,1 juta per tahun dan mencerminkan penurunan $4,9 juta dari angka dasar tahun 2003.
Biaya pemeliharaan untuk kuartal kedua tahun 2005 adalah $96 per metrik ton yang diproduksi dan target ditetapkan untuk mencapai $87 dalam waktu dekat.
Penilaian tindak lanjut LCE menempatkan pabrik dalam kategori "kondisi proaktif" dan pekerjaan sedang dilakukan untuk meningkatkan ke dalam kategori "keunggulan".
Ada optimisme dan momentum.
“Ketika saya dipekerjakan 15 tahun yang lalu, kami berkata, 'Kami adalah teknologi lama. Kami tidak dapat bersaing dengan beberapa fasilitas yang lebih modern,'” kata Fulton. “Bagi saya, hadiahnya adalah melihat kami bersaing dan memiliki efisiensi yang lebih tinggi. Kami memproduksi lebih baik dengan teknologi kami yang berusia 40 atau 50 tahun daripada di lokasi yang dibangun 10 atau 20 tahun yang lalu.”
Meskipun panas tidak akan pernah benar-benar hilang untuk tanaman ini, ia melakukan apa yang bisa dilakukan untuk membuat pesaing berkeringat.
Apa Karakteristik Pekerjaan yang Direncanakan?
-
Ada perkiraan waktu yang akurat untuk pekerjaan tersebut sehingga supervisor memiliki ekspektasi yang masuk akal tentang kapan dia dapat memberikan tugas tersebut.
-
Ada perkiraan akurat dari sumber daya yang dibutuhkan dalam hal personel kerajinan, suku cadang perbaikan/penggantian, peralatan, peralatan pendukung, dll.
-
Semua informasi yang diperlukan (cetak biru, izin, terkait keselamatan, dll.) diperoleh.
-
Urutan langkah pekerjaan, prosedur, dan instruksi untuk menyelesaikan pekerjaan telah ditetapkan.
-
Semua suku cadang dan bahan yang dibutuhkan telah disiapkan.
-
Sebagai pemeriksaan bawaan untuk memastikan kualitas pekerjaan yang direncanakan, diskusikan sifat pekerjaan secara berkala dengan supervisor dan/atau pengrajin yang ditugaskan untuk menyelesaikan pekerjaan tersebut. Pastikan ada pemahaman penuh tentang ruang lingkup pekerjaan dan bahwa paket pekerjaan lengkap telah selesai.