50 Ide untuk Program Pemeliharaan yang Efektif
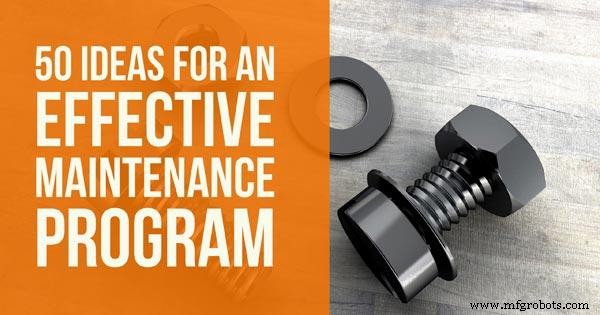
Ketika program pemeliharaan berhasil, setiap area perusahaan akan terpengaruh secara positif. Saat ini, organisasi teratas menuai manfaat dari penerapan program keandalan yang dirancang dan dikelola dengan baik. Apakah Anda siap untuk membawa program keandalan Anda ke tingkat berikutnya? Berikut adalah 50 ide untuk Anda mulai:
Pelajari 12 elemen manajemen keandalan yang efektif. Pastikan organisasi Anda memahami elemen-elemen penting ini dan dampaknya terhadap kinerja – mulai dari yang paling atas. Tanpa fokus kepemimpinan ini untuk program pemeliharaan Anda, tidak ada hal lain yang penting.
Melacak metrik pemeliharaan. Dengan menggunakan metrik dan KPI, organisasi pemeliharaan dapat mengelola aktivitas pemeliharaan secara efisien dan memfokuskan inisiatif peningkatan untuk mendorong nilai.
Terapkan perencanaan dan penjadwalan pemeliharaan. Dengan perencanaan yang efektif, pekerjaan dapat diselesaikan dengan gangguan operasi yang paling sedikit dan penggunaan sumber daya pemeliharaan yang paling efisien.
Pertimbangkan program keandalan yang digerakkan oleh operator. Tanpa kepemilikan peralatan Anda di tangan operator, sulit untuk dapat diandalkan. Menggunakan pendekatan terencana yang melibatkan semua karyawan, keandalan peralatan akan berdampak langsung dan positif pada keuntungan Anda.
Tingkatkan sistem kerja dasar. Banyak organisasi menghabiskan terlalu banyak waktu untuk mencari konsep keandalan dan pemeliharaan baru, dan sangat sedikit waktu untuk menerapkan dan meningkatkan apa yang baru saja mereka mulai.
Gunakan sistem penghargaan bersama untuk mendorong hasil. Jika sebuah organisasi serius tentang integrasi yang lebih erat antar departemen, sistem penghargaan harus dirancang untuk mendorong tindakan dan kinerja semua orang menuju tujuan dan penghargaan yang sama.
Buat rencana pemeliharaan Anda. Membuat rencana pemeliharaan umumnya tidak sulit dilakukan. Tetapi menciptakan program pemeliharaan komprehensif yang efektif menimbulkan beberapa tantangan yang menarik. apa yang membuat perbedaan antara rencana pemeliharaan biasa dan program pemeliharaan preventif yang baik dan efektif.
Dengarkan peralatan Anda. Apakah Anda mendengarkan motor Anda mengeluh tentang kelebihan beban? Apakah Anda melihat kemasan pompa Anda menangis banjir? Apakah Anda mendengar bantalan Anda mengeluh tentang pelumas yang terkontaminasi? Apakah Anda melihat sistem uap Anda batuk kondensat yang berlebihan dan mengeluh tentang siku tegang?
Berhenti menghargai kegagalan. Manajer dapat berbicara sepanjang hari tentang keinginan organisasi untuk proaktif, meningkatkan keandalan, mengurangi biaya, dll. Tetapi orang tidak memperhatikan apa yang Anda katakan; mereka memperhatikan apa yang Anda lakukan. Jika Anda berbicara "keandalan" tetapi membayar dan mengakui kegagalan, coba tebak apa yang akan Anda dapatkan? Apa yang mendapat imbalan akan diselesaikan, titik.
Targetkan 60 persen. Rata-rata, 30 persen dari semua kegiatan pemeliharaan preventif tidak menambah nilai dan harus dihilangkan. 30 persen lainnya dari aktivitas ini dapat diganti dengan teknologi pemantauan kondisi dan pendekatan pemeliharaan prediktif.
Sepenuhnya dengan pemantauan berbasis kondisi. Ada sedikit atau tidak ada pengembalian dari menggunakan satu atau dua teknologi pemantauan kondisi – atau menerapkan CBM ke sejumlah kecil aset Anda dan berharap itu akan berkembang menjadi program yang sukses.
Perkirakan jam kerja dengan lebih akurat. Pengalaman menunjukkan bahwa perkiraan tenaga kerja terbaik secara rutin turun sebanyak 100 persen. Pekerjaan yang diperkirakan memakan waktu lima jam kerja mungkin memakan waktu hingga 10 jam atau paling sedikit dua jam.
Dapatkan pemimpin yang tepat. Pemimpin keandalan perusahaan mengatakan bahwa jika mereka dapat melakukannya lagi, mereka akan menghabiskan lebih banyak waktu untuk memilih orang yang tepat untuk posisi kepemimpinan kunci. Dengan kepemimpinan yang tepat di area yang tepat mendorong hal yang benar, Anda akan sukses.
Gunakan pendekatan multi-alat untuk menghemat lebih banyak. Tim pemeliharaan preventif di American Axle and Manufacturing mengatasi masalah yang ditemukan selama perintah kerja pemeliharaan preventif rutin menggunakan beberapa alat pemantauan kondisi.
Buat daftar peralatan yang terperinci dan akurat. Terlepas dari apa yang mungkin pernah Anda dengar, dasar dari program keandalan yang sukses adalah daftar – daftar peralatan yang terperinci dan akurat yang idealnya direkam dalam perangkat lunak CMMS Anda. Ini berisi informasi penting yang Anda butuhkan untuk merancang, mengembangkan, dan merekayasa program pemeliharaan Anda dari awal.
Jangan pernah menerima “cukup baik”. Dalam proses perbaikan pemeliharaan, ada beberapa area di mana selalu ada keinginan atau arus bawah untuk jalan pintas proses. Salah satu tindakan paling penting dari kepemimpinan pemeliharaan dan keandalan adalah mengharapkan dan mengatur lingkungan yang memungkinkan seluruh organisasi untuk mempraktikkan “Tidak Pernah Cukup Baik” setiap hari.
Meningkatkan proses kerja. Praktik pengoperasian adalah bagian penting dari setiap program pemeliharaan preventif. Praktik yang baik mencegah kegagalan. Praktik yang buruk mendorong kegagalan. Artikel ini membahas contoh praktik bisnis yang harus diterapkan untuk meningkatkan keandalan pabrik secara keseluruhan.
Gunakan metrik pemeliharaan prediktif yang tepat. Apa yang diukur akan ditingkatkan. Atau sebaliknya, apa yang tidak diukur tidak akan pernah diperbaiki. Pelacakan dan pelaporan pada metrik utama memungkinkan Anda berfokus tepat pada perubahan perilaku yang Anda inginkan.
Buat visi yang jelas dan ringkas. Salah satu tanggung jawab pertama kepemimpinan adalah memberikan pandangan yang sederhana dan jelas tentang seperti apa masa depan yang bisa dan seharusnya. Memiliki visi yang jelas dan ringkas untuk meningkatkan pabrik Anda adalah penting. Visi ini harus sederhana dan terlihat.
Pelajari teknik analisis akar masalah. Ketika masalah keandalan muncul, sebagian besar organisasi mengatasinya pada tingkat gejala atau segera mencari untuk menyalahkan seseorang atau kelompok. Analisis akar penyebab adalah proses sistematis untuk memahami dan mengatasi penyebab mendasar dari suatu masalah.
Lihat, dengar, rasakan, cium. Terlepas dari apakah Anda melakukan inspeksi dengan komputer genggam atau sistem kertas, dapat tren data atau tidak, atau memiliki indikator kinerja utama atau tidak, Anda tidak akan berhasil kecuali orang-orang Anda dapat melakukan inspeksi kualitas pada peralatan.
Tentukan model penempatan staf pelumasan. Pertanyaan tentang siapa dalam suatu organisasi yang harus bertanggung jawab atas tugas pelumasan mesin sehari-hari adalah hal biasa. Pelajari tiga struktur organisasi yang paling umum dan buat struktur organisasi Anda sendiri.
Buat backlog yang direncanakan. Prinsip penjadwalan perawatan yang pertama adalah prasyarat untuk memiliki backlog yang direncanakan. Pelajari cara mempersiapkan dan menggunakan jadwal sebagai standar kontrol untuk meningkatkan produktivitas pemeliharaan.
Gunakan analisis Pemeliharaan yang Berpusat pada Keandalan. Analisis Pemeliharaan yang Berpusat pada Keandalan harus dilihat sebagai latihan serius untuk bisnis Anda. Analisis RCM adalah investasi yang membutuhkan waktu, sumber daya, dan uang untuk diselesaikan, tetapi sepadan dengan usaha.
Terapkan Pemeliharaan Produktif Total dalam 12 langkah. Menerapkan TPM menggunakan 12 langkah ini akan memulai Anda di jalan menuju “zero breakdowns” dan “zero defect.” Mencapai keandalan 100 persen membutuhkan disiplin dan kerja tim.
Keluar dari penjara anggaran pemeliharaan. Jika Anda berada di penjara anggaran dan telah mencoba keluar dengan mengkhotbahkan keandalan kepada orang-orang di atas Anda tetapi hanya membuat sedikit kemajuan, inilah rencana untuk membebaskan Anda.
Pelajari nilai “P”. Titik P pada Kurva P-F adalah dimana suatu cacat masuk ke dalam mesin. Pada beberapa waktu di masa depan, ini akan menyebabkan beberapa jenis kehilangan fungsi. Saat cacat tetap ada di mesin, fungsionalitas mesin berkurang seiring waktu. Di beberapa titik di masa depan, Titik F, kegagalan total mesin terjadi.
Buat daftar bahan peralatan. Bill of material peralatan mencantumkan semua komponen aset, termasuk rakitan dan subrakitannya. Dengan daftar bahan peralatan yang andal, seorang perencana dapat menentukan dengan tepat suku cadang apa yang dibutuhkan. Dan dalam keadaan darurat, ini memberikan informasi berharga kepada pengrajin dan orang lain untuk memastikan bahwa suku cadang yang tepat diidentifikasi dan dibeli.
Gunakan interval P-F untuk memetakan dan mencegah kegagalan. Interval P-F adalah bagian informasi yang berharga untuk setiap tim pemeliharaan, dan Anda tidak memerlukan pendidikan khusus untuk menggunakannya. Penggunaan interval P-F dalam menentukan perawatan yang tepat untuk dilakukan pada waktu yang tepat tidak perlu terbatas pada RCM.
Pertimbangkan sistem pemantauan berkelanjutan. Pemantauan berkelanjutan adalah aplikasi perangkat khusus untuk mengumpulkan data gaya pemeliharaan prediktif untuk membantu program pemantauan kondisi. Setiap tahun, teknologi ini semakin murah, dan keinginan untuk pemantauan yang lebih kompleks dan kuat semakin besar.
Bangun hubungan yang kuat dengan operasi. Untuk menjadi lebih baik dalam pemeliharaan, Anda harus menjadi lebih baik dalam membangun hubungan positif dengan operasi. Untuk mencapai keunggulan pemeliharaan, Anda harus memiliki hubungan yang sangat baik. Ini berarti memiliki pemeliharaan yang selaras sepenuhnya dengan tujuan yang lebih besar dari operasi dan perusahaan Anda.
Kuantifikasi biaya mode kegagalan fungsional. Berapa biaya sebenarnya dari sebuah kegagalan? Sayangnya, kami tidak tahu sampai kegagalan terjadi - dan keandalan adalah tentang menghindari kegagalan.
Kembangkan prosedur perawatan standar. Pabrik sering gagal melihat pentingnya memiliki prosedur yang ditulis dengan baik untuk sebagian besar tugas. Artikel ini membahas pentingnya memiliki prosedur yang baik dan menyajikan detail yang diperlukan untuk mengembangkan prosedur pemeliharaan standar yang ditulis dengan baik.
Kelola aset berdasarkan kekritisan. Melalui konstruksi model analisis kekritisan yang tepat, rekayasa keandalan akan dapat menggambarkan peningkatan keandalan apa yang harus dilakukan untuk mengelola kekritisan, sehingga meningkatkan kemampuan mereka untuk mengelola aset berdasarkan kekritisan.
Ajari operator metode “Seharusnya-Seharusnya Lima Alasan”. Operator dalam budaya yang berfokus pada keandalan harus memiliki sikap bertanya dan sangat jeli. Dimasukkannya alat S-A-5Whys dalam keahlian mereka akan menguntungkan organisasi dengan identifikasi awal dan penyelesaian masalah, yang mengarah pada peningkatan keandalan aset.
Dapatkan lebih banyak dari EAM Anda. Semua sistem EAM memiliki kemampuan dasar yang sama untuk mendukung program pemeliharaan Anda. Mereka seperti paket perangkat lunak lainnya – keberhasilannya bergantung pada cara penerapannya dan, yang lebih penting, cara penggunaannya.
Optimalkan pemadaman dengan perencanaan tugas yang efektif. Pemadaman dapat memiliki jadwal yang rumit, tetapi seringkali tidak berhasil karena perencanaan lanjutan yang tidak efektif, yang mengakibatkan pelaksanaan pekerjaan yang tidak efisien dan jadwal pemadaman yang terlampaui. Pemadaman hanya dapat berhasil jika pekerjaan pemadaman direncanakan secara efektif sebelum pekerjaan dijadwalkan dan/atau dimulai.
Gunakan beberapa alat CBM. Sangat penting untuk memahami bagaimana kinerja peralatan di fasilitas dan untuk dapat memprediksi dan mencegah kegagalan sebelum terjadi. Hasil dari kombinasi teknologi pemantauan berbasis kondisi akan memberikan insinyur keandalan kepercayaan yang lebih besar saat berkomunikasi dengan manajemen saat aset mendekati kegagalan yang akan datang.
Terapkan strategi pemeliharaan yang benar. Keandalan yang sebenarnya dicapai ketika metode yang paling hemat biaya diterapkan pada aset di pabrik Anda, sehingga memaksimalkan keandalan dengan total biaya minimum untuk bisnis.
Tolok ukur program pelumasan Anda. Pembandingan memberikan kartu skor yang sangat dibutuhkan untuk area pelumasan yang mungkin tidak terlihat jelas atau sering dipertimbangkan untuk ditingkatkan. Memang benar bahwa kita “tidak tahu apa yang tidak kita ketahui”.
Deteksi masalah mesin sejak dini. Daftar item inspeksi yang sangat banyak ini akan memungkinkan Anda untuk mendeteksi masalah lebih awal, dan semoga menghilangkan waktu henti dan/atau mengurangi biaya perawatan.
Hapus kemacetan proses. Jika hambatan proses Anda terkait erat dengan pemeliharaan dan keandalan peralatan Anda, kemungkinan besar Anda memiliki organisasi pemeliharaan yang sangat reaktif. Untuk beralih dari rezim yang terutama reaktif, fokus yang signifikan harus ditempatkan pada pengembangan dan penerapan sistem yang menggerakkan organisasi menjadi proaktif.
Optimalkan tugas PM. Sayangnya, sebagian besar tugas pemeliharaan preventif tidak memiliki detail yang akan menyediakan data kuantitatif untuk riwayat peralatan, dan tugas tersebut ditulis tanpa mempertimbangkan mode kegagalan. Solusinya adalah dengan mempraktekkan Preventive Maintenance Optimization (PMO), menggunakan semua aspek untuk menulis prosedur PM yang bernilai tambah, komprehensif, dapat diulang, diatur, dan menentukan durasi dan interval eksekusi yang benar.
Buat program analisis oli yang ramping dan efektif. Analisis oli adalah alat yang ampuh dalam program perawatan. Studi kasus ini menyajikan alternatif untuk peralatan uji internal yang mahal, pemanfaatan laboratorium luar yang baik, solusi penyimpanan minyak, metode pelaporan temuan untuk melanjutkan program, dan menjual program kepada manajemen tingkat atas serta operasi dan pemeliharaan.
Gunakan daftar periksa pemeliharaan. Sementara sebagian besar kelompok akan mengatakan bahwa mereka memiliki daftar periksa, memerlukan penggunaan dan akuntabilitas sering kali menjadi faktor utama keberhasilan. Di organisasi Anda, proses apa yang Anda miliki untuk memastikan bahwa orang-orang menggunakan prosedur pemeliharaan dan daftar periksa?
Hindari 5 risiko terbesar. Manajemen aset adalah pendekatan terpadu untuk mengoptimalkan siklus hidup aset Anda, mulai dari desain konseptual, hingga penggunaan, penonaktifan, dan pembuangan. Dengan mengakui dan memperhatikan lima risiko utama berikut untuk pengelolaan aset yang efektif, Anda dapat membuat rencana untuk mengurangi dampak yang mungkin terjadi pada program mereka.
Berikan kepemilikan peralatan teknisi pemeliharaan. Bagaimana Anda mencapai keseimbangan antara kepemilikan peralatan dan membangun keterampilan melalui pelatihan silang, dan memiliki kemampuan untuk menyelesaikan pekerjaan sepanjang waktu? Apakah berdasarkan budaya organisasi?
Bersikaplah cerdas tentang kiting. Perlengkapan untuk pekerja pemeliharaan untuk melakukan tugasnya adalah salah satu cara yang lebih mudah dan efektif untuk memungkinkan penyelesaian pekerjaan yang berkualitas dengan dampak produktivitas yang minimal, terutama jika disertai dengan pekerjaan yang terencana dengan baik dan terjadwal secara fungsional.
Bekerjalah menuju nol kegagalan. Pengalaman dan data menunjukkan bahwa tidak ada kegagalan yang mungkin terjadi dalam program pemeliharaan. Seperti seseorang pernah berkata, “Jika Anda berpikir Anda tidak bisa, Anda mungkin benar. Jika Anda pikir Anda bisa, Anda mungkin benar.”
Kelola proses perubahan. Aspek yang paling sulit tetapi paling bermanfaat dalam memimpin upaya pemeliharaan dan peningkatan keandalan adalah mengelola proses perubahan dalam organisasi. Proses perubahan perilaku dari status reaktif ke status proaktif adalah transisi yang menantang untuk program pemeliharaan apa pun.