Pengecoran dan Pengecoran Lempengan Tipis
Pengecoran dan Pengecoran Lempengan Tipis
Untuk produksi produk datar, baja cair umumnya dicetak dalam bentuk pelat biasanya dalam kisaran ketebalan 150 mm hingga 350 mm di mesin pengecoran pelat kontinu. Pelat ini diperiksa, dijahit dan kemudian dipanaskan kembali di tungku pemanas pelat ke suhu penggulungan sebelum digulung ke gulungan canai panas di pabrik strip panas semi kontinu atau kontinu. Pengembangan teknologi thin slab casting and rolling (TSCR) merupakan langkah maju untuk mengurangi jumlah langkah proses dalam produksi hot rolled coils (HRC). Awalnya teknologi TSCR dikembangkan dengan tujuan utama untuk mengurangi investasi dan biaya produksi tetapi hari ini telah menjadi salah satu jalur produksi yang paling menjanjikan untuk mempertahankan baja sebagai bahan utama dalam aplikasi teknologi dan dianggap sebagai teknologi yang telah mencapai tingkat kedewasaan yang tinggi. Kecepatan pengecoran 6,0 meter per menit (m/min) untuk ketebalan pelat 50/55 mm cukup umum akhir-akhir ini.
Awalnya, hanya baja karbon biasa berkualitas komersial yang dicor melalui jalur pengecoran pelat tipis. Namun saat ini sebagian besar grade baja termasuk baja karbon rendah, sedang dan tinggi, grade baja HSLA (high strength low alloy), grade baja line pipe, dan grade baja untuk aplikasi otomotif termasuk grade IF (interstitial free) dapat dicetak melalui pelat tipis. rute pengecoran. Ternyata teknologi ini telah membawa perubahan paradigma dalam teknologi baja casting dan rolling. Teknologi pengecoran dan pengerolan pelat tipis dimungkinkan karena beberapa perbaikan dalam proses pengecoran dan pengerolan yang meliputi (i) desain cetakan, (ii) osilasi cetakan hidrolik, (iii) penggunaan rem elektromagnetik (EMBR), (iv ) penggunaan descaler tekanan tinggi dan pemandu sisi roller (edger) di pabrik, (v) reduksi inti cair dinamis (LCR), (vi) kualitas bubuk cetakan, dan SEN yang didesain ulang, dan (vii) pendinginan semprotan air.
Keuntungan utama teknologi TSCR dibandingkan pengecoran pelat tebal dan pengerolan panas meliputi (i) pengurangan biaya modal, (ii) pengurangan tenaga kerja, (iii) pengurangan ruang lantai yang dibutuhkan, (iv) peningkatan hasil produk akhir dari cairan baja, (v) pengurangan konsumsi bahan bakar spesifik, dan (vi) pengurangan konsumsi daya spesifik.
Sejarah
Implementasi konsep TSCR tidak berhasil sampai pertengahan tahun delapan puluhan karena banyaknya tantangan teknologi yang terkait dengan teknologi tersebut. Terobosan pertama ke arah ini dicapai pada bulan Oktober 1985 oleh SMS Schloemag-Siemag ketika pelat tipis pertama dengan ketebalan 50 mm dicetak di pabrik percontohan di Kreuztal-Buschhutten. Keberhasilan ini dicapai dengan cetakan berbentuk corong yang dipatenkan dan nozzle masuk terendam yang dioptimalkan. SMS Schloemag-Siemag memberi teknologi ini nama 'Compact Strip Production (CSP)'. Pabrik CSP pertama dipesan pada akhir 1987 dan ditugaskan di Nucor Steel, Crawfordsville, Indiana pada Juli 1989. Dalam beberapa hari setelah commissioning, terjadi kerusakan besar pada mesin pengecoran karena operator yang tidak berpengalaman. Hal ini berdampak pada cepatnya penerimaan teknologi ini. Hampir pada saat yang sama, proses In-line Strip Production (ISP) sedang dikembangkan secara intensif oleh Mannesmann Demag dan grup Arvedi. Pengembangan ISP dimulai pada tahun 1988 berdasarkan paten Arvedi-Mannesmann. Pada tahun 1992, pabrik ISP prototipe dibangun oleh Arvedi di tempat kerjanya di Cremona, di mana sebagian besar pengembangan proses ini telah dilakukan. Pada tahun 1994-95 pabrik prototipe menyelesaikan tahap pertama pengembangannya. Kemudian berdasarkan teknologi ISP, Acciaieria Arvedi telah mengembangkan proses pengecoran pelat tipis/penggulungan tak berujung baru dengan nama merek Arvedi ESP. Dengan proses ini strip setebal 0,8 mm sedang diproduksi. Voest Alpine (VAI) dari Austria (sekarang menjadi teknologi Primetals) dan Danieli dari Italia juga telah mengembangkan teknologi pengecoran dan penggulungan pelat tipis. Teknologi VAI dikenal sebagai Continuous Thin Slab Casting and Rolling Technology (CONROLL) dan menghasilkan pelat hingga ketebalan 125 mm. Ini lebih dari pelat ketebalan sedang. Teknologi yang dikembangkan oleh Danieli ini dikenal sebagai Continuous flexible Thin Slab Rolling (fTSR) dan menghasilkan slab dengan kisaran ketebalan 70 mm hingga 90 mm. Implementasi Teknologi TSCR mendapat dorongan besar setelah China dan India mulai memperluas produksi baja mereka secara besar-besaran. Saat ini pabrik TSCR tiga untai berdasarkan teknologi CSP telah dipasang di ESSAR, Gujarat, India (sekarang Arcelormittal Nippon Steel India Limited).
Proses TSCR telah mengalami perkembangan yang sangat dinamis terutama berkaitan dengan output per pabrik, ketersediaan, biaya konversi, kisaran grade baja yang dihasilkan, dimensi bentuk-dekat-jaring, geometri strip, parameter kualitas, dan karakteristik permukaan. Saat ini, teknologi TSCR digunakan untuk memproduksi tidak hanya baja dalam rentang karbon rendah dan karbon menengah, tetapi juga baja tahan karat feritik dan austenitik serta baja silikon berorientasi butir. Tahap hulu dan fasilitas pemrosesan jalur panas hilir juga telah mengalami perkembangan lebih lanjut, dengan rekayasa dan teknologi pabrik yang beradaptasi dengan produk pabrik CSP, misalnya, ketebalan jalur panas turun menjadi sekitar 1 mm.
Fitur metalurgi dan fitur penting lainnya dari proses TSCR
Saat memproses baja dalam proses TSCR dari tundish ke coiler, ada beberapa fitur penting metalurgi dan proses lainnya seperti yang dijelaskan di bawah ini.
- Pemadatan yang cepat dari lempengan tipis menyempurnakan struktur dendritik. Koreksi pada struktur dendritik membantu struktur yang lebih homogen.
- Inklusi non-logam berukuran kecil dan bulat, mempertahankan bentuknya selama pengerolan panas dan berkontribusi pada sifat isotropik (seperti ketangguhan, dan kelenturan, dll.).
- Semua elemen paduan mikro yang ditambahkan tetap berada dalam larutan. Karena suhu tinggi pelat tuang sebelum pengerolan panas, curah hujan dini dapat dihindari.
- Untuk meminimalkan kesulitan pengecoran di daerah peritektik, kandungan karbon dari banyak baja paduan mikro dibatasi antara 0,05% dan 0,06%. Pembatasan ini menguntungkan ketangguhan dan kemampuan las.
- Suhu pelat yang tinggi selama pembengkokan dan pembengkokan meminimalkan kecenderungan untuk membentuk retakan melintang.
- Suhu dalam tungku penyeimbang bergantung pada elemen paduan mikro dan dirancang untuk menjaga paduan mikro dalam larutan.
- Pengisian langsung adalah faktor utama yang mengurangi konsumsi energi selama penggulungan panas.
- Pada pelat tipis yang menggelinding, deformasi pada lintasan awal seringkali melebihi 50%. Deformasi berat pada suhu tinggi sangat penting untuk menghaluskan butir austenitik kasar (lebih dari 1000 mikrometer) dengan kristalisasi ulang.
- Kehalusan dan keseragaman butir austenitik merupakan prasyarat untuk struktur feritik halus hingga 4 mikrometer hingga 5 mikrometer.
- Pendinginan yang dipercepat di meja run-out dan di bawah pendinginan austenit lebih lanjut memurnikan ferit.
Proses produksi dan tingkat evolusi suhu yang khas dalam proses TSCR ditunjukkan pada Gambar 1.
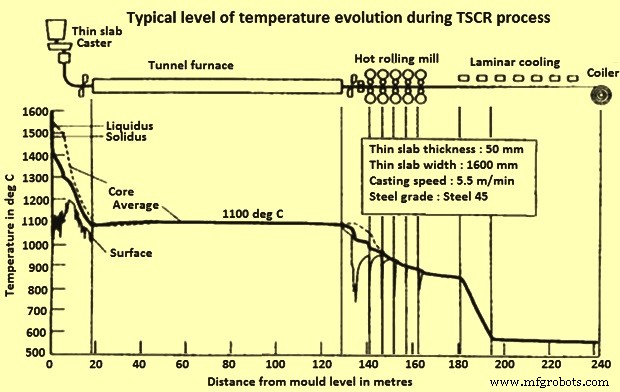
Gbr 1 Tingkat evolusi suhu yang umum selama proses TSCR
Pemadatan yang lebih cepat dalam TSCR memberikan struktur yang lebih seragam dan lebih halus. Jarak lengan dendrit sekunder yang halus (SDAS), dicapai karena pemadatan yang cepat dalam pengecoran, dan mendorong struktur yang lebih homogen dengan struktur pemisahan mikro yang lebih sedikit daripada pengecoran konvensional. Segregasi mikro adalah pemisahan antara lengan dendrit di mana konsentrasi zat terlarut minimum berada di tengah lengan dendrit dan konsentrasi zat terlarut maksimum berada di antara lengan. Faktanya, SDAS adalah ukuran non-homogenitas dalam pengecoran kontinu slab. Dalam pengecoran pelat tipis, sistem 'reduksi inti cair' (LCR) digunakan. Pengurangan inti cair memungkinkan ketebalan untai di bawah cetakan dikurangi saat inti masih dalam fase cair. Umumnya segmen pertama dalam sistem pemandu untai dapat disesuaikan untuk mendapatkan pengurangan ketebalan untai yang diinginkan. Proses TSCR yang berbeda dijelaskan di bawah ini.
Produksi Strip Ringkas
Konsep dasar dalam teknologi CSP adalah tercapainya efisiensi biaya yang maksimal melalui keterkaitan tiga tahapan proses yaitu (i) pengecoran, (ii) pemerataan temperatur, dan (iii) hot rolling. Baja cair setelah pembuatan baja dipadatkan ke dalam tundish dari mesin pengecoran kontinu (CCM). Dalam teknologi ini, baja cair dicetak ke dalam pelat dengan ketebalan yang diinginkan mulai dari 50 mm hingga 90 mm. Pelat tersebut kemudian digeser sampai panjang yang sesuai dan diangkut ke terowongan atau tungku penyeimbang yang biasanya diatur pada suhu 1150 derajat C. Pada titik ini, pelat menunjukkan ukuran butir austenit dari 500 mikrometer hingga 1000 mikrometer. Setelah waktu tinggal 20 menit di tungku, lempengan meninggalkan tungku dan dipotong. Pelat tipis panas kemudian memasuki pabrik finishing pada suhu sekitar 1000 derajat C. Pelat digulung menjadi strip panas (ketebalan mulai dari 0,8 mm hingga sekitar 16 mm dan lebar berkisar antara 800 mm hingga 1880 mm) saat melewati pabrik penyelesaian 5, 6 atau bahkan 7 berdiri. Strip panas setelah penggulungan memasuki run out table (ROT) di mana ia mengalami pendinginan laminar ke suhu melingkar. Kemudian digulung ke suhu kamar. Skema proses CSP ditunjukkan pada Gambar 2.
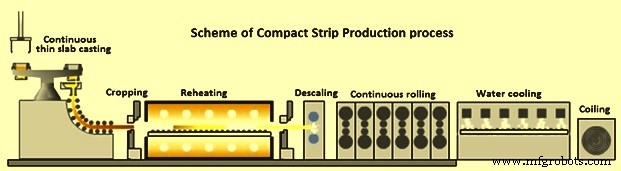
Gbr. 2 Skema proses Produksi Baja Ringkas
Elemen utama dari proses CSP adalah ladle turret, mould, strand guide system, pinch roll unit, pendulum shear, heating furnace dengan transfer car untuk menghubungkan dua casting stand, rolling mill dengan 5 sampai 7 stand, strip cooling dan coiler. Proses ini memiliki pengaturan ketebalan pelat yang fleksibel selama pengecoran melalui reduksi inti cair, memungkinkan adaptasi terhadap ketebalan strip akhir dan ketebalan pengecoran dan kecepatan pengecoran. Strip panas dengan ketebalan 1 mm dapat digulung panas dengan nyaman dengan teknologi ini. CSP menggunakan sistem kontrol profil dan kerataan yang mengadopsi teknologi CVC yang terkenal untuk penyesuaian. Kapasitas satu strand plant sampai dengan 1,5 juta ton per tahun (Mpta), two strand plant sampai dengan 3 Mpta, dan 3 strand plant sampai dengan 4 Mpta. Tata letak skema pabrik CSP tiga untai ditunjukkan pada Gambar 3 dan konsep yang berbeda dari pabrik CSP ditunjukkan pada Gambar 4..
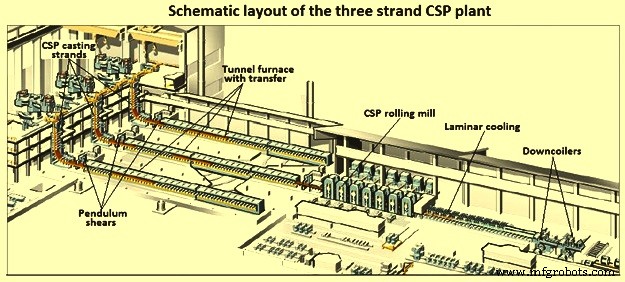
Gbr 3 Tata letak skema pabrik CSP tiga untai
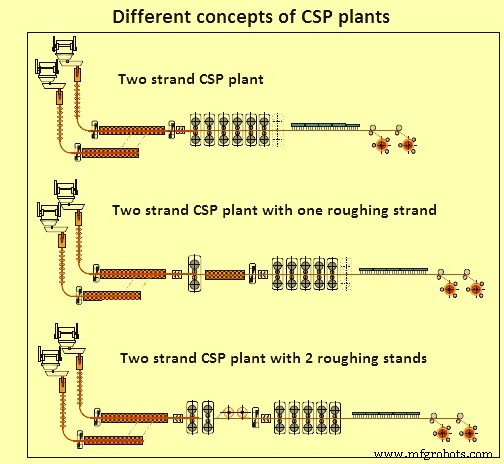
Gbr 4 Konsep berbeda dari pabrik CSP
Inti dari proses CSP adalah cetakan kromium-zirkonium-tembaga berbentuk corong yang dipatenkan dengan panjang 1100 mm (Gbr 5). Pengumpanan baja cair dilakukan melalui submerged entry nozzle (SEN) ke dalam batas-batas rongga cetakan yang sempit dengan melebarkan saluran masuk cetakan dalam bentuk corong. Corong ini berakhir kira-kira di tengah panjang cetakan di luar itu, dinding samping lebar cetakan sejajar dan dipisahkan oleh ketebalan yang sama dengan ketebalan pelat tipis. Sisi-sisi dinding cetakan diruncingkan untuk mengimbangi penyusutan baja yang mengeras. Karena pemadatan pelat tipis yang cepat, perlu untuk memberikan panduan untai sepanjang sekitar 4,5 m hingga 5 m hanya bahkan pada kecepatan pengecoran tinggi 6 m/menit.
Dibandingkan dengan desain aslinya, mesin pengecoran CSP telah mengalami perkembangan yang luar biasa sehubungan dengan konfigurasi cetakan berbentuk corong, panjang pemandu untai, loop kontrol teknologi, serta fleksibilitasnya dalam hal throughput dan ketebalan pengecoran. . Di pabrik pengecoran yang beroperasi saat ini, panjang pemandu untai telah ditingkatkan dari sekitar 6,0 m menjadi 9,7 m (Gbr 5). Pengembangan ini dilaksanakan dengan tetap mempertahankan konsep vertikal dengan segala keunggulan terkait peralatan dan metalurgi. Langkah yang menentukan adalah pengembangan cetakan lebih lanjut dari desain rangka-U ke cetakan rangka-ganda atau rangka-O. Cetakan inovatif ini diamankan di tengahnya, sementara pada saat yang sama, secara nyata meningkatkan stabilitas seluruh struktur. Rangka memiliki jendela lateral untuk mengakomodasi kuk jika dan saat rem elektromagnetik (EMBR) digunakan.
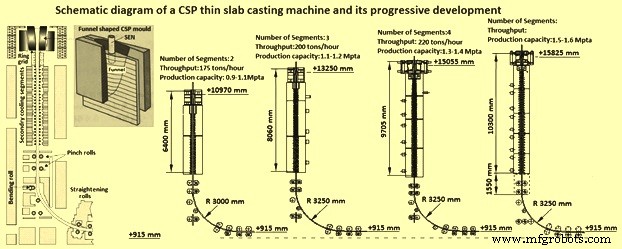
Gbr 5 Diagram skema mesin pengecoran pelat tipis CSP dan perkembangan progresifnya
Loop kontrol teknologi kastor CSP diperpanjang secara sistematis dengan tujuan untuk mencapai keandalan operasional maksimum dan kualitas produk yang optimal. Hal ini terutama berkaitan dengan kontrol level cetakan, osilator cetakan hidraulik, reduksi inti cair (LCR), dan pengukuran kerapatan fluks panas dalam cetakan dan deteksi dini breakout, serta kontrol dinamis pemadatan akhir untuk tujuan memastikan tinggi suhu masuk slab ke dalam tungku terowongan. Penghubung langsung antara pengecoran dan penggulungan menciptakan potensi tambahan sehubungan dengan kapasitas keluaran dan dimensi akhir. LCR memungkinkan ketebalan pelat yang optimal diatur untuk mencapai dimensi batas, kapasitas throughput maksimum, atau tingkat pembentukan yang diperlukan saat pengecoran sedang berlangsung.
Perkembangan rolling mill CSP telah berkembang untuk memenuhi permintaan pasar. Solusi terbaik untuk memenuhi berbagai persyaratan dan termasuk berbagai produk jadi adalah tata letak rolling mill kompak yang menampilkan enam atau tujuh stand tergantung pada bauran produk. Untuk mendapatkan ketebalan strip jadi minimum hingga 0,8 mm, ketebalan entri pelat yang berbeda digunakan dan diameter gulungan kerja dan bahan gulungan dioptimalkan sedemikian rupa sehingga dua atau tiga diameter gulungan yang berbeda digunakan. Teknologi CVC (continuously variable crown), yang telah terbukti berhasil di pabrik hot-rolling konvensional, telah lebih ditingkatkan dengan pengembangan pabrik finishing CSP. Hasilnya adalah apa yang disebut proses 'CVC Plus', yang menampilkan rentang penyesuaian yang jauh lebih luas untuk kontrol profil hingga 190% dari rentang pengaturan CVC.
Penggunaan sistem pendinginan antar dudukan yang lebih efisien memungkinkan penggulungan feritik baja karbon ultra rendah serta penggulungan termo-mekanis baja HSLA. Geser terbang yang dipasang di depan rotor coiler dan/atau dua down-coiler menawarkan kemungkinan penggulungan strip tipis semi-berujung. Sistem pendinginan cepat di hilir stand terakhir atau di bagian belakang jalur pendinginan, menawarkan fleksibilitas yang lebih besar dalam menerapkan kurva suhu-waktu untuk mencapai sifat strip tertentu dan untuk memproses baja multi-fase.
Kemampuan untuk menggulung hingga ketebalan akhir kurang dari 1,5 mm adalah fitur khusus dari proses CSP, dan paket teknologi telah dikembangkan secara khusus untuk ini, namun, tergantung pada ketebalan yang masuk, evolusi suhu, distribusi reduksi dan kecepatan rolling, minimum ketebalan akhir hingga 0,8 mm dapat dicapai pada suhu penggulungan akhir austenitik.
Dibandingkan dengan produksi hot-strip konvensional, ketebalan yang dapat dicapai hingga 50% lebih tipis tergantung pada grade baja yang digunakan. Hal ini, pada gilirannya, meningkatkan persyaratan di pabrik penggilingan CSP, terutama dalam hal kekuatan dan permintaan energi, keausan gulungan terutama di tribun akhir, dan kerataan strip. Pelumasan celah gulungan diadopsi untuk meminimalkan keausan, pengurangan gaya dan torsi pemisah gulungan, serta untuk meningkatkan permukaan strip. Untuk pengukuran dan kontrol kerataan, looper tersegmentasi dipasang di beberapa pabrik yang mendeteksi, tidak hanya tegangan antar-dudukan, tetapi juga distribusi tegangan strip di atas lebar, dan yang mengaktifkan fungsi pembengkokan rol kerja untuk tujuan kontrol kerataan.
Meskipun langkah-langkah ini, bagaimanapun, untuk strip yang sangat tipis, sulit untuk mencapai kerataan strip yang tinggi setelah strip menjadi dingin. Strip, meskipun masih rata di atas meja roller run out karena berada di bawah tegangan, dapat menunjukkan tepi bergelombang selama uncoiling nanti. Penutupan tepi, dikembangkan untuk menjaga kerataan strip yang didinginkan. Pelat pemandu yang dapat disesuaikan di bawah kelompok pendingin aliran laminar menjauhkan air dari tepi strip dan memungkinkan kerataan ditingkatkan dari 250 I-unit menjadi 25 I-unit (I-Unit adalah pengukuran kerataan kuantitatif yang tepat. Ini adalah angka tanpa dimensi yang menggabungkan tinggi dan panjang puncak ke puncak gelombang berulang).
Loop kontrol yang dipasang di seluruh rolling mill CSP terus diperbarui ke status teknologi aktual. Mereka melayani tidak hanya untuk menentukan strategi rolling, untuk menghitung jadwal lulus dan untuk preset rolling mill, tetapi terutama untuk mencapai parameter produk jadi yang diperlukan seperti profil, kontur dan kerataan, untuk memantau aliran massa, untuk mengontrol pabrik sehingga untuk mencapai ketebalan akhir yang diminta, dan untuk memastikan toleransi minimum dari parameter ini. Sifat mekanik dari strip jadi secara signifikan dipengaruhi oleh suhu penggulungan dan penggulungan akhir serta strategi pendinginan. Model proses fisik yang sesuai telah dikembangkan dan disesuaikan dengan kebutuhan produk yang terus meningkat.
Hot-rolled strip yang diproduksi dengan teknologi CSP, terutama strip dengan ketebalan yang lebih rendah hingga 0,8 mm, telah mulai mempengaruhi desain tahap proses teknologi hilir seperti pengawetan dan galvanisasi. Contoh tipikal dari konfigurasi instalasi gabungan adalah jalur hot-strip pickling dan galvanizing yang mulai beroperasi di Wuppermann di Belanda pada tahun 2000, yang membuat pickling dan galvanizes hot strip dalam kisaran ketebalan 0,8 mm hingga 3,0 mm. Dimungkinkan juga untuk mengintegrasikan satu atau dua cold rolling stand ke dalam jalur pemrosesan jenis ini.
Proses Produksi Strip Sebaris
Proses In-line Strip Production (ISP) menghasilkan gulungan canai panas hingga pengukur jadi 1 mm. Salah satu karakteristik yang paling mencolok dari proses ISP adalah kekompakan pabrik secara keseluruhan. Dengan panjang garis hanya 180 m dari baja cair ke gulungan canai panas, umumnya diakui sebagai garis strip terpendek di dunia. Karakteristik ini merupakan hasil dari tiga fitur proses ISP yang signifikan yaitu (i) pengecoran kontinu dengan reduksi inti cair selama pemadatan pelat, (ii) hubungan langsung antara pengecoran baja dan penggulungan pelat awal, dan (iii) penggunaan gabungan pemanas induksi kompak dengan dua tungku kotak koil, bukan tungku terowongan panjang di sisi masuk pabrik penggilingan panas.
Baja cair dicetak dalam cetakan multi-lentur dengan osilasi servo-hidraulik dan ketebalan keluar 70 mm. Pelat mengalami reduksi lunak saat bergerak menuruni radius 5,2 m, muncul dengan kecepatan 5,5 m/menit dan pada ketebalan maksimum 55 mm. Nosel tundish dirancang untuk memastikan pertumbuhan cangkang yang homogen dan casting urutan yang panjang.
Segera setelah meninggalkan kastor, slab memasuki pabrik roughing 3 stand untuk direduksi menjadi batang transfer setebal 10 mm hingga 18 mm, yang kemudian dipotong menurut panjangnya dengan geser pendulum transversal. Pengurangan inti cair memungkinkan produksi pelat baja homogen dengan kebersihan tinggi, hampir bebas dari segregasi dan dengan penyempurnaan butir yang baik untuk memberikan karakteristik mekanis yang lebih baik pada baja jadi. Selain itu, kombinasi reduksi inti cair dengan masuknya pelat secara langsung ke dalam roughing mill memberikan keuntungan penghematan energi dibandingkan dengan rangkaian penggulungan terputus konvensional.
Setelah melewati tungku pemanas induksi untuk menaikkan suhu baja sebesar 150 derajat C menjadi 250 derajat C, batang transfer mencapai 'Tungku Cremona'. Unit ini terdiri dari dua coiler yang ditempatkan di ruang terisolasi, atau kotak, dan sementara satu coiler menerima dan melingkari batang transfer yang datang dari tungku induksi, yang lain mendekoiling batang transfer sebelumnya untuk memberi makan pabrik hot-rolling.
Meskipun tungku Cremona berbahan bakar gas memisahkan tahap pengecoran dan pengasaran dari pabrik finishing, ini adalah penyangga dinamis yang menahan baja sejajar dan menyeragamkan profil suhu yang siap untuk pengerolan panas, dan karenanya dalam mencapai produktivitas tinggi dan efisiensi. Tepi hot-strip yang dihasilkan memperpanjang kampanye roll kerja di penggilingan akhir hingga 150 km.
Baja dihilangkan kerak pada tekanan tinggi sebelum memasuki hot mill 5 dudukan yang dilengkapi dengan pemindahan dan pembengkokan rol kerja ditambah kontrol pengukur otomatis pada semua 4 dudukan tinggi. Pengukur masuk pabrik berukuran 20 mm atau kurang memungkinkan Arvedi menghasilkan strip canai panas hingga 1 mm dalam satu lintasan dengan profil tinggi dan presisi pengukur, tingkat mahkota 1% hingga 3%, kekasaran permukaan rendah dan deformabilitas dingin yang baik.
Pada pengukur yang lebih rendah ini, deviasi panjang melintasi strip di bawah atau sama dengan satu unit 'I'. Akhirnya, strip yang digulung melewati meja pendingin aliran air laminar sebelum digulung ke bawah. Kontrol proses dan otomatisasi tingkat tinggi merupakan fitur integral dari seluruh pabrik. Emisi asap knalpot adalah 1,0 mg / N cum, dan resirkulasi air total di lokasi menghindari pembuangan cairan.
Toleransi dimensi strip canai panas sebanding dengan produk canai dingin, dengan kumparan pengukur 1 mm hingga 1,2 mm menunjukkan nilai transversal datar bila diukur 25 mm dari tepi strip. Proses ini ditunjukkan secara skematis pada Gambar 6.
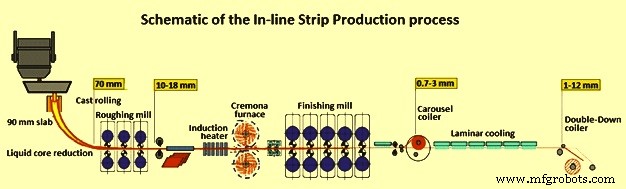
Gbr 6 Skema Proses Produksi In-line Strip
Teknologi pengecoran dan penggulungan pelat tipis dari Danieli
Proses generasi pertama atau thin slab casting and rolling dari Danieli terdiri dari unit flexible thin slab casting (fTSC) yang dihubungkan dengan thin slab rolling unit (fTSR) melalui tunnel furnace. Unit fTSC mampu mencetak pelat dengan ketebalan 60 mm. Kastor memiliki desain melengkung vertikal, memiliki cetakan corong dengan reduksi lembut dan pendinginan kabut udara. Rolling mill terdiri dari finishing mill dengan 6 sampai 7 rolling stand dalam konfigurasi cluster. Proses ini ditunjukkan secara skematis pada Gambar 7.
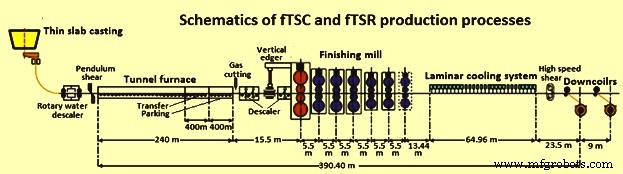
Gbr 7 Skema proses fTSC dan fTSR
Melalui pengembangan proses berkelanjutan, Danieli mengembangkan dua konsep tata letak yang berbeda dan di bawah konsep ini, pengecoran pelat tipis dan proses penggulungan dinamakan sebagai 'Produksi Jalur Kualitas (QSP), dan 'Produksi Jalur Kualitas Tanpa Akhir (QSP-E) (Gbr 8).
Di QSP, pabrik dengan satu atau dua untai tuang dihubungkan ke pabrik penggilingan melalui tungku terowongan panjang, yang memiliki fungsi untuk memanaskan kembali dan menyamakan suhu pelat serta menjamin waktu penyangga yang cukup jika terjadi penghentian yang dijadwalkan. pabrik (misalnya, perubahan gulungan pekerjaan) atau gangguan aliran material yang tidak terjadwal. Dalam beberapa tahun terakhir, berkat peningkatan progresif dalam aliran massa karena peningkatan kecepatan pengecoran yang diwarisi dari generasi terakhir kastor pelat tipis yang beroperasi pada kecepatan sangat tinggi, dan dikombinasikan dengan pengenalan teknologi pemanas induksi yang andal sebagai pengganti tungku terowongan , dimungkinkan untuk mengembangkan konfigurasi QSP-E. Konfigurasi ini menghasilkan pabrik yang sangat kompak yang secara khusus didedikasikan untuk produksi pengukur ultra-tipis. Hal ini dimungkinkan berkat penerapan proses rolling tanpa akhir (yaitu, koneksi langsung dan tidak terputus antara casting dan rolling), untuk mengatasi masalah threading strip yang terkenal saat memproduksi pengukur tipis dalam mode coil-to-coil.
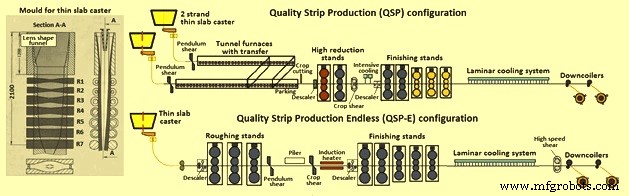
Gambar 8 proses QSP dan QSP-E
Pabrik QSP dapat dioperasikan dengan 2 untai tuang yang memungkinkan untuk secara drastis memperluas campuran nilai baja pelat tipis dan untuk meningkatkan produktivitas pabrik jauh lebih dari 3 Mpta. Pabrik ini awalnya dirancang untuk aplikasi penggulungan kumparan ke kumparan dan kemudian untuk proses semi-berakhir untuk menggulung pengukur yang lebih tipis di bawah 1 mm. Konsep QSP-E memungkinkan untuk mengoptimalkan produksi pengukur ultra-tipis dalam mode tanpa akhir, tetapi menunjukkan sedikit fleksibilitas dalam produksi grade yang lebih canggih karena hubungan yang kaku antara casting dan rolling.
Dalam kasus penggulungan tak berujung, kastor sebenarnya dipaksa untuk selalu berjalan pada kecepatan pengecoran yang sangat tinggi dan ini tidak mungkin untuk semua nilai baja karena alasan metalurgi. Selain itu, proses tanpa akhir telah terbukti kompetitif secara ekonomi hanya untuk produksi kumparan yang memiliki ketebalan strip di bawah 1,5 mm, tetapi segera setelah ketebalan strip ditingkatkan, daya yang dibutuhkan oleh pemanas induksi untuk terus beroperasi menjadi sangat tinggi, sehingga ekonomis diperlukan untuk kembali ke mode kumparan-ke-kumparan.
Dalam upaya terus menerus untuk meningkatkan proses dan teknologi yang ada dan mengatasi keterbatasan mereka saat ini, Danieli telah mengembangkan konsep baru di pabrik TSCR. Konsep ini disebut Danieli Universal Endless (DUE). Konsep DUE mampu menyatukan dalam satu lini produksi semua fitur unggulan yang hingga kini telah dikembangkan dengan menggunakan pendekatan yang berbeda, sekaligus menghilangkan faktor pembatas dari masing-masing fitur tersebut.
Fitur tata letak DUE (i) produktivitas tinggi karena kombinasi ketebalan dan kecepatan pelat yang belum pernah terjadi sebelumnya, (ii) fleksibilitas produksi yang tinggi, mampu beroperasi dalam mode rolling coil-to-coil, semi-endless dan endless, (iii) operasional tinggi fleksibilitas, karena adanya tungku terowongan dan waktu penyangga yang relevan, (iv) mencakup spektrum penuh kadar baja yang diproduksi untuk produk datar, termasuk yang paling canggih yang digulung melalui penggulungan termo-mekanis (nilai pipa API) atau pengontrol suhu rolling (produk multi-fase) serta grade yang memerlukan kecepatan pengecoran sedang seperti peritektik, baja listrik dan grade karbon tinggi, sensitif terhadap retak, dan (v) mencakup spektrum penuh dimensi strip geometris, mulai dari 0,8 mm ultra -pengukur tipis, diproduksi dalam mode tanpa akhir, hingga setebal 25 mm. Ini, tentu saja, dikombinasikan dengan biaya transformasi yang tidak ada duanya, lebih rendah daripada proses lain yang tersedia saat ini.
Teknologi KONROLL
Proses CONROLL menghasilkan slab setebal 70 mm sampai 80 mm melalui cetakan lurus dengan sisi sejajar tetapi tidak melakukan pengurangan ketebalan strand. Kecepatan pengecoran tinggi dalam kisaran 2 m/mnt hingga 4 m/mnt dan lebar 800 mm hingga 1600 mm dimungkinkan. Kastor terhubung ke rolling mill melalui tungku pemanas ulang tungku rol yang menyetarakan suhu slab ke 1120 derajat C. Rolling mill dapat mencakup empat, lima, atau enam dudukan finishing tergantung pada campuran produk dan pengukur finishing yang diperlukan. Rolling mill terdiri dari mekanisme geser hidrolik, descaler air bertekanan tinggi, sistem pendingin strip laminar, dan downcoiler. Ketebalan strip akhir berkisar antara 1,8 mm hingga 20 mm.
Teknologi CONROLL dipasang pada April 1995 di Armco's Mansfield. Armco mengadopsi teknologi ini karena dirancang khusus untuk stainless steel. Nilai baja yang diproduksi meliputi baja karbon, baja tahan karat dengan mutu 400 seri 409 dan 430, sebagian kecil dari mutu paduan rendah kekuatan tinggi (HSLA), mutu baja paduan tinggi, dan baja silikon.
Teknologi TSP
Tippins Incorporated dari USA bekerja sama dengan pembuat kastor Samsung Heavy Industries dari Korea Selatan untuk mengembangkan teknologi TSP. Teknologi ini cocok untuk baja dengan kadar karbon rendah hingga karbon tinggi, baja tahan karat, baja HSLA, baja silikon, nilai baja API, dan baja berkualitas gambar. Salah satu kekuatan pabrik adalah keserbagunaannya. Ini dapat menghasilkan pelat koil atau diskrit yang memungkinkan berbagai lebar dan pengukur untuk diproduksi. Pengecoran pelat ketebalan menengah memiliki beberapa keunggulan. Pelat cukup tipis untuk menghilangkan kebutuhan akan penggilingan kasar yang terpisah dan cukup tebal untuk mempertahankan kualitas yang baik. Ketebalan menengah memungkinkan lebar pelat yang lebih besar, waktu pemanasan ulang yang lebih singkat, dan karenanya mengurangi pembentukan kerak dibandingkan dengan pelat tipis 50 mm.
Setelah pengecoran, slab dikirim langsung ke tungku pemanas ulang untuk menyamakan slab ke suhu rolling yang benar. Waktu penahanan tipikal untuk memanaskan pelat hingga 1250 derajat C adalah 12 menit hingga 13 menit. Setelah strip telah dikurangi menjadi 20 mm sampai 25 mm ketebalan, itu digulung ke dalam tungku melingkar untuk mempertahankan suhu strip. Strip kemudian dibalik bolak-balik melalui rolling mill. Total tiga lintasan roughing datar dan enam lintasan penyelesaian melingkar umumnya diperlukan untuk menyelesaikan pengukur hingga ketebalan 1,5 mm.