Total Productive Maintenance:Hubungan Antara Anda dan Jepang tahun 70-an
Apa yang harus diajarkan oleh manufaktur mobil Jepang pada tahun 1970-an kepada Anda tentang menjalankan departemen pemeliharaan hari ini? Bisa jadi banyak. Total Productive Maintenance (TPM) hanyalah tiga huruf pendek, tetapi ada banyak hal yang harus dilihat dan dipertimbangkan.
Latar belakang cepat
Antara tahun 1950 dan 1970, perusahaan Jepang menginvestasikan banyak waktu dan perhatian untuk menyempurnakan manufaktur. Mereka menemukan kuncinya adalah memberdayakan kelompok kecil karyawan garis depan dalam proyek perbaikan. Pada tahun 1971, Seiichi Nakajima meresmikan ini dan wawasan lainnya tentang Pemeliharaan Produktif Total. Kontribusi Jepang yang paling terkenal untuk praktik manufaktur, JIT (manufaktur tepat waktu), berasal dari dan bergantung pada prinsip dan praktik TPM.
Total Productive Maintenance saat ini dapat dipecah menjadi dua bagian, pertama fondasi 5S dan kemudian delapan pilar. Ada baiknya melalui setiap bagian untuk mendapatkan gambaran tentang bagaimana sistem bekerja secara keseluruhan. Sasaran TPM sangat cocok dengan beberapa tujuan utama setiap departemen pemeliharaan:
- lebih sedikit waktu henti
- lebih banyak waktu aktif
- lebih sedikit stres
- keamanan yang lebih baik
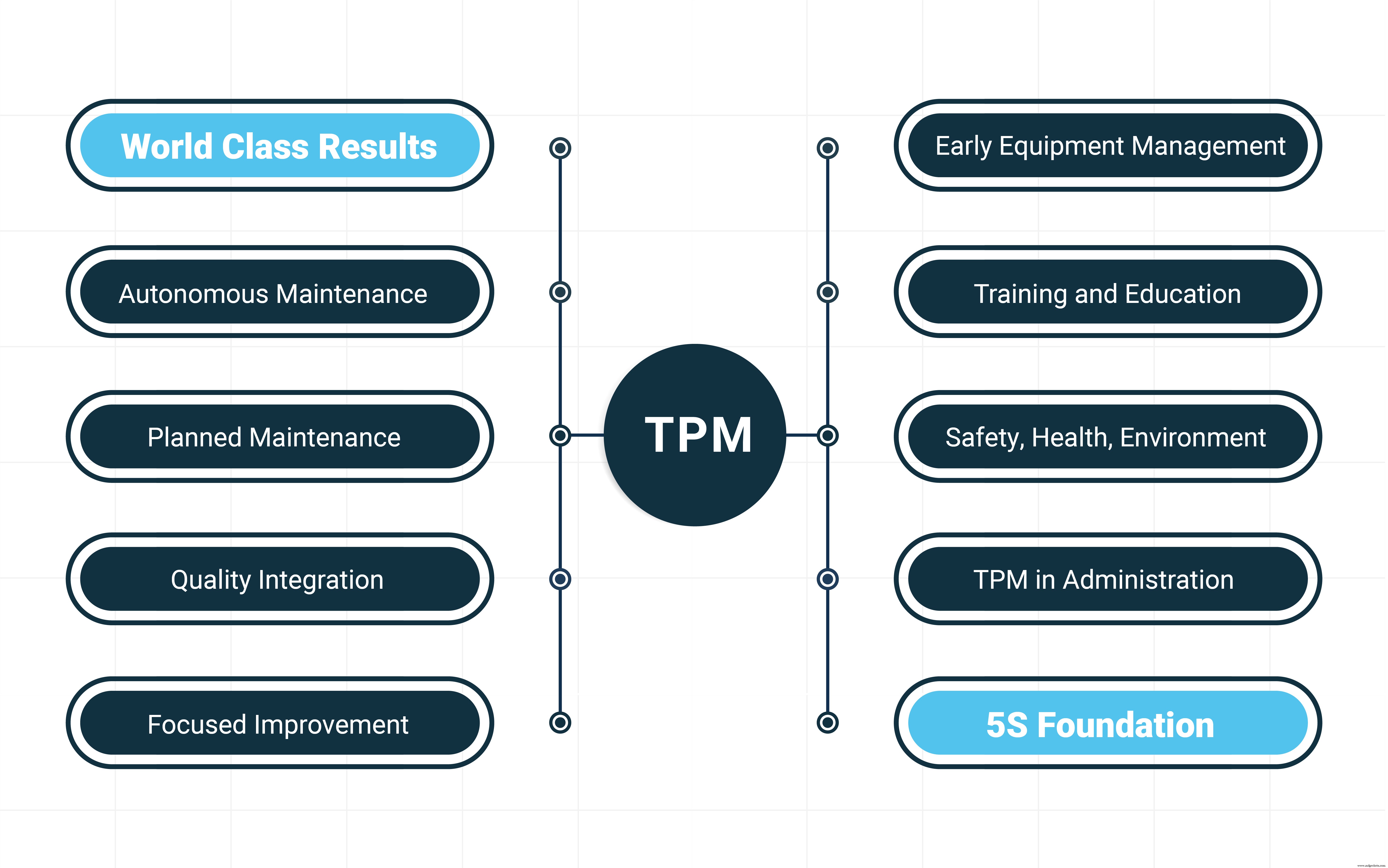
dasar 5S
Meskipun kata aslinya adalah bahasa Jepang dan ada lebih dari satu kemungkinan terjemahan untuk masing-masing kata, kata-kata tersebut cenderung disajikan sebagai:
- Urutkan
- Berurutan
- Bersinar
- Standarisasi
- Bertahan/Disiplin diri
Mari kita lihat masing-masing. Ingatlah bahwa mereka berurutan dan mengacu pada diri sendiri. Anda perlu melakukannya secara berurutan, dan langkah selanjutnya merujuk kembali ke langkah sebelumnya.
Urutkan
Di sini, Anda akan melalui dan pada dasarnya menyortir barang-barang menjadi dua tumpukan, satu hal untuk disimpan di area dan salah satu hal untuk dipindahkan atau dibuang.
Ini membuat semuanya tidak terlalu berantakan, dan kekacauan memperlambat Anda. Saat Anda mencari bagian, Anda dapat menemukannya lebih cepat ketika ada lebih sedikit bagian lain di sekitarnya. Mengapa begitu sulit menemukan jarum di tumpukan jerami? Itu karena semua jerami.
Selain membuat segalanya lebih cepat, itu juga bisa membuat segalanya lebih aman. Jika dasar di sekitar aset bersih, Anda akan melihat kebocoran lebih cepat. Inspeksi visual lebih mudah dan masalah dapat dideteksi lebih cepat saat ada lebih sedikit barang di sekitar, menghalangi pandangan Anda.
Setel dalam urutan
Setelah Anda menyingkirkan semua hal yang tidak Anda butuhkan, Anda perlu mengatur hal-hal yang Anda lakukan. Anda perlu meletakkan alat dan bahan di lokasi yang mendukung alur kerja Anda. Misalnya, letakkan alat di meja kerja sesuai urutan Anda akan menggunakannya. Jika Anda tidak selalu menggunakan alat yang sama dalam urutan yang sama, posisikan alat tersebut agar mudah ditemukan.
Keuntungan besar untuk ini adalah menjadi sangat mudah untuk melihat ketika ada sesuatu yang hilang. Jika semua kunci pas Anda diatur di sepanjang dinding dalam urutan ukuran, Anda akan langsung tahu jika ada yang hilang.
Pada dasarnya, langkah ini adalah tentang “Tempat untuk segala sesuatu, dan segala sesuatu pada tempatnya”.

Bersinar
Sekarang setelah Anda menyiapkan semuanya dengan baik, Anda harus berjuang untuk tetap seperti itu. Langkah bersinar adalah tentang secara teratur meluangkan waktu untuk membersihkan dan memastikan semuanya berada di tempat yang seharusnya. Saat membersihkan, Anda juga harus memeriksa alat dan mesin untuk memastikan semuanya berfungsi dengan baik.
Standarisasi
Di sini Anda akan melangkah lebih jauh untuk memastikan kerja keras Anda tidak hilang seiring waktu dengan membuat kebijakan formal dan jadwal yang ditetapkan untuk tiga langkah pertama. Misalnya, Anda dapat menetapkan kebijakan tentang siapa yang bertanggung jawab untuk area mana dan kemudian menjadwalkan 15 menit terakhir setiap shift untuk "bersinar".
Berkelanjutan/Disiplin diri
Manajemen top-down yang berat cenderung bekerja dengan benar sampai manajer pulang untuk hari itu. Agar sistem 5S benar-benar berfungsi, Anda memerlukan dukungan karyawan. Pada langkah ini, Anda dapat mengatur sesi pelatihan yang membantu pekerja memahami manfaat sistem. Anda juga dapat mengumpulkan masukan karyawan; pekerja akan lebih bersemangat menerapkan sistem yang mereka bantu kembangkan.
Sekarang setelah kita mendapatkan fondasinya, mari kita lihat delapan pilar. Mereka sedikit kurang saling berhubungan daripada 5S. Anda dapat melakukannya tanpa yang lain, dan pada dasarnya Anda dapat melakukannya dalam urutan apa pun.
Delapan pilar Pemeliharaan Produktif Total
Jika TPM adalah atap dan 5S adalah fondasinya, maka bagian-bagian berikutnya dari pilar berdiri di atas fondasi, menopang atap.
Pemeliharaan otomatis
Melihat frasa sekarang, Anda akan berpikir itu tentang kecerdasan buatan di CMMS dan robot berpikir. Tapi ingat, sistem ini diformalkan pada tahun 50-an, dan saat itu mengacu pada praktik operator yang mengambil alih tanggung jawab untuk pembersihan rutin, pemeriksaan, dan pelumasan peralatan mereka. Alih-alih departemen pemeliharaan, operator bertanggung jawab atas semua PM kecil yang terkait dengan peralatan.
Keuntungan besar adalah meningkatkan pengetahuan operator tentang mesin yang mereka kerjakan. Penting untuk diketahui bahwa harapannya bukanlah bahwa mereka akan menjadi ahli. Memikirkannya dalam hal memiliki mobil, mereka akan tahu cara memeriksa oli (tetapi tidak menggantinya) dan menambahkan udara ke ban. Jadi, jika ada yang salah dengan peralatan, mereka akan segera menyadarinya. Juga, karena mereka mampu menangani hal-hal kecil, teknisi departemen pemeliharaan, yang merupakan ahli sebenarnya, menghabiskan waktu mereka yang berharga untuk perbaikan yang lebih penting dan lebih kompleks. Kembali ke analogi mobil, mekanik Anda harus memeriksa segel dan menyetel idle. Jika Anda meminta mereka menyedot debu kursi belakang dan memasukkan udara ke dalam ban, Anda membuang-buang waktu dan bakat mereka. Anda juga membuang-buang uang.
Pemeliharaan terencana
Yang satu ini mudah dijelaskan. Itu hanya pemeliharaan preventif dengan nama lain.
Salah satu manfaatnya adalah Anda dapat merencanakan pemeliharaan preventif di sekitar waktu sibuk. Alih-alih menghentikan jalur di tengah shift pertama dengan kegagalan besar, Anda bisa mendapatkan inspeksi dan penggantian rutin semua diurus antara shift kedua dan ketiga, ketika keadaan relatif lebih tenang.
Lainnya termasuk:
- Mengurangi waktu henti
- Meningkatkan waktu aktif
- Kontrol inventaris lebih mudah
- Lebih sedikit perintah kerja sesuai permintaan
Pemeliharaan kualitas
Sebagian besar dari yang satu ini adalah analisis akar penyebab. Alih-alih hanya memperbaiki masalah, Anda juga mencari tahu apa penyebabnya sehingga Anda dapat menghindarinya di masa mendatang.
Biasanya, Anda akan mendengar orang berbicara tentang 5 Mengapa saat melakukan analisis semacam ini. Penting untuk diingat bahwa tidak ada 5 Whys. Sebaliknya, idenya adalah menanyakan "mengapa" lima kali untuk sampai ke akar masalah. Dan kita perlu menemukan akarnya; jika tidak, kita hanya membuang-buang waktu untuk menelusuri daftar gejala berulang yang tak ada habisnya.
Misalnya, katakanlah masalahnya adalah mobil Anda tidak mau hidup.
Satu:“Mengapa mobil tidak mau hidup?”
Jawaban:Baterai habis.
Dua:“Mengapa baterainya mati?”
Jawaban:Alternator tidak berfungsi.
Tiga:“Mengapa tidak berfungsi?”
Jawaban:Sabuknya putus.
Empat:“Mengapa sabuknya putus?”
Jawaban:Masa manfaatnya sudah lama berlalu.
Lima:“Mengapa sabuk tua masih terpasang di alternator?”
Jawaban:Mobil tidak dirawat sesuai dengan rekomendasi pabrikan.
Apakah selalu lima? Tidak selalu; lima hanyalah aturan praktis yang baik.
Peningkatan terfokus
Sejujurnya, saya tidak yakin mengapa ini disebut peningkatan fokus. Mungkin karena pekerjaan dilakukan oleh sekelompok kecil karyawan. Mungkin dari situlah ide fokus berasal.
Masuk akal untuk menyebutnya "peningkatan luas," meskipun. Tim dapat terdiri dari karyawan dari atas dan ke bawah tangga perusahaan. Dua kata penting lainnya adalah inkremental dan proaktif. Kemajuan tidak terjadi dalam lompatan raksasa. Sebaliknya, perubahan kecil dibuat terus-menerus dilihat dan diuji. Selain itu, tim ingin meningkatkan proses sebelum masalah muncul.
Manajemen peralatan awal
Kapan paling mahal untuk menjalankan mesin? Apakah sudah mendekati akhir masa manfaatnya? Itu masuk akal karena saat itulah kemungkinan besar Anda akan mengalami banyak perbaikan yang mahal.
Tapi itu juga mahal di awal. Ada biaya pemasangan. Lalu ada biaya kerusakan yang disebabkan oleh kesalahan operator. Ingat, mesin baru membutuhkan waktu untuk mencari tahu. Dan juga butuh waktu untuk mencari tahu cara memperbaikinya, jadi pekerjaan apa pun yang dilakukan segera setelah peluncuran akan menjadi agak lambat. Dan waktu adalah uang.
Manajemen peralatan awal mencoba mengatasi biaya ini dengan bekerja sama dengan operator dan departemen pemeliharaan untuk mengembangkan alat berat yang mudah diperbaiki dan ramah pengguna. Sesuatu yang sederhana seperti penempatan panel akses dapat menghemat banyak waktu selama masa pakai aset atau peralatan.
Pendidikan dan Pelatihan TPM Administrasi &Perkantoran
Untuk menghemat waktu dan ruang, mari gabungkan keduanya menjadi satu. Pada dasarnya, ide di sini adalah untuk menyebarkan konsep dan praktik TPM di antara staf frontline dan front-office. Dengan memastikan semua orang mengetahui konsepnya, Anda meningkatkan peluang mereka untuk menerapkannya.
Kondisi lingkungan kesehatan keselamatan
Ini satu lagi yang mudah ditebak hanya dengan melihat namanya. Tim bekerja sama untuk meningkatkan keselamatan dan mengurangi risiko di seluruh fasilitas. Alat berat tidak hanya dibuat lebih aman dengan pelindung dan sakelar pemutus, tetapi juga operator dan teknisi dibuat lebih aman dengan perlindungan pribadi seperti topi keras.
Apa artinya semua ini bagi saya?
Bisa sedikit atau banyak. Meskipun Anda perlu merangkul semua aspek TPM untuk mendapatkan manfaat maksimal, Anda juga dapat melihatnya sebagai restoran prasmanan. Dalam hal perangkat lunak pemeliharaan preventif, ambil apa yang menarik bagi Anda dan jangan khawatir tentang sisanya.
Misalnya, saat berikutnya perusahaan Anda berencana untuk berinvestasi dalam aset atau peralatan baru, Anda dapat memastikan bahwa departemen pemeliharaan memiliki suara dalam proses pemilihan. Atau, sebagai contoh lain, Anda mungkin menerapkan semua atau sebagian dari 5S ke ruangan tempat Anda menyimpan suku cadang. Terserah Anda untuk menemukan dan menerapkan ide-ide yang paling sesuai dengan situasi Anda saat ini.
Anda juga dapat dengan mudah mengadopsi semangat Total Productive Maintenance, yaitu gagasan bahwa kemajuan berkelanjutan adalah mungkin dan kemungkinan besar Anda akan berhasil jika departemen yang berbeda bekerja sama.