Teknologi untuk Peningkatan dalam Proses Sintering
Teknologi untuk Peningkatan Proses Sintering
Proses sintering digunakan untuk mengaglomerasi campuran fine bijih besi, return fine, flux, dan coke wind dengan ukuran partikel kurang dari 10 mm, sehingga sinter yang dihasilkan dengan ukuran tersaring 5 mm sampai 30 mm, dapat menahan tekanan dan kondisi temperatur di dalam blast furnace (BF). Proses sintering butiran halus bijih besi terutama dikembangkan untuk mengubah butiran halus yang dihasilkan di pertambangan dan mengubah butiran halus ini menjadi produk dengan granulometri yang sesuai, kualitas fisik, komposisi kimia, dan sifat mekanik yang cocok untuk pengisian ke dalam BF.
Proses sintering dilakukan pada mesin sinter yang diumpankan dengan beban campuran sinter yang telah disiapkan. Bahan bakar dasar untuk proses sintering bijih besi adalah kokas, yang penggunaannya dapat didukung oleh bahan bakar substitusi (misalnya antrasit). Campuran sinter dibuat dengan homogenisasi dan granulasi campuran mentah (juga disebut campuran sinter) dari bijih halus bijih besi, batu kapur, dolomit, pasir dan butiran halus kuarsit (fluks), bahan bakar padat (angin kokas atau antrasit), dan limbah metalurgi (debu yang terkumpul, lumpur, dan kerak pabrik dll) dalam drum berputar dengan 7% sampai 8% air dengan tujuan memperoleh produk pra-aglomerasi (campuran sinter), yang kemudian dikirim sebagai lapisan di atas jeruji atau untaian yang terus bergerak. mesin sintering.
Proses sintering adalah proses metalurgi yang dilakukan pada mesin sintering. Ini adalah proses aglomerasi termal. Proses sintering adalah proses intensif energi, di mana sejumlah parameter harus diperhitungkan. Prosesnya kompleks dan melibatkan berbagai fenomena fisik dan kimia seperti perpindahan panas, massa, dan momentum yang digabungkan dengan reaksi kimia. Fenomena ini terjadi secara bersamaan yang meningkatkan kompleksitas proses secara signifikan.
Sintering pada dasarnya adalah langkah proses pra-perawatan selama pembuatan besi untuk menghasilkan bahan pengisi yang disebut sinter untuk BF. Aglomerasi dalam proses sintering dicapai melalui pembakaran. Dalam proses ini udara tersedot pada untai sinter melalui lapisan campuran sinter. Partikel bahan bakar pada lapisan permukaan atas pertama-tama dinyalakan dalam tungku dan saat untaian bergerak maju, bagian depan yang tersulut atau pembakaran berjalan secara bertahap ke bawah melalui dasar sampai akhir tercapai.
Selama proses sintering, panas disuplai oleh angin kokas dalam campuran sinter untuk meningkatkan suhu unggun untuk mencapai fusi parsial dan ikatan difusi. Laju aliran udara dan kecepatan depan nyala api dalam proses sintering telah ditemukan untuk memandu kinerja pabrik sinter dan parameter ini terutama tergantung pada permeabilitas sinter bed. Kecepatan depan nyala api adalah salah satu parameter operasi yang penting. Produktivitas sinter sangat bergantung pada permeabilitas campuran sinter dari unggun campuran sinter. Hal ini karena semakin cepat kemajuan reaksi selama sintering, semakin tinggi laju aliran gas yang melewati unggun campuran sinter. Laju aliran gas dikendalikan oleh permeabilitas campuran sinter. Flowsheet proses sintering ditunjukkan pada Gambar 1.
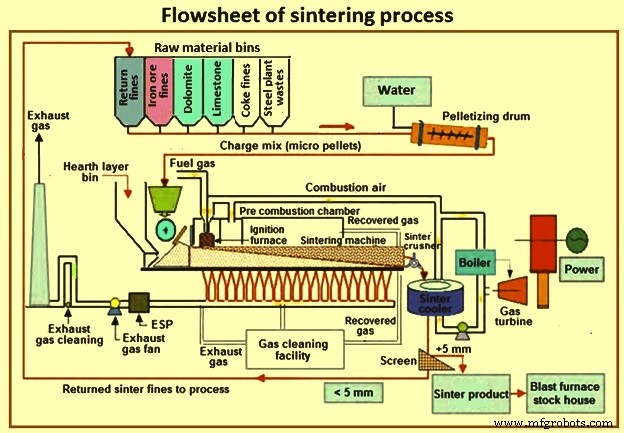
Gbr 1 Flowsheet proses sintering
Tujuan utama keseluruhan dari proses sintering adalah untuk mencapai output tinggi dari kualitas sinter yang seragam dengan biaya operasional yang rendah. Sebagai komponen utama dalam beban BF, produksi sinter berkualitas tinggi yang memiliki granulometri, sifat fisik, komposisi kimia, dan kekuatan mekanik yang tepat sangat penting untuk memastikan produktivitas BF yang tinggi dan stabil dengan konsumsi reduktor yang rendah. BF membutuhkan sinter dengan kekuatan tinggi, RDI rendah (indeks degradasi reduksi), RI tinggi (indeks reduksibilitas), kandungan halus rendah, ukuran sinter terkalibrasi rata-rata yang baik, dan sedikit variasi dalam komposisi kimia agar dapat beroperasi dalam rezim keadaan tunak. Kontrol kualitas sinter, melalui sintering yang memadai, penting untuk mengoperasikan BF pada laju bahan bakar yang rendah dan rezim operasi yang stabil. Dalam beberapa dekade terakhir. beberapa teknologi telah dikembangkan yang tidak hanya menghasilkan peningkatan besar dalam proses sintering tetapi juga telah meningkatkan kualitas sinter. Jurusan teknologi ini dijelaskan di bawah ini.
Penggunaan kapur kalsinasi sebagai pengganti batu kapur
Dalam campuran sinter, batu kapur dan dolomit ditambahkan sebagai fluks dasar. Oksida fluks dalam sinter diperlukan untuk memodifikasi kimia terak BF sedemikian rupa sehingga memiliki karakteristik yang diinginkan. Fluks dasar yang ditambahkan ke campuran sinter bertindak sebagai pengikat dalam campuran sinter dan meningkatkan aglomerasi partikel halus. Fluks meningkatkan produktivitas mesin sinter dan mengurangi konsumsi bahan bakar padat spesifik. Distribusi ukuran fluks penting untuk produktivitas sintering. CaO bergabung dengan oksida besi untuk membentuk senyawa dengan titik leleh rendah yang mendukung pembentukan lelehan primer, tingkat minimum yang diperlukan untuk menghasilkan sinter yang kuat. Senyawa tersebut adalah Fe2O3·CaO (1.205 derajat C) dan FeO·CaO (1.120 derajat C).
Kapur terkalsinasi (CaO) merupakan bahan pengikat aktif karena terhidrasi menjadi {Ca(OH)2} sebagai hasil reaksi hidrat dengan air. Sebagai pengikat, ini mempromosikan properti partikel kuasi dalam campuran sinter. Ini membantu dalam meningkatkan masukan butiran halus melalui butiran bijih besi. Karena granulasi campuran sinter yang lebih baik, ini meningkatkan produktivitas sinter. Selain sifat mengikat, kapur yang dikalsinasi juga mengurangi laju angin kokas karena berkurangnya kalsinasi batu kapur selama proses sintering. Penggunaan kapur yang dikalsinasi juga mengurangi beban penghancuran dan penyaringan batu kapur mentah yang lebih keras dan karenanya menghemat energi.
Nilai kelembaban granulasi yang optimal
Sebuah penelitian telah dilakukan di Jepang untuk menentukan nilai kelembaban granulasi yang optimal dari bahan baku sinter, menguji pengaruh kelembaban tambahan untuk enam jenis bijih yang disesuaikan dengan distribusi ukuran partikel yang sama. Nilai kelembaban optimal untuk mencapai permeabilitas unggun terkemas maksimum telah ditentukan untuk setiap jenis bijih. Dari hasil yang dicapai, metode penentuan nilai kelembaban optimal telah diadopsi, berdasarkan hipotesis bahwa kelembaban tidak mempengaruhi kelembaban optimal untuk bahan campuran, dan rata-rata tertimbang telah ditentukan untuk kelembaban optimal untuk proporsi campuran masing-masing. jenis bijih dan bahan pembantu. Penerapan kelembaban yang optimal memungkinkan nilai tambah kelembaban berkurang dibandingkan dengan metode konvensional. Permeabilitas lapisan terkemas di pabrik sinter meningkat dan produktivitas meningkat 11 ton per jam.
Sistem pencampuran dan granulasi intensif
Bahan baku sintering yang mengandung butiran halus bijih besi, fluxing agent dan bahan limbah berasal dari sumber yang berbeda dan memiliki karakteristik yang berbeda-beda. Mereka perlu dicampur untuk membentuk campuran yang homogen. Produktivitas sinter berhubungan langsung dengan permeabilitas unggun. Pada gilirannya, permeabilitas berhubungan dengan distribusi ukuran granul dan ukuran granul rata-rata, yang bergantung pada penambahan air. Permeabilitas naik ke nilai maksimum sebagai fungsi dari kelembapan.
Sistem pencampuran dan granulasi yang intensif memungkinkan persiapan campuran sinter yang optimal dengan menghomogenkan umpan bahan baku dan menghilangkan kebutuhan akan tempat pencampuran. Sistem pada dasarnya terdiri dari pengaduk pengaduk berkecepatan tinggi dan drum granulasi. Sistem ini menghasilkan peningkatan laju granulasi, peningkatan permeabilitas unggun, zona pembakaran yang lebih merata dan kontrol titik pembakaran yang optimal. Dengan sistem ini, campuran sinter yang lebih homogen disiapkan yang mengurangi konsumsi angin kokas hingga 5% dan meningkatkan produktivitas sinter hingga 2%. Sistem ini memfasilitasi penggunaan persentase ultra halus yang lebih tinggi dalam campuran sinter.
Di samping sistem pencampuran dan granulasi intensif, tahap granulasi pendahuluan yang terdiri dari pencampur dengan kecepatan pengadukan tinggi diikuti oleh pencampur drum juga digunakan di beberapa pabrik sinter. Sistem granulasi dua tahap ini memungkinkan pengolahan bijih besi halus sekaligus meningkatkan kecepatan nyala api, permeabilitas, dan produktivitas proses.
granulasi selektif
Proses granulasi selektif digunakan untuk memungkinkan sintering bijih besi dengan kandungan alumina tinggi, yang sebaliknya sulit untuk disinter karena reaktivitas rendah dari bahan pembawa alumina dan viskositas lelehan primer yang tinggi. Granulasi selektif terdiri dari penyaringan bijih dan pengiriman fraksi ukuran yang lebih besar yang memiliki kandungan alumina lebih rendah ke sirkuit granulasi konvensional, sedangkan fraksi ukuran yang lebih kecil dengan kandungan alumina yang lebih tinggi dipelet menjadi butiran 2 mm hingga 5 mm yang digabungkan dalam sirkuit granulasi konvensional . Fraksi ukuran yang lebih kecil mengandung bijih lempung yang tinggi alumina dan membutuhkan suhu leleh yang lebih tinggi.
Studi skala laboratorium, yang telah dilakukan dengan menggunakan bijih besi dengan kandungan 0,2% Al2O3 hingga 3,2% Al2O3 untuk mempelajari pembentukan lelehan primer yang dihasilkan dari reaksi butiran bijih dengan batu kapur, telah menunjukkan bahwa granulasi selektif mencapai inti granul dengan kandungan alumina yang lebih tinggi daripada granulasi konvensional. Dengan proses ini, butiran halus telah melekat pada inti, dengan kandungan alumina yang lebih rendah, dengan bereaksi dengan batu kapur dan mendorong pembentukan lelehan primer pada suhu yang lebih rendah. Gambar 2 menunjukkan aliran proses khas dari proses granulasi selektif.
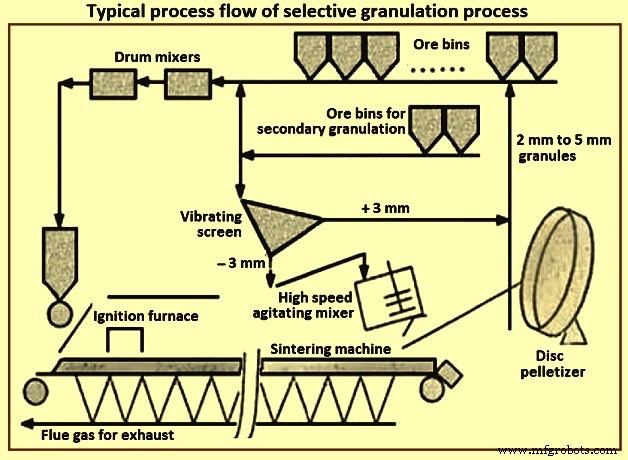
Gbr 2 Alur proses khas dari proses granulasi selektif
Pelapisan granulasi
Hal ini menguntungkan untuk meningkatkan proses granulasi konvensional, terutama bila menggunakan bijih goetit dan limonit yang biasanya memiliki kandungan Al2O3 lebih tinggi daripada hematit dan menyebabkan penurunan sifat sinter. Dalam hal ini, penelitian telah menunjukkan bahwa sintering meningkat ketika tahap granulasi konvensional dalam mixer drum diikuti oleh tahap kedua. Pada tahap pertama campuran bijih besi dan kembalian halus ditempatkan di dalam drum. Pada tahap kedua, coke ditambah batu kapur plus dolomit ditambahkan ke dalam campuran yang dihasilkan dari tahap pertama dan butiran yang diperoleh dibentuk oleh inti yang sebagian besar terdiri dari bijih besi yang dikelilingi oleh kokas dan fluks.
Proses granulasi pelapisan meningkatkan reaksi pembentukan fluks karena pemisahan CaO dari batugamping pada Fe(besi) dari bijih besi. Hal ini membuat sintering berlangsung pada suhu yang lebih rendah, meningkatkan permeabilitas dan produktivitas, dan mengurangi pembentukan hematit sekunder, dengan peningkatan konsekuen dalam RDI. TI (indeks tumbler) dan reducibility juga meningkat, karena pembentukan lebih banyak pori-pori mikro, yang juga mencegah penyebaran retakan yang menyebabkan kerusakan RDI.
Waktu pencampuran dalam drum pada tahap kedua sangat penting, dan sekitar 50 detik telah ditetapkan sebagai waktu optimal. Waktu yang lebih singkat tidak memungkinkan nukleus terlapisi dengan baik dengan kokas plus fluks. Waktu yang lebih lama menyebabkan penghancuran partikel kuasi, karena masuknya kokas dan fluks dalam butiran (inti), dan menghasilkan partikel kuasi yang serupa dengan yang diperoleh dalam granulasi konvensional satu tahap.
Pengembalian halus – proses sintering bijih besi penyematan mosaik
Untuk meningkatkan permeabilitas unggun sintering untuk produktivitas bijih sinter, proses 'return fine - mosaik embedding bijih besi sintering' (RF-MEBIOS) telah dikembangkan. Proses RF-MEBIOS, yang merupakan teknik pengembalian halus melewati granulasi. Dalam proses ini kembali halus seperti partikel kering ditambahkan ke bahan baku granulasi dan kemudian dibebankan ke dalam mesin sintering yang mengakibatkan peningkatan produktivitas mesin sintering.
Peningkatan produktivitas disebabkan oleh peningkatan ukuran partikel semu pada granulasi dan penurunan densitas bulk sinterpacked bed setelah pengisian. Yang pertama dicapai dengan kadar air yang lebih tinggi dalam bahan baku pada granulasi. Yang terakhir ini dicapai dengan gesekan yang lebih tinggi di unggun sintering yang terdiri dari senyawa partikel kering dan basah, yang memiliki peran menurunkan kerapatan curah. Dengan meningkatkan rasio halus pengembalian by-pass dan ukuran, kecepatan sintering dan produktivitas sinter meningkat.
Gambar 3 menunjukkan aliran material khas di pabrik sinter. Transportasi denda pengembalian menyimpang menjadi dua rute dengan peredam divergensi. Salah satunya adalah ke tempat sampah pengembalian yang ada dan yang lainnya ke tempat sampah pengembalian by-pass yang baru. Denda pengembalian dari bak halus pengembalian yang ada dan bahan baku sinter lainnya dicampur dan digranulasi bersama dengan air di dalam mixer. Denda pengembalian dari nampan pengembalian by-pass ditambahkan setelah mixer. Bagian yang diberikan di sisi kanan Gambar 3 menunjukkan hubungan posisi antara peredam dan konveyor sabuk. Posisi peredam disesuaikan untuk mengontrol rasio denda pengembalian by-pass. Peredam dapat memisahkan denda pengembalian antara lapisan atas (denda pengembalian by-pass) dan lapisan bawah (denda pengembalian granulasi). Konveyor sabuk melepaskan partikel jalur sebagai lapisan atas, sehingga partikel yang relatif besar diangkut ke bak halus pengembalian by-pass.
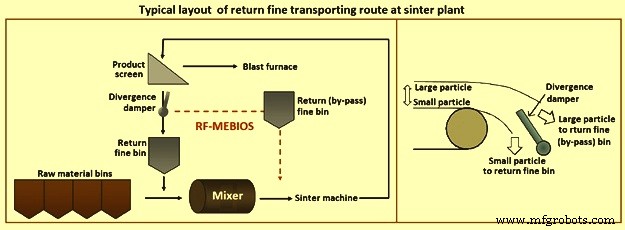
Gbr 3 Tata letak tipikal rute pengangkutan halus kembali di pabrik sinter
Permeabilitas ditingkatkan oleh dua faktor yaitu (i) rasio ukuran partikel semu yang rendah (minus 0,25 mm) dan (ii) kerapatan curah yang rendah. Yang pertama disebabkan oleh granulasi dengan kadar air tinggi karena penambahan butiran halus kembali kering setelah granulasi ketika kadar air saat pengisian konstan.
Pengisian dua lapisan
Dengan pengisian campuran sinter yang seragam pada untai sinter dapat menyebabkan suhu yang lebih tinggi menyebabkan peleburan campuran sinter. Ini membatasi aliran udara downdraft dan proses sintering. Dalam pengisian lapisan kembar, bahan muatan ukuran butir yang lebih kecil dengan konsentrasi angin kokas yang lebih tinggi dibebankan di lapisan atas. Bahan ukuran butir yang lebih besar (pengembalian bijih dan sinter) dengan konsentrasi angin kokas yang lebih rendah dibebankan di lapisan bawah. Ini memastikan aliran panas yang tepat di lapisan bawah, permeabilitas lapisan yang tinggi, dan penggunaan bahan bakar yang efisien.
Peningkatan peralatan makan campuran sinter
Pemuatan campuran terpisah hasil campuran sinter menjadi partikel besar di bagian bawah campuran sinter pada pelet sedangkan partikel kecil di bagian atas campuran sinter pada palet untai mesin sinter. Pemuatan campuran terpisah membantu dalam permeabilitas campuran dan karenanya membantu dalam meningkatkan produktivitas alat berat. Ada beberapa desain sistem pengisian untuk pemuatan terpisah. Beberapa di antaranya adalah (i) pemasangan saringan tambahan pada saluran miring konvensional, (ii) pengumpan pengayakan intensif, (iii) kawat celah segregated, dan (iv) pengumpan pemutus magnet. Gambar 4 menunjukkan sistem pengisian tanpa sistem pemuatan campuran terpisah serta sistem pengisian dengan berbagai jenis sistem pemuatan campuran sinter.
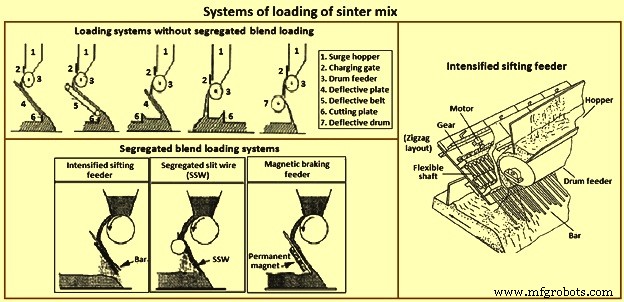
Gbr 4 Sistem pemuatan campuran sinter
Pembakar multi celah di Tungku Pengapian
Saat menyalakan bagian atas sinter mix bed pada mesin sinter di tungku pengapian, stabilitas api burner sangat penting. Pembakar multi celah membantu menghasilkan nyala api tunggal yang lebar dan stabil yang tidak menghilangkan area nyala api dan memasok masukan panas minimum untuk penyalaan. Hal ini pada gilirannya menghasilkan penghematan input energi di kap pengapian. Telah dilaporkan di pabrik Jepang bahwa masukan panas total untuk pengapian dengan pembakar multi celah telah berkurang sekitar 30% bila dibandingkan dengan pembakar konvensional. Garis besar pembakar multi celah ditunjukkan pada Gambar 5.
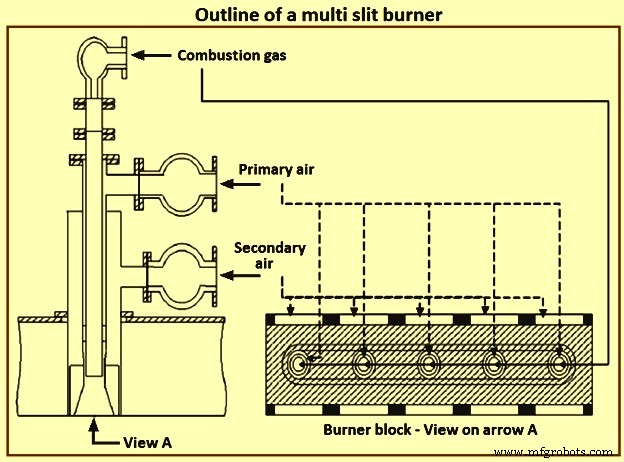
Gbr 5 Garis besar pembakar multi celah
Sintering dukungan berdiri
Teknik sintering baru yang disebut 'stand support sintering', untuk menopang kue sinter dengan dudukan baja (batang atau pelat) yang menempel pada palet telah dikembangkan di Jepang. Teknik ini meningkatkan penyusutan, porositas, dan tingkat reducibility. Karena sistem pendukung berdiri, produktivitas mesin sinter meningkat pesat dan mesin berjalan lebih stabil.
Pada metode stand support sintering, beban sinter cake di bagian atas sinter mix bed ditopang oleh stand baja selama proses sintering. Beban kue sinter pada zona lebur pembakaran di bawahnya membuat unggun campuran sinter menyusut (pemadatan unggun), dan dengan demikian secara signifikan menurunkan permeabilitas unggun. Dudukan penopang yang dipasang di dalam palet sintering mulai menopang beban kue sinter di atas pada saat bagian unggun campuran sinter di sekitar bagian atas dudukan mulai mengeras setelah dipanaskan dan dilebur. Proses sintering dari bagian bawah unggun berlanjut setelahnya di bawah beban yang dikurangi, dan jaringan perembesan berkembang dengan baik di bagian tersebut untuk meningkatkan permeabilitas.
Pemulihan panas limbah
Pemulihan panas di pabrik sinter merupakan sarana untuk meningkatkan efisiensi proses pembuatan sinter. Sinter panas diperlukan untuk didinginkan. Panas yang diperoleh kembali dari pendingin sinter digunakan untuk memanaskan awal udara pembakaran untuk burner di tungku pengapian atau untuk menghasilkan uap bertekanan tinggi yang dapat digunakan untuk pembangkit tenaga listrik. Dalam hal pembangkitan uap bertekanan tinggi, konfigurasi fasilitas sistem pemulihan energi gas buangan terdiri dari kap mesin, penangkap debu, boiler pemulihan panas, kipas sirkulasi, dan de-aerator.
Pabrik sintering terdiri dari dua bagian ukuran yaitu (i) bagian sintering, dan (ii) bagian pendingin sinter panas. Pemulihan panas dari kedua bagian telah dikembangkan dari gas buang bagian sintering dan dari gas pendingin bagian pendingin. Gambar 6 menunjukkan distribusi temperatur gas dari kedua bagian. Seperti yang ditunjukkan pada gambar, ada perbedaan suhu yang besar tergantung pada posisi bagian. Suhu gas rata-rata di kedua bagian berada dalam kisaran 100 derajat C hingga 150 derajat C yang terlalu rendah untuk pemulihan panas yang efektif. Pemulihan panas terbatas pada zona suhu gas tinggi, bagian akhir dari bagian sintering dan bagian awal dari bagian pendinginan, di mana suhu gas 300 derajat C atau lebih tinggi tersedia. Meskipun zona pemulihan panas terbatas, volume gas dari proses sintering cukup besar untuk pemulihan panas praktis yang layak secara komersial. Juga, karena sifat korosifnya, suhu gas setelah pemulihan panas harus dijaga di atas titik asam dari gas.
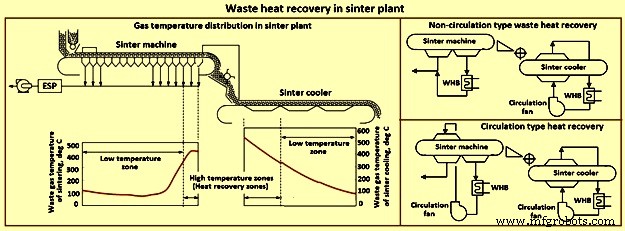
Gbr 6 Pemulihan panas limbah di pabrik sinter
Perolehan panas gas buang mesin sintering dapat dikategorikan menjadi tipe sirkulasi dan tipe non-sirkulasi (Gbr 6). Pada tipe sirkulasi, gas setelah pemulihan panas disirkulasikan ke mesin sintering sebagai pengganti gas pendingin, sedangkan pada tipe nonsirkulasi, gas setelah pemulihan panas dialirkan ke fasilitas pengolahan gas secara langsung. Jenis sirkulasi diadopsi untuk meningkatkan efisiensi pemulihan panas.
Selain pemulihan panas, sistem membantu dalam pengurangan SOx, NOx dan emisi partikulat dan dalam meningkatkan produktivitas, hasil dan kekuatan dingin sinter. Pemulihan energi ke tingkat 30% dicapai dengan metode ini.
Sistem sintering yang dioptimalkan emisi
Tingginya volume gas buang dan rendahnya konsentrasi elemen yang harus dibersihkan selalu menjadi salah satu masalah pabrik sinter. Tujuan mendasar dari sistem sintering yang dioptimalkan emisi (EOS) adalah untuk mengurangi volume gas yang akan dibersihkan (berpotensi mencapai pengurangan hingga 50%) dengan menempatkan tudung di atas jeruji sinter yang diumpankan dengan udara bersih dan daur ulang. udara dari kotak angin. Gambar 7 menunjukkan untai sinter dengan sistem EOS.
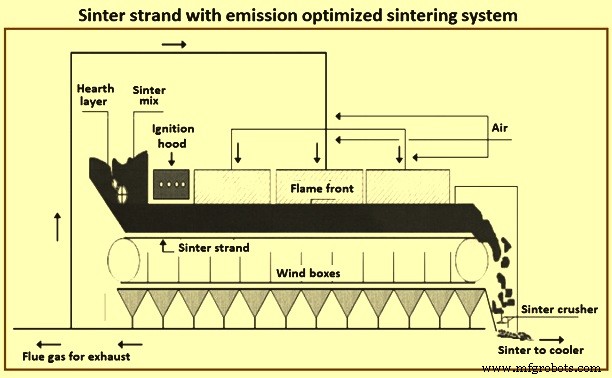
Gambar 7 Untaian sinter dengan sistem sinter yang dioptimalkan emisi
Kontrol emisi debu
Peningkatan produksi pada mesin sinter menyebabkan timbulnya debu yang lebih tinggi yang berarti emisi partikulat yang lebih tinggi. Emisi ini sarat debu dan mengandung berbagai macam polutan udara berbahaya organik dan logam berat (HAP). Dengan mengirimkan gas buang ke presipitator elektrostatik melalui pipa bermuatan negatif, partikel dalam aliran gas limbah menjadi bermuatan negatif. Mengarahkan aliran ini melewati pelat bermuatan positif kemudian menarik dan mengumpulkan partikel bermuatan negatif, sehingga menghasilkan limbah gas bersih dan meningkatkan jumlah pemulihan uap. Debu kasar dihilangkan dalam penangkap debu kering dan didaur ulang. Penggunaan ESP (electro static precipitator) mengurangi tingkat debu off-gas.
Proses PUS
Proses ini dikenal sebagai 'entrained flow absorber (EFA). Ini dikembangkan oleh Paul Wurth. Proses EFA dipasang pada akhir proses sinter plant. Ini pada dasarnya terdiri dari penyerap aliran entrained dan filter tipe kantong. Menggunakan peralatan ini, dari sinter plant off-gas, debu, sulfur oksida, hidroklorik, asam fluorida, dioksin dan furan ditangkap. Penyerap beroperasi dengan kapur terhidrasi (kalsium hidroksida) dan kokas batubara coklat untuk menyerap dioksin dan furan. Kondisi reaksi optimum dicapai dengan cara menyemprotkan air ke dalam reaktor pada tekanan tinggi dan mempertahankan suhu pada kisaran 80 derajat C sampai 110 derajat C. Air yang diinjeksikan diuapkan dan debu dari gas yang hilang dikumpulkan di dalam kantong. -jenis saringan. Kandungan sulfur lebih rendah dari 50 mg per cum pada STP, kandungan debu lebih rendah dari 5 mg per cum pada STP dan kandungan furan/dioksin lebih rendah dari 0,1 nano gram per cum pada STP.
proses MEROS
Proses pengurangan emisi maksimal sintering (MEROS) adalah teknologi inovatif yang dikembangkan oleh Primetals Technologies untuk mengurangi emisi polusi dari pabrik sinter. Melalui penggunaan aditif khusus, komponen pencemar dalam aliran gas digabungkan dan dipisahkan dalam filter kain yang terhubung. Prosesnya 'semi-kering' dan karenanya 100% bebas limbah.
Proses MEROS adalah proses pembersihan untuk menghilangkan debu, gas asam, logam beracun dan senyawa organik dalam beberapa tahap. Prosesnya terdiri dari tiga langkah yaitu (i) injeksi adsorben berbasis karbon dan agen desulfurisasi ke dalam aliran sinter off-gas dalam arah berlawanan untuk mengikat logam berat dan senyawa organik, (ii) sirkulasi aliran gas melalui a reaktor pendingin di mana gas dilembabkan dan didinginkan hingga suhu sekitar 100 derajat C melalui kabut halus yang disuntikkan (mempercepat reaksi kimia yang diperlukan untuk mengikat dan menghilangkan SO2 dan komponen gas asam lainnya, dan (iii) aliran off-gas yang meninggalkan reaktor pengkondisian melewati bag filter tempat debu dengan polutan yang terperangkap dihilangkan.
Dalam proses ini, debu, gas asam, logam berbahaya, dan senyawa organik yang ada dalam gas sintering dihilangkan dengan tingkat efisiensi yang tinggi. Pada tahun 2007, instalasi pertama mulai beroperasi di Linz (Austria), dengan kapasitas pengolahan gas 1 juta N cum per jam. Emisi debu dengan proses MEROS diturunkan menjadi kurang dari 5 mg per N cum. Emisi merkuri, timbal, senyawa organik (seperti dioksin dan furan (PCDD/F)), HCl, HF, dan total VOC terkondensasi (senyawa organik yang mudah menguap) diturunkan hingga kurang dari 0,1 nano gram per N cum. Salah satu karakteristik yang paling menonjol dari proses MEROS adalah memenuhi peraturan lingkungan saat ini dan dapat bekerja dalam batasan yang dapat ditetapkan di masa mendatang. Flowsheet dasar dari proses MEROS ditunjukkan pada Gambar 8.
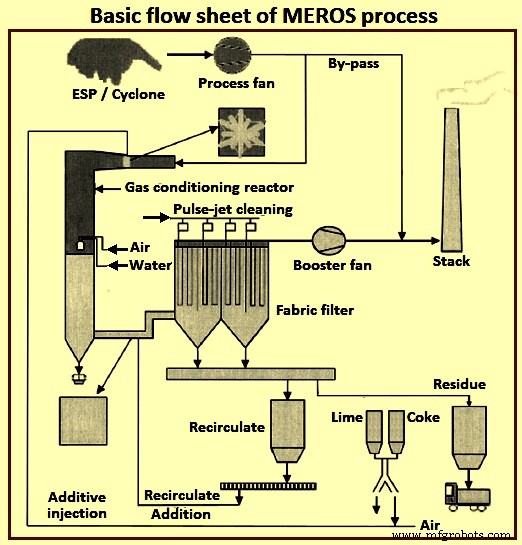
Gbr 8 Flowsheet dasar proses MEROS
Sistem resirkulasi gas limbah selektif
Selama proses sintering, volume udara yang dihisap biasanya lebih tinggi dari yang dibutuhkan untuk pembakaran sempurna bahan bakar untuk memungkinkan kecepatan tinggi dari bagian depan nyala. Gas limbah sinter karenanya biasanya mengandung sekitar 12% hingga 15% sisa oksigen. Itu juga pada suhu yang jauh di atas titik embun kritis. Ini cukup untuk resirkulasi ke proses sintering setelah penambahan sedikit udara tambahan.
Dalam 'sistem resirkulasi gas limbah selektif', off-gas dari zona yang dipilih dari mesin sinter dicampur dengan udara yang lebih dingin dan kemudian disirkulasikan kembali ke untai sinter. Sistem resirkulasi limbah-gas selektif dikembangkan pada awalnya untuk menjaga volume off-gas pada tingkat yang konstan sambil meningkatkan kapasitas sintering dan mengurangi emisi spesifik. Hal ini memungkinkan biaya investasi dan pengoperasian untuk fasilitas pembersihan gas berada pada tingkat yang dapat diterima.
Diagram skematik tipikal sistem resirkulasi gas limbah selektif diberikan pada Gambar 9. Pada gambar ini, gas buang limbah panas dari bagian pertama dan ketiga dari mesin sinter dicampur dengan udara luar dari pendingin sinter dan udara ambien dan disirkulasikan kembali ke bagian kedua dari mesin sinter. Sebagian dari limbah gas didaur ulang kembali ke tudung yang menutupi bagian untai sinter.
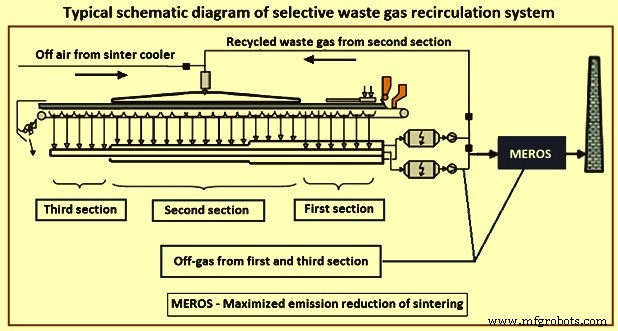
Gbr 9 Diagram skematik tipikal sistem resirkulasi gas buang selektif
Keuntungan dari sistem ini adalah (i) mengurangi volume gas buang per unit sinter sekitar 50%, (ii) mengurangi konsumsi bahan bakar padat spesifik sebesar 10% hingga 15% karena pemanfaatan panas gas buang dan pos CO (karbon mono-oksida). pembakaran, (iii) investasi dan biaya operasi yang lebih rendah untuk pabrik pembersihan limbah-gas, (iv) tingkat produktivitas dan kualitas sinter dipertahankan, (v) penurunan emisi CO2, dan (vi) emisi spesifik SOx, NOx, PCDD/ yang lebih rendah PCDF (dibenzo-p-dioxins/dibenzofurans), dan logam berat.
Pemodelan proses sintering
Selama proses sintering, beberapa reaksi kimia dan transformasi fasa terjadi, tidak hanya karena perubahan panas depan, tetapi juga karena modifikasi komposisi gas lokal dan suhu leleh awal campuran bahan baku. Ketika suhu lokal dan komposisi padatan tercapai, sebagian besar transformasi fase didorong oleh suplai panas dan difusi yang terjadi di dalam lapisan partikel dengan mekanisme pembentukan cairan memainkan peran utama. Bahan sebagian meleleh ketika suhu lokal mencapai suhu leleh dan saat bergerak, kontak dengan gas dingin mendorong pemadatan ulang dan dengan demikian, aglomerasi partikel membentuk kue sinter berpori yang terus menerus. Sifat kue sinter akhir sangat bergantung pada siklus termal, komposisi kimia awal bahan baku, dan sifat termo-fisik yang dikembangkan selama sintering. Model matematis dari proses sintering mensimulasikan fenomena yang terjadi di dalam mesin sinter dalam produksi industri sinter ke tanur tinggi.
Metode untuk pemodelan proses sintering mesin strand industri didasarkan pada persamaan transpor multi-fase, dan multi-komponen momentum, massa, dan energi untuk fase gas, padat dan cair dengan mempertimbangkan fenomena lokal pembentukan sinter berpori ( Gambar 10). Model mempertimbangkan fase berinteraksi secara bersamaan dan spesies kimia dari setiap fase dihitung berdasarkan persamaan konservasi spesies kimia. Deskripsi akurat dari laju pertukaran untuk momentum, energi, dan reaksi kimia sangat penting untuk keseluruhan akurasi model.
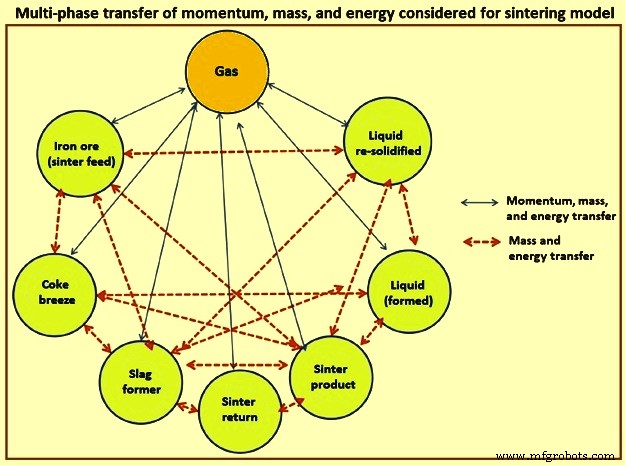
Gbr 10 Transfer multifase momentum, massa, dan energi dipertimbangkan untuk model sintering
Spesies kimia secara individual diperhitungkan dengan memecahkan persamaan transportasi setiap spesies kimia dari fase gas dan padat. Fase padat menyumbang campuran umpan sinter bijih besi, sinter halus (sinter halus yang dikembalikan), angin kokas (atau bahan bakar padat lainnya), kerak (halus dari pabrik baja), dan fluks. Fase cair terdiri dari komponen-komponen yang meleleh dan terbentuk dalam fase cair. Fase re-solidifikasi terdiri dari cairan yang dipadatkan kembali dan fase yang terbentuk selama proses re-solidifikasi dan sangat bergantung pada komposisi cairan lokal dan pertukaran panas. Kue sinter akhir dibentuk oleh campuran bahan-bahan ini dan kualitasnya tergantung pada komposisi akhir dan fraksi volume masing-masing bahan ini dan distribusinya dalam struktur sinter mosaik.
Dalam model proses sinter, diasumsikan bahwa fase cair yang terbentuk bergerak bersama dengan fase padat yang tersisa karena viskositas dan mengingat bahwa cairan yang terbentuk melekat pada permukaan partikel yang tidak meleleh, dengan demikian, persamaan untuk perpindahan momentum dan entalpi akun padatan untuk campuran cairan kental dan bahan padat ini. Dalam model, sifat termo-fisika yang bergantung pada suhu-komposisi diasumsikan mengikuti aturan campuran untuk memperhitungkan sifat-sifat fase individu yang dicermati oleh fraksi volume fasenya.
Otomasi dan sistem kontrol
Dengan tujuan akhir untuk menstabilkan proses sintering, meningkatkan produktivitas, dan menurunkan biaya produksi, sistem otomasi dan kontrol diperlukan di pabrik sinter untuk memastikan operasi yang optimal dan stabil selama proses sintering. Untuk tujuan ini, beberapa upaya telah dilakukan untuk memahami fenomena di tempat tidur dan mengarahkan proses menuju operasi yang optimal. Teknik kontrol utama dalam sintering adalah kontrol densitas muatan untuk mencapai sintering yang seragam di seluruh lebar untaian dan kontrol kecepatan palet untuk mempertahankan produktivitas dan kualitas sinter yang optimal.
Sistem otomatisasi dan kontrol untuk pabrik sinter adalah sistem hierarki tiga tingkat yang menggunakan sistem kontrol terdistribusi (DCS), sistem komputer proses terpusat (PCS), dan sistem komputer pusat (CCS) dari pabrik baja. DCS melakukan fungsi seperti mengukur distribusi kecepatan angin dan distribusi suhu gas di sepanjang untai sinter, dan juga 'kontrol digital langsung' (DDC). PCS melakukan fungsi seperti kontrol proses untuk mengoptimalkan operasi pabrik sinter, dan layanan informasi kepada operator. CCS melakukan fungsi seperti perencanaan, pengelolaan, dan analisis data produksi dan operasi berdasarkan basis data tujuan umum. Gambar 11 menunjukkan sistem otomatisasi dan kontrol untuk pabrik sinter.
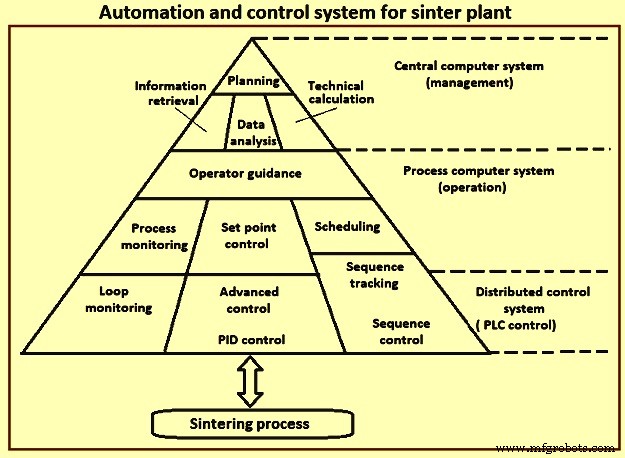
Gbr 11 Sistem otomasi dan kontrol untuk pabrik sinter
Sistem pakar sinter loop tertutup dirancang sehingga operator harus mengambil 'tindakan sesedikit mungkin, sebanyak yang diperlukan' dengan target untuk mengaktifkan operasi sinter yang dioptimalkan yang memerlukan interaksi operator minimal. Sistem pakar, yang dirancang sebagai sistem keputusan berbasis aturan, menangkal fluktuasi proses yang disebabkan oleh perubahan komposisi dan kualitas campuran mentah, faktor manusia, atau kondisi proses. Semakin cepat sistem merespons situasi proses yang tidak normal atau berubah, semakin lancar operasi sinter secara keseluruhan. Waktu yang akurat untuk aktivitas pengendalian dan antisipasi gangguan sangat penting untuk menghindari kondisi proses yang kritis dan untuk mempertahankan tingkat produksi yang tinggi dengan biaya rendah.
Dengan sistem otomasi dan kontrol, kondisi kontrol proses yang optimal tercapai karena keselarasan sempurna dari parameter proses terjadi. Sistem otomasi level 2 terintegrasi di pabrik sinter, standar deviasi parameter kualitas dapat diturunkan sekitar 5% hingga 10%. Sistem ini juga membantu dalam pengurangan konsumsi coke angin dapat dikurangi sekitar 3% dan produktivitas dapat ditingkatkan sekitar 3% sampai 5%.