Penggulungan baja di Hot Strip Mill
Penggulungan baja di Hot Strip Mill
Pabrik strip panas saat ini adalah pabrik strip panas konvensional atau pabrik strip untuk menggulung pelat tipis. Fungsi utama pabrik strip panas (HSM) konvensional adalah untuk memanaskan kembali baja setengah jadi slab (digulung atau dicor terus menerus) ke suhu rolling dan kemudian menggulungnya lebih tipis dan lebih lama melalui serangkaian dudukan rolling mill yang digerakkan oleh motor besar dan akhirnya menggulung lembaran baja yang diperpanjang agar mudah ditangani dan diangkut. diameter dalam 750 mm pada coiler, dengan diameter luar hingga 2400 mm dan dengan batasan berat coil hingga lebar 220 kg per cm. Hot strip mill memasok coil untuk unit cold rolling mill, strip shearing dan slitting sebagai serta produk jadi untuk pengiriman langsung ke pelanggan. Sebagian besar material diangkut keluar dari area pabrik dengan sistem penanganan kumparan otomatis ke lorong penyimpanan.
Atribut yang diberikan ke strip oleh pabrik strip canai panas meliputi kualitas permukaan, ketebalan, lebar, dan kontrol kerataan serta profil strip.
Penggulungan pelat baja di pabrik strip panas terdiri dari beberapa sub-proses dan pada akhirnya produk akhir 'kumparan canai panas' diproduksi. Sub-proses utama adalah (i) pemanasan pelat baja di tungku pemanas ulang, (ii) kerak pelat yang dipanaskan dan ukurannya di sizing press, (iii) penggulungan di pabrik pengasaran dan pembersihan kerak sekunder, (iv) penggulungan di penggilingan akhir, (v) mengontrol pendinginan strip canai panas dan (vi) penggulungan strip canai.
Pemanasan ulang pelat
Penting untuk pabrik strip panas adalah tungku pemanasan ulang. Pabrik hot strip modern dilengkapi dengan tungku pemanas balok berjalan yang canggih yang telah menggantikan dan mengungguli tungku pemanas ulang tipe pendorong yang lebih tua. Tungku pemanasan ulang ini secara nominal dinilai untuk menghasilkan pelat yang dipanaskan dalam kisaran 250 ton per jam hingga 300 ton per jam dengan kemampuan memproduksi hingga 25% ekstra untuk keluaran terukurnya dengan beberapa pengorbanan dalam keseragaman suhu pelat. Tungku membutuhkan sekitar 350.000 kkal bahan bakar gas per ton slab untuk pemanasan slab dari suhu kamar ke kisaran suhu 1100 derajat C sampai 1250 derajat C. Pelat yang diperiksa sesuai jadwal rolling ditempatkan satu per satu di meja rol pengisian tungku di halaman pelat dan diposisikan di depan pintu pengisian pada tungku pemanas ulang. Ketika ruang tersedia di tungku, lengan pendorong mendorong pelat ke dalam tungku. Begitu masuk, pelat ditopang sekitar 2,5 m di atas lantai tungku dengan pipa berpendingin air, berlapis tahan api yang disebut 'selip'. Untuk meminimalkan titik dingin ('tanda selip') yang tertinggal di pelat, jarak selip berubah dalam beberapa desain tungku pemanas ulang sekitar dua pertiga jalan melalui tungku. Dua set skid independen, satu tetap dan satu berjalan, bergiliran menopang pelat saat berjalan melalui tungku oleh sub-rangka besar yang diberi energi oleh sepasang silinder hidrolik besar. Tergantung pada desain tungku, bagian dalam tungku dibagi menjadi beberapa (lima sampai sepuluh) zona untuk kontrol suhu. Zona pemanasan awal dan pemanasan membakar campuran bahan bakar gas dan udara pembakaran yang dipanaskan sebelumnya dengan pembakar di atap dan di dinding samping tungku, baik di atas maupun di bawah selip, untuk memanaskan pelat hampir ke suhu pelepasannya.
Sebagian besar pemanasan awal pelat baja dicapai dengan gas buang panas yang mengalir melewati pelat menuju recuperator. Panas apa pun yang tersisa di gas buang memanaskan lebih dulu udara pembakaran yang masuk hingga sekitar 500 derajat C hingga 550 derajat C di dalam recuperator. Di zona pemanasan baja terutama dipanaskan oleh radiasi oleh dinding tungku panas. Di zona rendam, ukuran dan lokasi burner sedemikian rupa sehingga dapat mempertahankan suhu yang seragam di dalam zona untuk menyeimbangkan titik dingin di pelat.
Pembagi tahan api membantu membedakan zona secara fisik, dan sensor suhu termokopel di seluruh tungku berinteraksi dengan sistem kontrol burner otomatis untuk mempertahankan suhu target di setiap zona. Model komputer yang kompleks menghitung suhu keluar pabrik roughing yang ditargetkan untuk mendapatkan suhu tujuan pelepasan tungku. Memperkirakan profil suhu melalui ketebalan setiap pelat di tungku secara berkelanjutan, komputer membantu operator dalam memilih tingkat produksi dan titik setel zona yang memaksimalkan produksi pelat baja yang dipanaskan secara seragam hingga sedekat mungkin dengan suhu target . Setelah proses penggulungan dimulai, saat baja keluar dari pabrik pengasaran, suhunya diumpankan kembali ke tungku, memperbarui model komputer dan menginformasikan operator tungku tentang keseragaman suhu.
Ketika pelat mencapai 'pintu pelepasan' di ujung keluar tungku, dan komputer telah menentukan bahwa pelat telah cukup panas, pintu terbuka dan lengan pengekstrak mencapai di bawah pelat, angkat dari selip mendukung, dan menariknya keluar dari tungku. Tungku pemanasan ulang biasanya memiliki dua ekstraktor. Ekstraktor ini dapat bertindak secara independen satu sama lain untuk menghilangkan pelat bermuatan ganda satu per satu atau dalam kombinasi untuk mengekstrak pelat yang lebih panjang. Pelat panas ditempatkan di meja rol masuk yang membawanya ke pabrik pengasaran melalui pemutus kerak.
Pembersihan kerak dan ukuran pelat
Pembersihan kerak pada pelat yang dipanaskan adalah suatu keharusan di pabrik strip panas untuk mendapatkan kualitas permukaan yang baik dari strip canai panas. Pengoperasian pembersih kerak perlu dioptimalkan untuk memastikan pembuangan kerak secara maksimal dan karenanya meningkatkan pembersihan pada pendinginan minimum pelat yang dipanaskan.
Setelah meninggalkan tungku pemanas ulang, pelat melewati dengan kecepatan berkisar dari 0,15 m/detik hingga 2,0 m/detik melalui unit kerak, sebuah selungkup yang menggunakan dua pasang kepala semprot. Header semprot ini sederhana, desain ramah perawatan dan menyemprotkan air bertekanan tinggi (tekanan air hingga 400 kg/cm²) pada pelat untuk menghilangkan lapisan besi teroksidasi yang terbentuk di permukaan pelat dalam atmosfer yang kaya oksigen. tungku pemanas ulang. Header ini biasanya dilengkapi dengan nozel canggih untuk menyemprotkan air secara efektif. Pembersih kerak biasanya berdesain tertutup untuk mencegah air keluar dan ada aliran air yang dioptimalkan di dalam pembersih kerak. Konsumsi air untuk membersihkan kerak berkisar dari 200 cum/jam hingga 700 cum/jam.
Pabrik hot strip modern dilengkapi dengan sizing press sebagai pengganti edger. Keuntungan teknologi penting dari sizing press adalah bahwa selain menghasilkan pengurangan lebar yang besar (hingga 350 mm) dalam satu lintasan, itu menyebabkan dengan jelas lebih baik melalui pembentukan pelat tepat di tengahnya. Mesin press slab sizing menghasilkan 'dogbones' yang lebih rata yang mengarah pada pengurangan penyebaran dan efisiensi ukuran yang lebih besar. Pers sizing menawarkan keuntungan yang berbeda dari lebih banyak fleksibilitas dalam produksi strip panas. Pengurangan lebar dalam sizing press pass memungkinkan jumlah ukuran dalam pengecoran kontinu distandarisasi menjadi beberapa lebar yang pada gilirannya membantu dalam peningkatan produktivitas dalam mesin pengecoran kontinu. Mode guratan pendek khusus di ujung kepala dan ekor pelat menghasilkan lebih sedikit kehilangan panen dan hasil yang lebih tinggi.
Penggilingan kasar dan kerak sekunder
Di pabrik strip panas semi kontinyu, pabrik roughing biasanya terdiri dari satu atau dua stand roughing di mana slab digulung panas secara reversibel. Pelat digulung di pabrik pengasaran 5 atau 7 kali berulang kali untuk mencapai persyaratan ketebalan minimum sekitar 30 mm. Roughing mill juga berisi edger rolls yang digunakan untuk menggulung tepi slab dan memusatkannya.
Pabrik strip panas dapat berupa pabrik kinerja tinggi atau pabrik kompak. Perbedaan dari kedua tipe mill ini adalah pada coil box yang pada compact hot mills dipasang antara roughing dan finishing mill. Ini menyetarakan suhu batang transfer dengan efek bahwa dengan sedikitnya enam dudukan finishing, pengukur akhir 1,2 mm dapat dicapai. Ketebalan batang transfer yang dapat ditangani oleh kotak koil biasanya berkisar antara 20 mm hingga 40 mm dan kecepatan penggulungan sekitar 5,5 m/detik. Kapasitas output dari hot mill kompak biasanya berkisar 3,5 juta ton per tahun, sedangkan pabrik berkinerja tinggi dapat mencapai hingga kira-kira. 5,5 juta ton per tahun.
Throughput tinggi untuk HSM meminta jumlah minimum lintasan di pabrik pengasaran yang sangat penting untuk HSM semi kontinu. Ini berarti pengurangan tinggi per lintasan, yang hanya mungkin dilakukan dengan perilaku menggigit gulungan yang sangat baik. Sudah diketahui bahwa gigitan rol ditingkatkan dengan kandungan karbida yang lebih rendah dan kekerasan permukaan kerja rol kerja yang lebih rendah.
Dalam HSM berkelanjutan, pabrik pengasaran biasanya terdiri dari enam berdiri penggilingan independen, empat hingga lima terakhir yang menggabungkan pabrik penggilingan vertikal kecil yang disebut edgers. Pelat yang dipanaskan digulung melalui satu dudukan pada satu waktu untuk menghasilkan apa yang disebut batang transfer yang cocok untuk penggulungan akhir. Nozel jet air bertekanan tinggi membersihkan besi teroksidasi, atau kerak, dari permukaan di sepanjang jalan. Saat batang pemindah keluar dari dudukan penggilingan kasar terakhir, ketebalan tepi depan batang diperkirakan. Demikian pula, pirometer mengukur profil suhu batang dari kepala ke ekor dan kamera khusus memotret kedua ujungnya. Tergantung pada ukuran, lebar, dan tingkat produk yang akan digulung, suhu rata-rata batangan saat keluar dari penggilingan kasar terakhir biasanya berkisar antara 1050 derajat C hingga 1150 derajat C. Data ini dikumpulkan untuk mengantisipasi penggulungan akhir.
Empat sampai lima pabrik roughing terakhir masing-masing menggabungkan edger untuk kontrol lebar. Pabrik roughing individu ditempatkan semakin jauh terpisah untuk mengakomodasi pemanjangan batang transfer karena digulung lebih tipis dan lebih tipis. Pada suhu yang sangat tinggi di mana baja digulung di pabrik pengasaran, itu sangat plastis dan 'mengalir' dengan mudah. Akibatnya, saat pelat direduksi, batang cenderung menyebar lebar pada ujungnya. Edger berfungsi untuk menahan lebar yang seragam melalui panjang bilah.
Persyaratan pabrik roughing sehubungan dengan properti roll kerja untuk stand roughing diringkas sebagai berikut.
- Roll bite tinggi berdasarkan koefisien gesekan tinggi, memungkinkan pengurangan tinggi per lintasan tanpa gesekan atau selip dan akibatnya throughput yang lebih tinggi dengan pengurangan kehilangan panas produk.
- Ketahanan material cangkang yang tinggi terhadap keausan, kelelahan termal, dan oksidasi/korosi, menghasilkan keausan yang rendah dan homogen sehingga memungkinkan kampanye rolling lebih lama dan mengurangi waktu henti.
- Ketahanan terhadap panas tinggi dan retak api yang merupakan singkatan dari jaringan api kecil halus yang mencegah kerusakan tinggi yang disebabkan oleh kios pabrik.
- Kualitas permukaan gulungan yang sempurna dalam jangka panjang, yang terkait dengan tidak ada pengelupasan, tidak ada pita, tidak ada micro-spalling selama satu waktu kampanye.
- Keamanan tinggi terhadap kegagalan gulungan yang dihasilkan oleh segala jenis kondisi operasi termasuk insiden pabrik, beban termal dan mekanis yang tinggi, dll.
Karena ujung kepala yang berbentuk persegi sangat penting untuk memasang ulir dengan benar pada penggilingan akhir dan penggulung bawah, dan karena ekor yang tidak rata dapat merusak permukaan gulungan kerja atau menyebabkan masalah pemasangan ulir untuk proses produksi berikutnya, ujung kepala dan ekor hampir setiap transfer bar dipotong oleh sepasang drum baja besar masing-masing dengan pisau geser memanjang sepanjangnya. Dengan batang merayap di sepanjang meja rol sekitar 30 m/mnt, sensor mendeteksi posisi dan kecepatannya untuk mengatur waktu drum geser tanaman untuk mengoptimalkan jumlah yang dipotong; karena bilah transfer tebalnya sekitar 30 mm, setiap pemotongan ekstra berarti kerugian panen yang cukup mahal.
Antara geser tanaman dan stand rolling pertama dari pabrik finishing biasanya ada pemutus skala kedua, yang tugasnya adalah penghapusan skala akhir. Semprotan air di atas dan di bawah batang transfer pada tekanan sekitar 200 kg/cm2 memecah kerak yang telah terbentuk kembali (skala sekunder), serta semua kerak yang bertahan melalui operasi pembersihan kerak sebelumnya. Penyesuaian ketinggian dari tajuk penyemprotan atas dan bak pengumpul air memungkinkan adaptasi optimal dari batang transfer yang sedang ditangani. Karena pengaturan nosel khusus, tingkat pendinginan yang berbeda pada bilah transfer sisi bawah diminimalkan.
Setelah pembersihan kerak sekunder, batang dijepit oleh sepasang gulungan yang digerakkan secara pneumatik untuk secara mekanis melonggarkan kerak yang tersisa, yang, saat suhu pemrosesan mendingin, menjadi semakin lengket bahkan ketika kembali lebih lambat ke permukaan yang masih merah. baja panas.
Penggilingan akhir
Pabrik finishing HSM biasanya memiliki lima hingga tujuh dudukan gulungan akhir, yang mengurangi ketebalan batang transfer hingga ke ukuran yang diperlukan. Kecepatan rolling diatur untuk memungkinkan stand terakhir melakukan reduksi akhir pada suhu akhir, antara 820 derajat C hingga 900 derajat C, sehingga mencapai sifat mekanik tertentu dalam strip canai panas. Pabrik finishing menggulung bar transfer secara bersamaan, yang berarti setiap bar digulung melalui semua dudukan finishing sekaligus. Baja panas cukup rapuh saat digulung dan ketegangan antara dudukan pabrik finishing harus dikontrol dengan ketat pada tingkat yang sangat rendah untuk menghindari peregangan atau robeknya strip.
Penyesuaian dibuat seperlunya untuk memastikan benang strip dengan benar melalui masing-masing penggilingan tanpa melingkar dan melipat atau meregangkan dan merobek. Posisi setiap gulungan diumpankan kembali ke sistem otomasi canggih pabrik finishing yang, bersama dengan informasi dari sel beban yang memantau gaya rolling dan dari pengukur sinar-X yang mengukur ketebalan strip akhir, bekerja untuk menyesuaikan celah gulungan dan kecepatan dengan lancar. mempertahankan penggulungan strip yang stabil hingga ketebalan yang diperlukan terlepas dari variasi suhu yang ada di setiap batang.
Setelah batang dipasang di antara setiap pasangan penggilingan yang berurutan, looper memasang strip untuk memantau tegangan di antara dudukan. Looper yang diatur di antara dudukan akhir HSM menjaga kontrol aliran massa yang benar dan karenanya berkontribusi pada penggulungan strip jadi yang stabil hingga ketebalan akhir strip. Looper digerakkan oleh silinder hidrolik.
Untuk penggulungan strip ultra tipis, looper yang menampilkan pengukuran tegangan diferensial digunakan untuk mendeteksi perbedaan tegangan strip antara drive dan sisi operator yang dapat dihilangkan dengan memutar set gulungan atas. Perbedaan tegangan kecil berkontribusi pada pelepasan jalinan yang andal dan membantu mencegah tabrakan di bagian belakang.
Fungsi looper tensiometer adalah untuk mengukur distribusi tegangan tarik melintasi lebar strip yang merupakan prasyarat penting untuk kontrol kerataan online otomatis. Tensiometer sebaiknya diatur di antara dua dudukan terakhir.
Fasilitas antar stand sangat penting untuk produksi strip canai panas dengan kualitas permukaan terbaik. Peralatan penting termasuk (i) panduan masuk dan keluar, (ii) sistem pendingin roll kerja, (iii) perangkat anti mengelupas, (iv) sistem pelumasan celah gulungan, dan (v) sistem pendinginan dan pembersihan kerak antar stand. Interaksi yang erat dari semua fasilitas ini adalah suatu keharusan untuk mencapai hasil yang optimal. Sideguard yang menampilkan penyesuaian lebar hidraulik memastikan pemosisian yang tepat dalam waktu minimum. Area pemandu strip dirancang agar semua suku cadang yang aus dapat diganti dengan cepat. Efisiensi pendinginan ditingkatkan dengan pemilihan dan pengaturan nozel yang dioptimalkan.
Kombinasi pendinginan celah gulungan, pelumasan celah gulungan, dan sistem pendinginan sisi keluar yang ditingkatkan mengurangi suhu gulungan. Ini menghasilkan lapisan oksida yang lebih tipis pada permukaan gulungan dengan konsekuensi pengelupasan gulungan yang lebih sedikit. Pelumasan di dalam celah gulungan meminimalkan gesekan, sehingga memungkinkan pengurangan gaya guling sebesar 20% hingga 30%. Dengan cara ini dimungkinkan untuk mendistribusikan kembali gaya rolling untuk mengoptimalkan jadwal lintasan dan pengukur strip akhir yang lebih tipis. Selain itu, celoteh atau getaran pada dudukan dapat dicegah yang menyebabkan masa pakai gulungan lebih lama.
Transformasi metalurgi yang mendalam dalam struktur kristal terjadi saat material mendingin, yang, tergantung pada kimia spesifik material, biasanya antara 800 derajat C dan 850 derajat C. Selain itu, sifat mekanik produk akhir merespons hingga tingkat tertentu. ke suhu tertentu di mana lintasan reduksi akhir diambil.
Akibatnya, suhu penyelesaian untuk setiap produk ditentukan dan otomatisasi pabrik menyesuaikan kecepatan berdiri pabrik finishing pertama berdasarkan suhunya dan sejauh mana batang diharapkan mendingin saat melewati setiap dudukan, untuk memungkinkan strip yang keluar dari dudukan akhir untuk memenuhi suhu target. Operasi kerja panas terakhir biasanya dilakukan di atas suhu kritis atas 787,8 derajat C yang memungkinkan baja canai melewati transformasi fase setelah semua pekerjaan panas selesai. Ini menghasilkan butiran halus yang seragam di seluruh baja. Jika bagian dari hot rolling dilakukan pada baja yang telah sebagian berubah menjadi ferit, butiran ferit yang terdeformasi akan menjadi kasar selama self-anneal yang terjadi selama pendinginan baja yang digulung. Kondisi ini dapat membatasi kesesuaian baja untuk beberapa aplikasi menggambar yang parah.
Karena setiap batang pemindah menghabiskan kira-kira satu menit di penggilingan akhir, dari kepala ke ekor, suhu baja yang masuk ke dudukan akhir secara signifikan lebih rendah, mungkin 100 derajat C, pada saat ujung ekor digulung dibandingkan dengan ujung kepala. Akibatnya, setelah 150 m pertama dari strip telah digulung pada kecepatan ulir dan coiler bawah telah diulir, penggilingan mulai berakselerasi pada tingkat 'zoom' yang telah dihitung dari profil suhu batang saat keluar. penggilingan kasar terakhir. Kecepatan tertinggi setinggi 20 m/dtk dicapai oleh otomatisasi pabrik yang berupaya mempertahankan suhu penyelesaian yang ditentukan di seluruh produk akhir. Sebuah pirometer yang ditempatkan setelah stand terakhir memperbarui model komputer pabrik finishing dan memungkinkan penambahan suhu ini untuk menghapus catatan kualitas.
Dengan gaya rolling yang luar biasa yang ada di rolling mill, tidak cukup hanya mengatur celah antara work roll dengan ketebalan yang diinginkan dan mengharapkan strip keluar dari sisi lain pada ketebalan itu. Dengan gaya rolling yang secara teratur melebihi 3.000 ton di stand finishing awal, rumah pabrik dapat diharapkan untuk meregangkan sebanyak 10 sampai 15 mm setelah bar memasuki gigitan saat menggulung produk yang lebar, kaku, dan/atau light-gauge. Saat mengatur celah gulungan untuk threading, faktor ini sangat penting untuk dikompensasikan di setiap dudukan pabrik; untuk melakukannya, model canggih digunakan oleh otomatisasi pabrik untuk memperkirakan gaya guling untuk setiap batang transfer di setiap dudukan berdasarkan, antara lain, ketebalan masuk dan keluar, lebar, kadar baja, dan perkiraan suhu seketika. Model yang digunakan oleh otomatisasi pabrik diperbarui dengan parameter penggulungan dan pengukuran produk setiap kali pelat baru digulung, terus mengoptimalkan pengaturan otomatisasi pabrik. Kualitas produk dan hasil produksi mendapat manfaat dari penjadwalan produk dengan pengukur dan tingkat yang serupa untuk digulung secara berurutan, memungkinkan otomatisasi untuk menerapkan model penggulungan yang paling baru digunakan.
Selain sejauh mana pabrik berdiri meregang di bawah beban bergulir, gulungan membelokkan, atau menekuk, di bawah beban karena mereka dipaksa terpisah di tengah oleh strip tetapi didukung di ujungnya oleh bantalan. Defleksi ini adalah sumber dari atribut strip yang biasa disebut sebagai mahkota. Strip crown dimulai di pabrik roughing dan berlanjut melalui setiap stand rolling mill berturut-turut. Mahkota strip diukur di ujung keluar pabrik finishing dengan sedetik, memindai pengukur sinar-X yang melintasi bolak-balik melintasi lebar strip saat baja digulung. Ketebalan yang diukur dibandingkan dengan ketebalan yang diukur dengan sinar-X utama yang memantau pengukur garis tengah melalui panjang strip dan perbedaannya kemudian diplot sebagai catatan kualitas produk. Biasanya, HSM memproduksi material dengan mahkota antara 0,025 mm dan 0,075 mm tergantung pada sejumlah faktor yang mencakup ukuran, lebar, dan tingkat produk jadi.
Operator dari dudukan rol mana pun memiliki tingkat kontrol atas bentuk celah rol dengan menyesuaikan sekrup ke bawah untuk menambah atau mengurangi gaya rol yang ada di dudukan itu, yang memengaruhi sejauh mana rol dibelokkan. Empat dudukan penggilingan terakhir umumnya menggabungkan pembengkokan gulungan kerja hidraulik untuk memberi operator kontrol tambahan atas bentuk celah gulungan yang dimuat. Operator menyesuaikan pembengkokan rol kerja pada dudukan ini untuk memengaruhi kenop pada produk akhir. Tekuk work-roll di dudukan finishing akhir digunakan secara eksklusif untuk membuat bentuk celah gulungan yang cocok dengan profil strip yang keluar dari pabrik finishing sebelumnya untuk menghasilkan produk akhir yang rata.
Teknologi yang tergabung dalam hot strip mill modern untuk meningkatkan kualitas produk adalah (i) kontrol pengukur otomatis, (ii) kontrol lebar otomatis, (iii) pembengkokan gulungan kerja, (iv) mahkota variasi kontinu (CVC), (dan v ) menggulung kompensasi eksentrisitas. CVC adalah cara untuk mengubah profil strip dengan menggunakan gulungan dengan profil. Kesenjangan antara gulungan dapat diubah dengan menggeser gulungan secara aksial. Teknik CVC juga dikenal sebagai teknik roll shifting. Teknik CVC memiliki dinamika yang lebih lambat tetapi jangkauannya lebih luas dari work roll bending. Karena CVC dan work roll bending saling melengkapi, kedua teknik tersebut biasanya digunakan di pabrik hot strip modern.
Selama beberapa tahun terakhir, ada peningkatan permintaan pada profil, ketebalan, kerataan dan permukaan strip panas. Untuk memenuhi permintaan ini, teknologi CVC telah ditingkatkan. Peningkatannya ada pada peralatan mekanis dan model proses.
Kontrol pendinginan
Setelah keluar dari penggilingan akhir, strip dibawa ke bawah oleh sejumlah besar gulungan yang digerakkan secara individual melalui empat hingga 12 bank semprotan air volume tinggi bertekanan rendah yang mendinginkan strip merah-panas ke suhu melingkar tertentu antara 400 derajat C dan 900 derajat C dan ke dalam kumparan bawah. Pemandu samping di kedua sisi meja run out berusaha untuk menjaga ujung kepala strip tetap mengarah ke coiler; bagian akhir pemandu di depan setiap coiler menyesuaikan agar sesuai dengan lebar strip dan dilengkapi sistem quick-close pneumatik yang memungkinkan operator untuk memusatkan head-end strip saat coiling dimulai.
Secara metalurgi kritis terhadap sifat-sifat baja canai panas adalah suhu penggulungan, karena kumparan mendingin dari suhu ini ke lingkungan selama tiga hari. Pada dasarnya perlakuan panas yang sebanding dengan anil, tegangan yang diberikan pada baja selama pengurangan dari ketebalan pelat ke ukuran strip panas diberi kesempatan saat kumparan mendingin untuk menghilangkannya. Meskipun baja terus menerus mengkristal selama pengerolan panas, pengurangan ketebalan kadang-kadang melebihi 99% dan terjadi dalam waktu kurang dari sepuluh menit sangat menekan baja; suhu melingkar ditentukan oleh ahli metalurgi produk untuk memanfaatkan dan memanipulasi tingkat stres tersebut untuk mencari sifat mekanik yang optimal. Pendinginan strip canai panas setelah penggulungannya di stand finishing terakhir ditunjukkan pada Gambar 1.
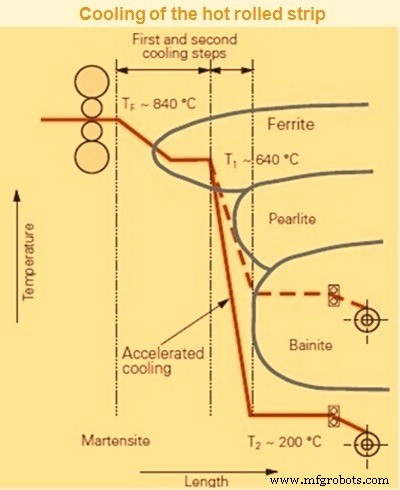
Gbr 1 Pendinginan strip canai panas
Area keluar yang terletak di antara gilingan akhir dan penggulung dari gilingan strip panas diperlukan untuk pengangkutan material dan pengaturan suhu material, dan karenanya untuk mencapai sifat mekanik. Pemilihan jarak rol sebagai fungsi dari rentang ketebalan strip mengamankan pengangkutan yang andal terutama pada kepala strip.
Bekerja sama dengan model pendinginan yang sangat efisien, sistem pendingin laminar yang diatur di area ini memastikan suhu penggulungan yang diinginkan serta pendinginan untuk mencapai sifat mekanik yang diinginkan dari bahan canai.
Kombinasi sistem pendingin laminar dan sistem penutup tepi mencegah pendinginan berlebih pada tepi strip, sehingga meminimalkan perbedaan tegangan pada lebar strip. Hasilnya, kerataan strip dingin meningkat.
Produk yang dijual sebagai canai panas dan canai panas acar dan diminyaki untuk dipotong laser oleh pelanggan digulung pada suhu yang relatif tinggi untuk mencoba mengendurkan baja sebanyak mungkin sehingga bagian yang dipotong dari kumparan tetap rata bahkan setelah tegangan sisa teratasi sendiri di sekitar konfigurasi bagian. Sebaliknya, penggulungan pada suhu yang relatif dingin memungkinkan mutu baja kualitas fisik untuk mempertahankan tingkat tegangan internal yang lebih tinggi dan membatasi ukuran masing-masing kristal dan karbida yang terbentuk di dalam dan di antara kristal; masing-masing faktor ini berkontribusi pada tingkat kekuatan yang lebih tinggi pada strip canai panas yang sudah jadi.
Mendinginkan baja 200 derajat C saat melewatinya dengan kecepatan hingga 20 m/dtk membutuhkan air dalam jumlah besar, sehingga sejumlah besar 152 kepala semprot, masing-masing dengan katup dan dikendalikan oleh sistem otomasi, membasahi baja dari atas dan bawah dengan tirai air. Perkiraan komputer, berdasarkan kecepatan ulir strip dan suhu penyelesaian target, berapa banyak air yang dibutuhkan untuk mendinginkan ujung kepala, dan keakuratan perkiraan ini dikonfirmasi oleh pirometer di depan kumparan bawah. Karena penyesuaian jumlah semprotan yang digunakan diperlukan, komputer menghidupkan dan mematikan semprotan untuk memenuhi suhu yang ditargetkan melalui panjang koil. Karena penggilingan akhir berakselerasi setelah koil bawah diulir untuk terus membuat suhu penyelesaian, semakin banyak semprotan yang diaktifkan saat baja digulung untuk mengimbangi pengurangan waktu yang dihabiskan di meja run-out.
Hingga 300 meter kubik air dipompa setiap menit ke seluruh HSM untuk mendinginkan strip yang sudah digulung, selip tungku, gulungan pabrik, dan komponen penggulung, dan untuk menghilangkan kerak pada batang transfer. Semua air didaur ulang melalui sistem lubang pengumpulan kerak/lumpur, melalui sistem pendingin laminar, dan kembali ke salah satu dari dua menara pendingin khusus.
Melingkar
Operasi penggulungan dimulai dengan sepasang gulungan penjepit yang menangkap ujung ujung strip dan membentuk tegangan melintasi meja run-out dan kembali ke pabrik finishing. Ujung kepala dibelokkan oleh gerbang ke mandrel yang terkait dengan coiler dan dipandu di sekitar mandrel oleh gulungan pembungkus yang digerakkan secara pneumatik yang dihubungkan oleh apron.
Panduan masuk yang dapat disetel hidraulik yang disediakan di ujung terminal meja run out berfungsi untuk memusatkan strip sebelum memasuki stasiun coiler. Strip yang berjalan pada kecepatan rolling akhir secara andal ditangkap oleh unit pinch roll dan diarahkan ke mandrel coiler. Gulungan penahan di sisi masuk unit gulungan jepit mencegah strip (terutama strip pengukur berat) menonjol di depan gulungan jepit.
Setelah ujung kepala berada di sekitar mandrel, putaran mulai terbentuk di sekitar mandrel, memaksa gulungan pembungkus menjauh. Setelah ujung kepala dicengkeram dengan kuat dan gesekan serta tegangan mencegah pembungkus baja tergelincir relatif terhadap mandrel, gulungan pembungkus terlepas dari kumparan baja yang tumbuh. Setelah strip keluar dari penggilingan akhir, gulungan penjepit terus menahan tegangan balik untuk mencegah gulungan terurai; sebelum ekor strip ditarik melalui gulungan jepit, gulungan pembungkus disambungkan kembali. Mobil koil hidraulik bergerak ke tempatnya di bawah koil, dan, setelah naik untuk menopang sebagian besar koil, melepaskan koil dari mandrel dan menempatkannya pada posisinya untuk diangkut ke mesin penjilidan dan pelabelan otomatis.
Dengan melihat kisaran ukuran lebar dari ketebalan strip canai panas dari 1,5 mm hingga 20 mm, lebar dari 750 mm hingga 2200 mm serta kondisi dan biaya untuk pemeliharaan stasiun penggulung, penggulung tiga gulungan atau empat gulungan menawarkan banyak manfaat praktis.