Aspek sejarah Pengecoran Berkelanjutan dan Teknologi terkait untuk Baja
Aspek historis Pengecoran Berkelanjutan dan Teknologi terkait untuk Baja
Teknologi continuous casting (CC) baja, sebagai metode pemrosesan solidifikasi baja cair memiliki sejarah yang relatif singkat — tidak lebih lama dari pembuatan baja oksigen. Berbeda dengan proses lain dalam produksi baja, pengecoran kontinu adalah penghubung penting antara fase cair dan padat dan harus hidup dengan efek metalurgi serta tantangan mekanis pada saat yang bersamaan.
Pengecoran kontinu mengubah baja cair menjadi padat secara terus menerus dan mencakup berbagai proses komersial yang penting. Proses ini adalah cara paling efisien untuk memadatkan volume besar baja cair menjadi bentuk sederhana untuk pemrosesan selanjutnya. Rasio CC untuk industri baja dunia sekarang sekitar 96% dari output baja mentah yang hanya 4% pada tahun 1970.
Pengecoran kontinu dibedakan dari proses pemadatan lainnya karena sifatnya yang stabil. Baja cair mengeras pada dinding cetakan sementara secara bersamaan ditarik dari dasar cetakan pada tingkat yang mempertahankan antarmuka padat / cair pada posisi konstan dengan waktu. Prosesnya bekerja paling baik ketika semua aspeknya beroperasi dengan cara kondisi mapan ini.
Dibandingkan dengan proses pengecoran lainnya, pengecoran kontinyu umumnya memiliki biaya modal yang lebih tinggi, tetapi biaya operasi yang lebih rendah. Ini adalah metode yang paling hemat biaya dan energi untuk memproduksi massal produk baja setengah jadi dengan kualitas yang konsisten dalam berbagai ukuran dan bentuk. Penampang melintang dapat berbentuk persegi panjang, untuk selanjutnya digulung menjadi pelat atau lembaran, persegi atau lingkaran untuk produk panjang dan pipa mulus, dan bahkan bentuk tulang anjing, untuk digulung menjadi balok I atau H.
Saat ini mesin continuous casting terdiri dari paket teknologi/mekatronik termodulasi untuk memungkinkan desain yang cepat dan waktu pelaksanaan proyek yang singkat serta peningkatan produksi yang cepat setelah heat pertama dicor. Dari sudut pandang metalurgi, mesin pengecoran kontinu canggih memiliki fitur untuk memungkinkan perawatan untai melalui teknologi pendinginan khusus dan reduksi lunak. Model proses yang canggih memungkinkan simulasi proses online dan kontrol loop tertutup untuk lebih mengoptimalkan kualitas produk dan sasaran produktivitas. Unit robot melakukan tugas di area berbahaya dan meningkatkan keandalan operasional tanpa campur tangan manusia. Kecepatan inovasi luar biasa dalam casting berkelanjutan sejak dimulainya komersialisasi pada 1950-an. Visi dan upaya pertama pengembangan proses ini selama 1960-an dan 1970-an serta tolok ukur pada 1980-an diamati.
Selama inkubasi yang agak lama pada periode pendahuluan, yaitu sebelum tahun 1950-an, rangsangan pengembangan penting datang dari industri nonferrous, yang telah menerapkan proses CC — khususnya, dengan prinsip cetakan bepergian — menggunakan roda dan/atau sabuk untuk mengatasi gesekan cetakan. Belakangan, ide-ide asli yang berasal dari pembuat baja menambahkan berbagai tonggak pencapaian dalam mendorong penerapan CC ke baja, meskipun terutama melalui proses yang didasarkan pada cetakan yang diam dan berosilasi.
Tahap awal dalam pengembangan casting berkelanjutan
Ide untuk membuat proses pengecoran lebih produktif melalui kontinuitas dikaitkan dengan J Laing yang pada tahun 1843 dipatenkan di Amerika Serikat setelah berhasil menguji mesin untuk pengecoran kontinu horizontal tabung dan lembaran dari paduan logam leleh rendah. Dalam paten ini, Laing mengusulkan pengumpanan logam cair dari reservoir vertikal melalui palung ke cetakan horizontal yang telah dipanaskan dengan mandrel yang dimasukkan yang diputar di sekitar porosnya untuk mencegah menempel pada pengecoran. Tabung didinginkan pada saat keluar dari cetakan.
Pengembangan lebih lanjut dari pengecoran kontinu dianggap berasal dari Henry Bessemer yang pada tahun 1857 menyarankan dan mematenkan di Inggris perangkat yang dikenal sebagai kastor gulung kembar. Dalam perangkat ini, baja cair dituangkan di antara dua drum berpendingin air, dan lembaran padat yang dihasilkan diekstraksi melalui pelat pemandu melengkung di mana lembaran itu terus menerus dipotong untuk diukur, dan selanjutnya diekstraksi melalui gulungan pegas (Gbr 1). Namun Bessemer tidak mengejar teknologi ini dengan memberikan prioritas yang lebih tinggi untuk mengembangkan proses pembuatan baja terlebih dahulu.
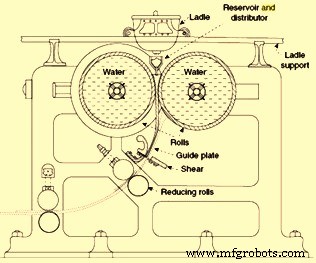
Gbr 1 Proses pengecoran kontinu diusulkan oleh Henry Bessemer
Butuh lebih dari 100 tahun untuk pengecoran baja terus menerus untuk menjadi teknologi produksi massal, tetapi kemudian dengan desain yang berbeda dari pengecoran rol kembar yang telah diterapkan pada paduan ringan pada skala industri.
Dalam perkembangan selanjutnya, Bessemer kemudian menerapkan tundish dengan stopper untuk retensi terak. Cetakan 250 mm x 250 mm di bawah tundish menggabungkan ram hidrolik untuk mendorong ingot ke atas untuk penggulungan langsung ingot yang dimaksudkan tanpa pemanasan ulang. Ini adalah pendahuluan untuk menutup ujung bawah cetakan dengan dummy bar.
Goeran Fredrik Goeransson dari Swedia memperkenalkan sendok bersumbat untuk mentransfer baja cair dari bejana peniup ke lubang penuangan melalui kerekan pada tahun 1858. Ini digantikan oleh Henry Bessemer pada tahun 1859 dengan perangkat tipe ayun yang merupakan menara sendok pertama. Gerbang geser sendok pertama dibuat pada tahun 1885 oleh David D Lewis.
Langkah selanjutnya dalam pengembangan pengecoran kontinu dilakukan oleh Benjamin Atha pada tahun 1886. Sesuai dengan aplikasi patennya, cetakan tanpa dasar yang tinggi, berpendingin air, dan tanpa dasar terhubung langsung dengan tundish sementara batang tiruan menampilkan kepala berbentuk cakar dan mengekstraksi hasilnya. billet logam sebentar-sebentar dengan gulungan penarikan yang digerakkan. Metode ini digunakan untuk produksi semi komersial billet berukuran 100 mm persegi pada awal abad kedua puluh, tetapi tidak berhasil diproduksi secara massal. RM Daelen secara independen mematenkan pada tahun 1889 peralatan serupa (tidak benar-benar digunakan) dengan pemotongan geser dengan cepat.
Kastor pertama yang dibuat oleh pembuat mesin asli, Arthur McKee Co. dari Cleveland, Ohio, pada tahun 1915 telah dirancang oleh John T Rowley dari AS dengan tekuk dan tidak dapat ditekuk dan dengan ukuran billet 45 mm x 45 mm hingga 75 mm x 75 mm dengan panjang mulai dari 10 m hingga 50 m (tanpa dipotong dengan cepat). Ada kontrol panjang yang tidak menentu sebagai akibat dari gesekan cetakan yang berlebihan yang menyebabkan cangkang lengket dan robek secara acak.
Konsep untuk membalas cetakan pendek ke atas dan ke bawah untuk mengurangi gesekan cetakan dipatenkan oleh Cornelius W. van Ranst dari AS pada tahun 1921. Siegfried Junghans dari Jerman pertama kali menerapkan osilasi cetakan pada tahun 1930-an. Mesin pengecoran kontinyunya awalnya digunakan di Wieland-Werke untuk pengecoran kuningan. Cetakan terdiri dari tabung tembaga terbuka di kedua sisi dan dikelilingi oleh jaket air. Logam cair diumpankan dari atas, dan logam padat ditarik oleh gulungan dari bawah. Dengan sistem khusus, pengumpanan logam cair disesuaikan dengan kecepatan penarikan sedemikian rupa sehingga tingkat logam cair dipertahankan konstan dalam cetakan. Ini adalah bagian penting dari teknologi dan contoh nyata bahwa proses CC menawarkan keuntungan otomatisasi dan kontrol. Cetakan dilumasi dan diberi gerakan osilasi naik turun untuk mencegah menempelnya logam padat ke dinding cetakan. Fitur ini akhirnya diadopsi untuk pengecoran baja terus menerus. Gergaji terbang ditempatkan di lubang di bawah instalasi untuk pemotongan terus menerus dari billet ke panjang yang dibutuhkan. Skema semacam itu telah berhasil dan digunakan secara luas untuk pengecoran tembaga, dan paduan aluminium secara terus menerus di Jerman, AS, dan kemudian Uni Soviet. Proses Junghan diterapkan pada magnesium dari tahun 1937 dan seterusnya untuk pengecoran billet bulat berdiameter 200 mm untuk ekstrusi dan pelat dengan dimensi hingga 100 mm x 600 mm. Gambar. 2 menggambarkan metode Junghans casting terus menerus. Kemudian, Junghans menambahkan penyemprotan air langsung ke billet dan membuat banyak inovasi terkait sistem penyaluran dan distribusi logam cair yang tepat.
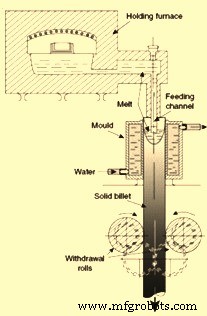
Gbr 2 Metode pengecoran kontinu Junghan
Dibandingkan dengan pengecoran cetakan permanen yang digunakan sebelumnya, metode Junghans memiliki keuntungan sebagai berikut.
- Proses yang benar-benar berkelanjutan dengan kemungkinan otomatisasi tingkat lanjut yang memungkinkan peningkatan produktivitas dengan lebih sedikit tenaga kerja
- Rejim casting yang dapat direproduksi yang memungkinkan kualitas billet yang dapat direproduksi
- Pengisian bagian tengah billet yang lebih baik dengan peningkatan kesehatan billet
- Struktur yang lebih seragam di seluruh billet
- Penghilangan gas yang lebih baik selama pengecoran melalui bagian cair dari billet
- Lebih sedikit bahan bekas
Namun metode Junghans tidak menyelesaikan semua masalah pengecoran cetakan permanen, terutama karena ekstraksi panas yang dominan melalui dinding cetakan. Akibatnya, bah billet itu dalam, cangkang yang dipadatkan tunduk pada gradien termal yang tinggi, dan pembentukan celah udara memerlukan pemeliharaan kecepatan pengecoran yang rendah atau, dengan kata lain, waktu pemadatan yang lebih lama. Billet yang lebih besar (diameter 300 mm – 500 mm) dicirikan dengan struktur dan komposisi kimia yang tidak homogen (segregasi makro). Cetakan panjang yang diperlukan untuk pendinginan yang tepat membutuhkan permukaan bagian dalam yang sangat halus.
Untuk menghilangkan kekurangan ini, perlu dikembangkan suatu teknologi, di mana panas akan diekstraksi terutama melalui bagian padat dari pengecoran. Akibatnya, bak penuangan harus lebih dangkal dengan profil pemadatan harus lebih rata. Segregasi makro, struktur dalam homogenitas, dan tekanan radial perlu lebih sedikit diucapkan. Kebutuhan ini dipenuhi dengan teknologi baru yang dikembangkan hampir secara bersamaan dan independen di Jerman dan Amerika Serikat. Teknologi ini dikenal sebagai 'teknologi direct chill (DC)'. Teknologi ini segera dikomersialkan dan digunakan dalam skala industri. Proses pengecoran DC sesuai teknologi adalah sebagai berikut.
Logam cair dituangkan dari atas ke dalam cetakan berpendingin air yang relatif pendek dan terbuka, yang pada awalnya ditutup dari bawah oleh balok tiruan yang dihubungkan dengan sistem penurun hidrolik atau mekanis. Setelah tingkat lelehan dalam cetakan mencapai tingkat tertentu, ram diturunkan dan bagian padat dari billet diekstraksi ke bawah. Laju aliran logam cair dan kecepatan pengecoran diatur sedemikian rupa sehingga tingkat cairan dalam cetakan tetap konstan. Segera setelah cangkang padat muncul dari bagian bawah cetakan, air dioleskan ke permukaan dalam bentuk semprotan atau film air. Pendinginan billet padat selanjutnya diintensifkan dengan menurunkannya ke dalam lubang berisi air (yang juga membuat proses lebih aman, karena logam cair, jika terjadi kebocoran, didinginkan dengan cepat dalam sejumlah besar air). Prosesnya semi-kontinyu. Segera setelah ram mencapai posisi terendah di lubang, pengecoran dihentikan, dan billet dikeluarkan dari lubang. Casting DC memiliki fitur unik yang membuatnya sangat berbeda dari teknologi casting yang digunakan sebelumnya.
Pemadatan terjadi pada lapisan tipis coran di dalam dan di bawah cetakan. Selama tahap pengecoran yang stabil, bentuk dan dimensi daerah ini tetap konstan dan dapat direproduksi dari satu panas ke panas lainnya. Dengan mengontrol distribusi logam cair selama memberi makan cetakan, pendinginan langsung di bawah cetakan, dan kecepatan pengecoran, bentuk dan dimensi daerah pemadatan dapat dipertahankan dalam batas optimal. Karena bentuk dan dimensi ini menentukan gradien termal dan bertanggung jawab atas retak, segregasi makro, dan homogenitas struktur, terjadinya cacat ini juga dapat dikontrol. Pengecoran DC memiliki keuntungan sebagai berikut dibandingkan metode casting Junghan.
- Segregasi garis tengah jauh berkurang
- Peningkatan kepadatan bagian tengah billet
- Struktur yang lebih halus dan homogen dengan sifat mekanik yang lebih baik
- Kualitas permukaan lebih baik
- Biaya operasi lebih rendah
Mesin CC pertama untuk logam non-ferrous dipasang oleh Rossi, seorang pengusaha, pada tahun 1937 di Scovill Manufacturing Co. di Waterbury menerapkan beberapa proses CC saat itu. Kastor kontinu (Gbr 3), dengan cetakan berosilasi ditambah pendinginan langsung dengan semprotan air di bawah tampak agak sederhana tetapi sistem yang rumit untuk penyediaan dan pengumpanan logam cair diimplementasikan. Ini termasuk (i) transfer logam cair terselubung sepenuhnya dari sendok melalui corong ke dalam dua bejana induksi yang dipanaskan dan diinertisasi, diatur secara paralel, (ii) dari sana, transfer logam cair terselubung ke dalam bak pengumpanan perantara kecil dan inertisasi oleh gas inert tekanan (memastikan retensi terak lengkap) melalui saluran resistensi yang dipanaskan, dan dilengkapi dengan indikator ketinggian logam, dan (iii) kemudian, umpan gravitasi logam cair melalui saluran pemanas resistensi lain ke dalam cetakan terselubung gas. Rossi telah menjamin operasi kastor tanpa gangguan selama tujuh hari yang dicapai sejak awal kastor kontinu.
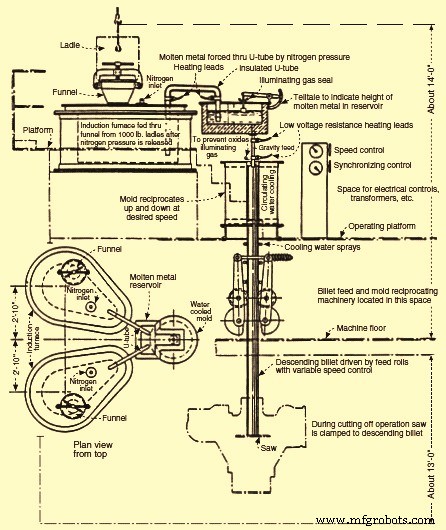
Gbr 3 kastor Rossi dengan cetakan berosilasi
Dirangsang oleh contoh sukses industri nonferrous ini, upaya secara bertahap diintensifkan untuk menerapkan teknologi CC pada baja juga. Namun, sebagian besar perkembangan tersebut sangat dibatasi pada tahun-tahun selama dan tak lama setelah perang dunia kedua. Sangat sedikit detail dan detail operasional yang muncul selama periode ini karena lingkungan kerahasiaan umum selama periode tersebut. Edward R. Williams, presiden 'Vulcan Mould and Iron Co.' menggunakan cetakan yang panjang dan stasioner dan berusaha mengurangi gesekan cetakan dengan penarikan untai yang terputus-putus. Aplikasi patennya termasuk dukungan untai roller apron yang diperlukan dalam pengecoran bagian pelat. Dia bersama dengan Republic steel memulai kastor percontohan besar pada tahun 1942 untuk billet ukuran 100 mm x 100 mm serta lembaran mini ukuran 75mm x 215 mm. Unit percontohan lebih lanjut dibangun dengan Babcock dan Wilcox pada tahun 1948 yang dilengkapi dengan fitur-fitur canggih seperti kontrol level cetakan otomatis dan pengawasan TV.
Berdasarkan cetakan tetap stasioner, banyak upaya kontemporer serupa dimulai kemudian di Amerika Serikat, di Inggris Raya, di Rusia (kemudian Uni Soviet), di Jepang, di Austria, dan di Prancis. Upaya pengecoran ini terganggu oleh gesekan cetakan dan karenanya kurang berhasil daripada pengecoran pilot awal baja dengan cetakan Junghans- Rossi yang berosilasi. Pada tahun 1949 Junghans memulai kastor percontohannya sendiri, diberi makan oleh konverter I ton Bessemer. Setelah memulai kastor ia menandatangani perjanjian kerjasama dengan Mannesmann, yang memulai kastor percontohan mereka di Huckingen pada tahun 1950. Pada tahun 1952, pengembang CC Jerman dan Austria bergabung, kemudian menominasikan Demag sebagai pembuat mesin mereka pada tahun 1956, yang mengarah ke grup akronim DMB, Demag- Mannesmann- Boehler.
Rossi yang ditinggal sendiri, mensuplai mesin pengecoran baja pertamanya, dibangun oleh Koppers Co. yang dimulai di Allegheny Ludlum pada tahun 1949. Kastor ini untuk bagian billet bulat ukuran diameter 150 mm dan mini slab ukuran 75 mm x 380mm. Rossi memberikan jaminan untuk produktivitas kastor sebesar 20 ton per jam serta untuk kualitas produk. Kastor ini dianggap sebagai percobaan pertama pada kastor komersial untuk baja. Kastor ditunjukkan pada Gambar 4. Selain fitur yang terlihat pada Gambar 4, kastor ini memiliki selubung inert dari tundish dan cetakan serta ketahanan pemanasan awal dari tabung tuang yang tidak terendam. Untuk aplikasi akhirnya dari submerged entry nozzle (SEN) ke bagian pelat tipis, Rossi mengusulkan dan mematenkan setengah cetakan atas bentuk corong tetapi dia tidak menggunakannya.
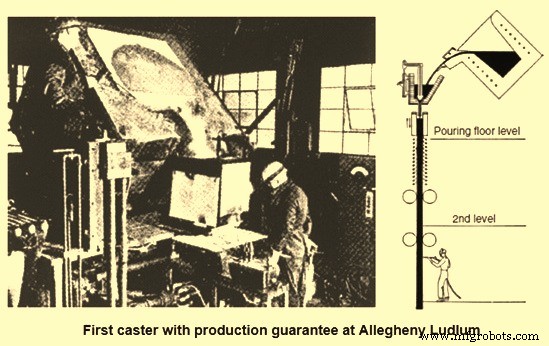
Gbr 4 Kastor pertama dengan jaminan produksi
Rossi membentuk perusahaan teknik 'Continuous Metalcast Inc. dengan Allegheny dan Koppers di antara pemegang saham dan menerima empat pesanan lagi dari pembuat baja khusus di AS, Inggris, Swedia, dan Prancis. Untuk menangani bisnis luar negeri, Concast AG, Zurich, Swiss didirikan oleh Rossi pada tahun 1954. Jadi dua kelompok saingan utama muncul dalam desain dan pasokan kastor pada awal industrialisasi CC, selain banyak upaya pembangunan mesin dengan kapasitas yang lebih kecil. Pemahaman tertentu antara kedua kelompok tercapai setelah penerapan konsep cetakan melengkung ketika kedua konsorsium DMB dan kelompok Concast membentuk perusahaan patungan pada tahun 1963 bernama MBC (Mannesmann-Boehler-Concast) di Zurich.
Awalnya pengembangan CC di baja difokuskan pada pembuatan baja khusus di mana potensi penghematan hasil memerlukan keuntungan biaya terbesar. Kapasitas sendok yang lebih kecil juga lebih kompatibel dengan tingkat keluaran kastor yang lebih rendah. Hambatan lebih lanjut untuk mengadopsi pengecoran kontinu oleh produsen besar adalah karena upaya yang gagal dalam memproduksi baja rimming dengan kualitas permukaan yang dapat diterima. Jadi upaya awal dalam pengecoran slab terbatas pada produksi baja pelat baja mangan-silikon (Mn-Si). Hanya konversi ke aluminium (Al) membunuh baja dan secara paralel peningkatan kualitas permukaan untai membuka jalan untuk aplikasi yang lebih luas dari pengecoran kontinyu untuk produk datar dan panjang. Dalam hal ini, pengembangan dalam pembuatan baja sekunder juga menjadi prasyarat penting, sama pentingnya baik untuk produktivitas kastor maupun kualitas produk.
Dalam perkembangan mesin pengecoran kontinu, beberapa jenis kastor telah direalisasikan dengan perbedaan tinggi desain yang signifikan (Gbr 5). Beberapa dari jenis ini memiliki produktivitas kastor yang terbatas baik karena panjang penyangga yang terbatas (kastor vertikal) atau karena kecepatan pengecoran yang dibatasi oleh gesekan cetakan yang tinggi (kastor horizontal). Selain itu, terdapat juga perbedaan karakteristik dalam hal kualitas produk.
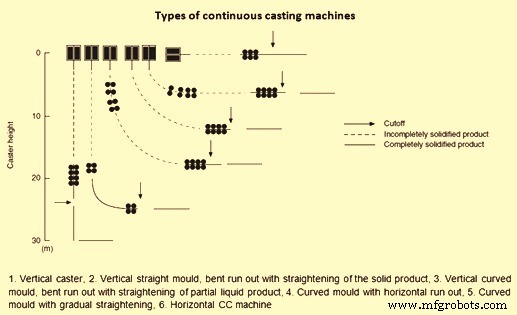
Gbr 5 Jenis mesin continuous casting
Mesin pengecoran vertikal adalah desain mesin alami, pengecoran dengan gravitasi dan juga memastikan struktur makro simetris; tetapi produktivitas kastor sangat dibatasi oleh ketinggian alat berat. Oleh karena itu, beberapa upaya dalam sejarah CC patut diperhatikan untuk memperpanjang panjang alat berat pada ketinggian bangunan rendah dengan menekuk dan meluruskan untai, mis. kastor billet oleh Rowley dan proposal yang lebih maju oleh Tarquinee dan Scovill. Untuk mencegah keretakan bagian dalam, beberapa aturan untuk desain kastor, berdasarkan regangan kritis dan laju regangan pada antarmuka padat/cair telah dikembangkan yang menghasilkan zona pembengkokan dan pelurusan yang berbeda yang memanjang pada beberapa pasangan roller.
Dengan munculnya prinsip pengecoran cetakan melengkung, yang diperkenalkan secara bersamaan oleh percobaan pabrik perintis di Mannesmann Huckingen dan Von Moos Stahl pada tahun 1963, ketinggian bangunan yang dibutuhkan berkurang secara substansial. Jenis kastor ini memulai pertumbuhan pesat aplikasi CC dalam hal pengecoran terus menerus dari billet dan mekar, terutama di toko pengecoran billet kecil yang dapat menggunakan bangunan yang ada. Dalam pengecoran slab, bagaimanapun, meluasnya penggunaan desain cetakan melengkung terhenti dalam beberapa tahun terakhir karena akumulasi seperempat pita yang ditekankan dari inklusi makro dan / atau gelembung argon. Oleh karena itu, selain mesin pengecoran baru yang sekarang dibuat secara eksklusif sebagai jenis cetakan lurus/bengkok, mesin cetakan lengkung yang ada semakin banyak diubah.
Sejak awal pengembangan CC, perhatian utama adalah kontrol suhu baja cair. Ini merupakan kendala utama untuk kapasitas sendok kecil dengan permukaan yang besar untuk rasio volume. Sementara kastor percontohan awal diberi makan langsung dari tungku peleburan atau penahan, ini tidak praktis untuk operasi skala besar. Salah satu pendekatan sebelumnya yang dilakukan oleh Halliday di pabrik baja Barrow di Inggris dalam arah ini adalah penggunaan sendok tuang bibir tertutup yang dapat dipanaskan selama pengecoran dengan pembakar can-jet melalui tutup sendok, memungkinkan waktu pengecoran hingga 2 jam dari sendok 7 ton. Halliday juga bersikeras pada pemanasan awal sendok suhu tinggi. Untuk kapasitas yang lebih besar, sendok tuang bibir tidak praktis sehingga sendok dengan kontrol aliran stopper diperkenalkan. Namun, penggunaan kontrol stopper tidak sesuai dengan peningkatan waktu tinggal logam. Oleh karena itu, kemajuan besar dalam keandalan operasional dan produktivitas kastor dicapai dengan penerapan gerbang geser sendok.
Sejak 1980-an sejumlah besar perkembangan telah terjadi untuk meningkatkan kinerja teknologi pengecoran kontinyu untuk baja. Perbaikan ini telah terjadi dalam perawatan sendok baja cair, sendok ke tundish dan transfer tundish ke cetakan logam cair, dalam tundish (metalurgi tundish), dalam cetakan dan pendinginan primer (pengadukan elektro-magnetik dll.), dalam pendinginan sekunder dan dukungan logam cor (pengadukan elektro-magnetik dan pendinginan kabut udara, dll.), pemotongan dan pendinginan baja cor (tempat tidur pendingin tipe pergantian), dan otomatisasi dan kontrol proses. Gambar 6 memberikan contoh khas sistem pakar dan pengadukan elektro-magnetik.
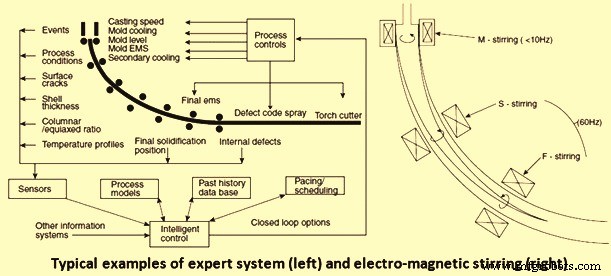
Gbr 6 Contoh umum sistem pakar dan pengadukan elektro-magnetik