Pengecoran billet baja terus menerus
Pengecoran billet baja terus menerus
Pengecoran baja terus menerus adalah proses di mana baja cair terus menerus dipadatkan menjadi untaian logam. Bergantung pada dimensi untaian, produk setengah jadi ini disebut lembaran, mekar atau billet. Billet baja memiliki penampang persegi dengan satu sisi biasanya 150 mm atau kurang. Ini adalah bahan pakan untuk penggulungan baja di pabrik bagian ringan, pabrik batang, dan pabrik batang kawat. Billet baja juga digunakan dalam penempaan produk tertentu.
Proses pengecoran kontinyu ditemukan pada 1950-an dalam upaya untuk meningkatkan produktivitas produksi baja. Sebelumnya hanya tersedia pengecoran ingot yang masih memiliki manfaat dan kelebihan tetapi tidak selalu memenuhi tuntutan produktivitas. Sejak itu, pengecoran kontinu telah dikembangkan lebih lanjut untuk meningkatkan hasil, kualitas, dan efisiensi biaya.
Pengecoran baja terus menerus sekarang menjadi metode pilihan oleh semua produsen baja menggantikan metode lama pengecoran ingot. Dibedakan dengan banyak kelebihannya, proses ini telah melalui banyak perbaikan dan masih menjadi subjek studi yang luas baik secara empiris maupun matematis. Pengecoran billet baja kontinyu adalah salah satu jenis pengecoran kontinu yang diadopsi dalam industri baja, dimana billet baja diproduksi secara terus menerus dan bersamaan. Jenis proses ini membutuhkan kontrol parameter operasi yang besar untuk menghasilkan billet yang baik dan berkelanjutan. Prosesnya dapat dibagi menjadi beberapa langkah dimulai dengan menuangkan baja cair panas dari tungku pembuatan baja ke dalam ladle, di mana kimia baja diatur dalam pembuatan baja sekunder, kemudian dituangkan ke distributor (tundish), dan dari distributor ke cetakan pengecoran. Pemadatan baja dimulai dalam cetakan pengecoran tembaga dengan pendinginan tidak langsung, area yang menjadi sasaran banyak penelitian. Dari cetakan, billet cor mengalami pendinginan sekunder dengan semprotan air.
Produksi baja billet mendapat dorongan pada tahun 1960 karena saat ini konsep mini-mill dikembangkan dengan menggabungkan pembuatan baja listrik dengan pengecoran kontinyu dan struktur organisasi ramping untuk menghasilkan budaya baru yang menguntungkan dari produksi baja. Produsen billet meskipun sangat menguntungkan tertinggal dalam produksi produk cor terus menerus berkualitas tinggi.
Sebuah survei yang dilakukan pada tahun 1980-an telah menunjukkan bahwa desain cetakan dan pengoperasian pengecoran terus menerus dari billet tidak standar dan setiap perusahaan melakukan sesuatu yang berbeda. Brimacombe dan rekan kerja di akhir 1970-an mulai mengeksplorasi kerja bagian dalam cetakan billet dan membangun hubungan antara desain cetakan, parameter operasi, dan kualitas billet dengan bantuan model matematika dan pengukuran di pabrik. Karena upaya ini, pengecoran billet bergerak menuju desain standar dan parameter operasi yang menghasilkan peningkatan substansial dalam kualitas billet cor. Hal ini diungkapkan oleh survei baru yang dilakukan pada tahun 1994 dan diketahui bahwa produsen billet telah mulai memasok billet kualitas batang khusus ke sektor otomotif dengan berhasil memenuhi persyaratan kualitas yang ketat. Sejak saat itu, pemasok mesin pengecoran billet telah memeriksa kembali kecepatan pengecoran untuk pengecoran terus menerus dari billet, sehingga memunculkan sejumlah perkembangan baru yang ditujukan untuk produktivitas yang lebih tinggi. Fitur umum dari teknologi pengecoran kecepatan tinggi untuk billet adalah peningkatan panjang cetakan.
Berbagai macam mesin pengecoran kontinu billet sekarang tersedia. Mesin-mesin ini memiliki radius pembengkokan yang berbeda, dari untai tunggal hingga delapan untai dan memiliki kecepatan pengecoran hingga 6 m/menit. Kastor billet untai tunggal dengan radius 6 m ditunjukkan pada Gambar 1, sedangkan dua mesin pengecoran billet delapan berdiri ditunjukkan pada Gambar 2.
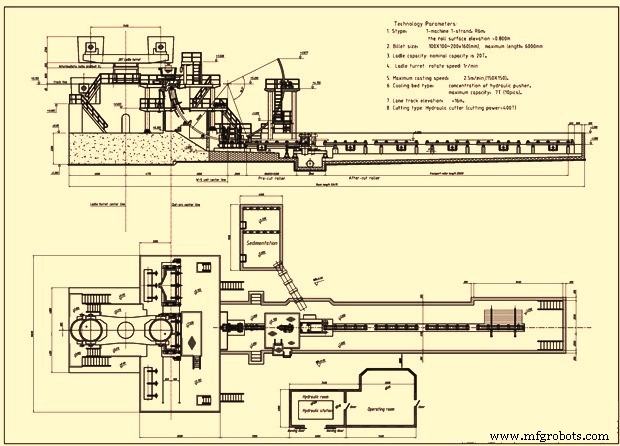
Gbr 1 Kastor billet untai tunggal
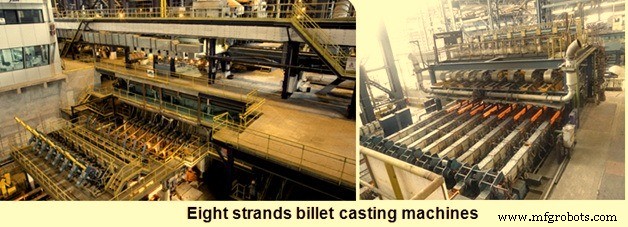
Gbr 2 Mesin pengecoran billet delapan untai
Proses pengecoran terus menerus dari billet baja dijelaskan di bawah ini.
Sendi baja
Baja cair dipindahkan dari fasilitas pembuatan baja ke mesin pengecoran billet di sendok baja. Selama transfer ini ada peluang yang tersedia untuk kontrol kebersihan, komposisi dan suhu baja cair. Jika peluang ini tidak dimanfaatkan maka baja cair yang dikirim ke mesin pengecoran billet kotor dan terlalu panas atau terlalu dingin. Casting billet berkualitas kemudian menjadi tugas yang jauh lebih sulit.
Selama pemindahan baja cair ke kastor billet, masalah utama adalah penyerapan oksigen (O2) dari udara, terak tungku, dan lapisan refraktori sendok. Hal ini diperlukan untuk meminimalkan pengambilan O2 selama setiap langkah transfer. Luapan terak dalam sendok baja harus dicegah dari tungku pembuatan baja pada akhir penyadapan. Permukaan baja dalam sendok harus dilapisi dengan terak sintetis (i) untuk mencegah penyerapan O2 dari udara, (ii) untuk penyerapan inklusi non-logam, dan (iii) untuk meminimalkan panas. kehilangan. Di beberapa pabrik, sendok baja ditutupi di bagian atas dengan penutup sendok. Selanjutnya selama pengecoran, sendok baja dilengkapi dengan tabung tahan api untuk mencegah pengambilan O2 saat baja dituangkan ke dalam tundish. Aliran baja dari sendok ke tundish dikendalikan dengan katup gerbang geser. Di beberapa pabrik, berat sendok baja terus menerus diukur dengan bantuan sel beban.
Biasanya pembilasan baja cair dengan gas argon (Ar) inert dilakukan untuk menyeragamkan suhu baja. Kontrol suhu baja cair penting untuk mengontrol struktur cor serta untuk pencegahan masalah operasi seperti pembentukan tengkorak di sendok dan tundish, break-out dll. Laju aliran dan durasi pembilasan Ar perlu dikendalikan karena pelepasan gas dari baja membawanya ke dalam kontak dengan udara kecuali tindakan khusus diambil.
Tundish
Tundish harus memainkan banyak peran selama pengecoran terus menerus dari billet baja. Ini bertindak sebagai distributor, pemakaian baja ke beberapa helai mesin pengecoran billet. Ini juga memfasilitasi kontrol aliran baja cair ke dalam cetakan karena memiliki kepala hidrostatik yang konstan dan lebih rendah daripada sendok baja. Hal ini penting terutama selama start-up dari kastor, karena tundish dapat diisi dengan baja ke tingkat kondisi tunak normal sebelum memulai penuangan baja cair ke dalam cetakan. Fenomena penting lainnya yang dapat terjadi di tundish adalah mengambangnya inklusi yang membantu kebersihan produk cor. Selanjutnya tundish juga dapat digunakan sebagai reaktor, untuk penambahan agen seperti kalsium (Ca), untuk kontrol morfologi inklusi.
Karena fungsi di atas, bentuk dan ukuran tundish ditentukan terutama oleh kebutuhan untuk mengontrol aliran fluida. Karena ukuran panas, dimensi billet cor, jumlah untaian, jarak untai, dan laju penuangan berbeda dari satu pabrik ke pabrik lain; desain tundish optimal yang unik tidak ada. Namun, berikut ini adalah fitur utama dari tundish yang dirancang dengan baik.
- Desain tundish adalah untuk memaksimalkan inklusi yang mengapung. Untuk volume tundish ini harus besar, meskipun faktor-faktor yang meringankan lainnya membatasi ukurannya. Sebagai contoh, jika panas yang memiliki komposisi berbeda harus dicor secara berurutan, tanpa mengganggu operasi pengecoran, volume baja 'campuran' dalam tundish harus diminimalkan karena baja campuran tidak bermutu dan dapat menunjukkan kehilangan hasil. .
- Waktu tinggal baja yang mengalir ke masing-masing helai harus sama untuk memastikan kualitas kualitas baja.
- Hubungan pendek baja melalui tundish harus diminimalkan, yaitu, sejauh mungkin, aliran sumbat harus dicapai.
- Pola aliran dalam tundish memungkinkan sebagian besar baja bergerak mendekati permukaan di mana inklusi yang mengambang dapat diserap oleh terak tundish. Hal ini penting karena jarak yang dapat ditempuh oleh inklusi hanya dengan daya apung kecil dalam waktu yang tersedia di tundish.
- Volume mati harus diminimalkan karena secara efektif mengurangi waktu tinggal baja.
- Turbulensi dari aliran ladle yang masuk perlu diisolasi, terutama saat aliran terbuka mengalir dari tundish ke mould. Turbulensi mempengaruhi kekasaran aliran tundish dan masuknya gas di kolam cetakan.
- Kedalaman tundish harus cukup, lebih dari sekitar 500 mm, untuk mencegah pusaran pada sumur nosel, yang dapat menarik terak lebih rendah di kolam cetakan.
Penentuan desain tundish yang optimum memerlukan spesifikasi bentuk, dimensi dan letak serta ukuran alat pengatur aliran internal seperti bendungan dan bendung. Ini biasanya dicapai dengan penggunaan model air dan/atau model matematika secara ekstensif.
Satu aspek lagi dari desain tundish yang mempengaruhi produktivitas dan kualitas adalah pencegahan oksidasi ulang baja cair. Jadi terak penutup dengan kapasitas penyerapan inklusi diterapkan untuk mencegah penyerapan O2 dari udara. Baja yang mengalir dari tundish ke cetakan selanjutnya dilindungi dengan melewatkannya melalui tabung tahan api atau selubung gas inert. Yang terakhir ini digunakan ketika casting billet bagian kecil di mana rongga cetakan terlalu kecil untuk menampung tabung tahan api. Untuk pengecoran billet berkualitas rendah, baja biasanya dituangkan melalui udara tanpa memperhatikan oksidasi ulang. Tundish dilapisi dengan bahan tahan api yang harus inert terhadap baja. Juga de-oksidan dalam baja seperti Ca atau aluminium (Al), misalnya, tidak boleh bereaksi dengan oksida yang terdiri dari lapisan tahan api. Di beberapa pabrik, tundish dipanaskan terlebih dahulu untuk mengusir konstituen yang mudah menguap dalam jenis pelapis tertentu, yang dapat menyumbangkan hidrogen ke baja, dan juga untuk kontrol suhu baja yang lebih baik.
Masalah utama dengan operasi tundish adalah penyumbatan nozel penuangan oleh inklusi padat seperti alumina (Al2O3). Meskipun inklusi kecil dibandingkan dengan diameter nosel, mereka biasanya menempel pada refraktori melalui lapisan batas dan akhirnya, dengan penumpukan berturut-turut, membentuk jembatan melintasi nosel yang menghalangi aliran. Masalahnya parah untuk pengecoran billet kecil, yang membutuhkan nozel berdiameter lebih kecil. Saat casting bagian yang lebih besar menggunakan nozel yang lebih besar, Ar sering disiram terus menerus melalui nosel untuk mencegah penumpukan yang berlebihan. Penyumbatan nozzle tidak menjadi masalah jika inklusi dalam keadaan cair. Oleh karena itu untuk pengecoran bebas masalah baja Al yang terbunuh ke dalam billet, Ca ditambahkan dalam jumlah yang tepat untuk menghasilkan inklusi kalsium aluminat.
Laju penuangan melalui nosel tundish dicapai dengan teknik yang berbeda tergantung pada ukuran bagian yang dicor. Untuk bagian yang lebih besar, menggunakan tabung tahan api antara tundish dan cetakan, batang penghenti atau katup gerbang geser biasanya digunakan untuk mengontrol aliran, kontrol aliran otomatis untuk mencapai tingkat meniskus konstan dan kecepatan pengecoran biasanya digunakan. Dalam kasus billet bagian yang lebih kecil, dengan aliran terbuka, biasanya tidak ada kontrol aliran pada tundish. Laju aliran kemudian disesuaikan dengan pemilihan diameter nosel yang sesuai dan pemeliharaan kepala hidrostatik baja tertentu di tundish. Kontrol level meniskus kemudian diperoleh dengan memvariasikan kecepatan casting. Pemeliharaan kepala baja cair di tundish dilakukan baik secara manual atau dengan terus menerus menimbang tundish dengan load cell dan menghubungkan sinyal ke katup gerbang geser pada sendok.
Waktu normal yang dibutuhkan untuk membuang panas baja cair adalah sekitar satu jam, yang harus disamakan dengan waktu 30 sampai 40 menit sampai dengan dua jam yang dibutuhkan untuk suplai panas ke mesin billet casting.
Cetakan
Cetakan adalah 'jantung' dari mesin casting. Ini juga merupakan perangkat utama untuk menghilangkan panas. Fungsi cetakan adalah (i) menghilangkan panas berlebih dari baja cair, (ii) menumbuhkan cangkang padat dengan ketebalan yang cukup, (iii) menampung kumpulan cairan di bawah cetakan tanpa pecah, dan (iv) untuk mendukung cangkang dalam pertumbuhan awalnya. Karena cetakan mengatur pembuangan panas, desain dan pengoperasian cetakan sangat mempengaruhi kualitas internal dan permukaan billet cor. Bebas dari retakan permukaan sangat penting terutama jika billet cor akan diisi panas dalam tungku pemanas ulang untuk penggulungan karena retakan permukaan teroksidasi dan membentuk cacat lapisan oksida selama pengerolan.
Cetakan mungkin lurus atau mungkin memiliki kelengkungan dengan radius 4 m sampai 15 m. Cetakan melengkung digunakan dengan untaian kurva untuk mengurangi ketinggian mesin pengecoran dan biaya modal. Cetakan lurus membantu dalam distribusi inklusi dalam produk cor. Dalam kasus cetakan melengkung, terapung inklusi dapat dijebak secara istimewa oleh bagian depan pemadatan yang berdekatan dengan permukaan radius bagian dalam untuk membentuk pita. Karena ini tidak terjadi pada cetakan lurus, inklusi lebih merata. Sejauh mana kekhawatiran ini berlaku tergantung pada kebersihan baja yang masuk ke cetakan dan persyaratan kualitas yang dibutuhkan untuk billet cor. Bagaimanapun, baja tuang yang meninggalkan cetakan lurus umumnya ditekuk secara bertahap ke orientasi horizontal untuk mengurangi ketinggian kastor. Namun, di beberapa pabrik, cetakan dan daerah sub-cetakan lurus sehingga produk cor tidak mengalami gaya lentur mekanis yang dapat menghasilkan retakan. Dengan cetakan melengkung, untaian baja harus diluruskan ke posisi horizontal sebelum dipotong menjadi panjang.
Terlepas dari apakah cetakannya lurus atau melengkung, desain dasar cetakannya sama. Cetakan tabung digunakan untuk pengecoran terus menerus dari billet baja. Cetakan ini terdiri dari tabung tembaga (Cu) yang diposisikan secara konsentris di dalam baffle baja dengan air pendingin yang mengalir melalui anulus di antara keduanya. Ketebalan dinding tabung Cu berkisar antara 6 mm sampai 20 mm. Cetakan tabung dinding yang lebih tebal digunakan untuk bagian yang lebih besar. Tabung cetakan dibuat dari berbagai tingkat paduan Cu. Paduan Cu yang mengandung fosfor, perak (bantalan perak), atau kromium dan zirkonium adalah bahan yang biasa digunakan untuk tabung cetakan.
Selama pengecoran, cetakan dilumasi dan dibalas untuk mencegah baja menempel pada Cu, yang akan mengakibatkan pecahnya kulit padat. Cetakan berosilasi umumnya mengikuti bentuk gelombang sinusoidal, frekuensi dan amplitudonya disesuaikan untuk memastikan bahwa selama sepersekian detik selama gerakan turun, cetakan bergerak lebih cepat daripada untaian turun. Periode 'strip negatif' ini telah ditemukan mempengaruhi pembentukan tanda osilasi pada permukaan untaian. Pelumas yang digunakan biasanya bergantung pada ukuran bagian yang dicor.
Dalam kasus bagian kecil seperti billet persegi 100 mm, di mana baja dituangkan dalam aliran terbuka dari tundish ke cetakan, minyak lobak atau minyak sintetis digunakan. Minyak dipompa ke piring meminyaki di bagian atas cetakan dari mana ia merembes ke bagian dalam dinding cetakan. Tindakan pelumasan yang tepat dari minyak, yang pirolisis dalam kontak dengan baja cair, tidak terlalu jelas. Saat casting bagian yang lebih besar, baja dimasukkan ke dalam cetakan melalui nosel masuk yang terendam. Dalam hal ini, pelumasan dilakukan dengan menambahkan bubuk cor ke meniskus, di mana ia menyentuh baja, meleleh, dan ditarik ke celah antara cangkang pemadatan dan cetakan berosilasi. Komposisi bubuk yang biasanya terdiri dari oksida, karbon dan kalsium fluorida, disesuaikan untuk mengontrol rentang leleh dan viskositasnya. Tergantung juga pada komposisi adalah konduktivitas termal, dan ketebalan lapisan bubuk cetakan di celah cetakan/baja, yang mempengaruhi laju ekstraksi panas oleh cetakan.
Berbagai minyak seperti nabati, sintetis dan campuran dapat digunakan. Meskipun titik nyala minyak adalah properti kunci, rentang didih, relatif terhadap suhu muka panas maksimum lebih berarti untuk dipertimbangkan secara mendasar. Laju umpan minyak pelumas biasanya dalam kisaran 0,014 hingga 0,17 (nilai tipikal 0,05) mililiter per menit per mm pinggiran cetakan untuk billet persegi 125 mm. Namun, sehubungan dengan kebersihan industri, kualitas billet, dan biaya, semakin rendah tingkat minyak yang dapat dicapai, semakin baik.
Aspek penting sehubungan dengan cetakan mesin billet casting adalah sebagai berikut.
- Panas dari permukaan untai dipindahkan ke air pendingin cetakan melalui serangkaian tahanan termal seperti (i) celah udara yang memisahkan cetakan dan untaian, (ii) dinding cetakan, dan (iii) pendinginan cetakan antarmuka air. Dari jumlah tersebut, celah udara merupakan hambatan terbesar terhadap aliran panas dan menyumbang sebanyak 84% dari total hambatan. Pola penghilangan panas dalam cetakan sangat bergantung pada dinamika pembentukan celah. Kesenjangan antara cetakan dan untaian adalah fungsi kompleks dari beberapa variabel. Selanjutnya dimensi celah bervariasi baik dalam arah memanjang (penarikan) dan melintang, menghasilkan pola penghilangan panas yang tidak seragam. Meskipun banyak cahaya telah diberikan pada mekanisme pembentukan celah, itu masih merupakan fenomena yang kurang dipahami.
- Saat mempelajari profil suhu rata-rata waktu dalam cetakan, terbukti bahwa profil suhu di lokasi yang berbeda serupa, dengan puncak tepat di bawah tingkat logam dan penurunan suhu yang tajam setelahnya. Penurunan suhu berasal langsung dari pengurangan penghilangan panas dengan jarak ke bawah cetakan karena peningkatan celah udara, ketebalan shell dan distorsi cetakan. Terlihat juga bahwa suhu di lokasi sudut jauh lebih dingin daripada lokasi bagian tengah yang sesuai. Ini karena celah cenderung terbentuk pertama di sudut, karena aliran panas dua dimensi, dan menyebar ke seluruh permukaan.
- Fluks panas memuncak pada tingkat meniskus dan menurun setelahnya, karena peningkatan lebar celah udara. Tingkat karbon dalam baja juga berperan pada perpindahan panas cetakan karena penyusutan yang terkait dengan perpindahan fase delta-gamma.
- Perakitan cetakan tabung yang digunakan dalam pengecoran billet lebih sederhana dalam desain tetapi lebih rentan terhadap distorsi termal selama operasi karena cetakan tidak didukung di seluruh panjangnya. Selama operasi, tabung cetakan dikenai pola penghilangan panas yang tidak seragam dan memperoleh distribusi suhu yang tidak seragam. Cetakan billet terdistorsi sebagai respons terhadap perubahan suhu, dan perilaku termo-mekanisnya terkait dengan sejumlah masalah kualitas. Juga telah ditemukan bahwa bagian dari distorsi total selama operasi adalah permanen, karena besarnya tegangan yang timbul dari pemuaian termal diferensial, ditambah dengan pengekangan fisik dari sistem pendukung cetakan dan geometri tabung cetakan itu sendiri. Faktor-faktor yang mempengaruhi lancip negatif dan tonjolan puncak, serta posisinya relatif terhadap bagian atas cetakan termasuk kecepatan air pendingin, kualitas air, tingkat logam, posisi kendala relatif terhadap bagian atas cetakan, ketebalan dinding dan jenis. dukungan tabung cetakan.
- Variabel proses memiliki efek nyata pada perpindahan panas. Kandungan karbon baja, mould taper, praktik penuangan, pelumasan, dan kecepatan pengecoran merupakan variabel proses utama yang berpengaruh pada perpindahan panas.
- Selain ekstraksi panas, osilasi cetakan dan pelumasan merupakan dasar dari pengecoran kontinyu. Gesekan cangkang cetakan harus diminimalkan untuk menghilangkan baja yang lengket, sobek, dan retak. Osilator adalah mesin sederhana yang membalas cetakan billet untuk membantu mencegah baja menempel pada dinding cetakan. Cetakan biasanya berosilasi dalam mode sinusoidal, dengan parameter frekuensi stroke dan osilasi yang khas masing-masing 10 mm dan 2 hertz (Hz). Parameter osilasi cetakan untuk meminimalkan lengket dan kedalaman tanda osilasi adalah waktu langkah dan strip negatif. Waktu strip negatif didefinisikan sebagai periode waktu di mana cetakan bergerak lebih cepat ke bawah daripada tingkat penarikan untai. Timbal cetakan adalah jarak cetakan bergerak melewati cangkang selama strip negatif. Untuk pengecoran billet, lead cetakan yang direkomendasikan dan nilai waktu strip negatif masing-masing adalah 3-4 mm dan 0,12 – 0,15 detik. Mesin pengecoran dengan waktu strip negatif di bawah 0,1 detik dan timah cetakan di bawah 2-3 mm rentan terhadap lengketnya cangkang cetakan terutama jika meniskus berfluktuasi. Ujung cetakan yang lebih besar dari 5 mm dapat menyebabkan tanda osilasi yang lebih dalam dan tidak seragam.
- Permukaan continuous cast billet dicirikan oleh adanya tanda osilasi yang terbentuk secara periodik pada meniskus akibat adanya timbal balik cetakan. Setiap tanda osilasi adalah depresi lokal dari baja dan oleh karena itu menyebabkan peningkatan secara lokal pada lebar celah baja/cetakan. Akibatnya, penghilangan panas secara lokal berkurang di sekitar tanda osilasi. Tergantung pada kedalaman tanda osilasi, ketebalan cangkang yang berkurang secara lokal, retakan atau retakan permukaan melintang mungkin muncul. Pitch dari tanda osilasi pada permukaan untai terkait dengan frekuensi siklus osilasi.
- Tirus ke dalam cetakan, yang mengkompensasi penyusutan cangkang pemadatan, bervariasi tanpa lancip ke lancip tunggal dan lancip ganda. Di beberapa pabrik, ada praktik umum tidak hanya menggunakan cetakan yang tidak runcing tetapi juga membalikkan tabung cetakan setelah sejumlah keausan untuk memperpanjang umur tabung. Namun, telah terlihat sekarang bahwa ada pengaruh yang kuat dari lancip cetakan pada kedalaman dan keseragaman tanda osilasi dan, sebagai akibatnya, pada retakan internal yang tidak rata dan di luar sudut. Juga telah terlihat bahwa lancip cetakan di meniskus memiliki efek besar pada penghilangan panas lokal dan keseluruhan dari baja, dengan konsekuensi untuk distorsi cetakan, pelumasan minyak dan kualitas permukaan billet. Perhitungan berdasarkan profil aksial dari penghilangan panas terukur, penyusutan baja padat pendingin, dan distorsi cetakan telah menunjukkan bahwa lancip ganda diinginkan dan kurang parah untuk panas C rendah (, 0,16 %) daripada panas C tinggi.
- Perhitungan distorsi cetakan menunjukkan bahwa ketebalan dinding minimum adalah sekitar 13 mm untuk bagian billet dari 100 mm hingga 150 mm dan meningkat menjadi sekitar 20 mm untuk 200 mm persegi. Ketebalan dinding lebih besar dari 20 mm dapat menyebabkan masalah lengket, jika cetakan dilumasi dengan minyak, karena dinding yang lebih tebal dapat menyebabkan suhu panas permukaan cetakan di dekat meniskus yang melebihi kisaran didih minyak yang biasanya 220 derajat C hingga 350 derajat C. Sehubungan dengan jari-jari sudut dalam, pengalaman pengoperasian menunjukkan bahwa nilai sekitar 3 mm hingga 4 mm sangat membantu dalam meminimalkan retakan memanjang.
- Level meniskus (dari atas tabung cetakan Cu) harus optimal 100 mm hingga 150 mm. Meniskus yang dangkal menyebabkan zona ekspansi termal maksimum tabung cetakan menjadi dekat dengan pelat penahan, yang biasanya menahan tabung di tempatnya. Resistensi pelat penjaga terhadap gerakan tabung cetakan ke luar menghasilkan regangan plastik dan distorsi tabung permanen yang tidak diinginkan. Tingkat meniskus yang terlalu dalam tidak perlu mengurangi waktu tinggal cangkang yang mengeras di dalam cetakan.
- Diinginkan untuk mempertahankan kecepatan air yang tinggi, biasanya di atas 10-11 meter/detik karena alasan (i) permukaan tabung Cu yang didinginkan dengan air harus cukup dingin relatif terhadap titik didih air untuk menekan nukleat mendidih, (ii) permukaan panas tabung Cu tidak boleh melebihi rentang didih minyak pelumas di dekat meniskus, dan (iii) suhu Cu tidak boleh melebihi karakteristik pelunakan, ditentukan oleh waktu pada suhu, dari kadar Cu tertentu karena ini menyebabkan distorsi permanen pada cetakan.
- Ada tiga jenis penyangga cetakan yang digunakan. Mereka adalah (i) penyangga oleh pelat penahan yang dipasang ke dalam slot di keempat sisinya, (ii) pelat penahan pada dua sisi di dekat bagian atas tabung cetakan, dan (iii) penyangga di bagian atas dan bawah tabung cetakan. Dukungan kedua dalam kombinasi dengan tingkat logam dangkal menghasilkan distribusi cetakan yang tidak seragam di sekitar pinggiran tabung. Ini, pada gilirannya, kondusif untuk ketidaksesuaian, dibandingkan dengan jenis dukungan pertama dan ketiga.
- Kualitas air pendingin sangat penting. Bahkan deposit 20 mikrometer memiliki pengaruh buruk pada suhu tabung cetakan. Ini karena endapan, relatif terhadap Cu, menimbulkan hambatan termal yang besar terhadap aliran panas dari tabung ke air pendingin. Hasil paling langsung dari kualitas air yang buruk adalah distorsi cetakan permanen. Sering terlihat bahwa tingkat keparahan endapan tidak sama pada keempat permukaan tabung cetakan. Ini karena kecepatan air pendingin berubah di sekitar pinggiran luar cetakan karena variasi dimensi saluran air. Akar masalahnya adalah toleransi komponen seperti jaket air, tabung cetakan, rumah cetakan, dan bagian perakitan lainnya yang menentukan dimensi saluran air pendingin.
Pendinginan sekunder
Di bawah cetakan mesin pengecoran billet, untaian baja yang bergerak didinginkan oleh tepi semprotan air. Tujuan pendinginan sekunder adalah untuk melanjutkan penghilangan panas dan pemadatan yang dimulai dalam cetakan tanpa menimbulkan tegangan tarik yang cukup besar untuk menyebabkan cacat bentuk, retak permukaan, atau retak internal.
Nozel semprot biasanya dipasang ke header vertikal, atau riser, yang biasanya diposisikan di tengah setiap fase. Paling sering, nozel semprot yang digunakan pada mesin pengecoran billet menghasilkan pola kerucut penuh (bulat atau persegi) meskipun kadang-kadang nozel kerucut berongga juga digunakan. Tepat di bawah cetakan, di mana gulungan kaki sering berada, satu atau dua nozel per permukaan yang memberikan pola V sering digunakan. Panjang ruang semprot dapat bervariasi mulai dari 0,5 m hingga 5 m. Secara konvensional, semprotan air beroperasi berdasarkan prinsip atomisasi tekanan, yaitu, air dipaksa di bawah tekanan melalui lubang atau nosel dan pecah menjadi tetesan. Desain sistem pendingin sekunder untuk mesin billet casting terutama tergantung pada pertimbangan kualitas dan memerlukan pengetahuan tentang faktor-faktor yang mempengaruhi perpindahan panas dengan menyemprotkan pendinginan dengan air. Desain pendingin sekunder tergantung pada tiga aspek penting yaitu (i) efek pendinginan semprot pada generasi cacat pada billet, (ii) penghilangan panas karena semprotan yang tergantung pada variabel seperti tekanan air, jarak berdiri, jenis nosel, suhu permukaan untai, dan fluks air, dan (iii) distribusi air di atas area semprotan sebagai fungsi dari parameter semprotan yang disebutkan di bawah (ii).
Cacat terkait semprotan pada billet cor kontinu adalah retakan tengah, rhomboiditas, dan retak diagonal. Pengaruh pendinginan semprot pada pembentukan cacat dijelaskan di bawah ini.
- Bergantung pada profil aksial dari pendinginan semprot, regangan tarik yang besar dapat dihasilkan dalam cangkang pemadatan karena perubahan gradien termal. Pemanasan ulang billet setelah ruang semprotan adalah penyebab keretakan di tengah jalan.
- Intensitas pendinginan semprot mempengaruhi distribusi suhu lokal melalui shell, yang pada gilirannya mengubah sifat mekanik suhu tinggi dari baja dan kemampuan shell untuk menahan penonjolan karena tekanan ferostatik dari inti cair.
- Pergerakan suhu dari irisan melintang dari cangkang padat, saat bergerak melalui semprotan, dapat mempengaruhi pengendapan fase seperti aluminium nitrida (AlN), yang dapat mengurangi keuletan suhu tinggi. Jika, dalam kondisi ini, cangkang mengalami tegangan tarik yang besar, seperti selama pelurusan, cacat seperti retakan melintang dapat dihasilkan.
Ada hubungan antara laju penghilangan panas oleh semprotan air dan variabel semprotan. Koefisien perpindahan panas semprot dipengaruhi oleh sejumlah besar variabel seperti jenis nosel, jarak nosel ke untai, tekanan air, suhu air, dan suhu permukaan baja. Dari jenis nosel ini, jarak nosel ke untai, dan tekanan air mempengaruhi fluks air semprotan (liter/m2 dtk) yang merupakan variabel semprotan yang paling penting. Di sisi lain suhu air dan suhu permukaan baja mempengaruhi perpindahan panas secara langsung. Di bawah kondisi pengecoran kontinu normal di mana suhu permukaan berkisar dari 1200 derajat C hingga 700 derajat C, suhu permukaan memiliki efek kecil pada koefisien perpindahan panas sedangkan fluks air semprotan memiliki efek terbesar pada koefisien perpindahan panas.
Billet cor setelah pendinginan sekunder bergerak ke bagian pemotongan, di mana billet cor dipotong menjadi panjang yang diinginkan baik dengan geser hidrolik atau dengan obor pemotongan.