Cara Menyetel Frekuensi untuk Pemeriksaan Pemeliharaan Pencegahan
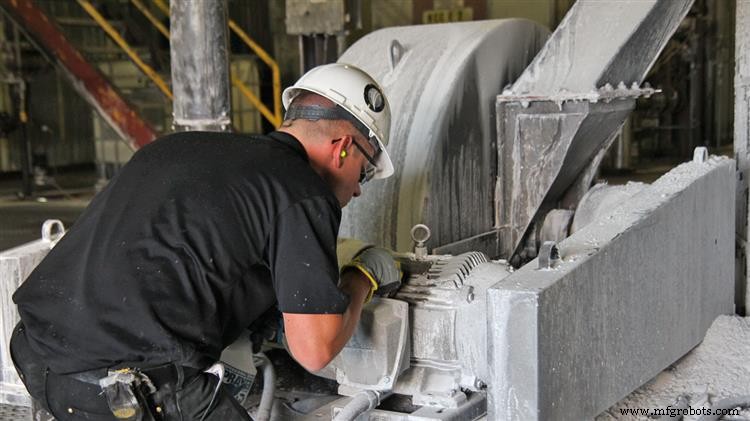
Bagi Anda yang ingin mendalami detail pengaturan pemeriksaan preventive maintenance (PM), mari kita mulai dengan mendefinisikan apa yang saya maksud dengan inspeksi. Inspeksi mencakup semua inspeksi objektif (kami mengukur sesuatu) menggunakan instrumen – misalnya, penganalisis getaran, kamera inframerah, volt meter, pengukur aliran, atau peralatan ultrasonik. Inspeksi juga mencakup semua inspeksi subjektif (lihat-dengar-rasa-bau). Untuk menyetel frekuensi inspeksi, kita perlu memahami apa itu periode pengembangan kegagalan.
Periode pengembangan kegagalan (FDP), juga disebut Kurva Pf oleh beberapa orang, adalah periode waktu dari saat kemungkinan untuk mendeteksi kegagalan sampai kita mengalami kerusakan. Kegagalan adalah ketika sistem atau peralatan beroperasi dengan benar dalam parameter yang diberikan, tetapi menunjukkan tanda-tanda masalah.
Misalnya, pompa sentrifugal mungkin mengalami kavitasi, tetapi masih menyediakan aliran yang diperlukan untuk operasi. Kami mengalami kegagalan tetapi bukan kehancuran. Kavitasi dalam contoh kita pada akhirnya akan berkembang menjadi kerusakan. Kerusakan terjadi ketika pompa tidak dapat menjalankan fungsi yang diinginkan.
FDP adalah perbedaan waktu antara kegagalan dan kerusakan. Jika pompa mulai kavitasi pada pukul 6 pagi dan rusak pada pukul 6 sore. empat hari kemudian, FDP adalah 108 jam.
Frekuensi Pemeriksaan
Frekuensi inspeksi kira-kira harus FDP dibagi dua. Misalnya, jika periode pengembangan kegagalan adalah 14 hari dan kami memerlukan waktu untuk merencanakan dan menjadwalkan pemeliharaan korektif untuk kegagalan itu, saya pikir frekuensi inspeksi yang wajar adalah tujuh hari (FDP/2). Jika frekuensi inspeksi lebih lama dari 14 hari, kami mungkin melewatkan kegagalan dan akan mengalami kerusakan di tangan kami. Jadi aturan praktis kami adalah:
Frekuensi pemeriksaan =FDP/2.
Namun, masalah sebenarnya adalah kita tidak tahu apa itu FDP. Tidak ada standar, tidak ada dokumentasi. Sebagian besar tanaman biasanya tidak memiliki riwayat FDP. Jadi apa yang kamu lakukan? Mari gali lebih dalam dengan beberapa informasi tambahan.
Alat Inspeksi Mengubah FDP
Kita juga perlu memahami bahwa FDP berubah ketika kita memiliki akses ke alat yang lebih baik. Misalnya, kita mungkin dapat mendeteksi masalah dengan bantalan blok bantal dengan mendengarkannya dengan menempelkan obeng ke telinga kita (dan bantalannya). Metode ini dapat memberi kita periode peringatan beberapa hari (rata-rata, tergantung situasi).
Namun, jika kita membeli penganalisis getaran, kita mungkin dapat mendeteksi kegagalan yang sama setidaknya enam minggu sebelumnya. Kegagalannya sama, tetapi FDP telah berubah. Sebagian besar, satu-satunya alasan kami membeli alat inspeksi adalah untuk memperluas FDP dengan akurat.
Pada kenyataannya, kemampuan untuk mendeteksi kegagalan dan FDP juga bergantung pada:
- kemampuan orang tersebut untuk melakukan pemeriksaan;
- lingkungan (pencahayaan, suhu, dalam ruangan vs luar ruangan, dll);
- parameter operasional pada saat pemeriksaan;
- desain peralatan dan aksesibilitas;
- dan banyak lagi.
Banyak Variabel
Setiap komponen memiliki banyak mode kegagalan, dan setiap mode kegagalan memiliki FDP yang berbeda. Kita juga tahu bahwa setiap FDP dapat berubah tergantung pada alat inspeksi, teknik, orang yang melakukan inspeksi dan banyak lagi. Di atas semua ini, setiap komponen berjalan pada kecepatan yang berbeda, beban yang berbeda dan di lingkungan yang berbeda. Semuanya berbeda. Sekarang kita dalam masalah.
Pada titik pemikiran ini, menurut saya, banyak tanaman yang salah jalan. Beberapa tanaman membuat kesimpulan bahwa studi besar-besaran perlu dilakukan untuk menemukan jawaban atas semua pertanyaan ini. Mengapa ini bukan pendekatan yang baik? Bukan karena dalam 999 kali dari 1.000 Anda tidak akan memiliki data yang Anda perlukan untuk melakukan analisis.
Bahkan jika Anda melakukannya, keuntungan terbaik biasanya adalah melatih orang-orang Anda dan kemudian melakukan inspeksi daripada melakukan analisis besar. Apa yang akan Anda dapatkan ketika Anda melakukan analisis yang rumit tanpa data adalah tebakan liar, agak terpelajar dengan banyak pekerjaan. Jadi, jangan lakukan analisis yang rumit dan alih-alih melakukan tebakan liar dan agak terdidik menggunakan pengalaman kami dan memotong 99,9 persen pekerjaan? Apakah itu terdengar bagus untuk Anda?
Tebakan Liar, Agak Terpelajar
Mari kita lihat beberapa masalah umum dengan motor AC. Ini jauh dari semua mode kegagalan. Misalnya, jika Anda melihat manual SKF, bantalan memiliki lebih dari 50 mode kegagalan. Oleh karena itu, kita perlu melihat masalah umum.
Contoh:Motor AC, 125 tenaga kuda, beban 80 persen, operasi 24/7, lingkungan berdebu
Seperti disebutkan di atas, ada lebih banyak mode kegagalan. Saya telah memilih beberapa masalah umum untuk mengilustrasikan poin saya.
Jika kita melihat kolom kanan, ada banyak frekuensi pemeriksaan yang berbeda, bahkan ketika kita melakukan analisis yang disederhanakan. Perkiraan kami hanyalah perkiraan dan akan bervariasi sebagai akibat dari siapa yang melakukan pemeriksaan, jenis alat dan lingkungan, jadi kami tidak boleh menganggap angkanya terlalu serius; itu adalah perkiraan.
Oleh karena itu, saya akan melihat beberapa interval inspeksi yang lebih pendek dan kemudian menambahkan beberapa inspeksi dengan interval yang lebih panjang karena kita mungkin juga melakukan yang lebih lama ketika kita berada di sana. Tidak perlu waktu lama untuk melakukannya, dan kami hanya menebak intervalnya.
Ketika saya melihat motor AC ini, saya akan mengelompokkannya sebagai berikut di lingkungan pabrik proses yang khas:
Catatan:Pemeliharaan Pencegahan dan Standar Pemantauan Kondisi dijual oleh Noria.
Inspeksi Lainnya
Jika itu adalah motor kritis, mungkin Anda ingin melakukan analisis motor penuh atau kebocoran sederhana ke ground. Saya belum memiliki vendor yang dapat menjelaskan perkiraan FDP yang menggunakan alat mereka untuk inspeksi di atas.
Kesalahan Logika Umum
Frekuensi pemeriksaan didasarkan pada FDP, bukan masa pakai komponen, atau kekritisan.
Umur komponen tidak ada hubungannya dengan frekuensi pemeriksaan. Misalnya, pabrik kelas dunia mungkin memiliki umur motor rata-rata 18 tahun. Beberapa motor bertahan delapan tahun dan beberapa 25. Namun, FDP untuk motor ini kemungkinan besar dalam rentang satu hingga empat minggu, jadi statistik masa pakai tidak ada hubungannya dengan frekuensi inspeksi. Argumen keliru yang umum adalah “kami telah memeriksa komponen ini selama tiga tahun dan tidak menemukan masalah.
Oleh karena itu, kami perpanjang frekuensi pemeriksaan dari satu minggu menjadi dua minggu.” Fakta bahwa Anda belum menemukan masalah tidak ada hubungannya dengan FDP. Itu tidak berubah hanya karena komponennya berjalan dengan baik. Setelah komponen itu gagal, mungkin setelah 15 tahun, FDP mungkin masih dua minggu dan Anda harus menangkapnya. Jika Anda mengubah periode pemeriksaan menjadi dua minggu, kira-kira ada risiko 50 persen bahwa Anda akan melewatkannya.
Kekritisan tidak memengaruhi FDP tetapi secara praktis merupakan faktor saat kami menetapkan frekuensi inspeksi.
Bantalan motor AC kami sama pentingnya dengan fondasi kami untuk pengoperasian motor. Jika salah satu gagal, motor berhenti. Namun, FDP dan frekuensi inspeksi berbeda karena kami mendasarkan frekuensi inspeksi pada FDP.
Kekritisan motor dapat mengubah pemilihan frekuensi pemeriksaan karena kami tidak yakin dengan FDP. FDP adalah tebakan. Jadi komponen yang sangat kritis dapat diperiksa lebih sering karena kita tidak begitu tahu FDP. Ini adalah polis asuransi.
Singkatnya …
- Frekuensi pemeriksaan didasarkan pada FDP, bukan kekritisan atau umur komponen.
- FDP hampir tidak mungkin diprediksi. Namun, kita bisa menebaknya dengan cukup baik.
- Jika Anda tidak memiliki data historis yang sangat baik tentang apa itu FDP, jangan buang waktu Anda untuk membuat studi besar. Buatlah tebakan yang masuk akal. Ini adalah apa yang akan Anda dapatkan dengan studi tanpa data.
- Jika Anda memiliki data FDP, tanyakan apakah tidak lebih baik menghabiskan upaya untuk melatih orang dalam melakukan inspeksi dan perencanaan serta penjadwalan tindakan korektif daripada membuat studi FDP besar. Sebagian besar waktu, lebih baik menghabiskan waktu untuk eksekusi.