Dasar-dasar (dan manfaat) dari pemeliharaan produktif total
Mengadopsi model pemeliharaan preventif untuk fasilitas Anda dan mempraktikkan prinsipnya sesuai dengan rutinitas rutin dapat meningkatkan produksi perusahaan Anda secara keseluruhan, menjaga peralatan tetap berjalan pada tingkat yang ideal, dan mengurangi waktu henti. Pemeliharaan produktif total (TPM) adalah salah satu metode paling populer yang digunakan untuk mencapai tujuan tersebut:Pendekatan ini sangat terfokus pada pemberdayaan karyawan, dan membantu menjamin ketersediaan, kinerja, dan kualitas yang lebih baik.
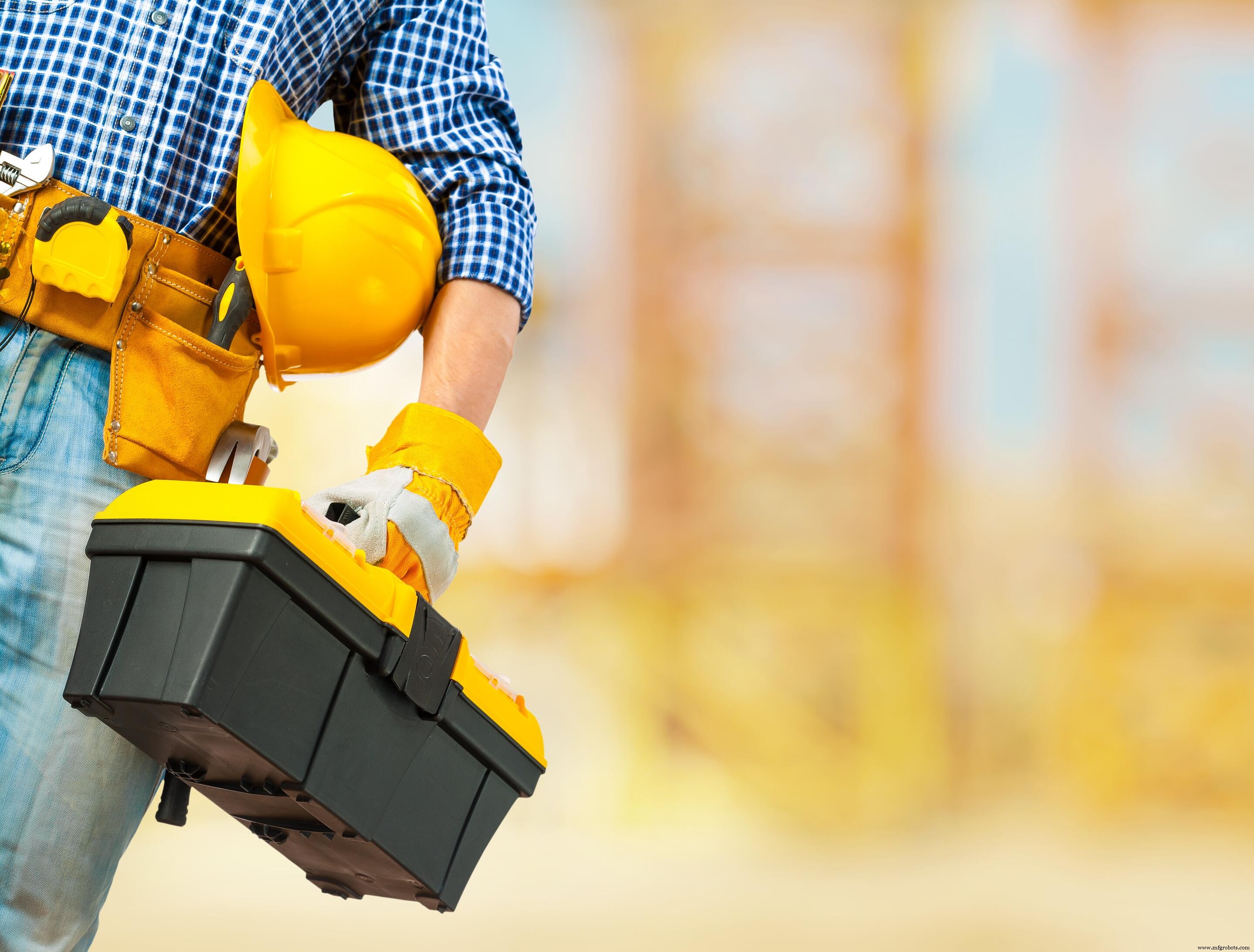
Performa dioptimalkan dengan meminimalkan kemungkinan kerusakan dan memastikan bahwa perlambatan atau jeda operasional sejarang mungkin. Ini, pada gilirannya, secara signifikan mengurangi kemungkinan cacat produk, yang dapat membantu meningkatkan kualitas barang jadi Anda. Selain itu, menerapkan strategi TPM dapat mewujudkan penghematan biaya yang signifikan dari waktu ke waktu dengan meningkatkan efisiensi peralatan secara keseluruhan:Menurut Mark Jolley, direktur layanan manufaktur di konsultan Marshall Institute, biaya pemeliharaan mungkin turun 25-30% dan biaya konversi turun sebesar 20-25% selama lima tahun.
Di sini, kita akan mengeksplorasi apa yang sebenarnya melibatkan TPM, dan juga melihat lebih dekat bagaimana hal itu menguntungkan produsen, perusahaan jasa makanan, penyedia energi, dan perusahaan dari berbagai sektor industri berat lainnya.
Dasar-dasar pemeliharaan produktif total
Pada intinya, pendekatan TPM adalah tentang memaksimalkan produktivitas — serta masa pakai peralatan — dengan memungkinkan pekerja untuk mengambil tanggung jawab lebih besar atas masalah ini setiap hari. Ini dicapai dengan cara berikut:
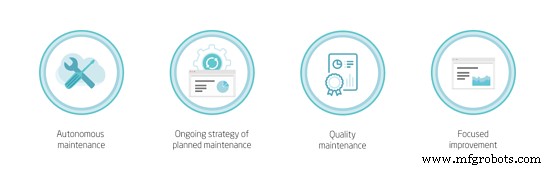
1. Pemeliharaan otonom
TPM memberikan tanggung jawab untuk tugas pemeliharaan peralatan rutin, seperti pelumasan, pembersihan, dan inspeksi, kepada operator reguler berbagai alat berat di seluruh fasilitas. Oleh karena itu, pekerja tidak bisa begitu saja membiarkan peralatan mereka rusak atau rusak, bergantung pada intervensi teknisi pemeliharaan khusus untuk mengembalikannya ke kondisi kerja. (Pikirkan seperti ini:Jika mereka adalah untuk mengambil pendekatan lesu itu, apa yang Anda dapatkan ketika staf pemeliharaan tidak tersedia karena alasan apa pun? Waktu henti yang tidak direncanakan, yang tidak dapat ditanggung oleh bisnis dalam waktu lama — atau, dalam beberapa kasus, sama sekali.)
Ada banyak manfaat dari teknik pemeliharaan proaktif ini. Pertama, staf pemeliharaan memiliki lebih banyak waktu untuk menangani tugas tingkat yang lebih tinggi — yaitu, menangani kegagalan peralatan produksi yang benar-benar tak terduga dan mendesak. Tetapi sementara operator pada awalnya mungkin kurang antusias untuk memiliki lebih banyak tanggung jawab, proses TPM meningkatkan tingkat keakraban mereka dengan peralatan dari waktu ke waktu, dan itu membuat pekerjaan mereka lebih mudah dalam jangka panjang. Ini juga memastikan bahwa karyawan ini lebih siap untuk mengidentifikasi masalah kecil apa pun dengan mesin saat mereka muncul dan mengatasinya tanpa harus melibatkan tim pemeliharaan.
2. Strategi pemeliharaan terencana yang berkelanjutan
TPM biasanya melibatkan penjadwalan tugas pemeliharaan berdasarkan tingkat kegagalan yang diukur dan/atau diprediksi. Hal ini mengurangi kejadian penghentian yang tidak direncanakan, memungkinkan peralatan untuk diservis selama jam kerja dan menghemat inventaris (melalui kontrol yang ditingkatkan dari suku cadang yang rawan kegagalan dan rawan aus). Dalam pengertian ini, ini adalah antitesis dari perawatan reaktif, di mana perbaikan hanya dilakukan jika benar-benar diperlukan — biasanya karena kegagalan total atau hampir malapetaka pada mesin atau sistem.
3. Pemeliharaan kualitas
Menerapkan strategi TPM dapat membantu organisasi memasukkan deteksi kesalahan dan praktik pencegahan ke dalam siklus produksi secara keseluruhan. Ini berasal dari dasar metodologi dalam prinsip-prinsip analisis akar penyebab (root cause analysis/RCA):Melihat pemeliharaan dari perspektif RCA menghindari pemeriksaan dinamika sebab-akibat sederhana untuk kepentingan melacak dengan tepat bagaimana suatu proses, sistem, atau perangkat gagal. Melakukan hal itu akan memperlengkapi pekerja dengan lebih baik untuk menentukan respons yang paling efektif terhadap suatu masalah.
Karena kerangka TPM berbasis RCA biasanya berfokus pada menghilangkan penyebab cacat yang menyebabkan kerusakan atau kegagalan peralatan, perlahan tapi pasti meningkatkan kualitas berbagai operasi. Selain itu, ini membantu mengurangi biaya dengan meningkatkan kemungkinan kesalahan ditemukan sejak dini, sebelum kesalahan tersebut dapat menyebabkan terlalu banyak kerusakan dan memerlukan tugas perbaikan atau penggantian yang mahal.
4. Dorongan untuk peningkatan yang terfokus
Aspek TPM ini adalah tentang memiliki kelompok staf yang lebih kecil yang bekerja bersama secara proaktif untuk mencapai peningkatan sistematis dan bertahap dalam pengoperasian mesin. Dengan demikian, Anda menghindari individu terjebak dengan satu-satunya tanggung jawab menjaga semuanya berjalan lancar dengan peralatan mereka dan kekacauan yang diakibatkan oleh "terlalu banyak juru masak di dapur".
Di sini, tim kecil namun lintas fungsi dapat mengidentifikasi dan menyelesaikan masalah yang berulang. Ini juga menggabungkan kumpulan bakat dalam perusahaan, dan ini lebih lanjut mengkatalisasi perbaikan berkelanjutan. 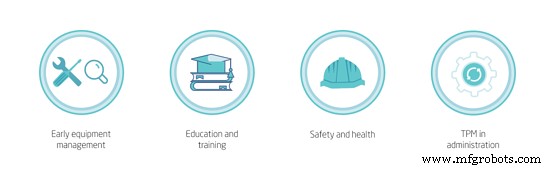
5. Manajemen peralatan awal
Pemahaman dan pengetahuan praktis tentang mesin pengolah yang diperoleh melalui pendekatan TPM diarahkan pada peningkatan dan perancangan peralatan baru dalam prinsip ini. Karena ada lebih sedikit masalah startup ketika TPM diterapkan dan dijalankan dengan benar, mesin baru dapat mencapai tingkat kinerja idealnya lebih cepat. Selain itu, servis peralatan dan aktivitas pemeliharaan lainnya jauh lebih mudah dan lebih kuat sebagai hasil dari keterlibatan karyawan dan tinjauan praktis sebelum pemasangan.
6. Pendidikan dan pelatihan
TPM bergantung pada mengisi kesenjangan pengetahuan yang mencegah bisnis Anda mencapai tujuan pemeliharaan utama. Ini berlaku untuk manajer, personel pemeliharaan, dan operator:
- Manajer melatih prinsip-prinsip TPM bersama staf bawahan, lateral dan atasan mereka. Ini membantu mereka lebih memahami bagaimana pemangku kepentingan di seluruh organisasi menangani masalah pemeliharaan dari sudut pandang mereka yang berbeda.
- Personil pemeliharaan menyempurnakan teknik yang diperlukan untuk pelaksanaan yang tepat dari strategi manajemen peralatan proaktif dan preventif.
Operator mengasah keterampilan mereka dalam mengidentifikasi masalah yang muncul dan memelihara mesin mereka secara rutin.
7. Keselamatan dan kesehatan
Menjaga lingkungan kerja yang sehat dan aman harus menjadi perhatian utama bagi perusahaan mana pun di mana mesin berat (atau peralatan lain yang dapat berbahaya di luar konteks operasi yang tepat) diperlukan secara teratur. Melakukan hal itu demi kepentingan terbaik dari kesopanan manusia yang sederhana dan kompleksitas kepatuhan terhadap peraturan.
TPM menempatkan masalah ini di depan dan di tengah. Ini membantu menghilangkan potensi risiko keselamatan dan kesehatan yang sedang berlangsung sementara juga meminimalkan kemungkinan kecelakaan mendadak dan bencana.
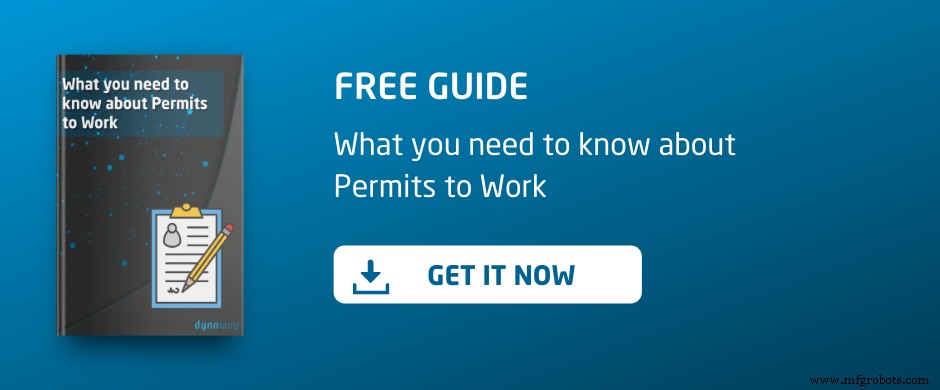
8. TPM dalam administrasi
Fundamental ini melibatkan penerapan teknik TPM pada fungsi administrasi perusahaan. Ini memperluas manfaat dari pendekatan di luar lantai pabrik fasilitas dengan mengatasi setiap waktu atau upaya yang terbuang selama operasi eksekutif dan manajerial. Mengadopsi prinsip-prinsip ini dapat menjadi sangat penting untuk meningkatkan pengadaan, penjadwalan, pemrosesan pesanan, dan manajemen aset.
Manfaat utama dari proses TPM
Dengan melibatkan operator dalam pelaksanaan tugas pemeliharaan — serta merencanakan dan menjadwalkan aktivitas tersebut untuk memastikan pengawasan yang konsisten terhadap peralatan utama — organisasi Anda berpotensi untuk mewujudkan manfaat berikut:
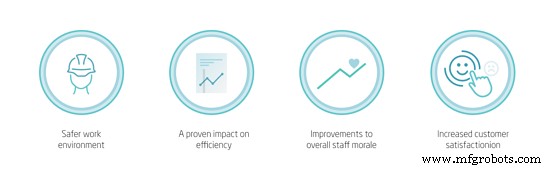
1. Lingkungan kerja yang lebih aman
Selain kerangka kerja seperti RCA, TPM juga didasarkan pada sistem manajemen terstruktur yang umumnya dikenal sebagai metode 5-S untuk langkah-langkah aliteratifnya:Sorting, Setting in order, Shining, Standardizing, dan Sustaining.
Semua poin S pada gagasan bahwa menjaga peralatan dan mesin tetap bersih, teratur, dan sehat dapat meningkatkan keselamatan di lingkungan kerja. Fokus TPM pada servis proaktif dan preventif meningkatkan masa pakai peralatan sekaligus mengurangi ketidakteraturan di tempat kerja. Ini juga memfasilitasi desain yang memaksimalkan produktivitas, efisiensi, dan aliran. Semua kualitas ini membentuk dasar keselamatan bagi pekerja di semua tingkatan.
2. Dampak yang terbukti pada efisiensi
Tujuan utama dari pendekatan TPM adalah mencapai suatu kondisi yang kadang-kadang disebut sebagai "produksi yang sempurna". Dengan kata lain, setiap pabrikan yang mempertimbangkan TPM bertujuan untuk mencapai nol cacat, kerusakan, atau kecelakaan. Ini berarti Anda mungkin harus fokus pada kualitas daripada kuantitas sambil juga memprioritaskan efisiensi daripada output.
Anda dapat mengukur TPM menggunakan skala penilaian Overall Equipment Effectiveness (OEE) — umumnya dianggap sebagai standar emas untuk mengukur produktivitas dalam proses manufaktur. Peringkat berlaku untuk kedua proses dan pengaturan produksi diskrit. Ini memfasilitasi peningkatan dengan mengidentifikasi area yang hilang dengan cepat, membandingkan kemajuan, dan meningkatkan produktivitas peralatan — semuanya dengan dasar data yang komprehensif. Metrik yang solid berbicara banyak, dan dengan OEE, Anda dapat membandingkan fasilitas dengan standar industri dan mengonfirmasi apakah program peningkatan TPM yang Anda gunakan berfungsi.
3. Peningkatan moral staf secara keseluruhan
Untuk sepenuhnya menerapkan lean manufacturing, Anda memerlukan karyawan di seluruh organisasi Anda di semua tingkatan untuk menyetujui gagasan tersebut dengan sepenuh hati. Jika memberikan hasil yang positif, kemungkinan kecil staf akan menolak perubahan secara inheren.
TPM serupa dalam banyak hal:Melalui prinsip-prinsipnya, karyawan diberdayakan dengan tanggung jawab untuk merawat peralatan mereka. Akibatnya, mereka mungkin cenderung bangga dan memiliki pekerjaan mereka. Langkah-langkah pencegahan yang melekat pada TPM menghasilkan lebih sedikit kasus kegagalan peralatan dan waktu henti yang membuat frustrasi. Keberhasilan ini hanya akan meningkatkan komitmen karyawan Anda terhadap filosofi TPM.
4. Meningkatkan kepuasan pelanggan
Tempat kerja yang aman, semangat kerja karyawan, dan produksi yang efisien merupakan keuntungan utama dari pemeliharaan produktif. Namun, banyak yang berpendapat bahwa pengalaman dan kepuasan pelanggan bahkan lebih penting dalam jangka panjang. Pilar pemeliharaan kualitas TPM memungkinkan integrasi peningkatan kualitas ke dalam proses produksi. Akibatnya, biasanya ada pengurangan pengerjaan ulang dan cacat serta peningkatan output dan kualitas. Hal ini, ditambah dengan alat berat yang andal yang mengalami lebih sedikit waktu henti, dapat membantu meningkatkan pelanggan yang puas dan bisnis yang berulang.
Apakah program TPM ideal untuk bisnis Anda?
Sangat sedikit yang dipotong dan dikeringkan di berbagai sektor manufaktur dan industri, dan setiap perusahaan berbeda. Meskipun TPM dapat bermanfaat bagi perusahaan mana pun secara teori, itu mungkin bukan sistem yang sempurna untuk organisasi Anda dalam praktiknya. Mungkin ada baiknya Anda menerapkannya dalam skala yang lebih kecil, atau sebagai program percontohan, dan mengamati hasilnya untuk periode yang terbatas (beberapa bulan atau lebih) sebelum berkomitmen untuk itu sebagai solusi permanen.
Pemeliharaan berbasis kondisi mirip dengan TPM, tetapi mencapai pemantauan peralatan yang berkelanjutan melalui implementasi dan pemanfaatan kerangka kerja internet of things (IIoT) industri. Ini mungkin lebih baik jika Anda merasa lebih nyaman menugaskan pengawasan efisiensi peralatan ke teknologi mutakhir (dan sepenuhnya objektif). Konon, seperti TPM, implementasinya bisa mahal, dan pemeliharaannya juga tidak murah. Jika Anda benar-benar kekurangan uang, mungkin perlu untuk tetap berpegang pada model reaktif untuk saat ini — sambil tetap mengingat TPM sebagai sistem yang dicita-citakan.
Bagaimana Anda merancang strategi perawatan terbaik untuk peralatan Anda?
Anda mungkin juga ingin mempertimbangkan untuk tidak memilih satu model pemeliharaan tertentu daripada yang lain:Sebagai gantinya, Anda dapat menggabungkan elemen dari beberapa metode, menciptakan model unik untuk kebutuhan spesifik organisasi Anda. Misalnya, tidak masuk akal untuk mengambil pendekatan reaktif untuk peralatan yang berprioritas rendah atau telah mengurangi risiko kerusakan. Pada saat yang sama, operator Anda akan melakukan pendekatan kepemilikan langsung terhadap teknologi operasional penting seperti sistem kontrol industri (ICS). Keragaman gaya ini akan membutuhkan waktu bagi karyawan untuk terbiasa dengannya, jadi melanjutkan secara bertahap adalah yang terbaik.
Pemeliharaan produktif — baik dalam kerangka TPM atau dalam format lain — bertujuan untuk meningkatkan keandalan peralatan dengan menginspirasi karyawan untuk bangga dengan pemeliharaannya. Jika dilakukan dengan baik, pendekatan tersebut dapat menghasilkan manfaat yang terukur dan langgeng seperti budaya perusahaan yang proaktif, pengurangan omset, peningkatan kualitas output, dan kepuasan pelanggan yang lebih besar.
Solusi manajemen aset perusahaan (EAM) Dynaway sangat ideal untuk memfasilitasi penerapan TPM, pemeliharaan berbasis kondisi, dan kerangka kerja pencegahan serupa. Dibangun ke dalam Microsoft Dynamics 365 Business Central, solusi ini menyederhanakan proses termasuk perintah kerja dan manajemen aset, inventaris, analisis kegagalan, dan pencatatan pemeliharaan, untuk efisiensi optimal di seluruh fasilitas. Tinggalkan perjuangan berurusan dengan alat terintegrasi dari banyak pihak ketiga dan pusatkan pengawasan fasilitas dan EAM dalam satu platform terdepan.