Apa itu Pemeliharaan Pencegahan?
Penjelasan Pemeliharaan Pencegahan
Pemeliharaan preventif (PM) sangat penting untuk profitabilitas dan kinerja di industri yang padat aset.
Setiap tugas PM harus memberikan pandangan yang jelas terhadap tujuan manajemen aset dan tujuan organisasi. Anda harus tahu mengapa Anda mengencangkan setiap baut, mengapa Anda menyelaraskan setiap motor, dan mengapa Anda sering mencuci setiap konveyor.
Setiap tugas PM harus memberi nilai tambah dan memainkan perannya dalam mencapai ketersediaan aset yang tinggi dan menjaga keandalan aset yang melekat. Setiap tugas PM harus memberikan laba atas investasi selama seluruh siklus hidup aset.
Sebelum kita masuk ke mur dan baut, mari kita mundur selangkah.
Apa sebenarnya itu Pemeliharaan Pencegahan?
Sederhananya, pemeliharaan preventif adalah strategi yang terdiri dari semua tugas yang dilakukan oleh departemen pemeliharaan dan operasi kami untuk mencegah kegagalan peralatan dan mempertahankan fungsi utamanya.
Anda pasti pernah mendengar akronim PM berkali-kali sekarang atau bahkan mendengarnya disebut pencegahan pemeliharaan.
Tapi itulah adanya. Tugas pemeliharaan yang mencegah kegagalan peralatan kami dan mempertahankan fungsi operasionalnya untuk mengirimkan barang atau jasa kami yang dapat dijual. Ini melindungi organisasi kita dari musuh bebuyutan itu:waktu henti yang tidak terjadwal dan kerugian produksi.
Itu harus ditargetkan pada peralatan dan aset yang tepat, dan harus bernilai secara finansial lakukan.
Tapi lebih lanjut tentang itu nanti.
Pemeliharaan Pencegahan memiliki sejarah
Berikut adalah beberapa tren industri dan perusahaan yang dominan selama beberapa dekade terakhir:
Dekade |
Tren dominan |
10 detik |
Industri 4.0
IoT.
Pemeliharaan 4.0.
Ekonomi sirkular dan produksi berkelanjutan,
Google. Facebook. Indonesia. Snapchat. |
00s |
Produksi berkelanjutan.
“Glokalisasi” (global + beradaptasi dengan lokal).
Robot industri.
GE. Microsoft. Intel. |
90-an |
Globalisasi.
Manufaktur ramping, Six Sigma, RCM.
Toyota, General Motors |
80-an |
Otomatisasi, komputer, elektronik.
Exxon Mobil, IBM |
70-an |
Internasionalisasi.
|
60-an |
Produksi massal.
Perdagangan internasional.
Efek Deming pada Kualitas. |
50-an |
Pertumbuhan pasca perang, peningkatan konsumerisme. |
40-an |
Tuntutan WW2. |
Peralatan dirancang secara berlebihan dan lugas pada saat menjelang tahun 1940-an. Ini berarti secara umum dapat diandalkan dan mudah dirawat, dan perawatan reaktif adalah strategi utama. Tetapi selama tahun 1940-an, sesuatu berubah secara dramatis. Saat WW2 berkecamuk di seluruh Eropa, peningkatan permintaan industri berarti peristiwa downtime diperbesar. Peralatan secara alami menjadi lebih kompleks dan membutuhkan waktu lebih lama untuk diperbaiki. Dengan demikian, pemeliharaan preventif muncul dalam bentuk perbaikan terjadwal.
Tahun 1950-an terjadi peningkatan konsumerisme dari generasi yang selamat dari tahun-tahun perang yang sulit dan permintaan lebih lanjut ditempatkan pada industri dan pemeliharaan preventif.
Pada tahun 1960-an, produksi massal berlaku penuh dan perdagangan internasional tumbuh secara substansial – menempatkan tuntutan yang lebih tinggi pada peralatan. Ide dan pengaruh Edward Deming memiliki pengaruh besar pada kualitas produk, tetapi overhaul terjadwal dan pemeliharaan reaktif masih dominan.
Sejak tahun 1970-an dan seterusnya muncul kebutuhan akan kualitas dan ketersediaan yang lebih tinggi, waktu henti yang lebih sedikit, dan siklus hidup peralatan yang lebih lama. Organisasi telah terinternasionalisasi dan perlu bersaing secara global. Pemeliharaan preventif harus menambah nilai, dan itu harus layak dilakukan. Kesadaran datang bahwa perbaikan terjadwal tidak selalu menambah nilai dan tidak selalu mencegah kegagalan.
Pemeliharaan preventif harus dilanjutkan.
Teknologi baru seperti pemantauan kondisi sekarang masih dalam masa pertumbuhan. PM lebih fokus pada pembersihan, pelumasan, dan pemeriksaan.
Tahun 1980-an menyaksikan ledakan otomasi industri, komputer, dan elektronik untuk mendorong efisiensi operasional. Bersamaan dengan ini muncul kebutuhan akan keterampilan pemeliharaan baru, multi-keterampilan, dan rutinitas PM baru.
Tahun 1990-an menyaksikan globalisasi massal dan popularitas lean manufacturing dan pendekatan six sigma untuk mengurangi pemborosan dan cacat. Pemeliharaan yang berpusat pada keandalan (RCM) meningkatkan pemahaman strategi pemeliharaan. Dan tahun 90-an melihat dorongan menuju pemeliharaan yang digerakkan oleh operator di mana operator diharapkan untuk melakukan
pertama
pemeliharaan jalur dan tugas PM.
Fokus bergeser di tahun 2000-an ke keberlanjutan karena perubahan iklim dan istilah 'Glokalisasi' lahir. Saat ini teknologi pemantauan kondisi telah meningkatkan pemeliharaan preventif secara signifikan. Robot industri juga muncul dan membawa persyaratan PM baru.
Lanskap industri telah berubah secara signifikan di tahun 2010-an. Pemeliharaan preventif menemukan dirinya dalam 4
th
revolusi industri (industri 4.0) di mana sensor dan sistem yang saling berhubungan memberikan informasi waktu nyata tentang kesehatan peralatan - meskipun fokus tetap pada keberlanjutan dan ekonomi sirkular. Raksasa teknologi mendominasi lanskap di mana aset dan peralatan utama mereka adalah pusat data.
Saat ini, dalam industri yang padat aset dan dinamis, kami memiliki pemahaman yang jauh lebih baik tentang pemeliharaan preventif dan bagaimana hal itu menambah nilai dalam mencapai tujuan organisasi kami.
Kami memahami bahwa membiarkan aset gagal - dan kemudian memperbaikinya - adalah bisnis yang mahal. Dan bahwa ada cara yang lebih baik untuk melakukan pemeliharaan preventif.
Pemeliharaan preventif terdiri dari berbagai jenis tugas
Beberapa percaya bahwa PM hanya terdiri dari penggantian berdasarkan waktu atau penggunaan. Ini tidak sepenuhnya benar. Ini hanya setengah gambar. Pemeliharaan preventif dapat dibagi menjadi dua bidang utama:pemeliharaan berbasis waktu/penggunaan dan pemeliharaan berdasarkan kondisi.

Pemeliharaan berbasis waktu/penggunaan
Ini mungkin yang muncul di benak Anda ketika Anda memikirkan PM:Suku cadang dan komponen yang diganti atau diperbarui berdasarkan waktu (kalender) atau basis penggunaan. Filter proses dapat dijadwalkan untuk diganti setiap 12 bulan atau pisau pemotong kertas dapat dijadwalkan untuk diganti setelah 2500 jam servis. Dalam kedua kasus tersebut, barang diketahui akan segera aus setelah batas tersebut tercapai. Dan, oleh karena itu, produsen mencegah kegagalan.
Tugas berbasis kalender jauh lebih mudah untuk dijadwalkan tetapi berisiko berlebihan atau kurang dalam mempertahankan aset karena tidak ada jaminan bahwa filter proses telah digunakan setiap hari selama 12 bulan tersebut. Di sisi lain, tugas berbasis penggunaan – meskipun lebih sulit untuk dilacak dan dikelola - lebih efektif dan ekonomis karena didasarkan pada pemanfaatan aset yang sebenarnya.
Tugas PM khas lainnya seperti pembersihan dan pelumasan aset dapat dianggap sebagai aktivitas berbasis waktu/penggunaan. Tugas sederhana - namun kritis ini sering dilakukan secara terjadwal dalam beberapa minggu atau bulan aktivitas manufaktur dan berfungsi untuk menjaga fungsi dan keandalan peralatan.
Pemeliharaan berbasis kondisi (CBM)
Jenis pemeliharaan ini berarti bahwa kami melakukan tugas perbaikan atau penggantian hanya berdasarkan kondisi aset yang diukur.
Kami menggunakan teknik yang disebut pemantauan kondisi untuk memungkinkan kami melakukan pemeliharaan berdasarkan kondisi.
Pertama, kami mengukur parameter spesifik kesehatan aset seperti getaran, suhu, desibel, partikel aus, atau kontaminasi. Kemudian kami tren nilai parameter dari waktu ke waktu. Saat kami yakin telah mencapai titik kritis bahwa aset mengalami kegagalan fungsional (tidak dapat menjalankan fungsinya lagi), kami menjadwalkan intervensi pemeliharaan berbasis kondisi.
Berikut adalah beberapa contoh intervensi CBM:
- Mengganti bantalan yang aus
- Menyeimbangkan impeler kipas
- Memperbarui kontaktor listrik
- Menyejajarkan set pompa
- Mengisi ulang minyak pelumas
- Mengencangkan kabel listrik yang longgar
CBM adalah cara yang paling hemat biaya dan ekonomis untuk memelihara aset berdasarkan mekanisme kerusakan yang nyata dan nyata.
Bagian dari teknik pemantauan kondisi adalah inspeksi sensorik dan rinci. Mereka bermain besar peran dalam pemeliharaan preventif dan penyorotan aktif kerusakan aset. Meskipun seringkali bersifat kualitatif, kita harus selalu berusaha membuatnya sekuantitatif mungkin. Inspeksi sensorik dapat mencakup hal berikut:
- Mendengarkan suara yang tidak biasa.
- Mencari kerusakan.
- Berbau untuk tanda-tanda terbakar.
Inspeksi terperinci (dan daftar periksa) dapat digunakan pada semua jenis dan kategori aset mulai dari pompa dosis kecil 1kW di tempat pembuatan bir hingga turbin uap 250 MW di pabrik baja. Pemeriksaan dapat mencakup hal berikut:
- Pastikan runout poros 0,004” atau kurang.
- Periksa kelenjar kabel motor apakah ada tanda-tanda kerusakan.
- Pastikan ketegangan sabuk penggerak diatur antara 88 dan 90 lbs.
- Periksa segel mekanis pompa dari kebocoran.
Sekarang kita semua tahu apa yang dimaksud dengan pemeliharaan preventif dan terdiri dari apa, sekarang saatnya untuk bertanya pada diri sendiri pertanyaan berikutnya.
Apa yang baik PM terlihat seperti?
Pertama, harus dijelaskan bahwa pemeliharaan preventif tidak berlaku untuk semua aset. Paling sering, ini akan berlaku untuk aset kekritisan menengah dan tinggi di organisasi Anda. Aset dengan kekritisan rendah sering kali mengalami kegagalan karena konsekuensi dari kegagalan mereka tidak membenarkan waktu dan sumber daya PM.
Kedua, diskusi tentang pemeliharaan preventif tidak dapat lengkap tanpa menyatakan bahwa organisasi terbaik di kelasnya menggunakan mode kegagalan dan analisis efek (FMEA) untuk mengembangkan pendekatan dan strategi pemeliharaan mereka – di mana PM selalu menjadi elemen kunci.
Ketiga, kelola PM Anda dalam sistem EAM atau CMMS. Pemeliharaan Pencegahan memiliki proses alur kerja sendiri sebagai bagian dari manajemen kerja tradisional. Jika Anda mengetahui jadwal PM Anda, maka Anda dapat memperkirakan perencanaan sumber daya dan tetap mengendalikan biaya.
Berikut adalah beberapa praktik terbaik dan petunjuk yang akan membantu Anda melakukan dengan benar pemeliharaan preventif:
PM berbasis waktu atau penggunaan – simpan tugas ini untuk item atau komponen yang benar-benar aus seiring waktu. Jika Anda mengganti atau merombak item yang tidak menunjukkan karakteristik aus yang asli, maka Anda membuang-buang uang. Ingat, jenis PM ini harus disediakan untuk item yang bersentuhan dengan produk atau di mana terjadi gesekan.
CBM – pengukuran pemantauan kondisi Anda harus dilakukan pada interval yang tepat untuk deteksi kegagalan dan harus didasarkan pada mode kegagalan yang dapat dideteksi. Maksud kami, Anda mengukur getaran untuk menyoroti bantalan yang rusak, ketidaksejajaran, ketidakseimbangan, atau kavitasi. Itu tidak bisa memberi tahu Anda segalanya. Dan itu tidak akan memberi tahu Anda bahwa ada produk yang terkontaminasi melalui pompa Anda. Pengukuran juga harus dapat diulang dan dikumpulkan dari tempat yang sama setiap saat.
Inspeksi – program inspeksi Anda akan sangat berhasil jika didasarkan pada mode kegagalan yang diketahui, bersifat kuantitatif dan dapat diulang. Lihat perbedaannya di sini:
1a. |
Periksa bantalan untuk permainan aksial. |
1b. |
Pastikan semua baut kepala tutup sudah kencang. |
1a. |
Dengan menggunakan DTI, pastikan permainan aksial bantalan antara 0,001” dan 0,0015” pada suhu sekitar (18 hingga 30ºC). |
1b. |
Dengan menggunakan kunci momen yang dikalibrasi secara berselang-seling, pastikan keempat (4) baut kepala tutup diberi torsi hingga 250 inci-pon. |
Dapatkah Anda melihat bagaimana rangkaian pemeriksaan kedua menambah nilai ?
Sebaliknya, rangkaian pemeriksaan pertama bersifat ambigu dan dapat menyebabkan pemborosan waktu, salah tafsir, argumen, dan kesalahan.
Tidak ada yang menginginkan itu!
Apakah Pemeliharaan Pencegahan layak usaha?
Kami sebutkan lebih awal dari PM harus sepadan. Dan maksud kami secara finansial sepadan dengan usaha. Biaya untuk mencegah kegagalan harus lebih kecil dari biaya kegagalan itu sendiri – jika tidak, tidak .
Lihat diagram ini:
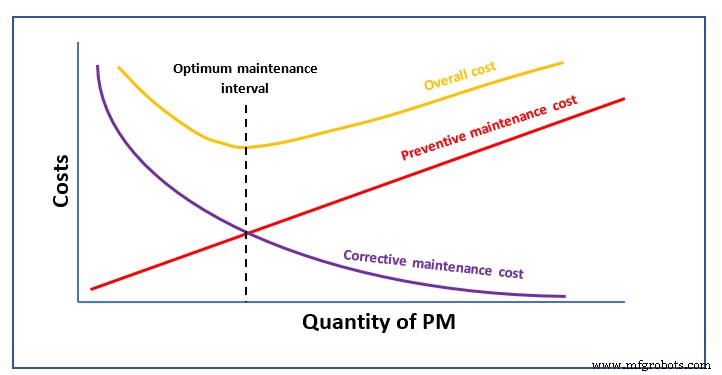
Ini menunjukkan konsep yang sangat sederhana.
Jika Anda melakukan PM sangat sedikit, maka biaya pemeliharaan korektif Anda akan tinggi, yaitu Anda akan memiliki banyak kegagalan untuk dikoreksi. Sebaliknya, jika Anda melakukan PM berlebihan, maka biaya pemeliharaan korektif Anda akan sangat rendah, tetapi biaya PM akan melambung tinggi.
Dengan memahami aset Anda, mode kegagalannya, dan kebutuhan perawatannya, maka Anda dapat menemukan sweet spot:interval perawatan optimal . Ini adalah interval PM yang akan memberikan organisasi Anda biaya pemeliharaan terendah selama siklus hidup aset untuk tugas PM tertentu.
Konsep serupa mengenai biaya dapat dilihat di sini:
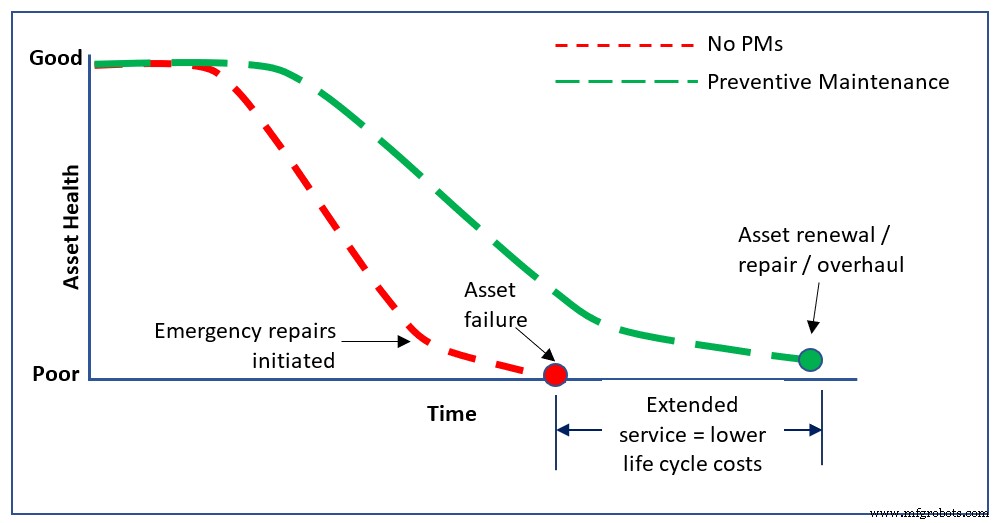
Ini menunjukkan bahwa dengan memperpanjang siklus hidup peralatan melalui pemeliharaan preventif rutin, kami dapat menghemat biaya siklus hidup yang signifikan dalam hal pengeluaran operasional dan pemeliharaan.
Pesan moral dari cerita tersebut? Jadilah terencana dan proaktif, bukan sepenuhnya reaktif.
Hal-hal yang harus diperhatikan
Setelah semua hal bagus itu, kita harus sedikit meredam diskusi dengan hal-hal yang harus diperhatikan atau waspada dari!
Pemeliharaan yang direkomendasikan OEM – jika aset Anda masih dalam masa garansi, maka ya, ikuti panduannya. Namun perlu diketahui bahwa setelah masa garansi berakhir, Anda harus meninjau strategi PM Anda. Ini karena PM yang direkomendasikan OEM didasarkan pada perkiraan konservatif dan skenario terburuk. Mereka dapat menyebabkan Anda terlalu menjaga aset Anda. Ini karena OEM tidak mengetahui industri tempat Anda berada dan tidak mengetahui lingkungan operasinya.
Dan poin selanjutnya yang perlu dipertimbangkan adalah bahwa semua OEM menghasilkan uang dari penjualan suku cadang.
PM kualitatif yang ambigu – ketahuilah bahwa inspeksi PM seperti 'periksa pompa' membuat organisasi Anda rentan terhadap kebingungan, panggilan palsu, salah tafsir, dan peningkatan risiko. Seperti yang kami katakan sebelumnya, buatlah nilai tambah dan kuantitatif jika memungkinkan.
Perombakan terjadwal – Jika Anda melakukan overhaul terjadwal dan mengganti suku cadang, maka pastikan bahwa suku cadang yang Anda ganti benar-benar aus melalui cara normal. Jika Anda mengganti motor dan girboks setiap enam bulan - untuk berjaga-jaga jika rusak – maka Anda mungkin membuang-buang waktu yang berharga, sumber daya yang terampil, dan uang.
Anda tidak mengganti girboks mobil Anda setiap enam bulan, bukan?
Itulah gambaran umum yang bagus tentang pemeliharaan preventif dalam hal apa itu, dari mana asalnya, praktik terbaik, dan apa yang harus diwaspadai.
Ke mana Anda bisa pergi selanjutnya?
Organisasi-organisasi yang berjuang untuk keunggulan operasional memahami kebutuhan untuk merangkul Industri 4.0 dan digitalisasi pemeliharaan. Pemeliharaan preventif, prosesnya, dan alur kerjanya sangat cocok dengan konsep baru ini. Pekerja sekarang dapat mengelola PM mereka di lantai toko secara real time dengan solusi seluler yang terhubung ke internet. Data dinamis pemeliharaan preventif yang dilihat melalui lensa industri 4.0 akan membuka jalur baru menuju pengambilan keputusan yang kaya data di EAM atau CMMS Anda.
Pastikan Anda mencakup semua langkah Perencanaan Pemeliharaan
Dynaway EAM untuk Pusat Bisnis adalah solusi sederhana namun intuitif yang mudah digunakan dan membantu Anda menjembatani semua kesenjangan dalam Perencanaan Pemeliharaan Anda.
Habiskan lebih sedikit waktu di belakang komputer dan lebih banyak waktu untuk merawat aset Anda!