Jenis Pemeliharaan:Perbandingan
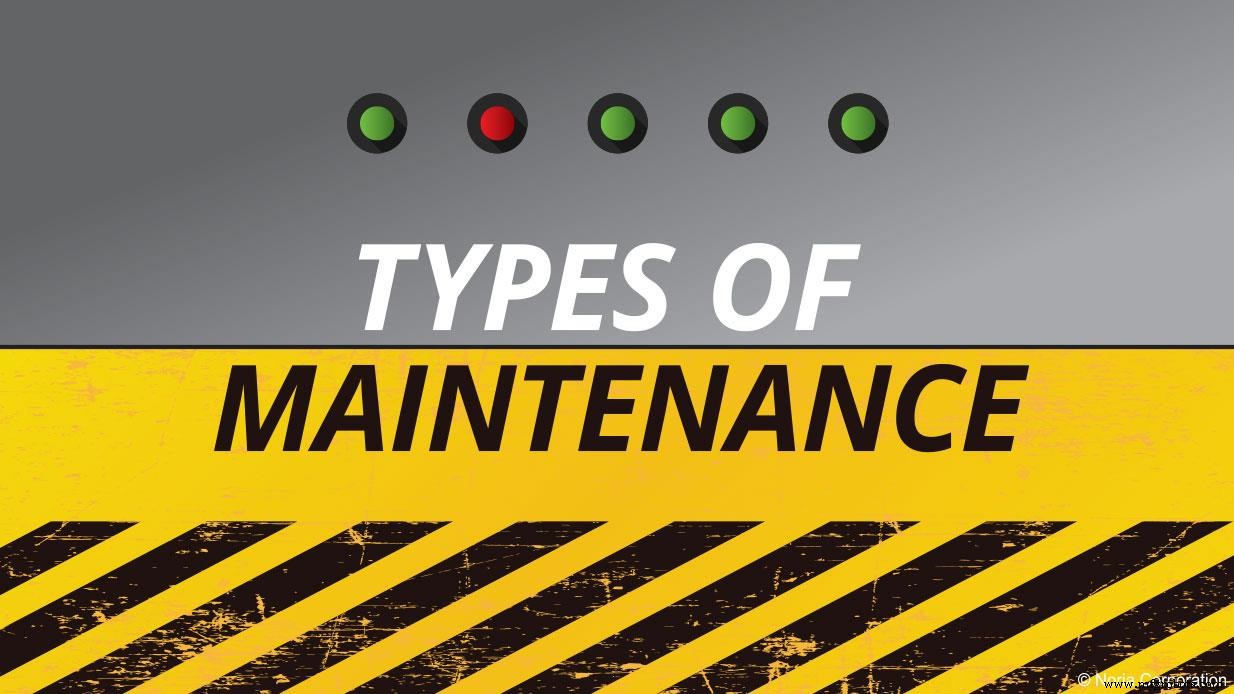
Jenis Pemeliharaan
Sudah diketahui bahwa miliaran dolar hilang setiap tahun karena waktu henti yang tidak terjadwal dan kualitas aset yang buruk. Dalam pertempuran tanpa akhir untuk memerangi statistik ini, organisasi menerapkan salah satu dari berbagai jenis pemeliharaan, sering kali menggabungkan dua atau lebih. Definisi jenis pemeliharaan berbeda-beda di setiap industri, sehingga agak membingungkan untuk membedakan hal-hal seperti pemeliharaan preventif dan prediktif.
Sebagian besar jenis pemeliharaan terbagi dalam dua kategori utama:preventif dan korektif. Pemeliharaan preventif adalah saat Anda secara proaktif memulai tugas dan rencana pemeliharaan untuk mencegah terjadinya kegagalan. Selain mencegah kegagalan, pemeliharaan preventif dapat memiliki tujuan meminimalkan konsekuensi kegagalan atau menentukan risiko kegagalan yang terjadi.
Pemeliharaan korektif terjadi setelah kegagalan terjadi. Tim Anda pada dasarnya mengembalikan aset ke urutan kerja pada saat ini. Untuk memperjelas, pemeliharaan korektif dapat direncanakan dalam bentuk strategi pemeliharaan run-to-failure, yang akan dibahas di bawah ini.
Mari kita periksa jenis perawatan yang paling umum digunakan di seluruh industri manufaktur dan proses.
- Pemeliharaan preventif. Pemeliharaan preventif adalah rutinitas yang ditetapkan untuk memeriksa peralatan secara berkala, memperhatikan masalah kecil dan memperbaikinya sebelum berubah menjadi masalah besar. Tujuan utama dari pemeliharaan preventif adalah nol downtime. Tujuan ini dicapai dengan menggunakan tiga tujuan:meningkatkan umur produktif peralatan, mengurangi kerusakan peralatan kritis dan meminimalkan kerugian produksi karena kegagalan peralatan.
Ada beberapa jenis pemeliharaan yang termasuk dalam kategori pemeliharaan preventif. Ini termasuk:
- Pemeliharaan berbasis penggunaan, yang menggunakan pemicu berdasarkan penggunaan aktual setiap aset. Melacak penggunaan aset dengan monitor peralatan memungkinkan manajer pemeliharaan untuk mengatur jadwal pemeliharaan preventif sesuai dengan parameter yang telah ditetapkan.
- Pemeliharaan preskriptif sangat mirip dengan pemeliharaan preventif, tetapi memanfaatkan perangkat lunak pembelajaran mesin seperti kecerdasan buatan (AI) dan internet of things (IoT) untuk membantu menjadwalkan tugas pemeliharaan preventif.
Untuk melihat secara mendalam jenis pemeliharaan preventif, cara merancang program pemeliharaan preventif, alat pemeliharaan preventif, dan lainnya, lihat tautan di awal bagian ini.
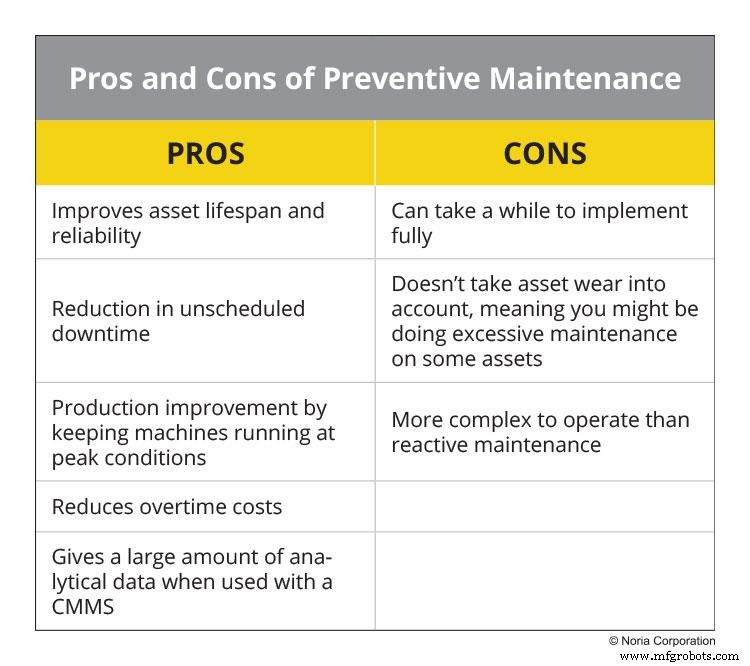
- Pemeliharaan prediktif. Pemeliharaan prediktif adalah pemeliharaan yang memantau kinerja dan kondisi peralatan selama kondisi operasi normal untuk mengurangi kemungkinan kegagalan. Mirip dengan perawatan pencegahan (beberapa orang bahkan mengkategorikannya sebagai jenis perawatan preventif) dan erat kaitannya dengan perawatan berbasis kondisi (CBM) , tujuan pemeliharaan prediktif terletak pada nama:untuk pertama memprediksi kapan kegagalan dapat terjadi dan kemudian mencegah kegagalan melalui pemeliharaan korektif terjadwal.
Meskipun banyak organisasi menggunakan pemeliharaan prediktif dan preventif (76 persen menggunakan pencegahan, sementara 65 persen menggunakan prediksi, menurut survei Pabrik Handal baru-baru ini), ada beberapa perbedaan utama. Terutama, pemeliharaan preventif tidak memerlukan aspek pemantauan kondisi seperti pemeliharaan prediktif. Ini berarti pemeliharaan prediktif menggunakan teknologi berbasis kondisi seperti termografi inframerah, pemantauan akustik, analisis getaran, dan analisis oli. Perbedaan utama lainnya adalah pemeliharaan preventif melibatkan pemeriksaan dan pemeliharaan aset terlepas dari apakah peralatan memerlukan pemeliharaan (jadwal pemeliharaan didasarkan pada pemicu). Pemeliharaan prediktif tidak.
Di bawah ini adalah bagan yang menunjukkan bagaimana pemeliharaan berbasis kondisi berhubungan dengan pemeliharaan prediktif dan proaktif. Di sini, pemeliharaan prediktif adalah salah satu dari dua sisi yang berasal dari CBM:sisi proaktif yang berfokus pada menemukan akar penyebab kegagalan dan sisi prediktif yang berkonsentrasi pada gejala kegagalan dan kesalahan.
Untuk detail selengkapnya tentang pemeliharaan prediktif, teknologi pemeliharaan prediktif, dan lainnya, klik tautan di awal bagian ini.
- Pemeliharaan yang Berpusat pada Keandalan (RCM). Pemeliharaan yang berpusat pada keandalan adalah proses mengidentifikasi potensi masalah dengan peralatan Anda dan menentukan apa yang harus Anda lakukan untuk memastikan aset tersebut terus berproduksi pada kapasitas maksimum. Dengan kata lain, Anda menganalisis kerusakan untuk mengetahui metode perawatan yang tepat dan jadwal perawatan yang disesuaikan untuk setiap aset individu.
Pemeliharaan yang berpusat pada keandalan terkadang dikacaukan dengan pemeliharaan preventif, tetapi ada satu perbedaan utama:pemeliharaan preventif tidak selektif seperti RCM, sehingga kurang efisien. Karena RCM melihat setiap aset satu per satu, inefisiensi dapat dikurangi dengan menetapkan tugas pemeliharaan yang disesuaikan untuk setiap peralatan.
Pemeliharaan yang berpusat pada keandalan menggunakan alur kerja empat langkah umum:Pilih aset, evaluasi aset, tentukan jenis pemeliharaan, dan ulangi prosesnya. Kriteria penilaian untuk mengimplementasikan program RCM mengajukan tujuh pertanyaan:
- Seberapa baik kinerja peralatan ini?
- Dengan cara apa peralatan ini bisa rusak?
- Apa yang menyebabkan setiap kegagalan?
- Apa yang terjadi jika terjadi kegagalan?
- Mengapa setiap kegagalan penting?
- Tugas (proaktif) apa yang harus dilakukan untuk mencegah kegagalan ini terjadi?
- Apa yang harus dilakukan jika tugas pencegahan yang sesuai tidak dapat ditemukan?
Klik tautan di awal bagian ini untuk membaca selengkapnya tentang pemeliharaan yang berpusat pada keandalan, termasuk cara menerapkan RCM, studi kasus dunia nyata dari organisasi yang telah menerapkan program RCM, dan banyak lagi.
- Total Productive Maintenance (TPM). Pemeliharaan produktif total adalah proses penggunaan mesin, peralatan, karyawan dan proses pendukung untuk menjaga dan meningkatkan integritas produksi dan kualitas sistem. Tujuan dari program TPM adalah untuk meningkatkan efektivitas peralatan secara keseluruhan (OEE) dengan membentuk tim kecil multidisiplin untuk menangani area inti seperti pemeliharaan preventif dan otonom, pelatihan operator mesin, dan standarisasi proses kerja. Pemeliharaan produktif total berfokus pada semua departemen dalam suatu organisasi, memastikan penggunaan alat produksi yang efisien dan efektif.
Pemeliharaan produktif total dianggap lebih sebagai proses daripada program serta proses peningkatan operasi daripada program pemeliharaan penuh. Ini juga bukan perbaikan cepat, karena butuh bertahun-tahun untuk mencapai manfaat maksimal dari proses TPM berkualitas tinggi; namun, Anda dapat langsung melihat hasilnya.
Pemeliharaan produktif total menggabungkan lean manufacturing dan teknik Sistem 5-S dari tolok ukur yang diterima secara internasional yang terdiri dari delapan pilar:pemeliharaan otonom, peningkatan terfokus, pemeliharaan terencana, pemeliharaan kualitas, manajemen peralatan dini, pelatihan dan pendidikan, keselamatan, kesehatan, dan lingkungan, dan TPM dalam administrasi.
Menerapkan TPM melibatkan lima fase:
- Identifikasi area percontohan
- Mengembalikan peralatan ke kondisi operasi prima
- Mengukur OEE
- Mengatasi/mengurangi kerugian besar
- Terapkan pemeliharaan terencana
Klik tautan di awal bagian ini untuk membaca lebih lanjut tentang TPM, termasuk delapan pilar TPM, cara menerapkannya, cara mempertahankan proses TPM, dan banyak lagi.
- Pemeliharaan otomatis. Pemeliharaan otonom adalah strategi pemeliharaan yang terdiri dari pelatihan operator untuk terus memantau peralatan mereka, melakukan penyesuaian dan melakukan tugas pemeliharaan kecil untuk meningkatkan efisiensi. Ini dilakukan alih-alih mendedikasikan teknisi pemeliharaan untuk melakukan pemeliharaan terjadwal secara teratur, membebaskan mereka untuk tugas pemeliharaan yang lebih signifikan dan mendesak.
Pemeliharaan otonom memiliki dua prinsip inti:untuk mencegah kerusakan peralatan melalui pengoperasian yang benar dan membawa peralatan ke dan menjaganya dalam kondisi "seperti baru" melalui pemulihan dan pengelolaan yang tepat. Hal ini mengharuskan operator untuk menguasai keterampilan seperti mendeteksi kelainan dengan memahami komponen alat berat, melakukan peningkatan, mengidentifikasi masalah kualitas, dan mencari tahu penyebab masalah kualitas.
Menerapkan pemeliharaan otonom melibatkan tujuh langkah:meningkatkan pengetahuan operator, pembersihan dan inspeksi alat berat awal, menghilangkan penyebab kontaminasi dan meningkatkan akses, mengembangkan standar untuk pelumasan dan inspeksi, inspeksi dan pemantauan, standarisasi perawatan visual, dan peningkatan berkelanjutan.
Untuk melihat lebih mendalam tentang pemeliharaan mandiri, cara menerapkannya, dan cara mempertahankannya, klik tautan di awal bagian ini.
- Pemeliharaan run-to-failure (RTF). Pemeliharaan run-to-failure adalah jenis pemeliharaan reaktif yang tidak direncanakan yang biasanya merupakan strategi yang disengaja yang dirancang untuk meminimalkan biaya. Organisasi dapat memilih untuk mengadopsi rencana RTF untuk hal-hal seperti aset sekali pakai (mesin dengan suku cadang sekali pakai yang dimaksudkan untuk ditukar daripada diperbaiki), aset tidak penting seperti alat, aset tahan lama, atau aset yang tidak akan aus atau tidak mungkin gagal dalam kondisi operasi normal, atau aset yang menunjukkan pola kegagalan acak yang tidak dapat diprediksi.
Peringatan untuk pemeliharaan RTF adalah memerlukan penilaian yang baik. Mengetahui kapan harus melabeli sesuatu sebagai kegagalan besar alih-alih memperbaikinya adalah bagian dari keahlian yang disertakan dengan pemeliharaan RTF. Ini dapat menimbulkan beberapa risiko karena aset tidak dipantau, menyebabkan organisasi mengabaikan waktu henti yang tidak direncanakan saat terjadi kerusakan.
Namun, ketika diterapkan pada aset yang tepat dengan perencanaan yang cerdas untuk menangani kegagalan yang tak terhindarkan, RTF dapat menghemat waktu dan uang dengan tidak mengganti peralatan yang tidak rusak.
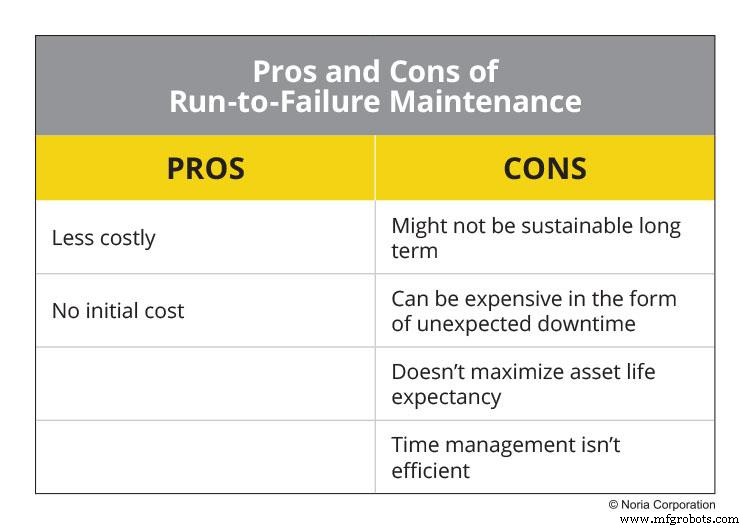
Perawatan Mesin dan Paralel Tubuh Manusia
Dalam hal jenis, teknik, dan biaya perawatan, jenis perawatan utama dapat dibandingkan dengan tubuh manusia untuk mendapatkan gambaran tentang tugas "pemeliharaan tubuh" yang setara. Tabel di bawah ini menggunakan contoh aset pembangkit listrik dan membandingkannya dengan hati manusia.
Jenis Pemicu Pemeliharaan
Pemicu pemeliharaan dapat diatur dan digunakan dengan beberapa jenis pemeliharaan. Pemicu kerusakan digunakan dengan rencana pemeliharaan run-to-failure atau reaktif. Pemeliharaan prediktif menggunakan hal-hal seperti pemicu berbasis waktu dalam bentuk peringatan untuk mencoba dan mencegah terjadinya kegagalan. Pemicu lain yang akan dibahas meliputi pemicu berbasis peristiwa, penggunaan, dan kondisi.
- Pemicu kerusakan. Seperti disebutkan sebelumnya, pemicu kerusakan digunakan dengan program pemeliharaan run-to-failure atau reaktif. Saat aset berhenti bekerja, peringatan dipicu, yang menjadwalkan perintah kerja pemeliharaan untuk memperbaiki aset dan memulihkannya ke kondisi pengoperasian normal.
Pemicu kerusakan biasanya hanya berguna ketika organisasi menjalankan sekelompok peralatan berbiaya rendah dan mudah diganti serta memiliki suku cadang dan unit pengganti yang dapat dengan mudah dan mudah ditukar, meminimalkan waktu henti sebanyak mungkin. Menggunakan pemicu kerusakan mirip dengan permainan kucing-dan-tikus; tidak harus merencanakan perawatan memungkinkan anggaran perawatan yang lebih murah, tetapi itu juga berarti Anda harus memiliki suku cadang dan peralatan yang tersedia setiap saat, serta personel untuk memperbaiki masalah. Memegang saham seperti ini bertentangan dengan prinsip lean seperti Just in Time (JIT), yang dirancang untuk mengurangi stok yang ditahan.
- Pemicu berbasis waktu. Mungkin pemicu pemeliharaan yang paling umum digunakan adalah berbasis waktu. Ini terkait dengan perangkat lunak perencanaan pemeliharaan seperti sistem manajemen pemeliharaan terkomputerisasi (CMMS) dan peringatan berdasarkan interval waktu yang telah ditentukan. Pemicu berbasis waktu digunakan dalam program perawatan prediktif dan preventif untuk tugas-tugas sederhana seperti melumasi roda gigi atau menjadwalkan inspeksi. Misalnya, saat aset mencapai runtime 14 hari, peringatan dipicu untuk memperbaikinya. Di luar pengaturan manufaktur, pemicu berbasis waktu akan mengubah filter udara unit pemanas, ventilasi, dan pendingin udara (HVAC) Anda setiap tiga bulan.
- Pemicu berbasis penggunaan. Mirip dengan pemicu berbasis waktu, pemicu berbasis penggunaan bergantung pada metrik yang telah ditentukan sebelumnya berdasarkan penggunaan aset yang bersangkutan, terlepas dari jangka waktunya. Tidak seperti pemicu berbasis waktu, yang dilakukan secara teratur terlepas dari kondisi mesin, pemicu berbasis penggunaan berarti aset hanya mendapatkan pemeliharaan setelah menyelesaikan sejumlah layanan tertentu.
Sama seperti mobil Anda yang mengganti oli setiap 5.000 mil, mesin apa pun yang melakukan operasi dengan batasan waktu atau kuantitas dapat disetel dengan pemicu berbasis penggunaan. Pembacaan meteran dapat ditambahkan ke CMMS dan digunakan untuk mengatur peringatan ketika jumlah atau nilai yang diinginkan tercapai. Pemicu berbasis penggunaan adalah cara yang bagus untuk memelihara peralatan yang tunduk pada jadwal yang tidak teratur dan paling sering digunakan dengan program pemeliharaan prediktif atau preventif.
- Pemicu berbasis peristiwa. Pemicu peristiwa dapat digunakan untuk menanggapi dan menilai peralatan atau fasilitas setelah peristiwa seperti kebakaran atau banjir terjadi. Misalnya, kebutuhan untuk menjadwalkan dan melakukan pemeriksaan sistem kelistrikan dan infrastruktur setelah banjir dapat didorong oleh CMMS, dengan sistem yang memberi tahu tim pemeliharaan tentang tugas tersebut. Meskipun pemicu berbasis peristiwa terjadi setelah suatu peristiwa terjadi, pemicu tersebut mungkin tidak semuanya terhubung langsung ke peristiwa itu sendiri. Sebagian besar pemicu berbasis peristiwa bertindak sebagai pemeriksaan tindak lanjut untuk suatu peristiwa.
- Pemicu berbasis kondisi. Pemicu berbasis kondisi digunakan sesuai dengan penilaian aset individu. Penilaian tersebut digunakan untuk menentukan apakah aset dapat terus berjalan atau jika pemeliharaan diperlukan. Ini adalah pilihan yang lebih mendalam karena memerlukan personel pemeliharaan untuk memiliki pengetahuan tentang aset untuk membuat keputusan yang tepat tentang kondisinya.
Kondisi peralatan juga dapat dinilai dari jarak jauh. Sensor yang ditempatkan pada aset untuk memantau parameter seperti suhu, getaran, dan kebisingan dapat digunakan sebagai peringatan yang dipicu oleh kondisi. Misalnya, jika sensor melihat lonjakan suhu yang melampaui rentang yang telah ditentukan, peringatan akan dikirim untuk menjadwalkan inspeksi.
Teknologi Pemeliharaan Modern
Salah satu kunci terbesar bagi produsen untuk unggul dalam pemeliharaan operasional adalah dengan menggunakan data yang disediakan oleh teknologi modern. Untuk melakukan ini, solusi pemeliharaan baru diperlukan untuk menjaga aset, karyawan, dan proses tetap teratur dan bekerja dengan lancar.
Kemajuan teknologi paling menonjol dalam pemantauan berbasis kondisi dalam bentuk pemeliharaan proaktif dan prediktif. Di bawah jenis perawatan ini, teknologi seperti analisis oli, analisis getaran, termografi, dan analisis arus motor dapat membantu menentukan akar penyebab dan gejala kegagalan, mencari manfaat seperti perpanjangan masa pakai alat berat dan deteksi kesalahan dini, serta mengurangi jumlah dan dampak kegagalan.
Revolusi teknologi saat ini dalam industri manufaktur telah menghasilkan lebih sedikit kesalahan dan cacat, produksi yang dioptimalkan, dan biaya tenaga kerja yang berkurang. Sensor otomatis yang dapat terus memantau mesin adalah salah satu peningkatan terbesar. Mereka tidak hanya dapat digunakan di berbagai jenis pemeliharaan, tetapi juga dapat menghasilkan sejumlah besar data yang dapat dianalisis dan digunakan untuk meningkatkan proses.
Solusi CMMS dapat membantu memanfaatkan semua data ini dan mengintegrasikannya dengan empat aspek utama untuk strategi teknologi pemeliharaan modern:menggunakan pemeliharaan prediktif, berfokus pada data dan IoT, mengelola inventaris, dan meningkatkan siklus untuk kesuksesan yang berkelanjutan.
Tren Teknologi Pemeliharaan Modern
- Internet of Things Industri: Seperti yang telah dibahas sebelumnya, internet of things, dan lebih khusus lagi industrial internet of things (IIoT), adalah bentuk modern dari pengumpulan data otomatis melalui penggunaan jaringan sensor nirkabel. Saat ini, sensor multiguna berbiaya rendah lebih tersedia daripada sebelumnya. Mereka dapat dikonfigurasi ke dalam jaringan sensor yang berbeda pada beberapa aset industri dan digunakan untuk mengumpulkan data pemeliharaan secara otomatis. Ini menghilangkan kebutuhan akan data manual yang mahal dan memakan waktu, yang rentan terhadap kesalahan manusia.
- Augmented Reality (AR): Pemeliharaan dan pelatihan jarak jauh mulai mendapat manfaat dari AR berkat kemampuan untuk menawarkan instruksi jarak jauh. Pendekatan yang disesuaikan ini memungkinkan tugas pemeliharaan disesuaikan dengan pemahaman dan tingkat keterampilan karyawan. Augmented reality dapat memfasilitasi pelatihan yang diberikan oleh vendor peralatan atau personel pemeliharaan tingkat senior melalui presentasi dunia maya yang menunjukkan cara melakukan tugas.
Meskipun masih merupakan tren yang muncul, penggunaan AR untuk pelatihan semakin populer karena meningkatnya kompleksitas peralatan industri. Augmented reality dapat meringankan beban personel pemeliharaan yang mencoba mengikuti variasi peralatan baru, termasuk kemampuan berteknologi canggih yang menyertai setiap aset. Sudah ada beberapa vendor yang menawarkan solusi AR skala besar untuk tugas pemeliharaan dan penyedia IIoT yang menyediakan AR sebagai bagian dari paket yang dibundel.
- Pemeliharaan sebagai Layanan (MaaS): MaaS adalah paradigma yang cukup baru untuk dunia pemeliharaan. Ini pada dasarnya melibatkan memberikan layanan pemeliharaan sesuai permintaan. Dengan MaaS, vendor dapat membebankan biaya kepada operator pembangkit sesuai dengan layanan pemeliharaan yang sebenarnya dia gunakan alih-alih biaya layanan tetap. Vendor melakukan ini dengan mengumpulkan dan memproses data dalam jumlah besar, menyimpannya melalui cloud dan menjadwalkan tugas berdasarkan data ini. Layanan meliputi:
- memprediksi masa pakai aset atau menawarkan wawasan tentang interval perawatan yang optimal;
- menyediakan manual layanan, video, dan virtual reality (VR) dan dukungan interaktif AR;
- mengonfigurasi teknologi informasi (TI) dan sistem lain di dalam pabrik berdasarkan hasil analisis; dan
- memberikan statistik dan laporan terperinci tentang mesin.
Tahap awal program MaaS mulai disediakan oleh vendor. ThyssenKrupp Elevators kini hadir dengan program pemeliharaan proaktif yang memprediksi masalah sebelum terjadi dan memberi tahu individu yang tepat untuk melakukan pemeriksaan. BMW juga berencana untuk membawa MaaS ke konsumen dalam waktu dekat, menawarkan program yang akan memberi tahu pemilik mobil waktu terbaik untuk melakukan perawatan pada kendaraan mereka.