Pengadukan Elektromagnetik dalam Proses Pengecoran Berkelanjutan
Pengadukan Elektromagnetik dalam Proses Pengecoran Berkelanjutan
Dalam proses pengecoran kontinyu baja cair, metode peningkatan kualitas produk baja cor selalu penting. Ini juga tetap penting untuk pengembangan proses. Selain memodifikasi sudut aliran jet dan membentuk kembali bentuk submerged entry nozzle (SEN), teknik elektromagnetik yang mampu mengontrol aliran fluida tanpa kontak antara baja cair dan pengaduk telah digunakan sebagai teknik kontrol aliran. Salah satu jenis teknik elektromagnetik adalah pengadukan elektromagnetik (EMS), yang menghasilkan aliran fluida dengan gaya Lorenz yang diberikan oleh motor induksi linier. Teknologi EMS telah digunakan dalam pengecoran baja terus menerus selama beberapa tahun tetapi efek dari aplikasi dan manfaat selanjutnya dari mengaduk inti cair sangat bergantung pada ukuran bagian, kadar baja, dan aplikasi produk.
Sejak penerapan pertama prinsip pengecoran kontinu pada baja dalam mesin uji pengecoran kontinu Junghans di bekas Jerman Barat, kualitas produk cor kontinu semakin diperhatikan. Dalam beberapa tahun terakhir dengan tekanan pada produksi baja bersih, ada persyaratan yang lebih tinggi untuk struktur mikro dan homogenisasi komposisi produk cor. Komposisi kimia, kondisi pemadatan, dan sifat aliran baja cair dalam cetakan mempengaruhi kualitas permukaan dan struktur bagian dalam produk cor. Penerapan teknik EMS mempromosikan pembentukan zona kristal equiaxed di untai. Ini menyebabkan penyempurnaan struktur pemadatan, pengurangan kandungan inklusi, dan peningkatan kualitas permukaan, sub permukaan, dan struktur bagian dalam produk cor.
Pada proses continuous casting, baja cair disuntikkan ke dalam cetakan. Cangkang baja akhir diperoleh setelah pemadatan yang dimulai dalam cetakan dan berlanjut di untaian. Perangkat elektromagnetik seperti pengaduk dan rem adalah teknologi terkenal yang digunakan untuk meningkatkan kualitas produk cor akhir dan kecepatan pengecoran. Cacat utama cangkang akhir dalam hal struktur mikro dan retak permukaan dapat berhubungan langsung dengan fenomena dalam cetakan seperti variasi suhu, kecepatan dan tekanan baja cair, perilaku permukaan bebas, dan terak entrainment yang merupakan beberapa penyebab utama. cacat pada produk akhir. Perlu disebutkan bahwa ada satu jenis perangkat elektromagnetik lain yang juga digunakan dalam mesin pengecoran kontinu dan disebut pengereman elektromagnetik (EMBR). Perangkat ini sebagian besar dipasang di cetakan dan menyerupai EMS linier tetapi memiliki arus searah, bukan arus bolak-balik.
EMS adalah teknik langsung dan kuat untuk mengendalikan proses pemadatan dalam pengecoran baja cair secara terus menerus. Sebuah signifikan, tetapi bukan satu-satunya keuntungan dari EMS, peningkatan kualitas dan keseragaman struktur dan kimia di garis tengah dari produk cor. Keunggulan produktivitas menyertai peningkatan kualitas. Hasil percobaan telah menunjukkan efek menguntungkan dari EMS pada mikrostruktur baja, misalnya dengan meningkatkan lebar zona equiaxed. Beberapa jenis cacat pada untaian dapat dikurangi secara efektif besarnya dengan penerapan EMS. Gelembung dan porositas juga diperkirakan akan sangat dipengaruhi oleh EMS. Lebih lanjut dilaporkan bahwa EMS meningkatkan hasil dan produktivitas proses pengecoran kontinu.
Penerapan EMS pada proses pengecoran kontinyu memiliki sejarah yang relatif panjang dan percobaan pertama EMS kembali ke tahun 1960-an. EMS diperkenalkan ke mesin pengecoran kontinyu kira-kira satu dekade setelah proses pengecoran kontinyu mulai memproduksi baja secara industri. Telah ditunjukkan bahwa EMS juga mempengaruhi inklusi dan gelembung. Strand EMS membuka pintu penerapan nyata EMS ke mesin continuous casting pada akhir 1970-an. Tujuan dari EMS strand adalah untuk memperoleh rasio zona equiaxed yang tinggi untuk tujuan menekan segregasi pusat. Setelah itu, EMS dalam cetakan (Gbr 1) telah dikembangkan untuk meningkatkan kualitas permukaan produk baja tuang dengan menekan jebakan inklusi non-logam dan gelembung argon ke cangkang yang dipadatkan.
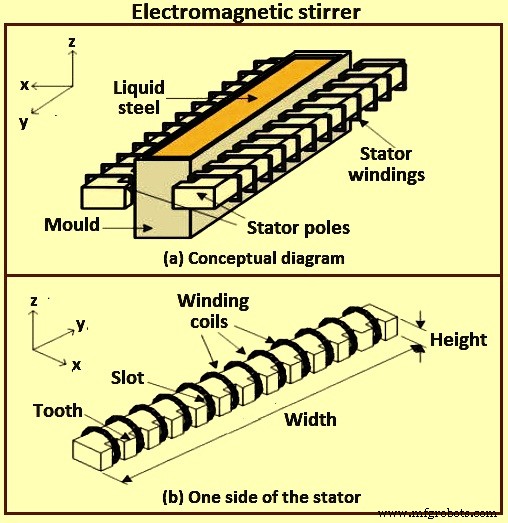
Gbr 1 Pengaduk elektromagnetik
Untuk mencapai produktivitas yang tinggi dari proses pengecoran kontinyu, EMBR telah dikembangkan pada tahun 1980-an untuk menstabilkan aliran baja cair dalam cetakan pengecoran kontinyu. Jenis EMBR yang pertama adalah menciptakan medan magnet lokal di mana sepasang magnet DC (arus searah) telah dipasang di sekitar port SEN. Medan yang dipaksakan 'mengrem' aliran yang dikeluarkan dari SEN secara langsung. Jenis EMBR kedua adalah medan magnet tingkat dimana medan magnet seragam dalam arah lebar cetakan mengembangkan aliran seperti sumbat di bawah area medan magnet. Salah satu jenis EMBR jenis kedua adalah cetakan kontrol aliran (FC) (di mana pengenaan sepasang medan magnet tingkat di bagian atas cetakan pengecoran kontinu, secara bersamaan menstabilkan aliran meniskus dan aliran turun di sepanjang permukaan cetakan yang sempit. ). Saat ini, kombinasi EMS dan EMBR juga telah dikembangkan.
Dengan tujuan untuk mengontrol proses dan mencegah produk akhir dari cacat, proses telah diperbaiki dengan perangkat elektromagnetik seperti EMS dan EMBR. Perbedaan utama adalah bahwa pengaduk bekerja di bawah suplai arus AC (arus bolak-balik) dan menghasilkan medan magnet yang dinamis. Rem adalah magnet permanen atau sirkuit yang dialiri arus DC (arus searah). Oleh karena itu mereka menghasilkan medan magnet konstan. Terlepas dari perbedaan mereka didasarkan pada gagasan yang sama bahwa superposisi medan magnet ke aliran logam menghasilkan gaya Lorentz yang dapat menggerakkan aliran sesuai dengan desain proses. Fenomena fisika yang terjadi pada cetakan merupakan masalah multifisika yang meliputi aliran cair, analisis multifase, komputasi elektromagnetik, perpindahan panas dan proses solidifikasi dimana masing-masing fisika ini bergantung satu sama lain.
Telah diketahui dengan baik bahwa medan magnet bolak-balik (fase tunggal atau multifase) diterapkan pada konduktor, baik padat atau cair, menginduksi arus listrik dalam konduktor, dan karenanya merupakan distribusi gaya Lorentz. Gaya Lorentz ini pada umumnya adalah rotasi, dan jika konduktornya cair, maka konduktor tersebut akan bergerak. Dengan demikian medan magnet bertindak sebagai alat pengaduk yang tidak mengganggu dan pada prinsipnya dapat direkayasa untuk memberikan pola pengadukan yang diinginkan. Pengadukan juga dapat dipengaruhi melalui interaksi distribusi arus tetap yang digerakkan melalui fluida dan medan magnet terkait. Ketika frekuensi medan tinggi, gaya Lorentz terbatas pada lapisan batas elektromagnetik tipis, dan efek bersih medan magnet adalah menginduksi kecepatan tangensial atau tegangan tangensial tepat di dalam lapisan batas. Distribusi kecepatan atau tegangan terkait dengan struktur medan yang diterapkan. Konfigurasi simetris dapat menyebabkan pola pengadukan di mana garis arus terletak pada permukaan toroidal, namun lebih normal, pola garis arusnya kacau.
Aliran di daerah cetakan dikendalikan oleh nosel dan geometri cetakan, kecepatan pengecoran, kedalaman perendaman nosel, injeksi gas argon, dan penerapan gaya elektromagnetik. Gaya elektromagnetik secara opsional diterapkan sebagai medan magnet statis atau bergerak melalui ketebalan untai. Medan elektromagnetik statis (DC) menginduksi arus dalam baja cair penghantar, yang pada gilirannya, menghasilkan gaya yang secara langsung menentang aliran, sehingga disebut sebagai 'rem', atau 'EMBR'. Bidang EMBR mencakup bidang berbentuk silinder lokal, bidang magnet 'berbentuk penggaris' lebar di seluruh lebar cetakan, dan bidang penggaris ganda, kadang-kadang disebut sebagai bidang 'kontrol aliran', atau 'cetakan FC'.
Gaya elektromagnetik merupakan alat penting untuk mengontrol aliran fluida dalam cetakan, dikombinasikan dengan kondisi pengecoran lainnya, nozzle, dan geometri cetakan. Metode termasuk medan magnet statis (EMBR lokal dan penggaris), dan medan magnet yang berubah-ubah waktu, seperti EMS, EMS multi-mode, penstabil level elektromagnetik (EMLS), dan akselerator level elektromagnetik (EMLA). Penggunaan yang optimal dapat menstabilkan aliran, menghasilkan lebih sedikit cacat permukaan, lebih sedikit inklusi, dan meningkatkan struktur mikro.
Medan bergerak (AC) berasal dari pengadukan elektromagnetik (EMS), di mana pergeseran fase medan dari beberapa seri magnet untuk membuat medan bersih bergerak dalam arah yang berlawanan di sisi berlawanan dari untai menginduksi aliran berputar, biasanya dalam bidang melintang di cetakan (M-EMS) atau pengadukan putar elektromagnetik (EMRS). Membuat medan bergerak ke arah yang sama, kadang-kadang disebut 'multi-mode EMS', dapat menginduksi aliran percepatan (EMLA), atau aliran perlambatan (EMLS). Gaya elektromagnetik menawarkan keuntungan dibandingkan parameter kontrol aliran lainnya karena gaya induksi bervariasi dengan kekuatan aliran baja cair, memberikan sistem kemampuan teoretis untuk menstabilkan diri untuk variasi aliran turbulen. Dalam praktiknya, hal ini sulit untuk dicapai.
Prinsip EMS
EMS menggunakan prinsip motor linier. Ini berbeda dari jenis mekanis dan dekompresi konvensional karena merupakan pengaduk non-kontak di mana tidak ada bagian yang menyentuh baja cair. Seperti ditunjukkan pada Gambar 2a, sebuah kumparan yang dipasang di bagian bawah tungku menghasilkan medan magnet yang bergerak (H), jika tegangan AC 3 fasa diterapkan pada kumparan ini (induktor). Gaya daya listrik dihasilkan dalam baja cair karena aksi medan magnet dan menyebabkan arus induksi (I) mengalir (aturan tangan kanan Fleming). Arus ini kemudian bekerja dengan medan magnet induktor untuk menginduksi gaya elektromagnetik (F) dalam baja cair sesuai dengan aturan tangan kiri Fleming. Gaya ini dikenal sebagai gaya Lorentz.
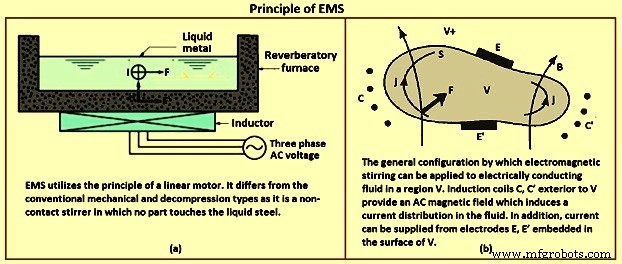
Gambar 2 Prinsip EMS
Pengaduk elektromagnetik rotasi setara dengan stator motor asinkron. Biasanya disuplai oleh konverter frekuensi tiga fase atau terkadang dua fase. Medan magnet berputar dihasilkan yang variasinya di dalam baja cair menghasilkan arus eddy, yang berinteraksi dengan medan magnet, menghasilkan gaya (gaya Lorentz). Hasil akhirnya adalah terjadinya torsi yang menginduksi putaran baja. Torsi yang dihasilkan tergantung pada beberapa faktor yaitu (i) intensitas arus yang disuplai, (ii) jumlah belitan yang membentuk kumparan, (iii) frekuensi, dan (iv) geometri sistem. Parameter ini berubah tergantung pada jenis pengaduk M-EMS (pengaduk elektromagnetik cetakan), S-EMS (pengaduk elektromagnetik untai), dan (iii) F-EMS (pengaduk elektromagnetik akhir).
Oleh karena itu, medan magnet bertindak sebagai perangkat pengadukan non-intrusif dan pada prinsipnya dapat direkayasa untuk memberikan pola pengadukan yang diinginkan. Desain, ukuran, dan posisi pengaduk, dll. bergantung pada data mesin pengecoran kontinu, nilai baja yang akan diproduksi, dan parameter pengecoran.
Sistem EMS menciptakan medan induksi magnet yang berputar dengan induksi B, yang menginduksi arus eddy j dalam arah tegak lurus terhadap B, yang kecepatannya v. Induksi B dan arus j menciptakan gaya elektromagnetik, yang bekerja pada setiap satuan volume baja dan menghasilkan gerakan pengadukan dalam baja cair. Produk vektor (v x B) menunjukkan hubungan antara medan elektromagnetik dan aliran baja cair. Kecepatan baja cair yang disebabkan oleh EMS berkisar antara 0,1 meter per detik (m/s) hingga 1,0 m/s.
Ketika arus listrik j(x,t) mengalir melalui benda konduktor, baik padat atau cair, dengan adanya medan magnet B,(x,t), ada gaya F per satuan volume (gaya Lorentz) diberikan dengan persamaan F =j x B yang bekerja pada konduktor. Secara umum, gaya ini adalah rotasi, yaitu, curl F tidak sama dengan nol, dan, jika konduktor adalah cairan, itu tidak dapat dikompensasi oleh gradien tekanan. Dalam keadaan ini, cairan harus bergerak sebagai respons terhadap gaya. Ini, dalam istilah yang paling sederhana, adalah prinsip pengadukan elektromagnetik.
Dengan mempertimbangkan cairan mampat terbatas pada volume terbatas V dengan permukaan S, dan biarkan V+ menjadi daerah luar. Di dalam konduktor, B dan j dihubungkan oleh hukum Ampere (Mo)j =curl B, V x B =0, di mana Mo =4 (pi) x (10)-7 (dalam satuan SI). Medan magnet juga dapat memiliki sumber eksternal, misalnya arus (AC atau DC) dalam kumparan di domain luar V+. Situasi normal yang dapat dipertimbangkan digambarkan pada Gambar 2b. Arus dalam kumparan eksternal C, C’, melalui hukum Faraday, menginduksi distribusi arus dalam konduktor. Arus ini dapat diperbesar dengan penerapan langsung perbedaan potensial antara elektroda E, E’ yang tertanam dalam batas S. Oleh karena itu, arus dapat diinduksi melalui penerapan medan magnet yang bergantung pada waktu, atau secara elektrik, atau keduanya. Rentang kondisi fisik yang sangat luas dan rentang aplikasi yang sama luasnya khususnya di bidang pemrosesan metalurgi dapat dipertimbangkan.
Terlepas dari pentingnya praktis yang besar dari beberapa aplikasi ini, dan fakta bahwa prinsip-prinsip dasar EMS dipahami dengan baik, pemahaman tentang aliran yang dihasilkan oleh EMS di semua tetapi keadaan yang paling ideal masih pada tingkat yang cukup primitif.
Kategori EMS
EMS dapat dikategorikan berdasarkan tempat pemasangannya di mesin pengecoran. Menurut posisi penyetelan dan aspek metalurgi, semua pengaduk elektromagnetik dapat diklasifikasikan menjadi tiga jenis. Tiga aplikasi pengaduk yang mungkin sesuai dengan posisi dan efek yang dibutuhkan pada produk baja tuang adalah (i) M-EMS, (ii) S-EMS, dan (iii) F-EMS. M-EMS terletak di cetakan, seperti namanya. Ini adalah pengadukan dalam cetakan (kadang-kadang disebut sebagai EMS primer). S-EMS terletak di bawah cetakan di wilayah pendinginan sekunder. Ini adalah pengadukan di bawah cetakan di mana masih ada sebagian besar baja cair (kadang-kadang disebut sebagai EMS sekunder atau pengadukan di bawah cetakan). FEMS terletak di ujung panjang metalurgi (tepat sebelum pemadatan selesai) Ini adalah pengadukan sesaat sebelum titik pemadatan akhir (disebut sebagai EMS akhir). Gambar 3 menunjukkan tiga jenis utama pengadukan.
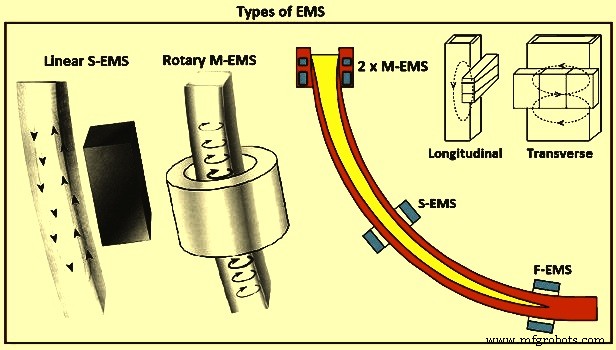
Gbr 3 Jenis EMS
M-EMS – M-EMS tipe putar biasanya merupakan pilihan pertama saat memilih peralatan pengadukan billet / bloom. Medan magnet berputar yang dihasilkan memberikan gerakan melingkar pada baja cair (Gambar 3). Zona pusat equiaxed diperbesar karena aliran rotasi mempromosikan rekahan ujung dendrit kolumnar, yang kemudian berfungsi sebagai inti untuk formasi kristal equiaxed di zona pusat. Selanjutnya, aliran rotasi menyiram bagian depan pemadatan, sehingga mencegah inklusi dan gelembung gas terperangkap. Lebih jauh lagi, gaya sentrifugal yang dikembangkan menghasilkan fase yang lebih ringan (yaitu inklusi dan gelembung gas yang bergerak menuju pusat untai menjauhi bagian depan pemadatan.
Linear M-EMS digunakan untuk bagian untai persegi panjang yang lebih besar. Dua pengaduk kemudian ditempatkan secara horizontal di sepanjang sisi lebar produk cor, dan manfaatnya serupa dengan yang diperoleh dengan pengadukan putar. M-EMS secara tradisional dibangun ke dalam cetakan dalam desain internal, di mana koil dilepas dari kastor dengan cetakan. Untuk setiap pertukaran cetakan, kabel listrik dan kemungkinan selang air harus dihubungkan / diputuskan ke koil. Mesin pengecoran baru memiliki desain eksternal di mana kumparan dibangun di sekitar cetakan dan tetap berada di dalam kastor selama pertukaran cetakan.
M-EMS biasanya dipasang di bagian bawah cetakan untuk mengaduk baja cair dalam cetakan. Ini meningkatkan kualitas permukaan, sub permukaan, dan untai dalam. Penerapan hasil M-EMS ke dalam pengurangan lubang kecil, porositas pusat, dan segregasi pada produk cor. Ini meningkatkan struktur pemadatan, mengurangi kekasaran permukaan, dan meningkatkan laju pengiriman panas. M-EMS adalah desain bulat atau persegi dan dapat dipasang secara internal atau eksternal. Untuk memberikan kontrol kecepatan pengadukan yang fleksibel dalam meniskus cetakan, M-EMS kumparan ganda (Gbr 6) telah dikembangkan. Kumparan ganda M-EMS terdiri dari dua EMS independen. EMS atas dimaksudkan untuk kontrol aliran di meniskus dan EMS bawah melakukan pengadukan logam utama dalam cetakan. Pengurangan kecepatan baja cair di meniskus dicapai dengan memutar medan magnet EMS atas ke arah yang berlawanan dengan EMS bawah. Desain M-EMS ganda seperti itu memperluas peluang untuk menggunakan teknik EMS dalam berbagai kondisi pengecoran baja kontinu.
S-EMS – Dalam S-EMS linier, kumparan elektromagnetik dipasang di sepanjang satu sisi untai dan menghasilkan pola aliran logam cair sirkulasi vertikal di untai (Gbr 3). Saat pengaduk ditempatkan di sepanjang satu sisi untai, itu dapat digunakan untuk ukuran untai yang sangat berbeda. Peningkatan zona kristal equiaxed pusat diperoleh dengan mekanisme yang sama seperti yang diperoleh dengan pengaduk putar. Inklusi, yang biasanya terkonsentrasi dalam pita yang dekat dengan permukaan atas dalam mesin pengecoran kontinu cetakan melengkung, juga didistribusikan secara lebih merata. S-EMS putar yang ditempatkan pada posisi optimal tinggi di bawah cetakan sensitif terhadap breakout.
S-EMS menghasilkan gaya pengadukan yang mendorong baja cair secara horizontal sepanjang lebar produk cor dan menghasilkan pola aliran tipe kupu-kupu dalam baja cair. Ketika S-EMS dapat ditempatkan di belakang rol pendukung (Gbr 4) maka S-EMS tidak tergantung pada diameter minimum rol pendukung dan karenanya dalam hal ini dapat ditempatkan secara optimal di sepanjang untai dari sudut pandang metalurgi. S-EMS saat dipasang ke dalam roller pendukung membutuhkan diameter roller minimum untuk menyertakan inti besi dan belitan. Dalam hal ini pengaduk ditempatkan pada jarak dari meniskus dan karenanya kurang efektif. S-EMS beroperasi pada frekuensi rendah untuk memastikan penetrasi yang baik dari gaya pengaduk melalui untai. Akibatnya, baja cair mengalami pengadukan melintang seperti yang ditunjukkan pada Gambar 3. S-EMS biasanya digunakan dalam kombinasi dengan M-EMS. S-EMS dapat berupa pengaduk tipe linier atau putar. Yang paling umum adalah pengaduk linier, yang mudah dipasang dan dilindungi dari radiasi panas dan kemungkinan berjerawat. S-EMS mempromosikan pembentukan struktur equiaxed. Ini mempromosikan penyempurnaan butir dalam produk cor dan mengurangi rongga susut, segregasi pusat, dan retakan internal. Ini juga menghilangkan panas berlebih secara efektif.
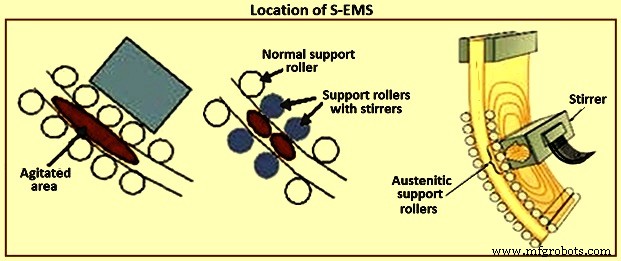
Gbr 4 Lokasi S-EMS
F- EMS – Ada minat yang sama kuatnya dalam menggunakan EMS untuk mengaduk jauh di bawah cetakan di zona pemadatan akhir dari untai pengecoran kontinu. Namun, sistem EMS konvensional terbukti agak tidak efektif bila diterapkan di wilayah ini. Sebagai solusi potensial, baru-baru ini ada minat yang cukup besar dalam menerapkan gaya Lorentz termodulasi untuk mengembangkan pengadukan kuat yang terdistribusi secara luas di zona akhir. F-EMS biasanya dipasang dalam kombinasi dengan M-EMS atau S-EMS untuk mengurangi dan memotong puncak di segregasi pusat. F-EMS sangat efisien saat pengecoran baja karbon tinggi atau baja paduan tinggi. Juga dengan penggunaan F-EMS, ditemukan bahwa struktur pemadatan produk cor ditingkatkan dan ada peningkatan rasio struktur equiaxed dan porositas bagian dalam. Penyusutan berkurang, dan rasio segregasi karbon pusat berkurang. Selanjutnya jarak lengan dendrit sekunder (SDAS) ditingkatkan, dan rasio butir pusat equiaxed jauh meningkat, yang menghasilkan butir lebih halus. Oleh karena itu, kualitas produk cor ditingkatkan dengan F-EMS.
Pada dasarnya, ada dua jenis pengadukan yang diterapkan pada pengadukan 'putar' pengecoran kontinu dan pengadukan 'atas dan bawah' (atau aksial) (Gbr 5). Di masa lalu, beberapa versi jenis pengadukan ini telah diusulkan dalam banyak paten, beberapa lebih canggih daripada yang lain, tetapi semua atau hampir semuanya dapat diklasifikasikan dalam salah satu kategori yang disebutkan di atas.
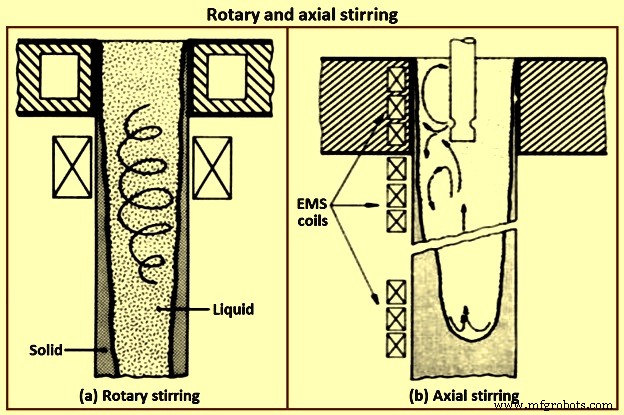
Gbr 5 Pengadukan putar dan aksial
Medan elektromagnetik di EMS dibuat dalam tiga cara berbeda yang meliputi pengaduk linier, pengaduk putar, dan pengaduk konduktif. Kutub magnet pengaduk linier terletak pada garis lurus dan kutub magnet pengaduk putar terletak pada lingkaran. Pengaduk elektromagnetik linier dan putar menggunakan AC untuk menghasilkan medan magnet dan efek yang diinginkan. Pengaduk elektromagnetik linier dan putar menginduksi arus dalam baja. Pengadukan konduktif, di sisi lain, menggunakan arus konduksi ditambah arus induksi untuk menghasilkan medan elektromagnetik dan efek yang diinginkan. Rotary EMS dipasang baik di cetakan maupun di daerah pendinginan sekunder, sedangkan EMS linier banyak digunakan sebagai perangkat S-EMS. Pengadukan konduktif adalah niche dibandingkan dengan dua mode lainnya.
Pengadukan putar – Karya asli tentang pengadukan putar dilakukan oleh sekelompok peneliti di Austria. Billet yang dicetak dalam cetakan bulat diaduk pada tingkat cetakan atau tepat di bawah cetakan. Memang, cetakan adalah satu-satunya area yang memungkinkan pengadukan berputar. Mengaduk secara substansial di bawah cetakan dengan cara berputar dapat menimbulkan lebih banyak masalah daripada yang dapat dipecahkannya. Seperti yang dinyatakan, ada beberapa manfaat dalam pengadukan putar putaran dalam cetakan. Inklusi padat dihilangkan dari permukaan pengecoran dan perpindahan panas ditingkatkan dengan memaksa kulit padat untaian berada dalam kontak yang lebih baik dengan cetakan. Tidak ada bahaya pecahnya kulit dengan pengadukan berputar di dalam cetakan. Tetapi keuntungan utama dari pengadukan putar adalah kemudahan desain peralatan. Insinyur listrik sangat akrab dengan jenis gerakan yang diinduksi secara elektromagnetik ini karena sama dengan hampir semua motor listrik yang digunakan saat ini.
Sementara gerakan berputar, tidak menimbulkan masalah desain teknik, ini mungkin bukan jenis gerakan terbaik dari sudut pandang metalurgi. Salah satu masalah dasar dengan pengadukan putar adalah bahwa cairan dikenai gaya sentrifugal yang cenderung memisahkan konstituen ringannya (misalnya inklusi) ke arah pusat (Gambar 5). Ini memberlakukan batas atas pada kecepatan cairan, yang belum tentu batas yang sama yang ditetapkan oleh munculnya efek 'bingkai gambar'. Kadang-kadang pertimbangan ini dapat diabaikan, seperti ketika melakukan casting untuk pipa tanpa sambungan, mungkin. Namun, batasan lain yang lebih tidak fleksibel tidak dapat diabaikan. Meningkatkan kecepatan melingkar cairan secara tidak proporsional meningkatkan tekanan pada cangkang padat, yang kemudian dapat pecah. Bahaya ini sangat akut ketika pengecoran grade baja yang mengandung elemen yang sangat memisahkan, seperti fosfor, selenium, dan timbal. Cairan leleh rendah yang terbentuk dari konstituen ini menempati ruang di antara dendrit yang mengurangi kekuatan apa pun yang dimiliki cangkang.
Situasi lain yang tidak diinginkan yang muncul ketika pengadukan di bawah cetakan dengan cara berputar, terutama bila dilakukan dalam satu tingkat saja, adalah pemisahan efektif kolam cairan menjadi dua bagian, bagian atas (panas) di atas tingkat pengadukan dan bagian bawah. (dingin) di bawah tingkat pengadukan. Selain mengganggu aliran alami di dalam kolam, sekat ini juga dapat menyebabkan masalah bridging. Menjembatani, pada gilirannya, mengintensifkan segregasi makro seperti yang dapat ditunjukkan oleh beberapa masalah yang dilaporkan baru-baru ini ketika pengadukan putar telah diterapkan di bawah cetakan saja. Masalah seperti itu sangat mungkin terjadi ketika mengaduk dengan kecepatan rendah. Fragmen besar dendrit yang terpisah dari zona lembek di daerah yang diaduk tidak dapat dikurangi ukurannya karena intensitas pengadukan yang rendah. Fragmen besar ini tenggelam ke bagian bawah (dingin) kolam di mana mereka memiliki kesempatan untuk tumbuh, membentuk kelompok, dan menyebabkan bridging.
Ada kerugian lain dari pengadukan putar. Data awal telah menunjukkan bahwa untuk mengurangi secara substansial ukuran inklusi dan kandungan baja oleh EMS, kecepatan cairan harus melebihi batas bawah tertentu. Misalnya, untuk grade baja AISI 4335, batas ini telah terbukti lebih dari 0,5 m/s, yang sebanding dengan kecepatan yang terjadi selama tindakan rimming pada ingot besar di mana kulit bersih juga dihasilkan. Hampir pasti bahwa batas atas yang disebutkan sebelumnya, untuk gerakan cairan putar yang aman, bertentangan dengan persyaratan kecepatan tinggi untuk pengurangan inklusi. Hal yang sama juga berlaku untuk menghasilkan struktur solidifikasi baru, yaitu struktur berserat dan struktur aliran termodifikasi atau thamnitic, yang juga membutuhkan kecepatan tinggi. Segmen industri baja yang secara agresif mengejar perkembangan baru untuk kualitas, secara umum, dan pengadukan induksi dapat segera mengejar struktur ini melalui pengadukan kecepatan tinggi.
Aduk aksial – Versi pengadukan aksial atau 'atas dan bawah' menyediakan untuk memindahkan bagian cair dari untaian yang mengeras ke arah yang sejajar dengan sumbu untaian, jenis gerakan yang diinduksi ini dapat digunakan untuk mengintensifkan yang terjadi secara alami, diinduksi secara termal, pola aliran konveksi. Di area cetakan, ada alasan untuk membalikkan aliran alami. Dalam pengecoran kontinyu baja, area cetakan merupakan bagian kecil dari kolam cairan yang dapat sedalam 15 m atau lebih (tergantung pada kecepatan dan ukuran mesin). Di bawah cetakan, alirannya 'bawah' berdekatan dengan kulit padat dan 'naik' di tengah untaian.
Versi 'naik dan turun' dari EMS adalah yang paling tepat dari sudut pandang metalurgi. Kecepatan cairan praktis tidak terbatas dalam teknik ini, yang memberikan banyak kebebasan untuk penerapan kontrol yang diinginkan. Bahaya break-out diminimalkan, karena gaya yang diinduksi secara elektromagnetik cenderung mengandung cairan daripada memaksanya melawan cangkang padat. Ada manfaat utama lainnya. Cairan panas dari atas dibawa dengan cepat ke dasar kolam, yang cenderung mengurangi ketebalan cangkang dan menjaga gradien suhu tetap tinggi melintasi zona lembek. Kedua efek ini meningkatkan aliran panas, yang pada gilirannya dapat berguna untuk meningkatkan produktivitas mesin pengecoran kontinu. Ada cara lain untuk meningkatkan produktivitas dengan versi EMS ini. Kontur cangkang padat dapat dimodifikasi untuk membentuk dasar bulat dan kedalaman kolam berkurang. Hal ini memungkinkan kecepatan casting yang lebih tinggi. Tingkat penyusutan dan segregasi garis tengah dapat dikurangi juga, karena isoterm berubah dan pertumbuhan di pusat untai memiliki komponen ke atas yang meningkat.
Akhirnya, bahkan inklusi yang terbentuk selama pemadatan, seperti gugus alumina yang terkenal, tidak diizinkan untuk terperangkap dalam padatan, mereka tersapu dengan cepat ke atas kolam di mana mereka memiliki kesempatan untuk bergabung dengan terak (yaitu mengambang di atas meniskus) dan, karenanya, dihilangkan. Jenis aliran ini agak sulit untuk diterapkan, terutama jika pengadukan diterapkan pada bagian yang cukup besar sepanjang panjang metalurgi, yaitu versi pengadukan 'naik dan turun' yang berkelanjutan. Akan tetapi, perlu ditekankan bahwa kesulitan dalam kasus ini terletak pada sisi masalah teknik elektro. Relatif sulit untuk menerapkan aliran satu arah tanpa gangguan besar yang muncul baik di antara kumparan atau di ujung serangkaian kumparan yang membentuk motor linier. Anomali ini tercermin dalam struktur cor sebagai pita baik segregasi positif atau negatif. Selanjutnya, pengadukan 'atas dan bawah' biasanya membutuhkan area yang agak luas dari untaian yang bebas dari gulungan pendukung, atau setidaknya modifikasi gulungan, sehingga tidak mengganggu medan motor linier yang digunakan. Akhirnya, motor linier yang digunakan untuk jenis pengadukan ini memiliki efisiensi yang sangat rendah (berurutan 1% atau bahkan kurang), terutama karena resistensi yang tinggi dari loop elektromagnetiknya (celah udara besar dan celah kulit logam padat).
Pengadukan terbalik sesekali – Variasi mode pengadukan putar telah diusulkan, awalnya oleh beberapa peneliti Jepang. Teknik ini menyediakan arah aliran bolak-balik yang berselang-seling, yang diklaim dapat meningkatkan ukuran zona equiaxed. Diskusi di atas untuk pengadukan putar berlaku di sini, dengan beberapa kualifikasi lagi. Gerakan terputus-putus memang membuang energi, tetapi memiliki manfaat dalam memenuhi satu tujuan EMS, pertumbuhan kolumnar yang membuat frustrasi. Membalikkan aliran dalam pengadukan tidak hanya dapat memecah dendrit menjadi fragmen yang lebih kecil dengan menggeser sel turbulensi lokal, tetapi juga dapat menggagalkan pertumbuhan dendrit kolumnar yang searah, karena dendrit ini berusaha untuk tumbuh ke dalam aliran (hulu) sepanjang waktu. Namun, diragukan bahwa kemungkinan manfaat lain dari EMS dapat diperoleh dengan teknik ini.
Pengaruh pengadukan elektromagnetik pada kualitas produk baja tuang
Komposisi kimia, kondisi pemadatan dan sifat aliran baja cair dalam cetakan pada dasarnya mempengaruhi kualitas permukaan dan struktur bagian dalam untaian. Proses pembentukan untai meliputi pemadatan baja cair dalam cetakan dan di zona pendinginan sekunder (SCZ). Medan magnet yang berputar atau bergerak mempengaruhi sifat aliran dalam cairan dan mengintensifkan proses perpindahan panas-massa. Tingkat pengaruh pengadukan elektromagnetik pada kualitas untai tergantung pada karakteristik teknis EMS dan pada pengaturannya di sepanjang sumbu lentur pengecoran kontinu. EMS dapat berhasil dipasang di cetakan, di SCZ dan di zona pemadatan akhir (FCZ).
For improving the surface, subsurface, and inner strand quality, the liquid steel stirring has to take place in the mould. M-EMS is either of round or square design and it can be installed internally or externally. The result of applying M-EMS is a reduction in centre porosity and segregation in the cast product. To provide flexible control of stirring speed in the mould meniscus, the dual-coil M-EMS (Fig 6) has been developed. It consists of two independent EMS. The upper EMS is intended for flow control in the meniscus. The lower EMS performs the main metal stirring in the mould. The reduction in metal speed in the meniscus is achieved by rotating the upper EMS magnetic field in the opposite direction to that of the lower EMS. Such an M-EMS design widens the opportunities for using the technique under various conditions of continuous casting of liquid steel.
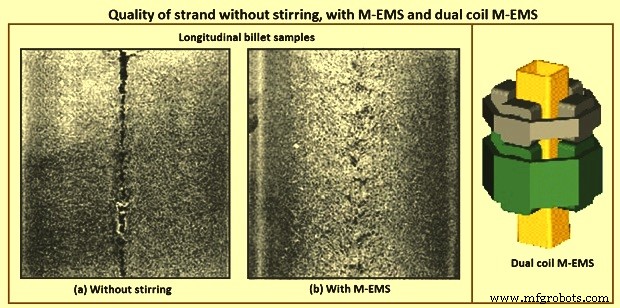
Fig 6 Quality of strand without stirring, with SMS, and dual coil M-EMS
The application of electromagnetic stirring of steels promotes the formation of an equiaxed crystallic zone in the strand. The stirring improves strand quality, even in steel casting with overheating. To further reduce and cut peaks in centre segregation, F-EMS, in combination with M-EMS or S-EMS, has to be used. F-EMS is particularly efficient when casting high carbon or high alloy steel grades. F-EMS and M-EMS combinations reduce the areas with the highest carbon content, where cementite and martensite otherwise can form. It has been found that stainless steels, solidifying with primary ferrite, have a sound centre at a reduction ratio of 3.6 when using S-EMS and F-EMS. The application of S-EMS increases the equiaxed crystallic zone instead of columnar structure and reduces cracks in the steel strand. The benefits available by using one or more EMS in combination are listed in Tab 1.
Tab 1 Benefits available with using one or more EMS |
| M-EMS | M-EMS + F-EMS | M-EMS + S-EMS + F-EMS | M-EMS + S-EMS | S-EMS | S-EMS + F-EMS |
Pinhole and blowhole | +++ | +++ | +++ | +++ | – | – |
Surface and subsurface cracks | +++ | +++ | +++ | +++ | – | – |
Breakout reduction | ++ | ++ | ++ | ++ | +* | +* |
Surface cracks (round) | ++ | ++ | ++ | ++ | – | – |
Solidification structure and internal cracks | ++ | ++ | +++ | ++ | +** | +** |
Centre line segregation, and centre porosity | ++ | +++ | +++ | ++ | ++ | +++ |
V segregation | + | +++ | +++ | ++ | +*** | ++ |
* S-EMS in high position |
** Better structure only in centre part of the product, after position of S-EMS, worse structure in external part compared to application of M-EMS. Risks of negative segregation when excessive stirring applied. |
*** with S-EMS in low position |
For more demanding qualities the use of EMS can be justified when the costs of the quality defects, conditioning or rejections, or the costs of casting larger sections are too large. Rotary stirring is used for carbon steel with carbon less than 0.2 %. In some cases, in-mould stirring is preferred than the secondary stirring since in the secondary stirring the negative segregation is found. In-fact negative segregation does not have any effect on the mechanical properties but one minor exception is that it can cause local variation in the hardenability which is not appreciated. Carbon content between 0.2 % and 0.5 %, two-stage stirring is used. It is better to complement the in-mould stirring with the secondary stirring or final stirring. For carbon content higher than 0.5 % and alloy steels with a large solidification range, three-stage stirring is used.
Any benefits from EMS for slabs can be negated from the poor geometry. So, care is to be taken for the machining. Method of reducing submerged nozzle convection currents with the EMBR for improving cleanness. This consists of two sets of coils placed along the outer walls of the mould faces. The magnetic field reduces the liquid steel velocity and impurities float to the surface where they are trapped by the mould powder. The roll gap geometry of bloom casters and more considerably slab casters can have a major influence on the internal quality of continuous cast semis and on various types of segregation and consequently the increased levels of some elements in these segregated areas. The main types of segregation caused by deviations from the true roll gaps are (i) inter columnar macro segregation, (ii) centre line macro segregation, and (iii) off centre line semi macro segregation (also termed V segregation or spot segregation).
In the temperature range 1,300 deg C up to the solidus the ductility of steel is very low. This is due to the liquid phases of FeS and MnS which have segregated to the boundaries between dendrites. FeS and MnS both have melting points much lower than steel and hence these weak boundaries open at quite low tensile strains.
One of the metallurgical problems found in continuously cast products is the development of large columnar dendritic zones. The effect of columnar growth on the mechanical properties such as loss of ductility in steel has been investigated by Weiser. Alberney, have shown that centre line defects in the continuous casting can be considerably reduced by controlling the columnar growth regions. The control of columnar growth is crucial in producing good quality strand cast products.
Essentially, induction stirring causes a sweeping flow along the solid-liquid interface which affects the final solidification structure since it influences the local growth conditions such as the temperature gradient, the boundary layer thickness, and the structure and size of the ‘mushy zone’. Since macro-segregation is known to result from inter-dendritic fluid flow, reduction in the length of the ‘mushy zone is to effectively reduce the extent of macro-segregation, particularly along the centre line. Several studies have shown that EMS is an effective means of improving continuously cast steel solidification structures by preventing columnar growth.
The size of columnar zones and associated inter-dendritic segregation and shrinkage porosity are greatly reduced by the use of in-strand or in-mould electromagnetic stirring. The latter technique effectively increases the size of the equi-axed solidification zone and greatly reduces the amount of centre line shrinkage (Fig 6). The relative size of columnar and equiaxed zones in a cast cross section are also affected by superheating of liquid steel. High superheating in unstirred billets increases the size of the columnar zone because the nucleation of equiaxed dendrites is retarded. EMS reduces the effects of high superheats but does not completely compensate for the increased size of columnar zones developed by high superheat temperatures.
Superheat was one of the most fundamental factors recognized from the early years of continuous casting especially for medium and high carbon steels. In an early report, pilot plant tests were performed casting 150 mm x 150 mm billets of high carbon steels. It was proven that at low superheats or even sub-liquidus temperatures of casting, the centre line segregation was minimized. The electromagnetic stirring at the mould (M-EMS) exhibited some benefits, and the application of EMS at the strand (S) and final (F) stages of solidification started being installed in some casters. It was found that the combination of EMS, that is, (S+F)-EMS for blooms and (M+S+F)-EMS for billets, is the most effective method for reducing macro-segregation among various EMS conditions, causing them to solidify more rapidly during the final stages of solidification, providing more finely distributed porosities and segregation spots along the central region. The optimum liquid pool thickness was found to decrease as the carbon content increased, which can be attributed to longer solidification times in the solid fraction (fs) range from fs=0.3 to 0.7. The effect of superheat on the solidification structure has been analyzed, verifying the empirical fact that increasing superheat the columnar dendritic growth increases against the equiaxed one. They concluded that convection effects influenced micro-segregation behaviour of the studied high carbon (C less than or equal to 0.7 %), and high manganese steels.
The effect of F-EMS parameters with current intensity increasing from 300 A (ampere) to 400 A and frequency increasing from 4 Hz (hertz) to 12 Hz, on the electromagnetic forces and carbon concentration distribution in the central cross section of 70 steel square billet has been studied. The optimal F-EMS parameter to make uniform the central cross-sectional carbon concentration and minimize the centre carbon segregation of 70 steel billets has been obtained with a current intensity of 280 A and frequency of 12 Hz. Under this stirring parameter, the carbon segregation indexes for all sampling points are in the range of 0.92–1.05, which is attributed to the fact that its stirring intensity is more suitable for decreasing the strand centre temperature and increasing the solidification rate of the billet. Hence, the rejected solute element has limited time to transport after electromagnetic stirring which promotes the reduction of centre segregation.
It is well known that porosities and shrinkage cavity occur in the central part of continuous cast blooms and billets. Although there are good results in carbon segregation levels at a stirring current and frequency of 280 A and 12 Hz, respectively, further investigations have shown that the F-EMS has a considerable impact on the other internal qualities of a square billet.
The effect of F-EMS parameters on centre segregation was studied in 140 mm × 140 mm billet continuous casting process. In the model, the initial growth of equiaxed grains which can move freely with liquid was treated as slurry, while the coherent equiaxed zone was regarded as porous media. The results show that the stirring velocity is not the main factor influencing centre segregation improvement, which is more affected by current intensity and stirring pool width. Because solute transport is controlled by solidification rate as stirring pool width, centre segregation declines continuously with current intensity increasing. As liquid pool width decreases and less latent heat needs to dissipate in the later solidification, the centre segregation can be improved more obviously by F-EMS. Due to centre liquid solute enrichment and liquid phase accumulation in the stirring zone, centre segregation turns to rise reversely with higher current intensity and becomes more serious with stirring pool width further decreasing, it forms positive segregation and solute can be concentrate with weak stirring, leading to centre segregation deterioration. With the optimized current intensity, centre segregation improvement is better with respect to F-EMS.
Some F-EMS stirring techniques are more effective than others in terms of structure morphological transformation from original dendritic to globulitic and in its refining. Macrostructure of casts without the use of stirring is different from the one with the use of stirring. The structure can be obtained with conventional stirring is largely globule-shaped with some presence of dendrites and dendrite fragments. The structure obtained with modulated stirring consists of entirely globule-shaped crystals and structure appears to be more refined.
Grain size can be varied by applying different stirring setting. With F-EMS conventional stirring, the grain diameter is reduced in both cast mid radius and in central area with comparison with the unstirred structure. A further grain diameter reduction has been achieved with counter-rotating modulated and unmodulated stirring. However, the smallest grain diameter in the casts has been obtained with unidirectional modulated stirring, in comparison with the grain diameter in the cast without stirring.
In general, the microstructure of samples using F-EMS consists of globules and elongated grains in the structure obtained with stirring, and fine inter-granular eutectic network containing different compounds. The coarse dendritic structure of the cast products cast without stirring can be transformed into mainly globular one with some rosette shaped as a result of the conventional stirring application. The structure obtained with unidirectional modulated stirring consists of a mixture of fine round-shape globules and large elongated grains. This structure also appears to be more refined in comparison with that obtained with the conventional stirring.
The globule mean area and length in the microstructure of the combined mid-radius and centre area of the cast obtained with conventional stirring is when compared with the structure of the other casts. The globule mean area in the structure can be reduced, but not in case of structure obtained without stirring. The structure obtained with unidirectional modulated stirring in the casts, the globule mean area in these casts is reduced in comparison with conventional stirring. A similar trend is determined in reduction of the globule length. Concurrent with globule size reduction, their density has increased. The effect of the M-EMS on the solidification structures has been obtained under fixed superheat, casting speed, secondary cooling intensity, and M-EMS frequency. The ratio of the central equiaxed grain zone was found to increase with decreasing superheat, increasing casting speed, decreasing secondary cooling intensity, and increasing M-EMS current. But the equiaxed zone is limited for M-EMS, since it has more responsibility towards columnar zone. The grain size obviously decreased with decreasing superheat and increasing M-EMS current but was less sensitive to the casting speed and secondary cooling intensity.
White band segregation – The increasing use of electromagnetic stirring (EMS) over recent years has brought with it increased interest in the problem known as white bands. The white band is a zone of negative segregation (appearing white on sulphur prints) frequently found in S-EMS stirred products and corresponding to the position of the solidification front during stirring. The visual appearance of segregation has not only given rise to the name but is probably also the white band’s most undesirable feature. The extent of negative segregation at the white band is less than the positive segregation at the centre line, but it is continued presence after hot working can result in a deterrent to customer acceptance, mostly on cosmetic grounds. Kor has suggested an explanation, in which the white band is the result of changes in growth rate at the start and end of strand stirring. White band is due to the solute washing mechanism which was firstly found by Bridge and Rogers. This proposes that the turbulent flows caused by EMS penetrate the dendrite mesh and sweep out enriched inter-dendritic liquid (Fig 7). However, in order to maintain this action it is necessary to assume that the removed solute is very rapidly dispersed throughout the remaining liquid. This being so, it is difficult then to explain the observed solute enrichment at the end of stirring.

Fig 7 Schematic of the solute washing mechanism for white band formation
Mathematical modelling
In tandem, mathematical modelling has played an important role in the implementation of EMS, as regards to providing a deeper understanding of the effects of stirring on, for example, the heat and fluid flow. A series of studies by Schwerdtfeger and co-workers have formed the cornerstone of the modelling in this area. Specifically, they have explored, both experimentally and theoretically, the effect of stirring in the round billet, rectangular bloom and slab geometries which are characteristic for the continuous casting of steel. These models consist of the Navier Stokes equations for the velocity field of the liquid metal and Maxwell’s equations for the induced magnetic flux density. In principle, these are two-way coupled, since the alternating magnetic field gives rise to a Lorentz force which drives the velocity field. This, in turn, can affect the magnetic field. Moreover, the frequency of the magnetic field is typically large enough to allow the use of the time-averaged value of the Lorentz force as input to the Navier Stokes equations.
Recent study by Vynnycky revisited the problem of a rotary EMS applied to round-billet continuous casting and found that the method used originally to determine the components of the Lorentz force led to a non-unique solution. This has been a consequence of the fact that the normal component of the induced magnetic flux density, rather than the tangential ones, has been prescribed as the boundary condition. Moreover, since the normal component has been prescribed in models for the case of longitudinal stirring for rectangular blooms also, it is natural to expect non-uniqueness in those models too. Furthermore, since the expressions for the components of the Lorentz force are still frequently used, it is clear that a resolution of the issue is still timely, especially in view of modern-day interest in modulated EMS. In this case, magnetic fields of different frequencies are applied and it is the intention that the resulting Lorentz force is to have a constant time-averaged part and a time varying one. It goes without saying that posing the correct boundary conditions for the magnetic field is important for achieving meaningful results from modelling.
Since the early industrial implementation of EMS, it has been recognized that demanding steel grades, especially those with a wide solidification range, benefit from stirring both within the casting mould and also at a later solidification stage. This type of stirring, in continuous casting of liquid steel, became known as final solidification zone stirring or F-EMS. Despite early reports on F-EMS effectiveness with respect to improving the cast strand internal quality, especially the structural soundness and segregation, in the long run it has been realized that the metallurgical performance of F-EMS lacked in both the effectiveness and consistency, which can be attributed to a number of defining factors. First, it is important to position the F-EMS with respect to the solidification stage which corresponds to a certain solid fraction level in the melt volume. Second, the stirring at this solidification stage is being performed under conditions of progressively diminishing stirring torque and increasing melt viscosity. The former occurs due to a reduction of the stirring pool radius, while the latter is due to an increase in the solid fraction of the melt.
There is also an additional important factor impacting on the stirring effectiveness, arising due to the nature of the magnetic field used for stirring. The stirring systems currently employed in the production of continuously cast steel products are based on application of a rotating magnetic field (RMF). Such fields have limitations in their application at a later, or advanced, solidification stage, arising from the fact that the resulting angular velocity is very nearly constant with respect to radial position. This flow pattern is characterized by intensive shear force and turbulence at the solid-liquid interface which is highly effective in terms of dendrite fragmentation and the subsequent development of an equi-axial solidification structure, but has very little impact on mixing in the melt volume, especially near its central region. In contrast, intensive turbulence and mixing throughout the melt volume is required at a late solidification stage in order to disrupt formation of the crystalline network and, associated with it, the development onset of structural defects such as porosity, fissures, and solutal segregation.
There have been numerous developments aimed at improvement of the RMF based stirring at a later solidification stage through enhancement of the secondary fluid flow in the radial-axial plane. Hence, intermittent and alternating stirring schemes, both of which use sequential forced and dormant periods, have been introduced in the 1980s. Kojima and co-workers, demonstrated experimentally, while Davidson and Boysan confirmed theoretically that strong recirculatory flow occurs in the radial-axial directions during the dormant periods (i.e. without active stirring) due to the initial axial gradient of the swirl flow.
However, these stirring methods have not resulted in a considerable improvement of F-EMS performance. The reasons for that can be found in the recent study by S Eckert and co-workers who have shown that the occurrence of strong recirculatory flows is contingent on a provision of a narrow range of stirring and casting parameters. Non-compliance with those provisions can negatively impact on stirring performance and even render it useless or harmful. There have been several recent attempts to intensify turbulence and mixing in the bulk of the solidifying melt by using modulated electric currents to energize the stirring coils. The objective is to produce a modulated electromagnetic field which consists of both a time-averaged and a time-varying component. These recent developments have been theoretical and laboratory-scale in nature and none has been implemented into production practice. Counter-rotating magnetic fields have also been tested for stirring a solidifying aluminum alloy in laboratory experiments conducted by Vives. Considerable improvements in solidification structure have been achieved by using this stirring method.
Advantages of EMS
Advantages of EMS in the final product depend on the application and some examples are (i) better hot workability, during extrusion forging of the bars the frequency of internal failures is lower, (ii) improved shearing ability by avoiding the structure which causes cracks, (iii) improved hardenability because of improved homogeneity, (iv) improved wire rod drawing performances with a low frequency of cup and cone breakages, and (v) higher and more consistent fatigue properties of bars.