Kontrol Proses Proses Teknologi
Kontrol Proses dari Proses Teknologi
Proses teknologi terdiri dari penanganan, pengerjaan, pemurnian, penggabungan, dan manipulasi bahan dan cairan untuk menghasilkan produk akhir yang menguntungkan. Proses ini bisa menjadi proses yang tepat, menuntut, dan berpotensi berbahaya. Perubahan kecil dalam suatu proses dapat berdampak besar pada hasil akhir. Variasi dalam proporsi, suhu, aliran, turbulensi, dan banyak parameter lainnya harus dikontrol secara hati-hati dan konsisten untuk secara konsisten menghasilkan produk akhir dengan kualitas yang diinginkan dengan bahan baku dan energi yang minimum.
Umumnya, apa pun yang membutuhkan pemantauan terus menerus dari suatu operasi, melibatkan peran kontrol proses. Kontrol proses mengacu pada metode yang digunakan untuk mengontrol variabel proses dari proses teknologi. Ini adalah alat yang memungkinkan proses menjalankan operasi proses dalam batas yang ditentukan dan untuk menetapkan batas yang lebih tepat guna memaksimalkan efisiensi proses, memastikan kualitas, dan keamanan.
Setiap proses teknologi membutuhkan sejumlah besar perencanaan agar berhasil menyelesaikan tugas yang ditetapkan. Namun, untuk menyelesaikan tugas-tugas ini, operator proses harus sepenuhnya memahami proses dan fungsi sistem kontrol. Sistem kontrol terdiri dari peralatan (alat ukur, dan alat kontrol dll) serta intervensi operator. Sistem kontrol digunakan untuk memenuhi tiga kebutuhan dasar proses, yaitu (i) mengurangi pengaruh gangguan eksternal, (ii) meningkatkan stabilitas proses, dan (ii) meningkatkan kinerja proses.
Instrumentasi menyediakan berbagai indikasi yang digunakan untuk mengoperasikan proses teknologi. Dalam beberapa kasus, operator mencatat indikasi ini untuk digunakan dalam operasi proses. Informasi yang direkam membantu operator mengevaluasi kondisi proses saat ini dan mengambil tindakan jika kondisinya tidak seperti yang diharapkan. Mengharuskan operator untuk mengambil semua tindakan korektif yang diperlukan tidak praktis, atau kadang-kadang tidak mungkin, terutama jika sejumlah besar indikasi harus dipantau. Untuk alasan ini, sebagian besar proses teknologi dikendalikan secara otomatis setelah beroperasi dalam kondisi normal. Kontrol otomatis sangat mengurangi beban operator dan membuat pekerjaan mudah diatur. Proses teknologi dikendalikan karena tiga alasan yaitu (i) mengurangi variabilitas, (ii) meningkatkan efisiensi, dan (iii) memastikan keamanan.
Kontrol proses dapat mengurangi variabilitas dalam produk akhir, yang memastikan produk berkualitas tinggi secara konsisten. Dengan pengurangan variabilitas proses, proses menjadi lebih stabil, andal, produktif, dan ekonomis. Beberapa parameter proses harus dipertahankan pada tingkat tertentu untuk memaksimalkan efisiensi proses. Kontrol yang akurat dari parameter ini memastikan efisiensi proses. Selanjutnya, proses run-away, seperti reaksi kimia di luar kendali, dapat terjadi jika selama operasi proses, kontrol yang tepat dari semua variabel proses tidak dipertahankan. Konsekuensi dari proses pelarian bisa menjadi bencana besar. Oleh karena itu, kontrol proses yang tepat juga diperlukan untuk memastikan keamanan peralatan dan pekerja.
Peran kontrol proses telah berubah selama bertahun-tahun dan terus dibentuk oleh teknologi. Peran tradisional dari kontrol proses adalah untuk berkontribusi pada keselamatan, meminimalkan dampak lingkungan, dan mengoptimalkan proses dengan mempertahankan variabel proses mendekati nilai yang diinginkan. Di masa lalu, pemantauan parameter proses dilakukan di tempat proses dan parameter dipertahankan secara lokal oleh operator. Ketika proses menjadi lebih besar dalam skala dan/atau lebih kompleks, peran otomatisasi proses menjadi semakin penting. Saat ini otomatisasi telah mengambil alih fungsi kontrol proses, yang berarti bahwa operator dibantu oleh sistem kontrol terdistribusi terkomputerisasi (DCS) yang berkomunikasi dengan instrumen di lapangan.
Kontrol proses adalah campuran antara statistik dan disiplin teknik yang berhubungan dengan mekanisme, arsitektur, dan algoritma untuk mengendalikan suatu proses. Untuk memiliki kontrol proses yang efektif, selain pemahaman tentang teknologi proses, juga perlu memahami konsep-konsep kunci dan terminologi umum dari kontrol proses.
Alasan untuk mengontrol suatu proses adalah untuk membuatnya berperilaku dengan cara yang diinginkan. Ini dapat melibatkan proses menjadi lebih akurat, lebih dapat diandalkan, atau lebih ekonomis. Dalam beberapa kasus, proses yang tidak terkontrol tidak stabil dan diperlukan kontrol yang baik agar tidak merusaknya. Oleh karena itu, kontrol yang baik dapat memiliki arti yang berbeda dalam aplikasi yang berbeda.
Dalam kontrol proses, tujuan dasarnya adalah mengatur nilai beberapa parameter. Mengatur berarti mempertahankan kuantitas parameter pada beberapa nilai yang diinginkan terlepas dari pengaruh eksternal. Nilai yang diinginkan disebut nilai referensi atau set-point. Operator dapat mengubah set-point. Prosesnya mengatur diri sendiri jika dengan mengubah titik setel input, output berubah sesuai dengan titik setel input. .Sistem yang mengatur sendiri tidak memberikan pengaturan variabel ke nilai referensi tertentu. Parameter mengadopsi beberapa nilai yang nilai input dan outputnya sama, dan tetap di sana. Tetapi jika laju aliran input berubah, maka outputnya juga berubah, sehingga tidak diatur ke nilai referensi.
Kontrol yang dibantu operator memungkinkan pengaturan buatan oleh operator. Untuk mengatur parameter agar dapat mempertahankan nilai yang dibutuhkan maka diperlukan suatu sensor untuk mengukur parameter tersebut. Parameternya disebut variabel terkontrol. Dengan mengoperasikan peralatan kontrol yang sesuai, parameter output dapat diubah ke set-point oleh operator. Parameter keluaran disebut variabel yang dimanipulasi atau variabel pengontrol.
Sistem kontrol otomatis menggantikan sistem kontrol dan menggunakan mesin, elektronik, atau komputer yang menggantikan operasi oleh operator. Sebuah instrumen yang disebut sensor ditambahkan yang mampu mengukur nilai parameter dan mengubahnya menjadi sinyal proporsional. Sinyal ini diberikan sebagai input ke mesin, sirkuit elektronik, atau komputer yang disebut pengontrol. Kontroler menjalankan fungsi operator dalam mengevaluasi pengukuran dan memberikan sinyal keluaran, untuk mengubah pengaturan peralatan kontrol melalui aktuator yang terhubung ke peralatan melalui hubungan mekanis. Ketika kontrol otomatis diterapkan pada sistem yang dirancang untuk mengatur nilai beberapa variabel ke titik setel, ini disebut kontrol proses otomatis. Gambar 1 menunjukkan proses kontrol konseptual yang menunjukkan variabel input output dalam diagram blok.
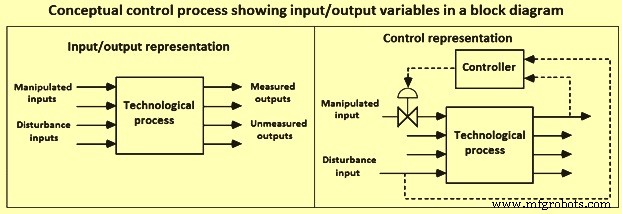
Gbr 1 Proses kontrol konseptual menampilkan variabel input output dalam diagram blok
Proses teknologi bersifat dinamis karena jarang beroperasi pada kondisi mapan. Operasi proses teknologi terdiri dari memastikan bahwa respon yang tepat dibuat untuk gangguan yang selalu terjadi sehingga operasi aman, efisien, dan menghasilkan produk yang diinginkan dengan kualitas tertentu pada tingkat yang diperlukan. Karena metode produksi bervariasi dari proses ke proses, prinsip-prinsip kontrol otomatis bersifat umum dan dapat diterapkan secara universal, terlepas dari ukuran dan jenis prosesnya. Tujuan dari sistem kontrol proses adalah untuk melakukan salah satu atau kedua tugas berikut.
Pertahankan proses pada kondisi operasional dan set-point – Banyak proses yang diperlukan untuk bekerja pada kondisi tunak atau dalam keadaan memenuhi semua persyaratan seperti biaya, hasil, keselamatan, dan sasaran mutu lainnya. Dalam banyak situasi kehidupan nyata, suatu proses tidak selalu tetap statis dan ada gangguan yang terjadi pada proses yang membuat proses tidak stabil. Dalam proses yang tidak stabil, variabel proses berosilasi dari batas fisiknya selama rentang waktu yang terbatas. Variabel proses yang tidak terkontrol dapat dikontrol hanya dengan menambahkan instrumen dan peralatan kontrol yang dapat mengontrol variabel proses dalam batas kontrolnya baik secara otomatis atau melalui intervensi operator.
Transisi proses dari satu kondisi operasional ke kondisi operasional lainnya – Dalam situasi kehidupan nyata, terkadang perlu untuk mengubah kondisi operasional proses untuk berbagai alasan yang berbeda. Alasan peralihan proses dari satu rangkaian kondisi operasional ke rangkaian kondisi operasional lainnya dapat disebabkan oleh ekonomi, spesifikasi produk, kendala operasional, peraturan lingkungan, dan spesifikasi produk yang berubah, dll.
Pengembangan strategi kontrol untuk proses teknologi terdiri dari merumuskan atau mengidentifikasi (i) tujuan kontrol, (ii) variabel input yang merupakan variabel yang dimanipulasi atau variabel gangguan dan yang dapat berubah terus menerus, atau pada interval waktu yang terpisah, (iii) variabel keluaran yang dapat berupa variabel terukur atau variabel tidak terukur dan yang dapat diukur baik secara terus menerus atau pada interval waktu tertentu, (iv ) kendala yang dapat berupa keras atau lunak, (v) karakteristik operasi yang dapat batch, kontinu, atau semi-kontinyu, (vi) pertimbangan keamanan, lingkungan, dan ekonomi, dan (vii) struktur kontrol di mana pengontrol dapat memberi umpan balik atau umpan maju di alam. Perumusan sistem kontrol proses untuk proses teknologi terdiri dari tujuh tahap.
Tahap pertama mengembangkan sistem kontrol adalah merumuskan tujuan kontrol. Proses teknologi biasanya terdiri dari beberapa sub-proses. Kontrol proses teknologi berkurang ketika kontrol setiap sub-proses dipertimbangkan secara terpisah. Meskipun demikian, setiap sub-proses dapat memiliki beberapa tujuan yang terkadang saling bertentangan, sehingga pengembangan tujuan pengendalian biasanya merupakan masalah yang sulit.
Tahap kedua merupakan penentuan variabel input. Variabel input menunjukkan pengaruh lingkungan pada proses. Biasanya mengacu pada faktor-faktor yang mempengaruhi proses. Variabel input dapat diklasifikasikan sebagai variabel yang dimanipulasi atau gangguan. Input yang dimanipulasi adalah input yang dapat diatur oleh sistem kontrol (atau operator proses). Masukan gangguan adalah variabel yang mempengaruhi keluaran proses tetapi tidak dapat diatur oleh sistem kendali. Ada input gangguan yang terukur dan tidak terukur. Input dapat berubah terus menerus atau pada interval waktu yang berbeda.
Tahap ketiga merupakan penentuan variabel keluaran. Variabel keluaran juga dikenal sebagai variabel kontrol. Ini adalah variabel yang merupakan output proses yang mempengaruhi lingkungan. Variabel output dapat diklasifikasikan sebagai variabel terukur atau tidak terukur. Pengukuran dapat dilakukan secara terus menerus atau pada interval waktu yang berbeda.
Tahap keempat merupakan penentuan kendala operasi. Setiap proses memiliki batasan operasi tertentu, yang diklasifikasikan sebagai keras atau lunak. Contoh hard constraint adalah laju aliran minimum atau maksimum di mana katup akan beroperasi antara kondisi ekstrem tertutup penuh atau terbuka penuh. Contoh batasan lunak adalah komposisi produk dan diinginkan untuk menentukan komposisi antara batas-batas tertentu, tetapi dimungkinkan untuk melanggar spesifikasi ini tanpa menimbulkan bahaya keselamatan atau lingkungan.
Tahap kelima merupakan penentuan karakteristik operasi. Karakteristik operasi biasanya diklasifikasikan sebagai batch, kontinyu, atau semi-kontinyu. Proses berkelanjutan beroperasi untuk jangka waktu yang lama di bawah kondisi operasi yang relatif konstan sebelum 'dimatikan' untuk melakukan pekerjaan tertentu seperti pembersihan, dan pemeliharaan preventif berkala, dll. Proses batch bersifat dinamis, yaitu, biasanya beroperasi untuk waktu yang singkat periode waktu dan kondisi pengoperasian dapat sedikit berbeda selama periode waktu tersebut. Contoh proses batch adalah pembuatan panas dalam tungku pembuatan baja. Untuk reaktor batch, pengisian awal dilakukan ke reaktor, dan kondisi proses divariasikan untuk menghasilkan produk yang diinginkan pada akhir proses batch. Proses semi-kontinyu tipikal dapat memiliki muatan awal ke reaktor, tetapi komponen umpan dapat ditambahkan ke reaktor selama proses batch. Proses pengecoran kontinyu adalah contoh dari proses semi-kontinyu. Pertimbangan penting adalah skala waktu yang dominan dari proses. Untuk proses kontinyu, hal ini sangat sering berhubungan dengan waktu tinggal material dalam reaktor.
Tahap keenam merupakan pertimbangan penting mengenai masalah keselamatan, lingkungan, dan ekonomi. Dalam arti tertentu, ekonomi adalah kekuatan pendorong utama karena proses yang tidak aman atau berbahaya bagi lingkungan pada akhirnya membutuhkan biaya lebih untuk beroperasi karena sanksi peraturan dan ketidakefisienan. Selanjutnya, penting untuk meminimalkan biaya energi sambil memproduksi produk yang memenuhi spesifikasi. Otomatisasi dan kontrol proses yang lebih baik memungkinkan proses beroperasi lebih dekat ke kondisi 'optimal' dan menghasilkan produk yang memenuhi spesifikasi variabilitas.
Konsep 'fail-safe' selalu penting dalam pemilihan instrumentasi. Sebagai contoh, katup kontrol membutuhkan sumber energi untuk menggerakkan batang katup dan mengubah aliran. Paling sering itu adalah sinyal pneumatik (Biasanya 3 -15 PSI). Jika sinyal hilang, maka batang katup masuk ke batas 3 PSI. Jika katup 'udara-untuk-membuka', maka hilangnya udara instrumen menyebabkan katup menutup dan ini dikenal sebagai katup 'gagal-tertutup'. Jika, di sisi lain, katup adalah udara untuk menutup, ketika udara instrumen hilang katup pergi ke keadaan terbuka penuh dan ini dikenal sebagai katup 'gagal-terbuka'.
Ada dua jenis kontrol standar yaitu (i) kontrol feed-forward, dan (ii) kontrol feed-back. Pengontrol umpan-maju mengukur variabel gangguan dan mengirimkan nilai ini ke pengontrol, yang menyesuaikan variabel yang dimanipulasi. Tujuan dari kontrol umpan balik adalah untuk menjaga agar variabel yang dikontrol tetap dekat dengan titik setelnya. Sistem kontrol umpan balik mengukur variabel keluaran, membandingkan nilainya dengan nilai keluaran yang diinginkan, dan menggunakan informasi ini untuk menyesuaikan variabel yang dimanipulasi. Dengan desainnya, pengontrol umpan balik mengambil tindakan korektif untuk mengurangi penyimpangan. Pengontrol umpan balik hanya dapat mengambil tindakan setelah variabel yang dikontrol menyimpang dari titik setel yang diinginkan dan menghasilkan kesalahan yang tidak nol. Namun, respon terhadap gangguan bisa sangat lamban, jika proses atau pengukuran berubah sangat lambat. Dalam situasi seperti itu, pengontrol umpan maju dapat meningkatkan kinerja. Kontroler feed-forward memprediksi efek gangguan terhadap variabel terkontrol dan mengambil tindakan kontrol yang melawan pengaruh gangguan.
Menentukan struktur kontrol umpan balik untuk suatu proses terdiri dari memutuskan variabel mana yang dimanipulasi yang akan disesuaikan untuk mengontrol variabel yang diukur. Nilai yang diinginkan dari output proses yang diukur disebut set-point. Ada dua alasan mengapa variabel terkontrol menyimpang dari set-pointnya. Set-point diubah dengan sengaja untuk mencapai kinerja yang lebih baik atau gangguan membuat operasi menjauh dari set-point yang diinginkan. Kontroler yang dirancang untuk menolak gangguan disebut regulator sedangkan pengontrol yang dirancang untuk melacak perubahan set-point disebut mekanisme servo. Biasanya untuk proses yang berkesinambungan, perubahan set-point jarang terjadi, biasanya hanya jika pengontrol pengawas menghitung titik operasi yang lebih menguntungkan, dan karenanya, regulator adalah bentuk pengontrol umpan balik yang paling umum digunakan. Sebaliknya, pengontrol untuk masalah servo adalah umum dalam proses batch, di mana sering terjadi perubahan set-point.
Konsep yang sangat penting yang digunakan dalam desain sistem kontrol adalah 'penguatan proses'. 'Proses gain' adalah sensitivitas output proses terhadap perubahan input proses. Jika peningkatan input proses menyebabkan peningkatan output proses, ini dikenal sebagai keuntungan positif. Jika, di sisi lain, peningkatan input proses menyebabkan penurunan output proses, ini dikenal sebagai keuntungan negatif. Besarnya 'perolehan proses' juga penting.
Setelah struktur kontrol ditentukan, penting untuk memutuskan algoritma kontrol. Algoritme kontrol menggunakan nilai variabel keluaran terukur (bersama dengan nilai keluaran yang diinginkan) untuk mengubah variabel masukan yang dimanipulasi. Sebuah algoritma kontrol memiliki sejumlah parameter kontrol, yang harus disesuaikan untuk memiliki kinerja yang dapat diterima. Seringkali penyesuaian dilakukan pada model simulasi sebelum menerapkan strategi kontrol pada proses yang sebenarnya. Dalam kasus kontrol berbasis model, pengontrol memiliki model proses yang 'terpasang'.
Diagram blok dari proses teknologi dengan variabel tunggal yang dimanipulasi dan satu variabel terkontrol (Gambar 2) termasuk umpan-maju, umpan-balik, dan kontrol pengawasan. Tujuan utama dari pengontrol umpan balik adalah untuk menjaga variabel terkontrol X yang diukur oleh beberapa instrumen sedekat mungkin dengan titik setel Xsp yang diinginkan. Variabel yang dikendalikan dapat berupa parameter apa pun dari proses teknologi. Set-point biasanya ditentukan oleh sistem kontrol pengawasan menggunakan teknik optimasi numerik real-time. Ada beberapa jenis elemen kontrol akhir yang berbeda. Variabel gangguan D, juga disebut variabel beban, dapat menyebabkan variabel terkontrol menyimpang dari set-pointnya, memerlukan tindakan kontrol untuk mengembalikannya ke titik operasi yang diinginkan. Baik kontrol feed-back maupun feed-forward dapat mengurangi efek gangguan, dimana masing-masing metode memiliki kelebihan dan kekurangannya masing-masing. Gangguan dapat dihasilkan dari berbagai sumber, termasuk variabel lingkungan eksternal. Bagaimanapun, variabel gangguan tidak dapat dipengaruhi oleh pengontrol proses. Kesalahan atau deviasi E antara variabel yang dikendalikan X dan titik setelnya Xsp adalah input ke pengontrol umpan balik, yang mengubah variabel yang dimanipulasi M untuk mengurangi kesalahan. Dalam proses teknologi yang khas, mungkin ada sejumlah besar loop kontrol seperti itu.
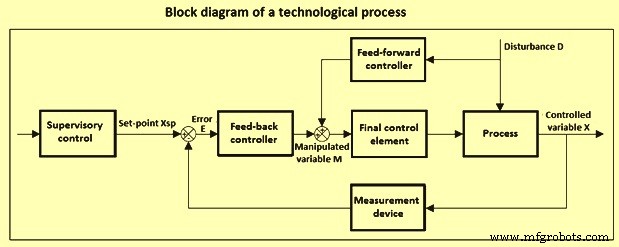
Gbr 2 Blok diagram untuk mengontrol proses teknologi
Mengontrol perangkat keras dan perangkat lunak
Kontrol proses seperti yang dipraktikkan dalam industri proses telah mengalami perubahan signifikan sejak pertama kali diperkenalkan pada tahun 1940-an. Pada awal 1960-an, perangkat keras kontrol analog elektrik menggantikan sebagian besar perangkat keras kontrol analog pneumatik. Namun, dalam banyak proses, elemen kontrol tertentu, yaitu aktuator katup kontrol, tetap pneumatik bahkan hingga hari ini. Kontroler analog elektrik tahun 1960-an adalah pengontrol loop tunggal di mana setiap input pertama kali dibawa dari titik pengukuran dalam proses ke ruang kontrol tempat sebagian besar pengontrol berada. Output dari kontroler kemudian dikirim dari ruang kontrol ke elemen kontrol akhir. Antarmuka operator terdiri dari panel kontrol yang memiliki kombinasi pelat muka tampilan dan perekam grafik untuk pengontrol dan indikator loop tunggal. Strategi kontrol terutama melibatkan kontrol umpan balik, biasanya dengan pengontrol proporsional-integral (PI). Selama akhir 1950-an dan awal 1960-an, komputer kontrol proses untuk melakukan kontrol digital langsung (DDC) dan kontrol proses pengawasan diperkenalkan. Dalam hal penggunaan DDC, loop DDC sering kali memiliki hampir 100% cadangan kontrol analog yang membuat sistem menjadi mahal.
Sistem awal lainnya terutama menggunakan komputer kontrol proses untuk kontrol proses pengawasan. Kontrol pengaturan disediakan oleh pengontrol analog, yang tidak memerlukan cadangan, tetapi perhatian operator terbagi antara panel kontrol dan layar komputer. Tampilan terminal menyediakan antarmuka operator ketika kontrol pengawasan sedang digunakan, tetapi panel kontrol masih ditempatkan di ruang kontrol untuk saat-saat cadangan analog diperlukan. Dalam lingkungan ini, ada perluasan penggunaan teknik kontrol canggih seperti kontrol feed-forward, kontrol decoupling multi-variabel, dan kontrol kaskade. Fungsionalitas sistem kontrol awal ini dirancang di sekitar kemampuan komputer daripada karakteristik proses. Keterbatasan ini, ditambah dengan pelatihan operator yang tidak memadai dan antarmuka pengguna yang tidak ramah, menyebabkan desain yang sulit untuk dioperasikan, dipelihara, dan diperluas. Selain itu, banyak sistem yang berbeda memiliki spesifikasi khusus, membuatnya sangat mahal. Infus aplikasi sistem digital ke dalam industri proses terjadi sekitar tahun 1970, ketika mikroprosesor murah tersedia secara komersial.
Sistem kontrol terdistribusi (DCS) – Sebuah DCS terdiri dari banyak elemen seperti yang ditunjukkan pada Gambar 3. Komputer host melakukan tugas komputasi intensif seperti optimasi dan strategi kontrol lanjutan. Jalan raya data, yang terdiri dari tautan transmisi digital, menghubungkan semua komponen dalam sistem. Jalan raya data yang redundan mengurangi kemungkinan hilangnya data. Stasiun kontrol operator menyediakan konsol video untuk komunikasi operator dengan sistem, untuk mengawasi dan mengontrol proses. Banyak stasiun kontrol berisi printer untuk pencatatan alarm, pencetakan laporan, atau penyalinan grafis proses. Unit kendali jarak jauh menerapkan fungsi kendali dasar seperti algoritme PID dan terkadang menyediakan kemampuan akuisisi data. Konsol programmer mengembangkan program aplikasi untuk sistem kontrol terdistribusi. Perangkat penyimpanan massal menyimpan data proses untuk tujuan kontrol serta keputusan perusahaan. Perangkat penyimpanan dapat berupa hard disk atau database. Komunikasi dan interaksi antara pengontrol, input, dan output diwujudkan oleh perangkat lunak, bukan dengan pemasangan kabel. Oleh karena itu, DCS merevolusi banyak aspek kontrol proses, mulai dari tampilan ruang kontrol hingga meluasnya penggunaan strategi kontrol tingkat lanjut.
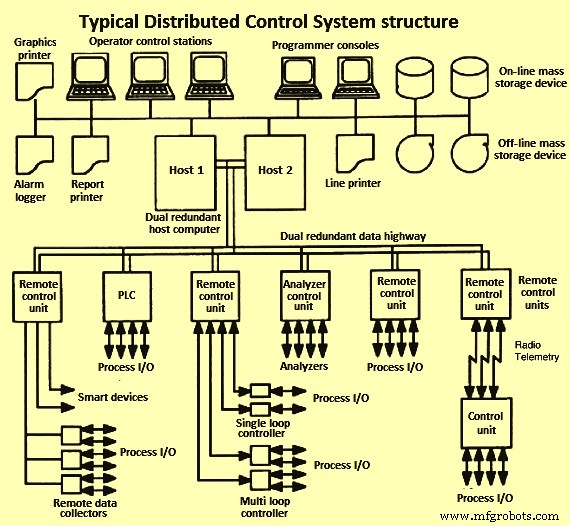
Gbr 3 Struktur tipikal sistem DCS
Pengontrol Logika yang Dapat Diprogram (PLC) – Awalnya, pengontrol PLC didedikasikan, berdiri sendiri, perangkat berbasis mikroprosesor yang mengeksekusi logika biner langsung untuk pengurutan dan interlock. PLC secara signifikan meningkatkan kemudahan modifikasi dan perubahan yang dapat diimplementasikan pada logika tersebut. PLC menjadi semakin kuat dalam hal kemampuan kalkulasi. Kontrol proses batch didominasi oleh kontrol tipe logika, dan PLC adalah alternatif yang lebih disukai daripada DCS. Karena ketersediaan antarmuka terintegrasi yang relatif mulus antara DCS dan PLC, praktik saat ini umumnya menggunakan kombinasi terintegrasi DCS dan PLC. Sebagian besar PLC juga menangani logika sekuensial dan dilengkapi dengan kemampuan pengaturan waktu internal untuk menunda tindakan dengan jumlah waktu yang ditentukan, untuk menjalankan tindakan selama waktu yang ditentukan, dan seterusnya.
Sistem keamanan dan penonaktifan – Kontrol proses memainkan peran penting dalam pertimbangan keamanan proses. Ketika prosedur otomatis menggantikan prosedur manual untuk operasi rutin, kemungkinan kesalahan manusia yang mengarah ke situasi berbahaya menjadi lebih kecil. Selain itu, kesadaran operator akan kondisi pembangkit saat ini juga ditingkatkan. Sistem proteksi harus disediakan untuk proses berbahaya. Salah satu caranya adalah dengan memberikan logika untuk tujuan khusus membawa proses ke keadaan di mana kondisi ini tidak dapat ada, yang disebut sistem interlock pengaman. Karena sistem kontrol proses dan sistem kunci pengaman melayani tujuan yang berbeda, mereka harus dipisahkan secara fisik. Ini mengurangi risiko secara tidak sengaja mengubah sistem keselamatan. Sistem kehandalan tinggi khusus telah dikembangkan untuk shutdown keselamatan, misalnya, sistem redundan triple modular. Ini memungkinkan sistem mengalami kegagalan internal dan masih menjalankan fungsi dasarnya. Pada dasarnya sistem redundan triple modular terdiri dari tiga subsistem identik yang secara aktif melakukan fungsi yang identik secara bersamaan.
Alarm – Tujuan alarm adalah untuk mengingatkan operator proses terhadap kondisi proses yang memerlukan perhatian segera. Alarm diaktifkan setiap kali kondisi abnormal terdeteksi dan peringatan dikeluarkan. Alarm kembali normal ketika kondisi abnormal tidak ada lagi. Alarm dapat didefinisikan pada variabel terukur, variabel terhitung, dan keluaran pengontrol. Berbagai kelas alarm yang berbeda ada.
Pemancar pintar, katup, dan bus lapangan – Ada tren yang jelas dalam teknologi kontrol proses menuju peningkatan penggunaan teknologi digital. Komunikasi digital terjadi melalui bus lapangan, yaitu, kabel koaksial atau serat optik, di mana perangkat cerdas secara langsung terhubung dan ditransmisikan ke dan dari ruang kontrol atau ruang peralatan jarak jauh sebagai sinyal digital. Pendekatan field-bus mengurangi kebutuhan akan pasangan bengkok dan kabel terkait (Gbr 4).
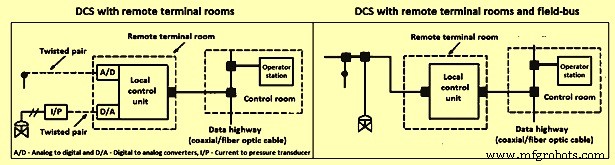
Gambar 4 DCS dengan terminal ruang jarak jauh dan bus lapangan
Berbagai protokol jaringan lapangan menyediakan kemampuan mentransfer informasi digital dan instruksi antara perangkat lapangan, instrumen, dan sistem kontrol. Perangkat lunak field-bus memediasi aliran informasi di antara komponen-komponen. Beberapa perangkat digital dapat dihubungkan dan berkomunikasi satu sama lain melalui jalur komunikasi digital, yang sangat mengurangi kabel.
Perangkat lunak kontrol proses – Pendekatan ramah pengguna yang paling banyak diadopsi adalah bahasa kontrol proses (PCL) isi formulir atau berbasis tabel. PCL populer termasuk diagram blok fungsi, logika tangga, dan logika yang dapat diprogram. Inti dari bahasa-bahasa ini adalah sejumlah blok fungsi dasar atau modul perangkat lunak, seperti analog in, digital in, analog out, digital out, dan PID dll. Secara umum, setiap modul berisi satu atau lebih input dan output. Pemrograman ini melibatkan perpindahan output dari blok ke input dari blok lain melalui antarmuka pengguna grafis. Pengguna diharuskan mengisi template untuk menunjukkan sumber nilai input, tujuan nilai output, dan parameter untuk formulir/tabel yang disiapkan untuk modul. Sumber dan tujuan yang kosong dapat menentukan saluran I/O (input/output) proses dan nama tag jika sesuai. Untuk menghubungkan modul, beberapa sistem memerlukan pengisian nama tag modul yang berasal atau menerima data. Bidang yang ditentukan pengguna mencakup fungsi khusus, pemilih (minimum atau maksimum), pembanding (kurang dari atau sama dengan), dan pengatur waktu (penundaan aktivasi). Sebagian besar DCS memungkinkan blok fungsi dibuat.
Hierarki kontrol fasilitas – Lima tingkat dalam proses teknologi di mana berbagai aktivitas optimasi, kontrol, pemantauan, dan akuisisi data digunakan ditunjukkan pada Gambar 5. Posisi relatif setiap blok pada gambar dimaksudkan untuk menjadi konseptual, karena dapat terjadi tumpang tindih dalam fungsi yang dijalankan. Skala waktu relatif di mana setiap level aktif juga ditampilkan. Masing-masing dari lima tingkat kontrol konseptual memiliki persyaratan dan kebutuhannya sendiri dalam hal perangkat keras, perangkat lunak, teknik, dan penyesuaian. Karena informasi mengalir ke atas dalam hierarki dan keputusan pengendalian mengalir ke bawah, pengendalian yang efektif pada tingkat tertentu hanya terjadi jika semua tingkat di bawah tingkat perhatian bekerja dengan baik. Tingkat tertinggi (perencanaan dan penjadwalan) menetapkan tujuan produksi untuk memenuhi kendala pasokan dan logistik dan menangani kapasitas yang berubah-ubah waktu dan keputusan pemanfaatan tenaga kerja. Ini disebut perencanaan sumber daya perusahaan (ERP).
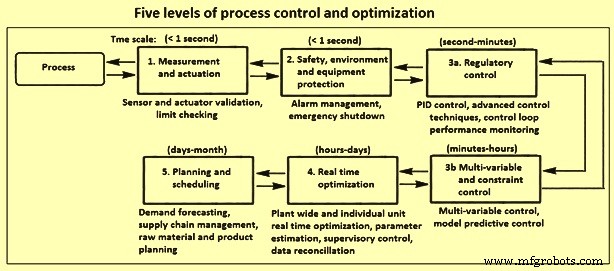
Gbr 5 Lima tingkat kontrol dan pengoptimalan proses
Umumnya, berbagai tingkat aplikasi kontrol ditujukan untuk satu atau lebih tujuan berikut yaitu (i) menentukan dan memelihara proses pada titik operasi optimal yang praktis, (ii) menjaga operasi yang aman untuk perlindungan personel dan peralatan, (iii) ) meminimalkan kebutuhan akan perhatian dan intervensi operator, dan (iv) meminimalkan jumlah, tingkat, dan penyebaran gangguan dan gangguan.
Instrumentasi – Ini terdiri dari komponen kotoran kontrol. Instrumentasi, yang menyediakan antarmuka langsung antara proses dan hierarki kontrol, berfungsi sebagai sumber informasi mendasar tentang status proses dan sarana utama di mana tindakan korektif ditransmisikan ke proses. Fungsi perangkat pengukuran proses adalah untuk merasakan nilai, atau perubahan nilai, dari variabel proses. Perangkat penginderaan yang sebenarnya dapat menghasilkan gerakan fisik, sinyal tekanan, dan sinyal mili-volt, dll. Transduser mengubah sinyal pengukuran dari satu kuantitas fisik atau kimia ke kuantitas lainnya, misalnya, tekanan ke mili-amp. Sinyal yang ditransduksi kemudian ditransmisikan ke ruang kontrol melalui saluran transmisi. Pemancar karenanya merupakan generator sinyal dan penggerak saluran. Peralatan kontrol modern memerlukan sinyal digital untuk tampilan dan algoritme kontrol, sehingga konverter analog-ke-digital (ADC) mengubah sinyal analog pemancar ke format digital.
Variabel proses yang paling sering diukur adalah suhu, aliran, tekanan, level, dan komposisi. Jika sesuai, sifat fisik lainnya juga diukur. Pemilihan instrumentasi yang tepat untuk aplikasi tertentu tergantung pada faktor-faktor seperti jenis dan sifat cairan atau padatan yang terlibat, kondisi proses yang relevan, keterjangkauan, akurasi, dan pengulangan yang diperlukan, waktu respons, biaya pemasangan, dan kemampuan pemeliharaan dan keandalan.
Transmisi dan pengkondisian sinyal – Berbagai macam fenomena digunakan untuk mengukur variabel proses yang diperlukan untuk mengkarakterisasi keadaan suatu proses. Because most processes are operated from a control room, these values are to be available there. Hence, the measurements are usually transduced to an electronic form, most often 4-20 mA, and then transmitted to a remote terminal unit and then to the control room. It is especially important that proper care is taken so that these measurement signals are not corrupted owing to ground currents, interference from other electrical equipment and distribution, and other sources of noise.
Final control elements – Good control at any hierarchial level needs good performance by the final control elements in the next lower level. At the higher control levels, the final control element can be a control application at the next lower control level. However, the control command ultimately affects the process through the final control elements at the regulatory control level, e.g., control valves, pumps, dampers, louvers, and feeders etc.
Process dynamics and mathematical models – A thorough understanding of the time-dependent behaviour of the technological processes is required in order to instrument and control the process. This in turn requires an appreciation of how mathematical tools can be employed in analysis and design of process control systems. There are several mathematical principles which are utilized for the automatic control. These are (i) physical models and empirical models, (ii) simulation of dynamic models, (iii) Laplace transforms, transfer functions, and block diagrams, and (iv) fitting dynamic models to experimental data etc.
Feed -back control systems – Measurements of the controlled variable are available in many process control problems. Specifically, this is the case when temperatures, pressure, or flows are to be controlled. In these situations the controlled variable can be directly measured and the manipulated variable is adjusted via a final control element. A feedback controller takes action when the controlled variable deviates from its set-point, as detected by the non-zero value of the error signal. The various types of feed-back controls are (i) on/off control, (ii) proportional control, (iii) proportional plus integral (PI) control, (iv) proportional plus integral plus derivative (PID) control, and (v) digital PID.
The simplest controller can only show two settings and is called an on/off controller. The output of this controller is either at its maximum or its minimum value, depending on the sign of the error. While this type of controller is simple, it is seldom used. The proportional controller offers more flexibility than the on/off controller because the manipulated variable is related not just to the sign of the error but also to its magnitude. The input-output behaviour of an actual proportional controller has upper and lower bounds i.e. the output saturates when the control limits are reached. Standard limits on the controller output are 3-15 PSI for pneumatic controllers, 4-20mA for electric controllers, and 0-10 VDC for digital controllers.
Integrating action needs to be included in the control loop, if an offset-free response in the presence of constant load disturbances or for set point changes is needed. If the process does not show integrating behaviour itself then it is possible to implement a proportional plus-integral controller to achieve the desired performance. There are both and disadvantages associated with integral action in a controller. One disadvantage of a PI controller is that the integral action can cause it to react more sluggishly than a proportional controller. If it is important to achieve a faster response which is to be offset-free then this can be accomplished by including both derivative and integral action in the controller. In order to anticipate the future behaviour of the error signal, a PID controller computes the rate of change of the error, thus the directional trend of the error signal influences the controller output. While many controllers have traditionally been analog PI/PID controllers, the trend towards digital control systems has also had an influence on controller implementation. In many modern process plants the analog PI/PID controllers have been replaced by the digital counterparts.
Open-loop and closed-loop dynamics – Open-loop dynamics refers to the behaviour of a process if no controller is acting on it. Similarly, if the controller is turned off by setting the proportional constant to zero, the control system shows open-loop behaviour and the system’s dynamics are solely determined by the process. Hence, it is not possible to reach a new set-point for a process in open-loop unless the input is changed manually. It is also not possible to reject disturbances when the process is operated without a controller.
The purpose of using closed-loop control is to achieve a desired performance for the system. This can result in the system being stabilized, in a faster system response to the set-point changes, or in the ability to reject disturbances. The choice of the controller type as well as the values of the controller tuning parameters influences the closed-loop behaviour. For a controlled process one needs to find controller settings which result in a fast system response with little or no offset. At the same time, the system is to be robust to the changes in process characteristics. Finding the appropriate settings is called ‘tuning’ the controller.
Controller tuning and stability – Finding of the optimum tuning parameters for a controller is an important task. Unsuitable parameters can result in not achieving the desired closed-loop performance (e.g. slowly decaying oscillations, or a slow acting process). It is also possible that a closed-loop process with a badly tuned controller can result in performance which is worse than for the open-loop case or that the process can even become unstable.
Mathematical software for process control – A variety of different software packages is available which support the controller design, controller testing, and implementation process.
Advanced control techniques
While the single-loop PI/PID feedback controller is satisfactory for many process applications, there are cases for which advanced control techniques can result in a significant improvement in closed-loop performance. These processes often show one or more of such phenomena as (i) slow dynamics, (ii) time delays, (iii) frequent disturbances, (iv) multi-variable interaction. A large number of advanced control strategies are being used. Some important ones are briefly discussed below.
Feed- forward control – One of the disadvantages of conventional feed-back control with large time lags or delays is that disturbances are not recognized until after the controlled variable deviates from its set point. However, if it is possible to measure the load disturbance directly then feed-forward control can be applied in order to minimize the effect which this load disturbance has on the controlled variable. In addition to being able to measure the load disturbance, it is also needed to determine a mathematical correlation for the effect which the load disturbance has on the controlled variable in order to apply a feed-forward controller. The reason for this is that the feed-forward controller inverts this model in order to cancel the effect that the disturbance has. A feed-forward controller can be designed either based on the steady-state or dynamic behavior of the process.
Cascade control – Another possibility of controlling processes with multiple or slow-acting disturbances, is to implement cascade control. The main idea behind cascade control is that more than just one controller is used to reject disturbances. Instead a secondary controller is added to take action before the slow-acting disturbance has an effect on the primary controlled variable. In order to achieve this, the secondary controller also requires a secondary measurement point which needs to be located so that it recognizes the upset condition before the primary controlled variable is affected. Cascade control strategies are among the most popular process control strategies.
Selective and override control – Some processes have more controlled variables than manipulated variables. Such a situation does not allow an exact pairing of controlled and manipulated variables. A common solution is to use a device called a selector which chooses the appropriate process variable from among a number of valid measurements. The purpose of the selector is to improve control system performance as well as to protect equipment from unsafe operating conditions by choosing appropriate controlled variables for a specific process operating condition. Selectors can be based on multiple measurement points, multiple final control elements, or multiple controllers.
Adaptive control and auto-tuning – Operating conditions of a process can frequently change during plant operations. This does lead to the process behaving differently from the model which has been used for the controller design. Hence, the controller does not have accurate knowledge of the process at the current operating point and hence cannot be able to provide adequate disturbance rejection or set-point tracking. One possibility to circumvent this is to use an adaptive control system which automatically adjusts the controller parameters to compensate for changing process conditions. Auto-tuning is a related method where the closed-loop system is periodically tested, and the test characteristics automatically determine new controller settings.
Fuzzy logic control – For many processes, it is very time consuming to determine accurate process models. However, at the same time, it can be intuitive to get a rough estimate of how the manipulated variable is to react to a process condition. For such a case, fuzzy logic controllers can offer an advantage over conventional PID controllers. The reason for this is that fuzzy controllers do not need an exact mathematical description of a process. Instead, they classify the controller inputs and output as belonging to one of several groups (i.e. low, normal, and high). Fuzzy rules are then used to compute the output category from the given inputs. These rules either have to be provided by the control engineer or they have to be identified from plant operations by auto-tuning. It is also possible to combine fuzzy logic controllers with neural networks in order to form neuro-fuzzy controllers. This type of controller can offer significant advantages over conventional PID when applied to non-linear systems whose characteristics change over time.
Statistical process control (SPC) – SPC, also called statistical quality control (SQC), has found widespread application in recent years due to the growing focus on increased productivity. Another reason for its increasing use is that feed-back control cannot be applied to many processes due to a lack of on-line measurements. However, it is important to know if these processes are operating satisfactorily. While SPC is unable to take corrective action while the process is moving away from the desired target, it can serve as an indicator that product quality might not be satisfactory and that corrective action are to be taken for further plant operations.
For a process which is operating satisfactorily, the variation of product quality falls within acceptable limits. These limits normally correspond to the minimum and maximum values of a specified property. Normal operating data can be used to compute the mean deviation and the standard deviation s of a given process variable from a series of observations. The standard deviation is a measure for how the values of the variable spread around the mean. A large value indicates that wide variations in the variable. Assuming the process variable follows a normal probability distribution, then 99.7 % of all observations is to lie within an upper limit and a lower limit. This can be used to determine the quality of the control. If all data from a process lie within the limits, then it can be concluded that nothing unusual has happened during the recorded time period, the process environment is relatively unchanged, and the product quality lies within specifications. On the other hand, if repeated violations of the limits occur, then the conclusion can be drawn that the process is out of control and that the process environment has changed. Once this has been determined, the process operator can take action in order to adjust operating conditions to counteract undesired changes which have occurred in the process conditions.
Multi-variable control – Many technological processes contain several manipulated as well as controlled variables. These processes are called multi-variable control systems. It is possible to analyze the interactions among the control loops with techniques like the relative gain array. If it turns out that there are only small interactions between the loops then it is possible to pair the inputs and outputs in a favourable way and use single loop controllers which can be tuned independently from one another. However, if strong interactions exist, then the controllers need to be detuned in order to reduce oscillations.
Model predictive control (MPC) – MPC is a model-based control technique. It is the most popular technique for handling multi-variable control problems with multiple inputs and multiple outputs (MIMO) and can also accommodate inequality constraints on the inputs or outputs such as upper and lower limits. All of these problems are addressed by MPC by solving an optimization problem and therefore no complicated override control strategy is needed. A variety of different types of models can be used for the prediction. Choosing an appropriate model type is dependent upon the application to be controlled. The model can be based upon first-principles or it can be an empirical model. Also, the supplied model can be either linear or nonlinear, as long as the model predictive control software supports this type of model.
Real-time optimization – Operating objectives for process facilities are set by economics, product orders, availability of raw materials and utilities, etc. At different points in time it can be advantageous or necessary to operate a process in different ways to meet a particular operating objective. A technological process, however, is a dynamic, integrated environment where external and internal conditions can cause the optimal operating point for each operating objective to vary from time to time. These operating points can be computed by real-time process optimization (RTO), where the optimization can be performed on several levels, ranging from optimization within model predictive controllers, to supervisory controllers which determine the targets for optimum operation of the process, to optimization of production cycles. The plant-wide problems which can be solved by optimization techniques on a daily or hourly basis can be large containing thousands or even tens of thousands of variables.
Batch and sequence control
In batch processes, the product is made in discrete batches by sequentially performing a number of processing steps in a defined order on the raw materials and intermediate products. Large production runs are achieved by repeating the process. The term recipe has a range of definitions in batch processing, but in general a recipe is a procedure with the set of data, operations, and control steps to manufacture a particular grade of product. A formula is the list of recipe parameters, which includes the raw materials, processing parameters, and product outputs. A recipe procedure has operations for both normal and abnormal conditions. Each operation contains resource requests for certain ingredients (and their amounts). The operations in the recipe can adjust set-points and turn equipment on and off. The complete production run for a specific recipe is called a campaign (multiple batches). A production run consists of a specified number of batches using the same raw materials and making the same product to satisfy customer demand. The accumulated batches are called a lot.
In multi-grade batch processing, the instructions remain the same from batch to batch, but the formula can be changed to yield modest variations in the product. In flexible batch processing, both the formula (recipe parameters) and the processing instructions can change from batch to batch. The recipe for each product must specify both the raw materials required and how conditions within the reactor are to be sequenced in order to make the desired product.
Batch process control hierarchy – Functional control activities for batch process control can be summarized in four categories namely (i) batch sequencing and logic control, (ii) control during the batch, (iii) run-to- run control, and (iv) batch production management.
In batch sequencing and logic control, sequencing of control steps follow the recipe involve. For example:mixing of ingredients, heating, waiting for a reaction to complete, cooling, or discharging the resulting product. Transfer of materials to and from batch reactors includes metering of materials as they are charged (as specified by each recipe), as well as transfer of materials at the completion of the process operation. In addition to discrete logic for the control steps, logic is needed for safety interlocks to protect personnel, equipment, and the environment from unsafe conditions. Process interlocks ensure that process operations can only occur in the correct time sequence for a prescribed period of time. Detection of when the batch operations are to be terminated (end point) can be performed by inferential measurements of product quality, if direct measurement is not feasible.
Run-to-run control (also called batch-to-batch) is a supervisory function based on off-line product quality measurements at the end of a run. Operating conditions and profiles for the batch are adjusted between runs to improve the product quality using tools such as optimization. Batch production management entails advising the plant operator of process status and how to interact with the recipes and the sequential, regulatory, and discrete controls. Complete information (recipes) is maintained for manufacturing each product grade, including the names and amounts of ingredients, process variable set points, ramp rates, processing times, and sampling procedures. Other database information includes batches produced on a shift, daily, or weekly basis, as well as material and energy balances. Scheduling of process units is based on availability of raw materials and equipment and customer demand.
Sequential function charts – Compared to a continuous process, batch process control requires a greater percentage of discrete logic and sequential control than regulatory control loops. Batch control applications is to control the timing and sequencing of the process steps based on discrete input and outputs as well as analog outputs. The complexity of the interactive logic within and between the various control levels, the required interactions with operators and the need for ongoing application modification and maintenance are reasons why organization, functional design, and clear documentation are so important to the successful use of batch control applications. In order to describe what is to be done, structural models are normally used to represent the required batch processing actions, the batch equipment, and the combination of components. Various formats have been proposed for describing the batch control applications, e.g., how the batch processing steps are carried out with the batch equipment and instrumentation, interfaces between the various levels of control, interfaces between the batch control and the operator actions and responses, and interactions and coordination with the safety interlocks. The formats proposed include flow charts, state charts, decision tables, structured pseudo-code, state transition diagrams, petri nets, and sequential function charts. A sequential function chart (SFC) describes graphically the sequential behaviour of a control program.