Jerawat selama Pengecoran Baja Cair Berkelanjutan
Terobosan selama Pengecoran Baja Cair Berkelanjutan
Salah satu bencana kegagalan proses terburuk yang dapat terjadi selama proses continuous casting (CC) baja cair adalah pecahnya baja cair. Breakout terjadi ketika memperkuat baja untai pecah shell atau robekan di bawah cetakan. Ada beberapa alasan yang menyebabkan cangkang padat untai pecah dan memungkinkan baja cair yang terkandung di dalamnya tumpah keluar dan merusak peralatan mesin CC.
Breakout adalah insiden yang paling merugikan yang terkait dengan proses continuous casting. Insiden ini tidak hanya sangat mahal tetapi juga merupakan bahaya keselamatan yang serius bagi operator mesin CC. Breakout menyebabkan penutupan untaian dan mengakibatkan hilangnya waktu produksi bersama dengan penurunan hasil yang signifikan. Oleh karena itu setiap breakout menyebabkan kerugian ekonomi langsung yang signifikan. Untuk pemulihan untai mesin CC, biasanya memerlukan perputaran yang diperpanjang yang melibatkan pemindahan material baja yang tumpah dari dalam peralatan untai dan/atau penggantian bagian peralatan yang rusak.
Jerawat dapat dihindari dengan mengurangi kecepatan pengecoran sehingga memberikan lebih banyak waktu tinggal di cetakan agar baja mengeras. Untuk menghindari terjadinya breakout, sangat penting untuk mendeteksi pemadatan yang tidak tepat dari cangkang baja terlebih dahulu dengan waktu tunggu yang cukup untuk memperlambat mesin CC dengan tepat. Sejumlah pendekatan telah diadopsi untuk memprediksi breakout dalam proses continuous casting.
Sebuah breakout biasanya karena dinding shell baja terlalu tipis untuk mendukung kolom baja cair di atasnya. Hal ini disebabkan karena suatu kondisi yang memiliki beberapa akar penyebab yang sering dikaitkan dengan manajemen perpindahan panas. Aliran air pendingin yang tidak tepat ke cetakan CC atau gangguan pada sistem semprotan air pendingin untai dapat menyebabkan penghilangan panas yang tidak memadai dari baja cair yang mengeras, menyebabkan cangkang padat menebal terlalu lambat. Jika laju penarikan baja dalam untaian terlalu cepat, cangkang mungkin tidak memiliki waktu yang cukup untuk mengeras hingga ketebalan yang diperlukan bahkan dengan semprotan pendingin yang ditingkatkan. Demikian pula, baja cair yang masuk mungkin terlalu panas dan pemadatan akhir dapat terjadi lebih jauh ke bawah untaian pada titik berikutnya dalam cetakan dari yang diharapkan. Jika titik ini berada di bawah gulungan pelurus maka cangkang dapat pecah karena tekanan yang diberikan selama pelurusan.
Breakout juga dapat terjadi sebagai akibat dari ketidakteraturan fisik atau kerusakan pada cangkang baja yang terjadi di dalam cetakan CC selama periode awal pemadatan. Turbulensi yang berlebihan di dalam cetakan CC dapat menyebabkan pola cangkang tidak beraturan yang tumbuh tidak normal. Itu juga dapat menjebak tetesan terak atau sampah di dalam cangkang baja yang mengurangi kekuatan dinding.
Kejadian umum adalah menempelnya cangkang baja ke permukaan cetakan CC dan robek. Cangkang baja yang dibatasi oleh cetakan CC pecah di bagian meniskus, dan baja cair mengalir keluar dari bagian yang pecah segera di bawah cetakan CC. Jenis breakout ini disebut sticker breakout. Cetakan CC modern yang memiliki beberapa instrumen dan sistem kontrol komputer biasanya mendeteksi pelekatan dalam cetakan dan memperlambat kecepatan pengecoran sementara untuk membiarkan dinding membeku dan sembuh saat masih ditopang dalam cetakan CC. Jika robekan terjadi di dekat pintu keluar cetakan CC atau dengan tingkat keparahan yang tidak terduga, cangkang baja mungkin masih gagal pecah setelah keluar dari dinding cetakan CC. Jenis kerusakan stiker adalah jenis kerusakan utama selama operasi pengecoran kontinu. Salah satu alasan stiker pecah adalah pelumasan yang buruk pada cetakan. Gambar 1 menunjukkan penyebaran lengket di cetakan yang mengarah ke breakout.
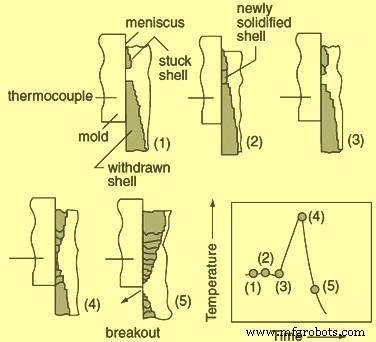
Gbr 1 Perkembangbiakan lengket di cetakan yang mengarah ke breakout
Retak juga menjadi penyebab munculnya jerawat. Dalam kasus pecah karena retak, bagian tipis dari cangkang baja yang disebabkan oleh penundaan pemadatan di sudut baja tuang atau tanda osilasi pecah segera di bawah cetakan CC.
Alasan lain untuk pelarian adalah jebakan sampah. Dalam hal ini bagian tipis dari cangkang baja yang disebabkan oleh penundaan pemadatan karena scum entrapment segera pecah di bawah cetakan CC.
Seiring dengan proses continuous casting yang telah berlangsung dan menjadi matang, distribusi jenis breakout berubah secara dramatis dari fenomena terkait perpindahan panas hingga dominasi pelekatan cetakan saat ini. Persentase jenis breakout yang menempel terhadap jumlah total breakout biasanya berkisar antara 75 % hingga 80 %. Persentase breakout karena retak biasanya berkisar antara 15% sampai 20% sedangkan persentase breakout karena terak dan scum entrapment biasanya berkisar sekitar 5%.
Sementara pemantauan terus menerus dari penghilangan panas cetakan dapat memberikan cara yang efektif untuk mendeteksi perkembangan kondisi breakout, waktu respons biasanya tidak cukup untuk menunjukkan fenomena yang terjadi dengan cepat dari robek dan robeknya cangkang baja.
Jika baja cair yang masuk terlalu panas (superheat sangat tinggi) maka lebih baik untuk menghentikan mesin CC daripada mengambil risiko breakout. Juga baja cair dengan kontaminasi timbal (Pb) dapat membentuk lapisan tipis antara dinding cetakan CC dan baja, menghambat pelepasan panas dan pertumbuhan cangkang baja sehingga meningkatkan risiko pecah.
Suhu fase panas cetakan CC sangat penting karena telah terlihat bahwa ketika suhu fase panas melebihi 350 derajat C maka terjadi pelekatan untai ke tembaga. Selanjutnya, dalam mesin CC produktivitas tinggi saat ini, pertukaran tundish secara rutin dan nozel masuk terendam 'on the fly' adalah praktik normal selama operasi normal. Operasi transien ini tak terhindarkan menyebabkan periode kecepatan casting dan kontrol level cetakan yang tidak stabil. Selama periode ini, proses pelumasan cetakan sangat tegang dan meningkatkan kemungkinan lengket.
Dalam kasus baja kelas tertentu (misalnya baja karbon tinggi) yang biasanya dicor pada suhu yang lebih rendah karena suhu likuidusnya yang lebih rendah, lengket sering dikaitkan dengan kinerja serbuk tuang yang buruk. Hal ini juga berlaku untuk grade baja yang akan dicor dengan kecepatan lebih rendah karena alasan metalurgi.
Tugas deteksi dan pencegahan breakout selama operasi continuous casting sama tuanya dengan teknologi continuous casting itu sendiri. Untuk tujuan ini beberapa metode pengukuran telah dikembangkan dan digunakan. Ini terdiri dari pengukuran suhu, gaya gesekan, gaya penarikan, getaran dan tingkat kebisingan yang ditanggung struktur. Dari metode ini, pengukuran suhu dengan menggunakan termokopel pada pelat tembaga cetakan adalah metode yang paling andal dan disukai.
Sistem kontrol untuk mengurangi frekuensi breakout secara efektif dikembangkan dengan memasang instrumentasi dalam cetakan CC. Awalnya instrumentasi ini didasarkan pada suhu diferensial air cetakan. Metode ini kemudian disempurnakan dengan menghitung hubungan perpindahan panas cetakan menggunakan data air cetakan. Namun dengan deteksi ini terbatas pada jerawat yang disebabkan oleh penurunan progresif dalam penghilangan panas.
Kemudian ketika jerawat yang diinduksi menempel meningkat dan menjadi dominan, sistem yang didasarkan pada teknik yang lebih langsung dikembangkan. Dalam teknik ini gesekan cetakan/untai diukur dengan akselerometer, sel beban, dan pengukur regangan. Sistem ini berhasil mendeteksi beberapa insiden yang mengganggu, tetapi sistem ini juga memberikan beberapa alarm palsu.
Sistem dimodifikasi lebih lanjut untuk pemantauan termal lokal dengan sensor fluks panas (termokopel tertanam). Sistem ini telah terbukti menjadi metode yang lebih efektif untuk mendeteksi dan mencegah kerusakan stiker. Terlihat bahwa deteksi stiker berbasis termokopel yang dikombinasikan dengan deteksi tingkat cetakan arus eddy memberikan keamanan breakout yang tinggi bahkan pada kecepatan casting yang tinggi.
Saat ini fokus telah bergeser dan tidak lagi secara eksklusif pada deteksi dini jerawat tetapi juga pada pemantauan pembuangan panas dan kontak antara cangkang baja dan cetakan CC. Oleh karena itu tidak biasa untuk cetakan CC individu untuk dilengkapi dengan sejumlah besar termosensor. Jumlah sensor yang besar ini membutuhkan jumlah kabel dan kopling yang baik dan karenanya membutuhkan investasi yang besar. Juga mengakibatkan biaya pemeliharaan yang cukup besar.