Perencanaan perawatan yang lebih baik adalah peluru perak MillerCoors
MillerCoors Asset CARE planner Tim Davison
Perencanaan tidak seksi. Tom Clancy tidak akan menulis film thriller spionase berjudul “The Maintenance Planner.”
Anda tidak akan menempatkan teman Anda di tepi kursi bar mereka menceritakan waktu Anda mengambil semua langkah yang tepat dan memastikan bahwa proyek perbaikan akan berjalan lancar. (“Bung, lalu apa yang terjadi?!”)
Tidak ada kemewahan atau flash atau eye candy.
“Ketika departemen pemeliharaan mencari peningkatan, biasanya ada fokus besar untuk menunjukkan kemenangan dan mengambil gambar sebelum dan sesudah – hal-hal yang 'wow',” kata Dan Roberts, direktur keandalan Asset CARE untuk Miller Coors di Golden, Colorado.
“Pemeliharaan prediktif itu seksi. Dengan termografi inframerah, Anda mengambil foto dan berkata, 'Lihat apa yang saya temukan.' Dengan analisis getaran, Anda menghubungkannya, mencetak bacaan Anda dan berkata, 'Ya, saya menemukan arah yang buruk.' Itu semua penting dan perlu, tapi ada pekerjaan bagus yang terjadi di intinya. Itu tidak seksi. Bagaimana Anda menunjukkan hasil perencanaan dan penjadwalan yang efektif? Anda tidak dapat melakukannya dengan foto sebelum dan sesudah.”
Diam-diam dan diam-diam, organisasi pemeliharaan dan keandalan MillerCoors menggunakan perencanaan dan penjadwalan sebagai alat peningkatan. Ini memberikan keseimbangan dalam lingkungan di mana ketidakseimbangan memiliki konsekuensi besar.
Mempertahankan Rantai
MillerCoors, pembuat bir terbesar ketiga di Amerika, telah menargetkan peningkatan pemeliharaan selama lebih dari satu dekade, dan untuk alasan yang baik. Tempat pembuatan bir Golden beroperasi 24 jam sehari, tujuh hari seminggu, untuk menyeduh 217 juta ons bir setiap hari.
“Mungkin ada dua hari dalam setahun kami tidak berproduksi,” kata Tim Davison, perencana Aset CARE di bagian pembuatan bir di kompleks pabrik ganda yang besar di Golden.
Proses pembuatan bir – dari bahan mentah hingga barang yang dikemas dan dikirim – berjalan dalam rantai yang saling terkait erat, dan banyak komponen proses menampilkan bagian mesin yang tidak berlebihan. Jika kerusakan mekanis terjadi, memindahkan pekerjaan ke peralatan serupa mungkin bukan pilihan. Dalam kasus ini, proses terhenti.
“Ketika ada kerusakan, biasanya itu menjadi masalah besar,” kata Ron Kerr, manajer Asset CARE untuk utilitas. “Ini mempengaruhi hampir semua orang di hulu dan hilir.”
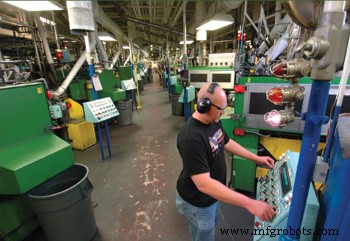
Operator pers Craig Doebele mengerjakan kontrol di sepanjang lini produksi
di Rocky Mountain Metal Container, usaha patungan MillerCoors/Ball.
Tujuannya adalah agar mesin bekerja tanpa henti selama berbulan-bulan, terutama selama puncak musim panas, hingga periode pemeliharaan singkat dapat dijadwalkan.
Struktur unik unit bisnis Golden menambah tekanan pada rantai. Sementara MillerCoors memiliki tempat pembuatan bir, itu adalah mitra bersama dalam unit manufaktur kaleng (dengan Ball Corporation) dan manufaktur botol (Owens-Illinois). Mengarahkan semua orang ke arah yang sama memang perlu, tetapi itu membutuhkan kesabaran.
Bahan yang Hilang
Laju peningkatan pemeliharaan, lambat dan stabil selama bertahun-tahun, dipercepat pada akhir 1990-an setelah pemain top Anheuser Busch mengumumkan pemotongan harga. Agar tetap kompetitif, MillerCoors berusaha menginvestasikan kembali di ujung depan bisnis.
“Harga barang-barang kami harus turun dengan margin yang besar,” kata Roberts. “Kami harus mengejar sejumlah elemen, salah satunya adalah operasi. Peluang dan tujuannya adalah menjadi operasi yang paling andal.”
Mike Zietlow, spesialis senior di toko forklift tempat pembuatan bir MillerCoors, perutnya naik ke bangku catok untuk melakukan beberapa pekerjaan presisi. Area forklift telah sangat meningkatkan tingkat penyelesaian pemeliharaan preventifnya selama 18 bulan terakhir.
Asset CARE (singkatan dari Capability, Availability, Reliability and Enhancement) menjadi seruan. Reliability-Centered Maintenance (RCM), root cause failure analysis (RCFA) dan alat pemeliharaan prediktif (PdM) digunakan. Bahkan dengan langkah positif ini, ada sesuatu yang hilang.
Roberts mengutip contoh seorang penggemar yang mengalami tiga kegagalan dinamis selama jangka waktu 18 bulan. Setelah kegagalan pertama, RCFA mengidentifikasi pelumasan sebagai penyebab utama. Sistem pelumasan otomatis dipasang. Setelah kegagalan kedua, pelumas mobil dianggap bermasalah. Setelah kegagalan ketiga, pemimpin pemeliharaan mundur selangkah.
“Kami sekarang berpartisipasi dalam latihan pemetaan penyebab yang membuat kami menjelajahi berbagai akar penyebab,” kata Roberts. “RCFA tidak mengatakan bahwa ada satu akar penyebab, tetapi mengarahkan orang ke arah itu.”
Dengan masuk lebih dalam, perencanaan dan penjadwalan muncul sebagai kontributor masalah.
Sebulan sebelum kegagalan ketiga, analisis getaran telah mengidentifikasi kelainan. Namun, langkah-langkah yang tepat tidak diambil untuk menjadwalkan pemeliharaan, dan menjadikannya sebagai prioritas, sebelum kegagalan terjadi. Pelajarannya:keuntungan besar tidak mungkin diperoleh jika perencanaan dan penjadwalan dasar tidak ada.
“Sebelum upaya terkonsentrasi kami, kami tidak merencanakan dan menjadwalkan,” kata Roberts. “Perencana memeriksa perintah kerja dalam sistem komputer, mencetaknya, memberikannya kepada supervisor dan menunggu supervisor menyerahkannya kepada kru. Ada sedikit upaya yang dilakukan untuk duduk setiap minggu dengan operasi dan meninjau apa yang akan terjadi, menentukan prioritas, dan mengidentifikasi sumber daya.”
Pabrik berfungsi dalam mode perawatan reaktif. Para perencana menghabiskan banyak waktu untuk mencari, menyimpan, dan menyebarkan suku cadang pengganti.
“Jika organisasi kami berpikiran maju, kami menemukan hal-hal yang perlu diperbaiki, menulis perintah kerja, merencanakan perintah kerja, dan menyelesaikan pekerjaan. Jika reaksioner, kami membeli kursi kelas satu di pesawat untuk mengirimkan motor,” kata Bobby McCall, manajer pemeliharaan untuk operasi pengemasan.
Pekerjaan reaktif memiliki imbalannya – tepukan di punggung dan ucapan terima kasih dari produksi. Trofi perjalanan diberikan setiap tahun kepada perencana yang bertanggung jawab atas pengiriman paling banyak dalam semalam.
Kemudian MillerCoors menemukan cara yang lebih baik dengan mengidentifikasi komponen penting dari perencanaan pemeliharaan yang efektif. Ini memaksimalkan sumber daya, meminimalkan biaya, dan meningkatkan keandalan peralatan secara keseluruhan. Bagian berikut menguraikan beberapa komponen ini.
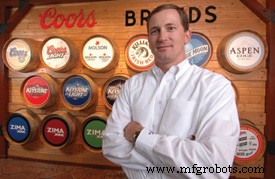
Dan Roberts adalah direktur Aset CARE dari
keandalan untuk Pembuatan Bir MillerCoors Perusahaan di
Golden, Colo. Sementara pabrik perusahaan
telah membuat langkah signifikan,
dia mengakui bahwa “kita belum sampai di sana”.
Benar-Benar Berdedikasi
Seperti dalam upaya apa pun, dedikasi adalah kunci kesuksesan. Di MillerCoors, pemeliharaan yang berpikiran maju dimulai dengan perencana dan sumber daya yang berdedikasi.
Sebuah organisasi perencanaan membutuhkan jumlah perencana yang sesuai. Setiap perencana harus memiliki area tanggung jawab yaitu:
• wajar dalam ukuran geografis;
• wajar dalam jumlah personel kerajinan yang diwakili; atau,
• jumlah peralatan yang masuk akal.
Tanpa batasan seperti itu, bagaimana perencana dapat mendedikasikan waktu dan sumber daya yang tepat untuk mempertahankan area tersebut secara efektif?
Davison mengatakan bahwa dengan area yang terlalu besar, satu perencana tidak dapat fokus pada seluruh ruang lingkup, hanya aktor buruk dan situasi darurat yang muncul. Ketika seorang perencana berfokus pada pelaku dan kegagalan yang buruk, itu tidak memungkinkan perencanaan prediktif dan proaktif yang diperlukan.
“Dua orang tidak dapat merencanakan 4.000 peralatan,” kata Davison. “Mereka hanya punya waktu untuk memesan suku cadang.”
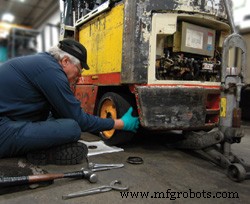
Mekanik forklift Jerry Mitchell melepas roda dalam
untuk mengekspos bantalan untuk pekerjaan pemeliharaan preventif.
Mengenai cakupan perencana-untuk-kerajinan, Roberts mengatakan tujuannya saat ini adalah satu perencana untuk setiap 15 hingga 18 orang pengrajin. Aturan umumnya adalah bahwa saat Anda maju menuju kelas dunia, Anda dapat memiliki lebih banyak pengrajin per perencana. Jika Anda berada di anak tangga terbawah, persentase perencana yang lebih besar sesuai.
Tujuan pembuat bir adalah untuk secara khusus membatasi perencananya pada tugas-tugas yang berkaitan dengan keandalan dan pemeliharaan area tanggung jawab yang ditentukan. Jika tidak, perencana mudah teralihkan oleh pekerjaan yang berada di luar peran dan fungsinya.
“Produksi dapat melihat perencana sebagai ‘go-fer’ atau Wal-Mart, yang siap melayani setiap kebutuhan dan keinginan mereka,” kata Brad Simpkins, manajer Asset CARE yang bertanggung jawab atas peralatan seluler.
Manajemen pabrik dan departemen juga dapat menghambat perencana dengan tugas administratif, pelaporan, dan input data.
“Tanpa kemampuan untuk memiliki fokus yang nyata, perencanaan menjadi reaktif,” tambah Simpkins.
Sama pentingnya, para perencana ini juga membutuhkan sumber daya khusus (waktu dan tenaga) untuk menyelesaikan pekerjaan yang direncanakan dan dijadwalkan. Ini bisa menjadi pil pahit bagi beberapa pekerja pemeliharaan dan produksi.
"Beberapa mekanik per jam berkata, 'Kami menyukai apa yang kami lakukan sekarang.' Mereka suka datang dengan kuda putih dan menyelamatkan hari," kata Jay Johnson, manajer pemeliharaan untuk operasi proses. “Tetapi mereka melihat bahwa manajemen berada di belakang 100 persen ini. Ini tidak akan hilang.”
Manajer produksi dan operator juga curiga tentang menempatkan kuda putih ke padang rumput.
Dalam organisasi pengemasan MillerCoors, kru pemeliharaan dibagi rata di antara tiga shift. “Tujuan mereka adalah untuk memperbaiki mesin dan menjalankannya,” kata Kerr.
Kemudian, perubahan penjadwalan pertama datang. Persentase yang cukup besar dari pekerja kerajinan yang bekerja malam dan akhir pekan dialihkan untuk melakukan pekerjaan yang direncanakan pada shift siang.
"Produksi memberi tahu kami, 'Anda tidak mendukung kerusakan kami!'" kata Kerr. "Kamu benar. Saya tidak akan mendukung kerusakan Anda. Saya akan mendukung pekerjaan proaktif. Membuat mereka menerima hal itu membutuhkan lompatan keyakinan.”
Di antara departemen fungsional dalam MillerCoors, pengemasan saat ini menjadi pelopor dalam mendorong sumber daya khusus untuk pekerjaan yang proaktif dan terencana.
“Kami akan merencanakan 100 persen dari jam yang tersedia untuk pekerjaan pemeliharaan yang direncanakan,” kata McCall. “Kami masih mendengar, 'Anda tidak bisa melakukan itu; Anda harus merencanakan kerusakan.’ Tidak, kami tidak akan merencanakan kerusakan. Kami akan merencanakan untuk melakukan pekerjaan yang direncanakan. Kami akan menangani kerusakan jika itu terjadi.”
Di semua tingkatan, organisasi harus menyadari bahwa operator dan personel pengrajin ada di fasilitas manufaktur karena ada proses untuk mengoperasikan dan memelihara. Ada perencana untuk memaksimalkan efektivitas operator dan pengelola. Ketika semua tingkat dalam operasi mulai bekerja sama sebagai sebuah tim, untuk tujuan bersama untuk meningkatkan keandalan dan kinerja operasional, tidak ada lagi fokus pada "kemenangan kuda putih" tetapi pada keuntungan jangka panjang yang berkelanjutan.
Manajemen Waktu
Kunci lain keberhasilan perencanaan MillerCoors adalah memanfaatkan waktu sebaik-baiknya.
Seperti disebutkan di bagian sebelumnya, produksi agak skeptis. Jika pemeliharaan dimaksudkan untuk mengurangi kesulitan produksi, "pemikir maju" ini harus membuktikan nilai mereka. Ingat, mesin offline dapat memiliki implikasi yang sangat besar.
Tantangannya adalah membuat produksi melihat bahwa mematikan mesin selama 40 menit untuk pemeliharaan preventif selama waktu dan hari yang telah ditentukan lebih baik daripada pemadaman tiga jam setelah kerusakan pada waktu dan hari yang tidak diketahui. Tantangan tambahannya adalah membuat produksi percaya bahwa waktunya yang berharga tidak akan terbuang percuma.
“Kami memiliki rekam jejak yang buruk dengan perencanaan dan penjadwalan. Kami harus membuktikan bahwa jika Anda memberi kami waktu, kami akan menyelesaikan pekerjaan yang terencana dan proaktif,” kata Davison. “Mereka menurunkan garis. Mereka kehilangan uang. Anda harus memanfaatkan jendela itu sebaik mungkin.”
Maksimalisasi waktu terjadi melalui perencanaan dan penjadwalan yang efektif.
Pertama, jangka waktu pemeliharaan harus didefinisikan dengan jelas (waktu yang dijadwalkan, tanggal, ruang lingkup dan durasi) dan disetujui oleh perencana pemeliharaan dan pemimpin produksi. Dari sana, perencana memesan suku cadang dan bahan yang diperlukan dan memastikan bahwa jumlah sumber daya yang benar tersedia untuk menangani pekerjaan itu. Perencana mengawasi agar tidak ada kejutan atau, lebih buruk lagi, pembatalan terjadi saat jendela terbuka. Tenaga kerja pemeliharaan yang terdampar atau tidak produktif memiliki dampak biaya langsung terhadap bisnis.
Keterlibatan tidak berakhir di situ. Selama jendela, perencana mengamati, membantu, dan mengevaluasi pekerjaan untuk mendapatkan pengetahuan penuh tentang pekerjaan itu. Pengetahuan itu diterapkan untuk merencanakan dan menjadwalkan tugas serupa dengan lebih baik di masa depan. Dia juga mendapatkan rasa hormat dan penghargaan dari orang-orang kerajinan yang mengerjakan pekerjaan itu. Ini penting ketika saran dan pertanyaan teknis muncul di lain waktu.
Meskipun ini adalah metode konvensional, rencana-sebagai-kerja-timbul di MillerCoors, metode perencanaan dan penjadwalan khusus juga ada.
Pabrik pembuatan kaleng, yang harus berjalan terus-menerus untuk memenuhi kebutuhan pembuatan bir (12 juta kaleng per hari), menggunakan rencana waktu henti selama 12 bulan yang dikembangkan bersama oleh pimpinan operasi, pemeliharaan, teknik, kontrol proses, kualitas, gudang, dan penjadwalan.
Rencana tahun 2005 mencantumkan tanggal, lokasi, kegiatan pemeliharaan dan rincian proyek untuk 1.655 jam waktu henti yang dijadwalkan. Rencana 2006 disepakati pada bulan September.
“Kami menempatkan 20 orang dalam satu ruangan dan membentuknya sebagai sebuah tim,” kata David Miller, direktur layanan teknis untuk Rocky Mountain Metal Container (usaha patungan MillerCoors/Ball). “Kami menempatkan semuanya sesuai jadwal dan mengeksplorasi, apa lagi yang bisa kami lakukan selama pemadaman itu? Bagaimana kita bisa memaksimalkan waktu itu? Kami tidak dapat memiliki kejutan sepanjang tahun. Kami harus berada di depan permainan. Oleh karena itu, rencana waktu henti adalah dokumen panduan kami untuk memastikan keandalan peralatan dan pengiriman kaleng aluminium untuk memenuhi persyaratan tempat pembuatan bir.”
Pabrik pembuatan botol, yang memproduksi 3 juta botol per hari, menggunakan pemikiran ke depan untuk penghentian mesin tunggal dan pabrik penuh terjadwal.
“Kami biasa beroperasi sepanjang tahun dan kemudian tutup saat Natal untuk pekerjaan pemeliharaan preventif (PM),” kata Tim Hood, manajer layanan teknik di Rocky Mountain Bottle Company (usaha patungan MillerCoors/Owens-Illinois). “Untuk sisa tahun ini, Anda akan menghadapi kegagalan saat terjadi karena kami tidak menjadwalkan waktu henti lainnya.”
Hari ini, perencana dan pemimpin pemeliharaan dan produksi di pabrik ini menjadwalkan sesi waktu henti yang disebut “maxi pit stop”. Serupa dengan rencana waktu henti pabrik kaleng, pemberhentian untuk PM dan overhaul ini sudah direncanakan sebelumnya.
“Kami menjadwalkan mesin yang berbeda pada waktu yang berbeda,” kata Hood. “Dengan begitu, Anda tidak memiliki semua peralatan Anda sekaligus. Kami memindahkan sumber daya untuk mengimbangi waktu henti.”
Penutupan pabrik tahunan, yang dipimpin oleh seorang perencana, terjadi pada bulan September.
"Dia terlibat dengan seluruh rencana, mencoba mencari tahu pekerjaan apa yang perlu dilakukan selama pemadaman," kata Hood. “Kami melakukan pembersihan uap pada mesin dan PM semua peralatan distribusi listrik selama ini. Ini adalah usaha besar. Saat kita menyelesaikan satu shutdown, perencana sudah menyusun rencana untuk shutdown berikutnya.”
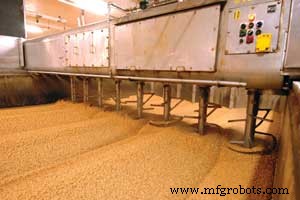
Proses pembuatan bir dimulai dengan malting barley.
Barley adalah direndam dalam air dan didorong untuk berkecambah.
Setelah empat sampai lima hari, "malt" dipanaskan untuk menghentikan pertumbuhan
lebih lanjut. Malt kemudian dipecah dengan rol baja untuk
mengekspos isinya.
Informasi yang Berguna
Keberhasilan perencanaan MillerCoors juga terkait dengan pemanfaatan informasi secara maksimal. Dimulai dengan sesuatu yang mendasar seperti memberikan informasi akurat tentang sumber daya yang tersedia untuk shift tertentu.
"Siapa disini? Berapa lama mereka di sini? Berapa banyak sumber daya yang harus direncanakan oleh para perencana? Sebelumnya, seperti di organisasi reaktif mana pun, itu samar-samar,” kata McCall. “Di SAP, kami memakukannya. Perencana melihat bahwa 'Saya memiliki jendela delapan jam dan 10 orang. Saya dapat merencanakan pekerjaan senilai 80 jam. Berikut adalah 80 jam kerja untuk dimasukkan ke dalam rencana itu.’”
Bekas area abu-abu lainnya adalah perintah kerja. Seperti di kebanyakan pabrik, perintah kerja dibuat ketika pekerjaan diidentifikasi. Tapi informasi apa yang disertakan dalam perintah kerja itu?
Belajar dari masa lalu, pemimpin pemeliharaan MillerCoors sekarang mengatakan perintah kerja harus mampu menangkap kode biaya peralatan yang tepat, semua riwayat peralatan, biaya tenaga kerja dan bahan, dan persyaratan layanan kontrak. Untuk melacak kegagalan peralatan secara akurat, deskripsi kerja terperinci dimasukkan saat pesanan dibuat dan deskripsi akurat tentang apa yang dilakukan untuk memperbaiki kegagalan dimasukkan setelah menyelesaikan perintah kerja. Jika ini tidak dilakukan, riwayat untuk peralatan tertentu terdistorsi dan mungkin tidak secara akurat menjelaskan kerusakan atau kegagalan. Juga, nomor peralatan yang tepat dimasukkan pada perintah kerja. Tanpa ini, tindakan pelacakan riwayat penting seperti bahan yang digunakan dan jam kerja yang dibebankan terkait dengan bagian peralatan yang salah atau hilang sama sekali.
“Dulu, keputusan buruk dibuat karena kami tidak memiliki informasi perintah kerja yang akurat,” kata Davison.
Saat perintah kerja dibuat di MillerCoors, catatan dibuat untuk membantu mengidentifikasi:
• setiap bagian, keterampilan, atau sumber daya luar yang diperlukan untuk menyelesaikan pekerjaan;
• alat, perlengkapan, atau sumber daya khusus yang berpotensi diperlukan; dan,
• potensi masalah keselamatan atau lingkungan.
Dengan informasi awal ini, perencana mendapatkan suku cadang dan bahan yang dibutuhkan, mengumpulkan sumber daya yang dibutuhkan, dan secara akurat merencanakan dan menjadwalkan pekerjaan. Ini meningkatkan waktu kunci pas.
Ketika pekerjaan selesai, seorang pengrajin memasukkan informasi rinci untuk menutup perintah kerja dengan benar. Dalam sistem perintah kerja SAP perusahaan, dia secara akurat memasukkan kode penyebab, kode kegagalan, dan bagian objek pada bagian riwayat akhir pemberitahuan. Deskripsi teks panjang yang mendetail tentang pekerjaan yang dilakukan didokumentasikan bersama dengan masalah atau perbedaan apa pun.
Namun semua langkah tersebut tidak ada artinya jika Anda tidak menggunakan informasi tersebut.
Pekerjaan pemeliharaan dilakukan berulang-ulang. Apa yang dipelajari tentang mesin hari ini terbukti bermanfaat ketika mesin yang sama atau serupa membutuhkan perawatan di masa depan. Histori mengidentifikasi tren dan membantu membangun strategi keandalan yang efektif.
“Jika data tidak akurat untuk peralatan itu, Anda tidak mendapatkan gambaran lengkap dan Anda akan membuat kesalahan dalam memelihara peralatan itu,” kata Davison. “Jika tidak dicatat dalam sistem, Anda tidak memiliki data untuk dianalisis. Para perencana membutuhkan itu untuk memutuskan bagaimana merencanakannya di lain waktu, melakukannya dengan lebih baik, dan menggunakannya untuk tujuan utama.”
Dengan informasi perintah kerja yang dimasukkan dengan benar, personel MillerCoors dapat mengakses perintah kerja dan riwayat biaya untuk masing-masing peralatan, departemen, pusat biaya, atau seluruh fasilitas. Dengan data ini, perencana menentukan persentase penyelesaian PM, waktu penyelesaian perintah kerja, waktu rata-rata untuk memperbaiki dan waktu rata-rata antara kegagalan. Mereka juga mengakses campuran persentase PM, korektif, rincian, dan perintah kerja proyek untuk jangka waktu tertentu. Laporan ini memberi mereka alat untuk menyesuaikan frekuensi PM menurut pesanan yang dihasilkan dan MTBF.
“Pada beberapa peralatan, kami menemukan frekuensi PM kami terlalu tinggi,” kata McCall. “Perencana kami melihat PM secara teratur. Mereka memastikan bahwa PM yang tepat, dengan frekuensi yang tepat, ada di tempatnya. Idenya adalah bahwa pekerjaan yang kita rencanakan adalah pekerjaan yang harus dilakukan. Kami ingin menggunakan waktu dan uang kami sebaik mungkin dan mengejar hal-hal yang tepat.”
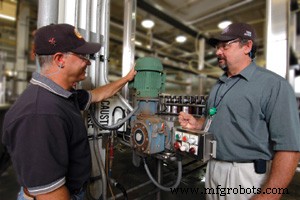
Manajer ASET CARE Bobby McCall (kiri) dan Ron Kerr
berdiskusi motor dan girboks di lini pengemasan tempat pembuatan bir.
Hasil Emas
Peningkatan perencanaan dan kecakapan perencanaan telah memberikan dampak di MillerCoors.
“Kami selalu memiliki orang-orang hebat dengan keinginan untuk melakukan hal yang benar,” kata insinyur pabrik Mike Fognani. “Perencanaan dan penjadwalan memungkinkan kami menggabungkan orang-orang hebat itu dengan alat, bahan, dan waktu yang dibutuhkan untuk menjadi sukses.”
Pekerjaan yang direncanakan dan dijadwalkan di banyak area lokasi sekarang merupakan lebih dari 60 persen dari beban kerja pemeliharaan; di masa lalu, angka itu kurang dari 30 persen.
Pekerjaan PM yang diselesaikan telah meningkat secara dramatis. Di area forklift, misalnya, Simpkins mengatakan tingkat penyelesaian meningkat dari 31 persen menjadi 82 persen dalam waktu kurang dari 18 bulan.
Ketersediaan peralatan, produktivitas, dan waktu kerja semuanya meningkat. Semua ini telah menghasilkan pengurangan biaya pemeliharaan.
“Dulu 'pemeliharaan tidak dapat membuatnya tetap berjalan', 'Anda tidak dapat diandalkan' dan 'Anda menghabiskan terlalu banyak uang,'” kata McCall. “Sejak kami menjadi stabil dan lebih proaktif, biaya pemeliharaan kami turun.”
Banyak peluang masih ada.
“Di banyak bidang, kami melakukan apa yang perlu kami lakukan dan menjaring hasil yang kami cari,” kata Roberts. “Kami berada di jalur yang benar, tetapi kami belum sampai di sana. Kami masih memiliki banyak peluang dengan perencanaan dan penjadwalan, dan berfokus pada cara-cara untuk membuat perubahan langkah, bahkan setelah pekerjaan hebat yang sudah dimainkan.”
Mengurangi biaya. Peningkatan keandalan. keputusan yang lebih baik. Stabilitas yang lebih baik.
MillerCoors mungkin telah menemukan cara untuk membuat perencanaan menjadi seksi.
Fakta
Situs :Pabrik MillerCoors di Golden, Colo. (termasuk tempat pembuatan bir dan area pendukung produksi terkait), dan Rocky Mountain Metal Container dan Rocky Mountain Bottle Company (dua pabrik patungan).
Ketenagakerjaan :Hampir 2.000 karyawan di pabrik manufaktur Golden.
Ukuran lokasi :Terletak terutama di lembah sepanjang lima mil di Golden.
Produk :Hampir selusin merek bir, termasuk Coors, Coors Light, Irish Red Lager milik George Killian, Aspen Edge, dan Keystone. Juga, minuman malt merek Zima.
Volume produksi :Lebih dari 20 juta barel bir diseduh di Golden setiap tahun.